1차원 BaTiO3 나노튜브 어레이의 압전발전성능에 수열합성 반응 조건이 미치는 영향
Effect of Hydrothermal Reaction Conditions on Piezoelectric Output Performance of One Dimensional BaTiO3 Nanotube Arrays
Article information
Abstract
One-dimensional (1D) piezoelectric nanostructures are attractive candidates for energy generation because of their excellent piezoelectric properties attributed to their high aspect ratios and large surface areas. Vertically grown BaTiO3 nanotube (NT) arrays on conducting substrates are intensively studied because they can be easily synthesized with excellent uniformity and anisotropic orientation. In this study, we demonstrate the synthesis of 1D BaTiO3 NT arrays on a conductive Ti substrate by electrochemical anodization and sequential hydrothermal reactions. Subsequently, we explore the effect of hydrothermal reaction conditions on the piezoelectric energy conversion efficiency of the BaTiO3 NT arrays. Vertically aligned TiO2 NT arrays, which act as the initial template, are converted into BaTiO3 NT arrays using hydrothermal reaction with various concentrations of the Ba source and reaction times. To validate the electrical output performance of the BaTiO3 NT arrays, we measure the electricity generated from each NT array packaged with a conductive metal foil and epoxy under mechanical pushings. The generated output voltage signals from the BaTiO3 NT arrays increase with increasing concentration of the Ba source and reaction time. These results provide a new strategy for fabricating advanced 1D piezoelectric nanostructures by demonstrating the correlation between hydrothermal reaction conditions and piezoelectric output performance.
1. 서 론
압전 현상을 기반으로 하는 에너지 하베스팅 기술은 주 변의 소모성 에너지원인 진동 및 기계적 움직임을 전기 에너지로 변환이 가능하여 외부 전력원을 대체하는 차세 대 전력공급 기술로 여겨지고 있다[1-3]. 고성능의 압전 에너지 하베스터(Piezoelectric energy harvester) 구현을 위 해서는 우수한 유전특성과 열적 안정성 및 높은 전기-기 계 결합계수를 나타내는 페로브스카이트(Perovskite) 결정 구조의 압전세라믹(Piezoceramic)을 활용하는 것이 유리하 다[4, 5]. 특히, BaTiO3(Barium titanate)는 납을 함유하지 않아 환경 친화적이며, 저비용공정으로 생산이 가능할 뿐 만 아니라, 비교적 높은 압전성능을 나타낸다는 장점이 있 어, 많은 연구자들에 의해 관련 연구가 보고되고 있다[6-8].
최근에는 웨어러블한 형태의 전자기기에 대한 수요의 증가로 이러한 전자기기에 적용이 가능한 플렉서블 에너 지 하베스터 개발에 관한 관심이 급증하고 있으며, 압전 세라믹의 취성을 극복하여 에너지 하베스터를 개발하고자 하는 연구들이 다수 보고되고 있다. BaTiO3를 나노입자 (Nanoparticle), 나노선(Nanowire) 및 나노막대(Nanorod) 등의 나노분말 형태로 합성한 후 폴리머 기상(Matrix)에 분산시켜 제작한 압전 나노복합체 기반의 에너지 하베스 터를 개발한 연구 사례가 대표적이다[9-11]. 개발된 소자 는 높은 기계적 안정성을 나타내고 저비용의 스핀코팅 (Spin-coating) 공정으로 비교적 간단하게 제작될 수 있다 는 장점이 있는 것으로 알려져 있지만, 낮은 압전세라믹 분율과, 폴리머 기상에서의 응력 흡수로 인해 압전 에너지 변환 효율이 낮다는 한계가 존재한다[12, 13]. 또한, 1차원 나노구조체를 활용한 플렉서블 에너지 하베스터에 대한 연구도 진행되었다. BaTiO3 나노선 어레이(Nanowire arrays) 를 금속기판에 성장시켜 제작된 에너지 하베스터는[14] 나노복합체 기반의 소자와 비교하여 높은 압전 세라믹 분 율을 가지며, 기계적 응력이 소재에 집중되어 보다 높은 전기적 출력 성능을 보이지만, 나노선을 기판에 수직한 일 정한 방향으로 균일하게 배열하기 어렵고, 나노선의 길이 를 조절하기 어렵다는 한계를 가지고 있다[15]. 나노분말 및 나노선 어레이를 적용한 에너지 하베스터들의 단점을 극복한 BaTiO3 나노튜브 어레이(Nanotube arrays)를 활용 한 연구는 최근에 보고되고 있으며, 금속 기판에 수직 성 장된 TiO2 나노튜브 어레이를 수열합성 공정을 통해 BaTiO3 나노튜브 어레이로 변환하여 제작한 에너지 하베 스터는 기존의 나노구조체 기반의 소재가 갖는 소재 형상 조절 및 일방향 성장의 문제를 해결하여 우수한 성능의 플렉서블 압전 에너지 하베스터를 개발했다는 의미가 있 다[13, 15]. 하지만, BaTiO3 나노튜브 어레이 제조를 위한 반응조건이 압전 발전성능에 미치는 영향이 명확히 확인 되지 않았다는 한계가 있다.
