X-ray tomography 분석과 기계 학습을 활용한 금속 3D 프린팅 소재 내의 기공 형태 분류
Characterization and Classification of Pores in Metal 3D Printing Materials with X-ray Tomography and Machine Learning
Article information
Abstract
Metal three-dimensional (3D) printing is an important emerging processing method in powder metallurgy. There are many successful applications of additive manufacturing. However, processing parameters such as laser power and scan speed must be manually optimized despite the development of artificial intelligence. Automatic calibration using information in an additive manufacturing database is desirable. In this study, 15 commercial pure titanium samples are processed under different conditions, and the 3D pore structures are characterized by X-ray tomography. These samples are easily classified into three categories, unmelted, well melted, or overmelted, depending on the laser energy density. Using more than 10,000 projected images for each category, convolutional neural networks are applied, and almost perfect classification of these samples is obtained. This result demonstrates that machine learning methods based on X-ray tomography can be helpful to automatically identify more suitable processing parameters.
1. 서 론
금속 3D 프린팅은 차세대 제조 기술로 주목받고 있는 기술로 다양한 산업분야에 빠르게 확산되고 있다. 특히, 항공, 의료 분야를 중심으로 기존 제조 방법으로 제작할 수 없는 적층 제조 특화 설계 기술을 통해서 새로운 가치 를 가진 소재, 공정, 제품의 영역으로 확장되고 있다. 적층 제조 방법은 균일한 소재에서 시작하는 종래의 절삭가공 기술과 다르게 다양한 크기와 형상 분포를 가진 다수의 금속 분말을 레이저로 용융 시켜 만드는 방식으로 기공과 같은 결함이 공정 조건에 따라 동반되기 용이하다. 이러한 기공은 적층제조물의 밀도를 떨어트리고 기계적 물성을 크게 저하시키는 것으로 보고되고 있다[1, 2].
적층 제조 밀도를 높이기 위해서는 레이저의 파워 및 스 캔 속도, 적층 높이, 적층 간격 등 공정 변수를 조절하여 개선할 수 있으며, 최적의 기계적 물성을 얻기 위해서는 위의 공정 변수를 통해서 단위 면적과 시간에 들어가는 에너지의 총량을 계산한 레이저 에너지 밀도를 주요 변수 로 경향성을 나타낸다고 알려져 있다. 에너지 밀도가 낮을 경우, 금속 분말이 충분히 녹지 않아 “unmelt” 상태가 되 며, 에너지 밀도가 높은 경우에는 기체가 용융풀 내에 고 립되면서 조형체의 밀도가 떨어지게 된다. 이를 분류하는 방법으로 “unmelt”, “proper”, “over-melt”의 3가지 단계로 분류할 수 있으며 시편 비파괴 검사를 통해서 밀도를 높 일 수 있는 새로운 공정 조건의 방향을 제시할 수 있다.
최근 연구에서는 실시간 비파괴 검사 등을 통해서 결함 을 실시간으로 예측하고 최적 공정 조건을 찾고자 하는 연구가 빠르게 진행되고 있다. 특히, X-ray CT이미지와 전산유체해석 시뮬레이션을 기반으로 적층 제조 장치 내 에 탑재하여 제조 중 발생하는 용융풀과 내부 기공을 관 찰, 예측하는 연구가 다수 진행되고 있다[3-6]. 하지만, 이 러한 논문에서는 적층 제조 공정 중의 짧은 시간과 영역 만을 관찰하고 판단하는 기술이며, 산업적인 측면에서는 대표성을 가진 형태로 접근하기는 어렵다. 또한 금속 3D 프린팅의 경우에는 공정 조건에 다양한 변수가 적용되므 로 에너지 밀도로 구성된 단순화된 지표를 기초로 하여 적층 제조 데이터를 확보할 필요가 있다.
적층 제조 기술을 인공지능을 적용하는 방법은 다양한 분야에서 제안되고 있다. 분말의 종류를 광학 현미경 이미 지를 기반으로 하여 분류하는 모델을 개발한 사례부터 공 정 조건을 최적화하기 위한 신형 알고리즘의 적용 등이 최근 연구되고 있다[7]. 이러한 연구 사례는 새로운 공정 조건을 빠르게 검토할 수 있는 방법을 고속으로 찾을 수 있는 방법을 제시하고 있으며, 향후 인공지능 기술의 진입 장벽이 낮아지고, 신뢰성이 높은 적층 제조 연구 기술이 확보됨에 따라서 적층 제조 기술과 인공지능 기술은 융합 되어 더욱 발전할 것이다.
본 논문에서는 결함 발생 시점을 실시간으로 관찰할 수 는 없지만, 적층 제조 공정 조건에 따른 대면적의 결함 구 조를 X-ray CT를 통해서 관찰하고 유사성이 큰 이미지를 대량으로 수집하여 기계 학습을 통해 에너지 밀도의 적정 여부를 판단하는 인공지능 모델을 제시하고자 한다. 이를 위해서 3종류의 에너지밀도에 따른 분류(“unmelt”, “proper”, “over-melt”)를 기반으로 하여 간단한 모델 실험을 수행하 였으며, X-ray CT를 통해서 얻어진 다수의 이미지를 기반 으로CNN 구조의 기계 학습 모델을 구축하여 평가하였다.
