선택적 레이저 조형된 AlSi10Mg합금의 후열처리에 따른 Si-rich상 형상변화가 기계적 특성에 미치는 영향
Influence of Si-rich Phase Morphologies on Mechanical Properties of AlSi10Mg Alloys p rocessed by S elective L aser M elting a nd P ost-Heat Treatment
Article information
Abstract
In this study, AlSi10Mg powders with average diameters of 44 μm are additively manufactured into bulk samples using a selective laser melting (SLM) process. Post-heat treatment to reduce residual stress in the as-synthesized sample is performed at different temperatures. From the results of a tensile test, as the heat-treatment temperature increases from 270 to 320°C, strength decreases while elongation significantly increases up to 13% at 320°C. The microstructures and tensile properties of the two heat-treated samples at 290 and 320°C, respectively, are characterized and compared to those of the as-synthesized samples. Interestingly, the Si-rich phases that network in the as-synthesized state are discontinuously separated, and the size of the particle-shaped Si phases becomes large and spherical as the heat-treatment temperature increases. Due to these morphological changes of Si-rich phases, the reduction in tensile strengths and increase in elongations, respectively, can be obtained by the post-heat treatment process. These results provide fundamental information for the practical applications of AlSi10Mg parts fabricated by SLM.
1. 서 론
금속 적층제조(Metal Additive Manufacturing) 기술은 3 차원의 디지털화된 데이터를 기반으로 분말, 와이어, 판재 등 금속 원료 소재를 연속적으로 적층하여 3차원 형상의 조형체를 제조하는 기술이다. 금속소재의 적층 제조공정 기술은 전통적인 주조 및 단조, 용접, 압출 기술에 비해 제 품 생산시간(Lead time)을 획기적으로 감소시킬 수 있고 가공에 의한 원료 소재의 손실을 최소화할 수 있으며 정 밀하고 복잡한 형태의 제품을 소량다품종으로 제조할 수 있다. 이러한 특성들로 인하여 적층제조 기술은 3D프린팅 이라는 이름으로 제조혁신을 가져올 신공정기술로 크게 각광받고 있다[1].
금속의 적층제조 방법에는 대표적으로 Directed Energy Deposition(DED) 공정과 Powder Bed Fusio n(PBF) 공정이 있으며 선택적 레이저 용융(Selective Laser Melting(SLM)) 공정은 PBF 공정의 대표적인 방식이다. SLM 공정은 기 판에 도포된 금속분말에 선택적으로 조사된 레이저가 금 속분말을 용융시킨 후에 응고되면서 원하는 제품을 제조 하는 기술로서 정밀한 부품 제작에 적합하다. 따라서, 최 근에는 SLM 공정방식으로 Ni계 및 Fe계, Ti계, Al계 등의 합금을 소재로 한 연구가 활발히 진행중이며 그 중 Al계 소재의 경우, 성형성 및 내구성, 경량성이 우수하여 자동 차나 항공 등의 수송분야에서 사용할 소재로써 주목 받고 있다[2-5]. 그러나, Al계 분말소재는 Al의 높은 표면 반사 율과 표면 산화막에 의한 조형체 치밀화가 어렵기 때문에 200W급 이상의 비교적 높은 레이저 파워를 사용하여 공 정을 진행하고 있다[6]. 현재까지 적층제조 분야에서 가장 활발하게 사용되는 Al계 합금의 경량금속소재는 Al-Si계 합금이다. Al 합금에 Si이 첨가될 경우, 레이저 흡수율이 증가하고 응고범위가 감소되므로 적층제조공정에서 생기 는 결함이 줄어들 수 있다는 연구결과가 보고되는 등 현 재 가장 많은 응용이 이루어지고 있는 합금조성이다[7].
SLM 공정으로 Al-Si계 합금을 제조하는 경우에는 전통 적인 주조방식에 비해 매우 빠른 냉각속도와 열팽창 및 수축이 반복되는 특징을 고려하여야 한다. 따라서 전통적 인 주조방식에서는 볼 수 없었던 불균일한 미세조직과 잔 류응력을 가지며 이것이 조형체의 기계적 물성에 영향을 끼치는 것으로 알려져있다[8-10]. 따라서 조형 직후의 적 층 조형체는 일반적으로 높은 인장 및 항복강도를 갖지만, 상대적으로 낮은 연신율을 가지므로[11], 이러한 특성을 개선하기 위해 후열처리(post heat treatment)에 대한 다양 한 연구가 진행되고 있다.