본 연구에서는 다양한 수열합성 반응 조건에서 합성된 BaTiO3 나노튜브 어레이를 이용하여 에너지 하베스터를 제작하고, 전기적 발전성능을 평가 및 비교함으로써 수열 합성 반응조건이 BaTiO3 나노튜브 어레이의 압전발전성 능에 미치는 영향을 확인하였다. BaTiO3 나노튜브 어레이 합성을 위한 TiO2 템플릿은 다양한 조건으로 양극산화를 진행하고 형상을 분석하여, 최적의 TiO2 나노튜브 어레이 를 선정하였다. BaTiO3 나노튜브 어레이는 TiO2 템플릿을 서로 다른 몰 농도의 Ba(OH)2 용액과 반응시간 동안 200°C에서 수열합성을 진행하여 합성하였다. 압전 나노튜 브 어레이의 발전성능을 평가하기 위해, 하부와 상부 전극 으로는 Ti foil 기판과 나노튜브 어레이에 부착된 Al foil 을 각각 사용하였다. 하중 인가장치를 이용하여 다양한 수 열합성 조건을 이용하여 제작된 에너지 하베스터의 출력 성능을 평가한 결과 0.1 M의 Ba(OH)2 용액에서 6 hr 동안 수열합성을 진행한 소자에서 약 0.57 V와 9 nA의 가장 높 은 전압과 전류가 생성됨을 확인하였다.
2. 실험방법
2.1. BaTiO3 나노튜브 어레이 제조
BaTiO3 나노튜브 어레이는 양극산화 공정으로 TiO2 나 노튜브 어레이 템플릿을 성장시키는 공정과 수열합성 반 응을 통해 BaTiO3 나노튜브 어레이를 합성하는 2단계의 공정을 이용하여 제작하였다. TiO2 나노튜브 어레이를 성 장시키는 양극산화 공정의 개략도를 그림 1(a)에 나타내었 다. 초음파 세척된 3 cm × 3 cm 크기로 준비된 50 μm 두께 의 Ti 포일(Goodfellow, 99.6%)을 니켈 전극에 부착한 후, 0.1~0.2 wt% NH4F과 0.5~1 vol% DI water가 혼합된 Ethylene glycol 기반의 전해질 내에 니켈 음극 전극과 2 cm의 전극 간격을 두고 고정하였다. 그 후 자력 교반기를 이용하여 150 rpm으로 용액을 교반시키며, 소스미터 (Sourcemeter, Keithley 2612B)를 이용하여 40~60 V의 정 전압 조건에서 2.5 hr 동안 전기화학적 양극산화 공정을 진행하였다. 양극산화 이후 TiO2 나노튜브 표면의 잔여물 을 제거하기 위해 DI water 내에서 20 sec 동안 초음파 세 척을 진행하였다. BaTiO3 나노튜브 어레이는 액체 상태의 Ba소스를 고온, 고압환경에서 TiO2 나노튜브 어레이 내부 로 확산시키는 수열합성 반응법을 이용해 제조하였다. 준 비된 TiO2 나노튜브 어레이와 다양한 몰 농도(0.01, 0.05 및 0.1M)의 Ba(OH)2 수용액을 테플론 용기에 넣은 후, 합 성 공정 중 고압이 잘 유지될 수 있도록 잘 밀봉하고 수 열합성 반응기에 결합하였다. Ba(OH)2 수용액의 최대 몰 농도는 수열합성 공정에서 발생되는 침전물을 최소화하기 위해 설정하였다. 결합된 수열합성 반응기는 대류식 오븐 을 이용하여 200°C에서 각각 2, 4, 6 hr 동안 가열되며 수 열합성을 진행하였다. 합성이 완료된 BaTiO3 나노튜브 어 레이 표면에 존재하는 부산물을 제거하기 위해 DI water 내에서 30 sec 동안 초음파 세척 과정을 거친 후, 상온에서 충분히 건조시켜 BaTiO3 나노튜브 어레이를 완성하였다.
2.2. BaTiO3 나노튜브 어레이 기반의 압전 에너지 하베 스터 제작
수열합성 반응법을 통해 제조된 BaTiO3 나노튜브 어레 이를 이용하여 압전 에너지 하베스터를 제작하였다. BaTiO3 나노튜브 어레이가 성장된 Ti 기판을 하부전극으 로 직접 사용하고, Al foil을 2 cm × 2.3 cm 크기로 잘라 나 노튜브 어레이 윗면에 부착하여 상부전극으로 사용하였다. 압전 에너지 하베스터에서 생성되는 전기적 신호를 수집 하기 위하여 상/하부 전극에 각각 전도성 에폭시(Ag paste)를 이용하여 구리선을 연결하였다. 폴리메틸 메타크 릴레이트(Polymethylmethacrylate; PMMA)를 Anisole 용 액에 10 wt%로 혼합한 후, 에너지 하베스터에 코팅하여 Passivation을 진행함으로써 최종 BaTiO3 나노튜브 어레이 기반의 압전에너지 하베스터를 완성하였다. 또한, 제작된 에너지 하베스터의 압전특성을 극대화하기 위해 열과 고 전기장을 인가하여 압전 소재 내부의 쌍극자를 일정한 방 향으로 정렬시키는 폴링(Poling) 공정을 120°C, 10 kV/cm 의 조건으로 진행하였다.
2.3. 생성 전압 및 전류 신호 측정
제작된 압전 에너지 하베스터의 전기적 출력성능 평가 를 위해 자체 제작된 하중 인가 장치(Pushing machine system, SnM)를 이용하였으며, 변위(Displacement)를 조절 하여 하중을 인가하였다. 본 장치를 이용하여 규칙적이고 반복적으로 일정한 수준의 응력을 인가하였으며, 소자에 서 생성되는 전류와 전압 신호는 전위계(Electrometer, Keithley 6514)에 의해서 실시간으로 수집되어 PC에 기록 되었다.
3. 결과 및 고찰
그림 1(b)는 양극산화 공정을 통해 Ti 포일 위에 균일하 게 수직 성장된 TiO2 나노튜브 어레이를 보여 주고 있다. 그림 1(c)는 양극산화 공정 중 형성되는 TiO2 나노튜브 어 레이 생성 매커니즘의 모식도로, 양극산화 공정이 시작됨 에 따라 Ti 포일의 표면에 얇은 산화층이 형성되며, 두 전 극 사이에 인가되는 높은 전기장으로 인한 Electric field assisted dissolution과 Chemical dissolution에 의해 산화층 표면에 국부적 용해가 발생하여 나노 기공들이 형성되게 된다[16]. 이때 TiO2 층의 형성과 나노 기공 형성에 관한 화학반응식은 다음과 같다[16].