일반적으로 주조공정으로 제조된 AlSi10Mg합금의 경우 T6 열처리를 하여, 용체화 처리 후 인공시효 과정에서 Mg2Si가 석출시켜 강도 및 연신율을 크게 향상시킨다[12]. 하지만, Aboulkhair 등의 연구결과에 따르면 SLM 공정으 로 제조된 AlSi10Mg합금의 경우, 용체화 처리 후 인공시 효 단계에서 강도 향상이 이뤄지지 않고 오히려 강도가 초 기값보다 떨어진다는 것이 확인되었다[13]. 또한 Fousova 등은 SLM 공정으로 제조된 AlSi10Mg합금을 120에서 180°C에서 열처리하였으나 항복강도는 크게 향상된 것에 비해 인장강도 및 연신율이 크게 감소하는 결과를 확인하 였다[14]. 또한 Fiocchi 등의 연구 결과에 따르면 SLM 공 정으로 제조된 AlSi10Mg합금을 263에서 294°C까지 열처 리한 경우, 모두 경도가 감소한 것을 확인하였지만 미세조 직의 변화는 하나의 온도조건(294°C)에서 열처리한 경우 에만 나타난 것으로 확인된 바 있다[15].
이와 같이 현재까지 SLM 공정으로 제조된 Al-Si계 합 금의 열처리에 대한 연구는 주로 T6중심으로 이루어져왔 다. 그러나, 최근 자동차 분야 등 조형 직후 응력완화 (stress-relief)를 통해 바로 경량 부품을 활용하고자 하는 응용분야가 늘어남에도 불구하고 조형체의 후열처리만으 로 인장특성과 미세조직을 제어하는 연구결과는 여전히 미미한 상황이다. 따라서, 본 연구에서는 SLM 공정으로 제조된 3차원 조형체에 응력완화 개념의 후열처리에 따른 조형체의 미세조직의 변화를 확인하였으며 미세조직의 변 화가 인장 특성에 미치는 상관관계를 고찰하였다.
2. 실험방법
2.1. 적층제조 및 열처리
본 연구에서는 평균입도 44 μm 크기로 분급한 AlSi10Mg 분말을 사용하였다. 분급한 분말은 Concept Laser사의 M2 장비(ytterbium fiber laser, 400W)를 사용하여 SLM 공정 을 수행하였다. 알루미늄 합금 분말 표면의 산화막을 극복 하고 분말을 완전히 용융시켜 고밀도의 조형체를 확보하 기 위하여 레이저 파워를 360W 및 레이저 스캔 스피드 를 1600 mm/s, 레이저빔 사이의 중첩도를 30%로 고정하 여 조형을 진행하였다. 레이저는 XY 평면에서 45o 방향으 로 조사되었고, Z축 방향으로 적층이 진행되었으며 층마 다 90°씩 회전하면서 조사되었다. 적층제조 공정은 조형체 의 산화 방지를 위해 산소 함량이 0.1% 이하인 A rgo n 분 위기에서 진행하였다. 조형체의 형상은 Thin wall(78 × 3 × 6 mm3)의 형태로 제조 후, ASTM E8 sub size로 가공하였 다. 가공된 시편들은 SiC tube furnace를 사용하여 10°C/ min로 승온시켜 각각의 설정값인 270, 280, 290, 300, 310 그리고 320°C까지 가열 후 90분 동안 유지하였다. 이때 실제로 시편이 위치한 Furnace의 내부 온도는 설정값에 비해 약 20°C 낮은 것을 확인하였으며 열처리가 종료된 후에는 로에서 꺼내어 공기중에서 냉각하였다.
2.2. 분석방법
AlSi10Mg 분말의 입도는 Laser particle size analyze (LS13, Beckman Coulter, United States)를 이용해 건식 분 위기에서 분석하였다. 분말의 유동도는 Hall flowmeter (Carney Funnel)를 이용하여 Ф4.93 mm의 직경을 분말 50 g 이 모두 통과하는데 걸린 시간으로 측정하였다. Hausner ratio는 각각 Tap density와 Apparent density를 측정한 후 Tap density / Apparent density로 계산하여 나타내었다.
조형체 내의 미세조직을 분석하기 위하여 시편을 마운 팅 한 후 폴리싱 하였고, HCl:HNO3:HF:Distilled Water = 1.5:2.5:1:95 로 혼합하여 만들어진 Keller reagent 용액으 로 에칭하였다. 미세조직은 OM(TME-BD, Nikon, Japan), FE-SEM(MIRA3 LM, Tescan, Czech Republic), TEM (TF30ST, FEI, USA)을 통해 분석하였다.