형성된 각각의 나노 기공 내부 곡면은 전기장이 집중되 기 때문에 전기화학반응에 의한 산화막 형성과 용해 반응 이 촉진되어 Ti 포일 내부로 길이방향 성장이 가속되는 반 면, 기공의 표면부는 전기장의 영향을 적게 받기 때문에 평 평한 산화막 표면에 구멍이 뚫린 상태를 이루게 된다[16, 17]. 이때, 양극산화 기공이 생성 및 성장하지 않은 공간의 경우 반응이 진행됨에 따라 Ti-F 복합물로 변화하여 기공을 둘러싸게 되는데, 이러한 복합물 층은 물에 쉽게 용해되어 기공 사이의 빈공간을 형성한다[17]. 이러한 반응은 양극 산화 공정에 의한 식각 속도와 용해의 속도가 동일해질 때 까지 진행되며 튜브의 최종 길이를 결정하게 된다[16].
그림 2는 양극산화 공정 최적화를 위해 공정에 이용되 는 전해질 조성 및 인가 전압을 변경하여 얻어진 나노튜 브 어레이의 표면 및 단면 주사전자현미경 (Scanning electron microscope, SEM) 이미지를 보여주고 있다. 그림 2(a)와 2(b)에서 나타나듯이 전해질 내의 0.1 wt% NH4F 조성의 전해질이 사용되었을 때 튜브 형상이 형성되지 않 은 반면, 0.2 wt% 조성에서는 명확한 TiO2 튜브 형상이 성 장되었음을 확인할 수 있다. 이는 전해질 내의 NH4F 함량 이 적을 경우 F- 이온에 의한 화학적 에칭이 불충분 하기 때문으로, F- 이온의 조절을 통해 나노튜브 어레이의 표면 형상, 직경 그리고 길이 형성에 영향을 줄 수 있음을 보여 주고 있다[18]. 또한 그림 2(c)와 2(d)에서 볼 수 있듯이 전 해질 내의 DI water 조성이 0.5 vol%에서 1 vol%로 증가 함에 따라 튜브 길이는 8 μm에서 15 μm로 증가하여 에너 지 하베스터로 적용될 때 보다 높은 성능을 보일 수 있는 최적화된 두께를 보였다. 이러한 결과는 H2O의 함량이 높 아질수록 전해질에서 금속 산화층으로 이동하는 O2- 이온 의 양이 증가하여 산화층 형성에 유리해지기 때문이며, H2O의 비율이 과도하게 높아질 경우 H+ 이온의 증가로 용해가 더욱 가속화되어 나노튜브 어레이의 길이가 감소 할 수 있다[19]. 그림 2(e)는 Ti 포일을 최적화된 조성의 전해질을 내에서 40 V의 전압을 인가하며 양극산화 공정 을 진행하였을 때 생성된 나노튜브 어레이를 보여주고 있 다. 형성된 나노튜브 어레이는 동일한 전해질에서 60 V로 양극산화 된 튜브 어레이보다 작은 직경과 짧은 길이인 약 50 nm 직경의 기공과 6 μm의 튜브 길이를 보였는데, 이는 전기장이 이온이동 및 나노튜브 형성 구동력의 증가 에 영향을 주기 때문으로, 인가 전압을 증가시킴에 따라 튜브 직경의 크기와 길이가 비례하여 증가함을 나타낸다. 결론적으로, 최적화된 형상의 TiO2 나노튜브 어레이는 0.2 wt% NH4F와 1 vol% H2O를 포함하는 Ethylene glycol 기 반의 전해질 내에서 60 V의 전압을 인가하며 양극산화를 진행하였을 때 형성됨을 확인하였다.