조형체의 기계적 특성은 인장시험 및 비커스 경도 측정 을 통해 분석하였다. 인장시험은 만능인장시험기(PB301, UNITECH-T, P&B Inc, Republic of Korea)를 사용하였고, 하중변화속도는 1mm/s로 상온에서 진행하였다. 비커스 경도는 Micro-Vickers hardness(HM-100, Mitutoyo, Japan) 을 통해 분석하였고, 경도 측정 시 하중은 0.5 N으로 설정 하였으며 유지시간은 15초로 설정하였다.
3. 결과 및 고찰
Fig. 1에는 본 연구에서 사용한 알루미늄합금 분말의 형 태 및 입도분포, 상분석결과를 나타내었다. Fig. 1(a)는 전 체적인 알루미늄 합금 분말의 표면사진으로 구형의 형상 을 가진 것을 알 수 있다. Fig. 1(b)는 구형 분말을 확대한 사진으로 구형분말의 표면에 작은 입도를 갖는 위성분말 이 일부 부착되어 있는 것을 확인 할 수 있었다. Fig. 1(c) 에는 Al-Si계 분말의 입도분포를 나타내었으며 D10, D50, D90은 각각 31, 44, 64 μm로 정규분포형태로 존재하는 것 으로 확인되었다. 특징적으로 20 μm 이하의 분말이 일부 존재하는 것을 함께 확인하였으며, 이들 분말의 양은 1~2% 수준으로 매우 적은 양이므로 분말 유동도 등에 큰 영향을 미치지는 않을 것으로 예상되었다. Fig. 1(d)는 분 말의 XRD 패턴을 나타내었으며 Al과 Si상이 주된 상으로 존재하는 것을 확인하였다.
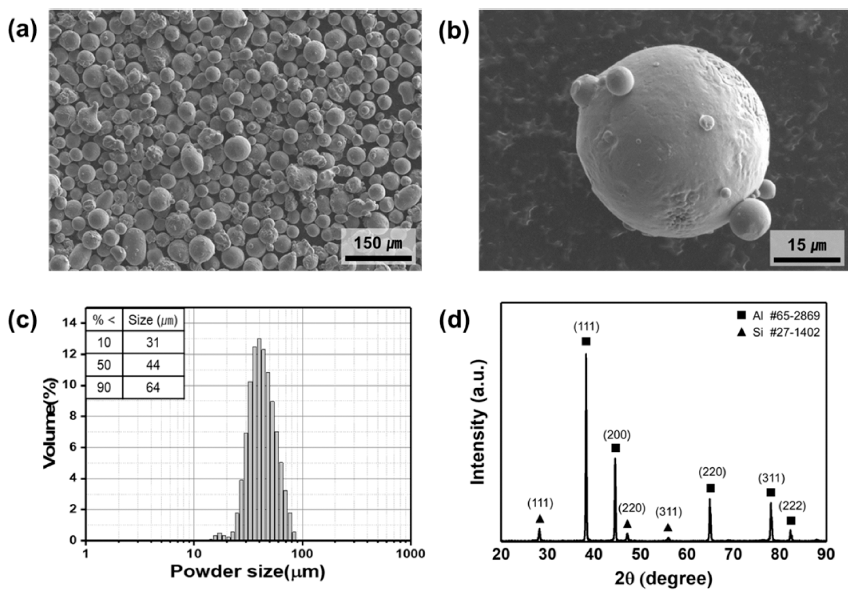
(a) Surface morphology in low magnification, (b) an SEM image of an individual particle, (c) particle size distribution and (d) XRD patterns of AlSi10Mg powder used in this study.
Table 1에는 본 연구에서 사용된 분말의 유동도(flow rate) 측정결과를 나타내었다. PBF 공정에서는 분말의 유 동도가 우수할수록 분말이 균일하게 적층되기 용이해지므 로 높은 유동도를 확보하는 것이 중요하다. 또한 겉보기밀 도와 탭밀도의 관계로부터 구할 수 있는 Hausner ratio는 PBF 공정에서 building chamber에 도포되는 분말의 충진 율을 예측할 수 있는 값으로 1에 가까운 수치를 가질수록 우수한 적층성(spreadability)을 갖는 것으로 알려져 있다. 본 분말의 유동도는 11.61, Hausner ratio는 1.41로 측정 및 계산되어 PBF 공정에 사용하기 적합한 분말임을 확인하 였다[16, 17].
Fig. 2(a)는 본 연구에서 사용한 적층 방식을 나타낸 모 식도이며 조형체의 미세조직은 적층 방향(z 방향)으로 관 찰하였다. Fig. 2(b)는 광학현미경으로 관찰한 미세조직을 나타내었다. 미세조직은 멜트 풀들이 서로 교차하여 적층 되어있는 것을 볼 수 있는 데, 이는 적층 제조 시 레이저 가 층마다 90도씩 회전하여 조사되기 때문에 생긴 것이다. Fig. 2(c)는 전자현미경으로 관찰한 멜트 풀(melt pool) 경 계의 미세조직을 나타내었다. 멜트 풀의 미세조직은 3가 지 영역으로 구분할 수가 있는데, 내부는 0.5 μm 이하의 입자로 구성되는 Fine cellular zone(FCZ)으로 구성되고 경 계영역은 1 μm 이상의 입자가 존재하는 Coarse cellular zone(CSZ)과 입자를 둘러싸고 있는 네크워크가 끊어진 형 태로 존재하는 Heat affected zone(HAZ)으로 구성된다. FCZ과 CCZ의 입자 크기의 차이는 냉각속도의 차이에서 발생하는데, 멜트 풀 내부의 냉각속도가 경계에서 보다 빠 르기 때문에 내부에 더 작은 입자가 형성되는 것이다. 또 한 멜트 풀 경계에 존재하는 HAZ은 인접한 두개의 멜트 풀 중에서 먼저 형성되어 있던 멜트 풀에 형성되는데 이 는 이미 응고된 영역 옆으로 레이저가 조사되면서 추가적 인 열을 받게 되어 입자의 형태가 변형된 것이다[18].
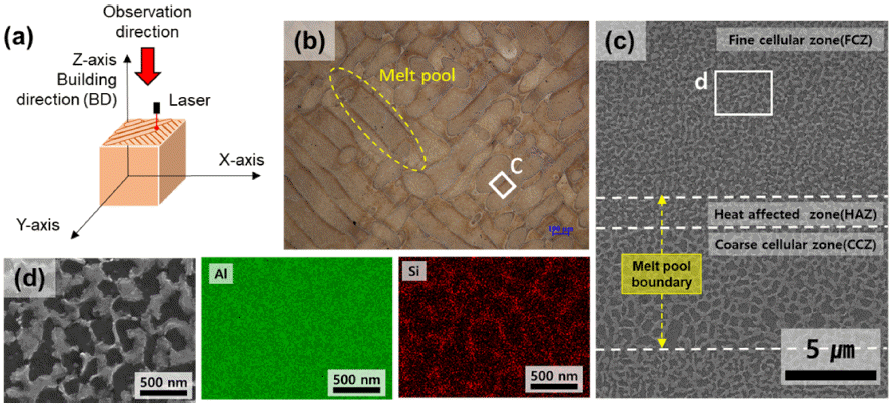
(a) Schematic illustration of building method and observation direction, (b) OM images on the etched XY plane of the as-built specimen, (c) SEM image of the white box of (b), and (d) EDS results of the white box of (c).
Fig. 2(d)에는 FCZ을 확대한 미세조직의 EDS 분석결과 를 나타내었다. 입자는 대부분 Al으로 구성되며, 입자를 둘러싸고 있는 경계는 Si이 다량 포함되어 있는 것을 확 인하였다. 이는 Al-Si계 합금이 급냉하여 응고될 때 발견 되는 미세조직 형상이며 Al-Si 공정상으로 보고된 바 있다 [19]. 따라서 이처럼 Al과 Si상 사이의 매우 높은 표면에 너지를 갖는 공정상은 열처리를 하였을 때 입자의 형상을 변화시키는데 있어서 큰 구동력을 제공해줄 것으로 기대 된다.
Fig. 3(a)는 조형에 사용된 분말과 조형체의 열처리하기 전과 후의 XRD 패턴 변화를 나타내었다. 열처리 유무에 관계없이 조형체의 주된 피크는 Al상과 Si상이라는 것을 알 수 있고 이는 조형전의 알루미늄 합금 분말과도 동일 하다는 것을 알 수 있다. Fig. 3(b)는 Fig. 3(a)의 빨간색 점 선으로 표시한 영역을 확대한 것이며 열처리 온도가 증가 함에 따라 Si상 피크의 강도가 증가하는 것을 알 수 있다. 보고된 연구결과에 따르면 SLM 공정으로 제조된 AlSi10Mg합금을 열처리하였을 때 Al 기지상에 순수한 Si 상이 석출되는 것을 확인한 바 있다[14]. 따라서 본 연구 에서 Si상 피크의 강도가 증가한 것은 SLM 공정 특성상 빠른 냉각속도에 의해 초정 Al상에 과고용 되어있던 Si이 열처리를 통해 일부 석출되었기 때문인 것으로 해석할 수 있다.