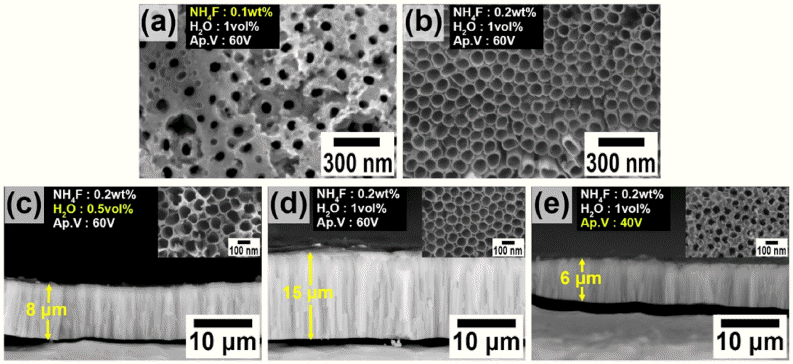
(a-b) Top-view images of scanning electron microscope (SEM) images of TiO2 nanotube arrays onto Ti foils from weight fraction of NH4F in electrolyte. (a) NH4F 0.1 wt% and (b) NH4F 0.2 wt%. (c-e) Cross-sectional SEM images of TiO2 nanotube arrays from volume fraction of H2O in electrolyte and applied voltage. (c) H2O 0.5 vol% (d) H2O 1 vol%, (e) Applied voltage : 40 V. The insets show top-view images of each nanotube arrays.
최적화된 조건의 TiO2 나노튜브 어레이를 수열합성반응 을 통해 BaTiO3로 합성하는 메커니즘 모식도를 그림 3(a) 에 나타내었다. 수열합성에 의한 BaTiO3 나노튜브 합성 공정은 크게 (1) TiO2 나노튜브 표면에서의 순간-전이기구 (in-situ reaction)과 ( 2) Ba2+ 이온의 내부 확산의 두 단계 로 구성된다[20, 21]. 수열합성 반응이 시작되면 Ba(OH)2 용액으로부터 제공된 Ba2+와 Ba(OH)+이온은 TiO2 튜브 표면에서 반응을 하여 BaTiO3 위치를 형성하게 되고 측면 성장 및 확산을 통해 튜브 표면에 걸쳐 BaTiO3 층을 형성 한다[20]. 합성이 진행됨에 따라 튜브 표면의 TiO2가 고갈 된 후 제공되는 추가적인 Ba2+ 이온은 TiO2 벽 내부로 확 산하여 형성된 나노튜브 전체를 BaTiO3로 치환한다[21]. 그림 3(b)에서 3(f)는 수열합성 온도를 200°C로 고정한 후 Ba(OH)2의 몰 농도와 수열합성 시간을 변화시켜 제작한 BaTiO3 나노튜브 어레이들의 실제 사진을 보여주고 있다.
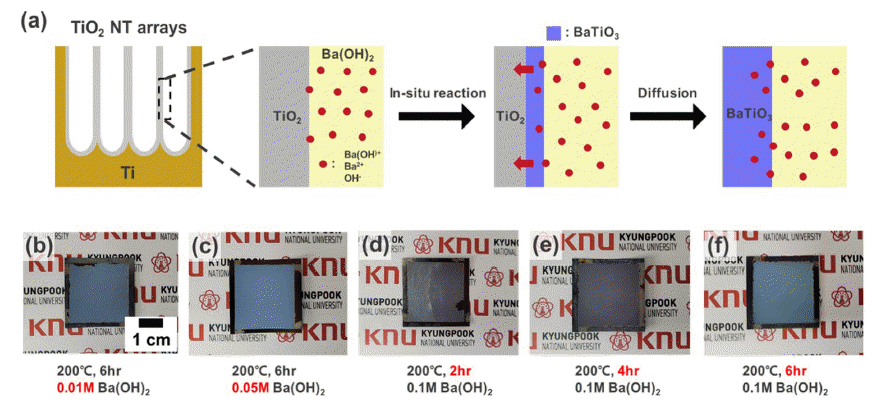
(a) A schematic diagram of the conversion steps to BaTiO3 nanotube arrays from TiO2 nanotube arrays by hydrothermal reaction. (b-f) Actual images of BaTiO3 nanotube arrays fabricated by several conditions of molarity of Ba(OH)2 and hydrothermal synthesis time.
그림 4(a)는 BaTiO3 나노튜브 어레이의 X선 회절(X-ray diffraction, XRD) 분석 결과를 보여주고 있으며, 전형적인 페로브스카이트 구조의 BaTiO3의 피크들과 일치하고 있 음을 통해 본 실험에서 합성된 나노튜브가 잘 결정화 되 었음을 확인할 수 있었다. 그림 4(b)는 0.1 M Ba(OH)2, 200°C, 6 hr의 조건으로 합성된 BaTiO3 나노튜브 어레이 의 표면 형상을 보여주고 있으며, 양극산화가 진행된 전체 영역에 걸쳐서 약 82 nm의 내경과 130 nm의 외경을 갖는 균일한 BaTiO3 나노튜브 어레이로 합성되었음을 확인 할 수 있다.