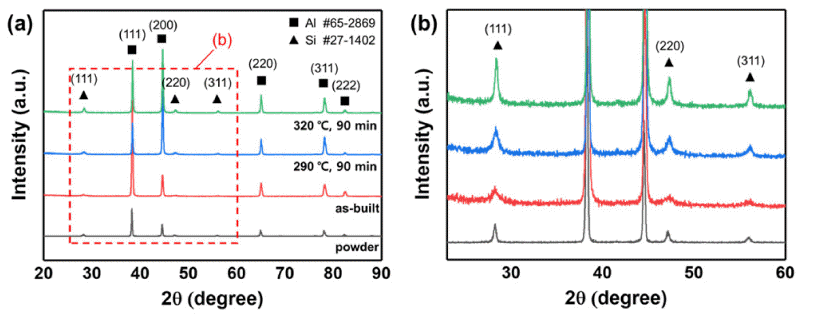
Comparison of XRD patterns (a) in the 2θ range of 20~90 and (b) on red-dotted region at (a) of the powders, as-built and heat-treated specimens.
Fig. 4(a)~(d)는 전자현미경으로 관찰한 조형체의 열처리 전후의 미세조직 변화를 나타내었다. 열처리 전 조형체의 미세조직은(Fig. 4(a)) 초정 Al상과 이를 네트워크형태로 둘러싸고 있는 Si-rich상으로 구성되어 있으나, 290°C에서 열처리한 경우(Fig. 4(b)) 초정 Al상 내부에 미세한 석출물 이 생성된 것을 확인하였고, Si-rich상이 일부 구형화가 진 행되어 네트워크의 연결이 불안정해진 것을 확인 할 수 있다. 300°C에서 열처리한 경우(Fig. 4(c)), 서로 연결되어 있던 Si-rich상의 네트워크가 끊어지고 대부분 구형화가 진행된 것을 확인하였다. 320°C에서 열처리한 경우(Fig. 4(d)), 300°C에서 열처리한 경우와 유사한 미세조직을 갖 는 것으로 확인하였다. 이처럼 연속적으로 네트워크를 이 루고 있던 Si-rich상이 불연속적으로 바뀌면서 조형체에 외부 인장력이 가해질 경우, 전위의 이동이 용이해지고 연 속적인 파단이 저해될 것으로 보인다.
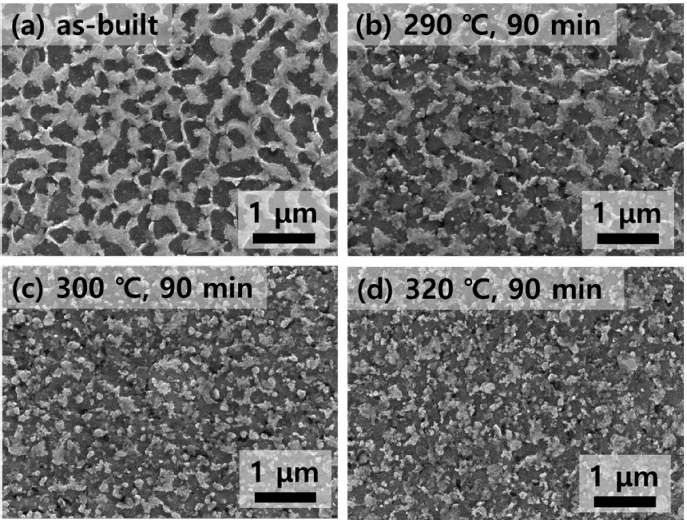
(a)~(d) SEM images of the fine cellular zones on the etched XY plane of the as-built and heat-treated specimens.
Fig. 5(a)는 인장시험에서 인장 방향과 조형체 미세조직 의 관계를 나타내었으며 인장방향은 레이저 스캔방향의 45°로 진행되었다는 것을 알 수 있다. Fig. 5(b)는 적층 직 후와 290, 320°C에서 열처리한 조형체의 인장시험에서 얻 어진 응력-변형률 곡선을 나타내었으며 각각의 인장시험 에서 네킹이 발생한 시점을 표시하였다. 적층 직후의 조형 체에서는 네킹 현상이 발견되지 않았지만, 290°C에서 열 처리한 경우 네킹 후 변형율이 1 % 증가한 후에 파단되 었으며, 320°C에서 열처리한 경우에는 네킹 후 변형율이 5% 증가한 후에 파단되었다. 또한 Fig. 5(b)의 응력-변형 률 곡선으로부터 진응력-진변형율 곡선을 구한 후에 각각 의 곡선의 갖는 가공경화지수(n)값을 도출하였고, 적층 직 후와 290, 320°C에서 열처리한 조형체의 n 값은 각각 0.182, 0.178 및 0.166인 것을 확인하였다. 따라서 열처리 온도가 증가함에 따라 조형체 내부에 전위의 이동을 방해 하는 요소가 감소한다는 것을 알 수 있다.