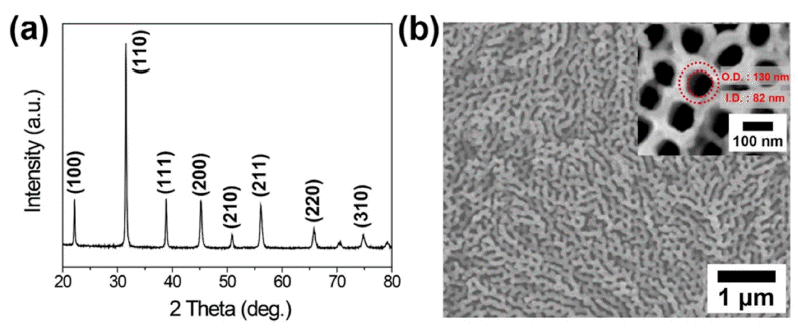
(a) X-ray diffraction (XRD) pattern of BaTiO3 nanotube arrays onto a Ti foil. (b) Top-view SEM image of the BaTiO3 nanotube arrays. The inset shows the magnified SEM image of a single BaTiO3 array to observe its detailed dimension.
다양한 수열합성 조건을 이용하여 제작된 BaTiO3 나노 튜브 어레이들의 압전 발전성능을 실험적으로 비교하기 위해 각각의 나노튜브 어레이를 이용한 에너지 하베스터 를 제작하고 전기적 출력성능을 측정 및 비교하였다. 그림 5(a)는 BaTiO3 나노튜브 어레이를 이용한 에너지 하베스 터 제작공정의 모식도를 보여주고 있으며, 자세한 제작공 정은 실험방법에 기술하였다. 제작된 에너지 하베스터의 성능평가는 하중인가 시스템을 이용하여 반복적이고 규칙 적으로 약 75.2 N의 하중이 인가되는 조건에서 진행되었 으며 (그림 5(b)), 각각의 소자에서 발생된 출력 전압 값을 그림 5(c)와 5(d)에 요약하였다. 그림 5(c)는 0.1M로 동일 한 Ba(OH)2 몰 농도 조건에서 수열합성 반응시간이 각각 2, 4, 6 hr로 증가함에 따라 변화하는 BaTiO3 나노튜브 어 레이 기반 에너지 하베스터의 출력신호 값을 보여준다. 출 력 전압은 합성 시간이 2 hr에서 6 hr로 증가함에 따라 약 0.2 V에서 0.57 V로 2.85배 증가하였는데, 이는 Ba2+ 이온 이 비압전성 TiO2 나노튜브 내부로 충분히 확산되어 압전 특성을 갖는 BaTiO3로 치환되었기 때문으로 판단된다 [21]. 그림 5(c)에 삽입된 그래프는 6 hr 조건으로 합성된 나노튜브 어레이 소자에 하중이 인가됨에 따라 주기적으 로 발생한 실제 전압 및 전류 신호를 보여주고 있다. 그림 5(d)는 6 hr의 동일한 수열합성 시간에서 Ba(OH)2 용액의 몰 농도를 0.01, 0.05, 0.1 M로 변경함에 따라 변화하는 소 자의 출력 전압 값으로 농도가 증가함에 따라 0.15 V에서 0.57 V로 증가하는 경향을 확인할 수 있다. 이는 Ba2+의 양이 증가함에 따라 수열합성 반응의 구동력인 농도구배 가 커지게 되어 확산이 잘 일어나며, 더 많은 TiO2를 BaTiO3로 치환할 수 있기 때문으로 사료된다[22].