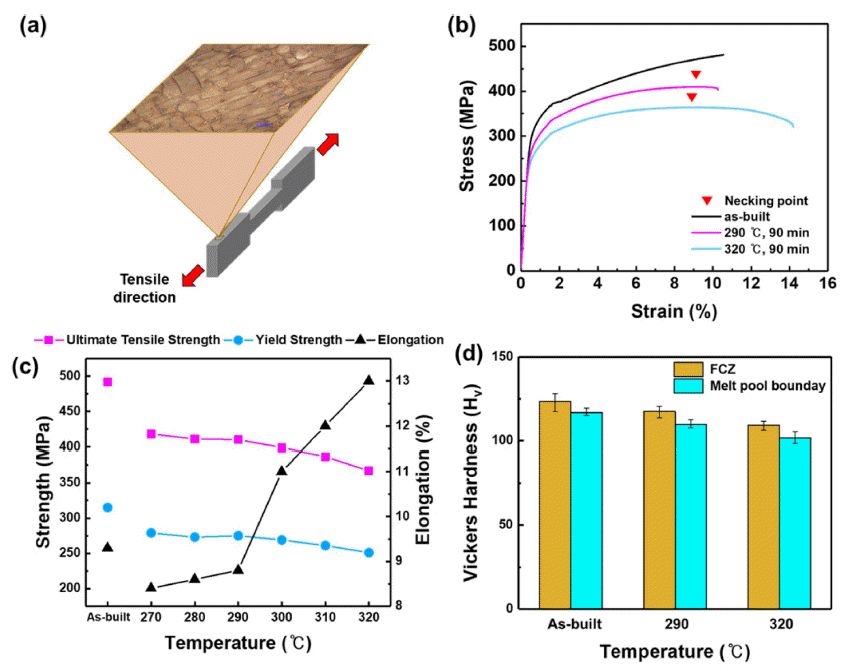
(a) Relationship between microstructure and tensile direction; (b) Room temperature tensile stress-strain curves of the as-built and heat-treated specimens; (c) Variation of strength and elongation values and (d) Comparison of Vickers hardness of fine cellular zone and melt pool boundary as a function of heat treatment temperature.
Fig. 5(c)는 인장시험을 통해 얻어진 조형체의 열처리 온 도에 따른 항복 및 인장강도, 연신율 변화를 나타내었다. 조형체의 인장 및 항복강도는 조형 직후 각각 492, 315 MPa로 가장 높았으며 열처리 온도가 270에서 320°C로 증 가함에 따라 비교적 일정하게 감소하였다. 조형체의 연신 율은 320°C에서 열처리한 경우 13%로 가장 높았으며, 연 신율의 증가율은 290에서 300°C로 열처리 온도를 증가한 경우 2.2%로 가장 크다는 것을 확인하였다. 이처럼 열처 리 온도가 증가함에 따라 강도가 감소하고 연신율이 증가 하는 현상은 Fig. 4에서 나타낸 바와 같이 조형직후 네트 워크를 이루고 있던 Si-rich상이 열처리 후에 불연속적으 로 끊어지는 정도와 관련이 있는 것으로 판단된다. 특히 열처리온도를 290에서 300°C로 증가하였을 때 Si-rich상이 불연속적으로 변화되는 정도가 가장 크다는 것을 통해 연 신율의 증가율도 가장 크다는 것을 설명할 수 있다.
270에서 290°C 사이에서 열처리한 경우에는 적층 직후 에 비해 오히려 연신율이 소폭 감소한 것을 확인 할 수 있 다. 기존 연구 결과에 따르면 SLM 공정으로 조형된 Al-Si 합금을 상대적으로 낮은 온도(160°C, 5 h)에서 열처리한 경우, Al 기지상에 needle 형태의 순수한 Si 상이 석출되 며, 비금속 Si상은 취성을 띄기 때문에 샘플의 연신율이 크게 감소한 것으로 보고된 바 있다[14]. 본 연구에서도 이와 마찬가지로 270에서 290°C에서 열처리한 경우, Sirich상 네트워크의 끊어짐에 의한 연신율이 증가할 수 있 지만, Al 기지상에 석출된 Si상 석출에 의한 연신율 감소 의 영향이 더 크기 때문에 조형 직후의 샘플보다 연신율 이 더 작은 것으로 판단된다.
Fig. 5(d)는 적층 직후와 290, 320°C에서 열처리한 조형 체의 비커스 경도 변화를 멜트 풀의 내부(FCZ)와 경계 (CCZ+HAZ)를 구분하여 나타내었다. 비커스 경도 값은 적층 직후 조형체의 경우 멜트 풀 내부와 경계가 각각 123과 117 Hv로 가장 높았으며 320°C에서 열처리한 경우 멜트 풀 내부 와 경계가 각각 109와 101 Hv로 가장 낮았 다. 열처리 유무에 관계없이 모든 시편의 멜트 풀 내부가 경계에 비해 경도가 큰 것을 확인하였다. 이는 멜트 풀 내 부가 경계보다 변형 저항성이 크다는 것을 의미하는데, Fig. 2(c)에서 볼 수 있듯이 멜트 풀 내부보다 경계의 입자 크기가 크기 때문인 것으로 해석할 수 있다. 또한 열처리 온도가 증가함에 따라 멜트 풀 내부와 외부 모두의 경도 값이 점차 감소하였으며 이는 열처리 온도가 증가함에 따 라 조형체의 변형 저항성이 감소된다는 것을 의미한다.
Fig. 6은 SLM 공정으로 제조된 Al-Si계 합금의 열처리 유무에 따른 Al 기지상 입자의 크기 및 외력이 가해질 때 발생하는 전위의 거동을 모식도로 비교하여 나타내었다.
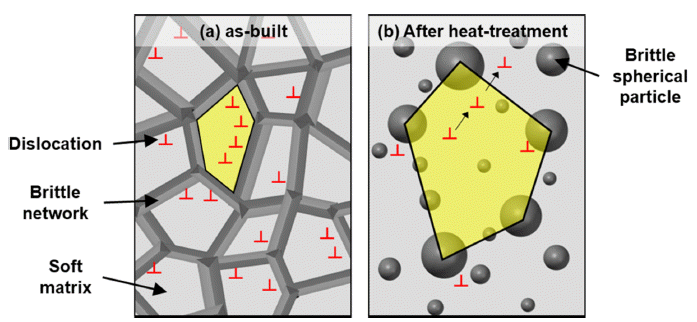
Schematic illustrations of comparison between as-built and post heat-treatment specimens on grain size & behavior of dislocations during tensile test.
Al 기지상의 입자 크기를 비교하면, 적층 직후(Fig. 6(a)) Al 기지상의 크기는 Si-rich상 네트워크에 둘러 쌓여 독립 적으로 존재하는 Al 기지상을 하나의 결정립으로 볼 수 있고, 열처리한 경우(Fig. 6(b))에는 Si-rich상의 연속적인 연결성이 없어지므로 상대적으로 조대한 크기의 Si-rich상 입자들을 연결한 선을 Al 기지상의 경계로 가정하였다. 여 기서 결정립크기와 항복강도를 Hall-Petch식에 의해 상관 관계를 가지며 그 식은 다음과 같다.
여기서 σy는 항복강도, σ0는 전위 이동을 방해하는 마찰 응력, Ky는 Hall-Petch 상수, d는 결정립의 크기를 나타낸 다. 본 연구에서는 Fig. 4에 나타낸 SEM Image에 선을 그 었을 때 포함되는 결정립계 수를 N으로 하고 그 선의 길 이를 L로 하였을 때, L/N로 계산한 값을 d 값으로 하여 대입하였으며, 300 및 320°C에서 열처리한 경우 Al 기지 상의 경계가 확실하지 않으므로 Si-rich상 입자의 길이가 1 μm 이상인 입자들을 결정립계로 가정하였다. 이를 바탕 으로 계산한 결과, 적층 직후와 290, 300 그리고 320°C에 서 열처리한 조형체의 평균 결정립 크기는 각각 0.5, 0.9, 1.0 및 1.1 μm로 도출해낼 수 있었다. 따라서 각각 조형체 의 항복강도와 계산한 평균 결정립 크기를 Hall-Petch 식 에 대입한 결과 σ0 = 194 MPa, Ky = 3.4·10-2MPa·m1/2의 값 을 도출할 수 있었으며 Fig. 7에 항복강도와 d-1/2의 관계 를 그래프로 나타내었다.