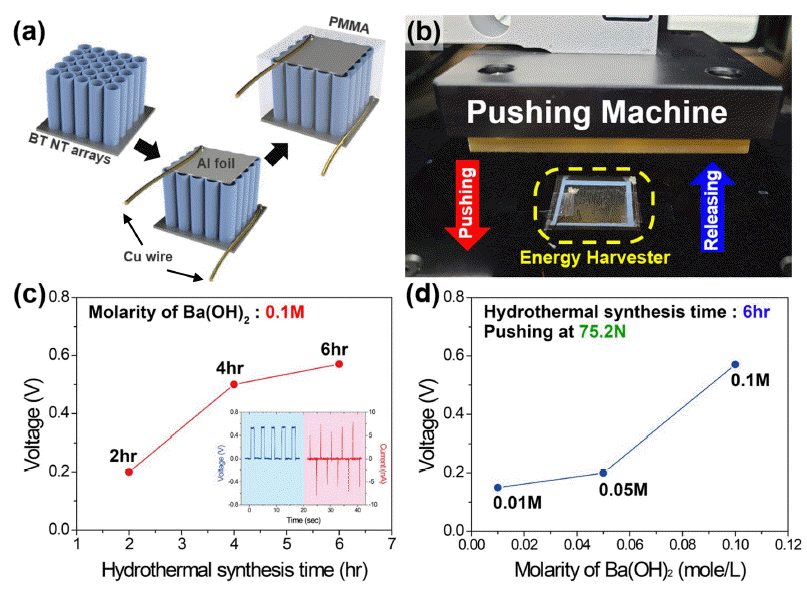
(a) A schematic illustration showing fabrication steps of an energy device for characterizing the piezoelectric output signals converted from BaTiO3 nanotube arrays. (b) Photographs of the pushing/releasing states of a BaTiO3 nanotube arraysbased energy harvester during output measurement. (c) The generated output voltages from energy harvesters fabricated by different hydrothermal synthesis time of 2, 4, and 6 hours. The inset shows output voltage and current signals harvested from an energy harvester based on the optimized BaTiO3 nanotube arrays. (d) The generated output voltages from energy harvesters fabricated by different molarity of Ba(OH)2 of 0.01M, 0.05M, and 0.1M.
4. 결 론
본 연구에서는 합성 공정 조건을 변경하여 다양한 조건 의 BaTiO3 나노튜브 어레이를 합성하고 형상을 분석하였 으며, 이를 이용하여 압전 에너지 하베스터를 제작하여 발 전성능 평가를 함으로써 나노튜브 어레이 제작 공정을 최 적화하였다. Ti 포일을 0.2 wt% NH4F, 1 vol% H2O를 포함 한 Ethylene glycol 기반의 전해질에 담근 후, 60 V의 일정 한 전압을 인가여 양극산화를 진행할 경우 약 82 nm의 직 경과 15 μm 길이로 TiO2 나노튜브 어레이가 형성됨을 확 인하였다. 또한, Ba(OH)2용액의 몰 농도와 합성시간을 변 화시키며 수열합성을 진행하여 얻은 다양한 조건의 BaTiO3 나노튜브 어레이를 이용하여 압전 에너지 하베스 터를 제작하였다. 제작된 각각의 에너지 하베스터에 약 75.2 N의 일정한 하중을 반복적으로 가하여 생성되는 전 압/전류 신호를 측정한 결과, 0.1 M Ba(OH)2 용액을 사용 하여 6 hr 동안 수열합성 반응을 진행했던 소자에서 약 0.57 V과 9 nA의 최대 전압 및 전류가 생성됨을 확인하였 다. 최적화된 BaTiO3 나노튜브 어레이를 제작함으로써 1 차원 압전나노소재 연구와 이를 이용한 에너지 하베스터 의 연구 방향에 비전을 제시할 것으로 기대되며, 소자 구 조 설계와 폴링 조건 최적화 등의 추가실험을 통해 발전 성능의 향상이 가능할 것으로 생각된다.
감사의 글
이 논문은 2021년도 정부(과학기술정보통신부)의 재원 으로 한국연구재단의 지원을 받아 수행된 연구임(No. 2019R1I1A2A01057073, No.2021R1A4A2001658).