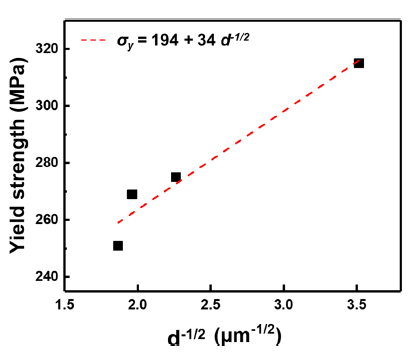
Relationship between yield strength and grain size for the as-built and post heat-treatment specimens.
또한 조형체에 외부 힘이 가해질 때 열처리 유무에 따 른 전위의 거동을 비교하였다. 적층 직후(Fig. 6(a)) 조형 체 내부의 전위는 상대적으로 변형이 쉬운 Al 기지상에서 주로 형성될 것으로 보인다. 생성된 전위는 Al 기지상 내 부에서 이동을 하다가 결정립계 역할을 하는 Si-rich상 네 트워크를 만나 이동이 저해될 것으로 보인다. 따라서 전 위가 계속 생성됨에 따라 Si-rich상 네트워크에 축적되므 로 응력이 계속해서 증가할 것으로 보인다. 이후 Si-rich 상이 응력 한계점에 달하면 네트워크가 끊어지면서 순간 적으로 파단이 발생할 수 있으므로 열처리하기 전 조형체 는 상대적으로 높은 강도와 낮은 연신율을 갖는 것으로 사료된다.
열처리하고 난 후(Fig. 6(b))에는 열처리하기 전과 마찬 가지로 Al 기지상에서 형성된 전위가 이동을 시작하지만, Si-rich상이 구상화 되어있으므로 전위의 이동이 비교적 원활할 것으로 보인다. 따라서 열처리한 경우, 외부 힘이 가해질 때, Fig. 3(c)에서 확인한 바와 같이 가공경화율이 감소하여 강도가 감소한 것으로 보이며, Si-rich 상의 연속 적인 파단의 위험이 감소하므로 높은 연신율을 갖는 것으 로 판단된다.
Fig. 8는 투과전자현미경으로 관찰한 조형체의 열처리하 기 전후 미세조직 변화 및 EDS 분석결과를 나타내었다. Fig. 8(a)는 열처리하기 전 조형체의 미세조직 사진이며, Al-Si 네트워크 주변과 Al 기지상 내부에 약 50 nm 이하 의 직경을 갖는 입자들이 미량 분포하는 것을 확인하였다. Fig. 8(b)는 320°C에서 열처리한 조형체의 미세조직 및 EDS 분석결과를 나타내었다. Fig. 8(a)에서 확인된 입자들 에 비해 입자 크기가 증가하였고 90 nm 이상의 직경을 갖 는 입자도 존재하는 것을 확인하였다. 또한 EDS 분석결과 조대화된 입자들은 Si상으로 구성되는 것을 확인하였다. 이는 열처리전 작은 크기의 Si 입자가 열처리 과정에서 Ostwald ripening 효과에 의해 조대화 된 것으로 보인다[20].
3. 결 론
본 연구에서는 SLM 공정으로 제조된 Al-Si계 합금의 후열처리에 따른 Si 형상 변화가 기계적 특성에 미치는 영 향에 대해 고찰하였다. 적층 직후의 조형체에는 레이저 용 융으로 인한 급속응고조직으로 Si-rich상이 네트워크를 형 성하는 미세조직을 보인다. 3차원 네트워크를 형성한 Si상 의 형상으로 인해 연질의 Al-Si 기지재료에서 외력에 의해 형성되는 전위가 Al/Si 계면에서 축적되기 쉬우므로 조형 체의 강도가 증가된 것으로 확인하였다. 급속응고로 형성 된 Si-rich 공정조직에 특정온도 이상으로 에너지를 공급 하는 후열처리공정이 진행되면 Al-Si기지재료내에 네트워 크를 이루던 Si-rich상이 입자 형태로 분리되어 존재하게 된다. 따라서, 후열처리공정만으로도 Si상의 형상을 불연 속적인 입자단위로 변화시킴에 재료에 인장응력이 가해질 경우, 전위의 이동이 용이해므로 항복 및 인장 강도가 감 소하지만, 연신율은 적층 직후에 비하여 상대적으로 증가 하는 것으로 판단된다.
감사의 글
본 연구는 산업통상자원부 전자시스템전문기술개발사 업 ‘3D 프린팅 전용 Al 소재 국산화 및 25% 경량 프런트 차체모듈 개발(과제번호: 20004486)’과제의 연구지원으로 수행되었습니다.