2. 실험 방법
본 실험을 위해서 상용 순수 티타늄 분말(Commercially pure titanium, CP-Ti, LPW 사)를 사용하였으며, 해당 분말 의 밀도 및 유동 특성은 Table 1과 같다. 유동도는 균일한 파우더 베드를 형상하는데 중요한 영향을 미친다. 본 실험 에 사용된 분말은 3D 프린팅용으로 적층 제조를 하기에 충분한 Ø2.54(FRH,)홀을 이용하여 50 g 기준의 이동속도 는 27 s 정도이며, 대표적인 유동 관련 평가 지표인 Hausner ratio(HR: 충진 밀도와 겉보기 밀도의 비)가 1.07로 흐름성 이 좋은 분말을 활용하였으며, Fig. 1에서 살펴보는 바와 같이 10~45 μm 입도를 가진 구형의 분말 형상을 가지고 있어 Powder Bed Fusion(PBF)방식의 3D 프린팅용으로 적합하다고 판단된다[8-11]. 레이저 파워와 스캔 속도가 상이한 15개의 시편을 PBF 방식의 금속 3D 프린터(Metal 3D printer, Mlab, Concept Laser 사)을 활용하여 제조하였 다. 금속 3D 프린팅 주요 공정 변수인 레이저 출력(laser power: 50 W, 70W, 90W) 및 조사 속도(Scan speed: 300~700 mm/s, 50 mm/s 간격)으로 변화시켜 실험하였고, 적층 제조 공정 중의 레이어 두께와 해칭 거리, 오버랩 (Layer thickness: 25 μm, Hatching distance: 80 μm, Overlap: 30%)은 유지하였다.
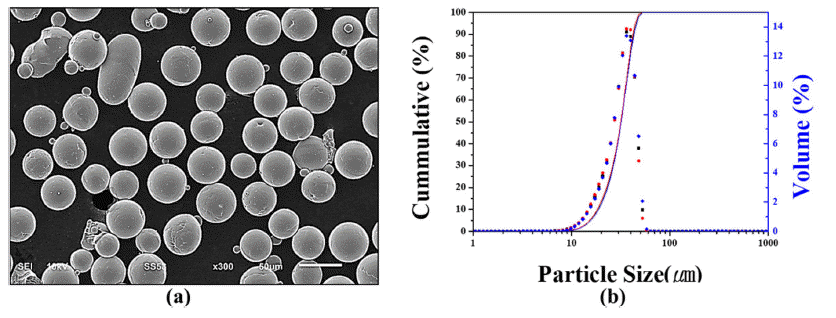
Commercial pure titanium powder characteristics; (a) Scanning electron micrograph (SEM) image; (b) Chart of particle size distribution.
제조된 시편은 아르키메데스 원리를 이용하여 조형체 밀도를 측정하였다. 또한, 적층면에 수평인 방향으로 광학 현미경(Optical microscope, ECLIPSE MA200, NIKON 사) 을 활용하여 Fig. 2와 같이 전체 이미지를 검사하였다. 기 존에 잘 알려져 있는 바와 같이 레이저의 파워가 충분하 지 않고, 스캔 속도가 빠른 경우에 분말이 충분이 용융되 지 못해 연결된 형태의 기공이 생기는 시편을 관찰할 수 있었다. 기공의 3차원 비파괴 분석을 위해서는 X선이 충 분히 투과가 되어야 하기 때문에 본 연구에서는 우선 가 장 밀도가 낮는 조형체를 대상으로 3차원 X-선 이미지 시 스템(X-ray tomography analysis, Xradia Ultra, Zeiss 사)분 석을 수행하였으며, 투과성 향상을 위해선 10 mm× 2 mm × 2mm의 막대 형상으로 가공하여, 기공의 형태에 대한 정밀도 평가를 수행하였다. 본 연구에 사용된 X-ray CT장 치는 회전판 위에 시편을 위치시켜 각도를 다르게 하여 투과된 이미지로부터 3차원 재조합을 통해서 내부의 밀도 차를 측정하는 방식을 사용하였으며, Ti 조형체와 기공 사 이의 밀도 차이를 정량화할 수 있다. 700 mm/s, 50W로 제작된 시편의 광학 이미지와 3차원 이미지를 비교하여 기공 구조의 유사성을 검토하였으며, 해당 방법이 유효함 을 확인하였다. 단, 밀도가 높은 경우 기공의 구조를 밀도 차이로 분석하는데, 밀도가 낮은 탄화물 등이 3차원 이미 지 상에 기공으로 분류될 수 있다는 점을 고려하여 이미 지 분석 결과는 2차원으로 확인된 이미지와 비교 검토할 필요가 있다.
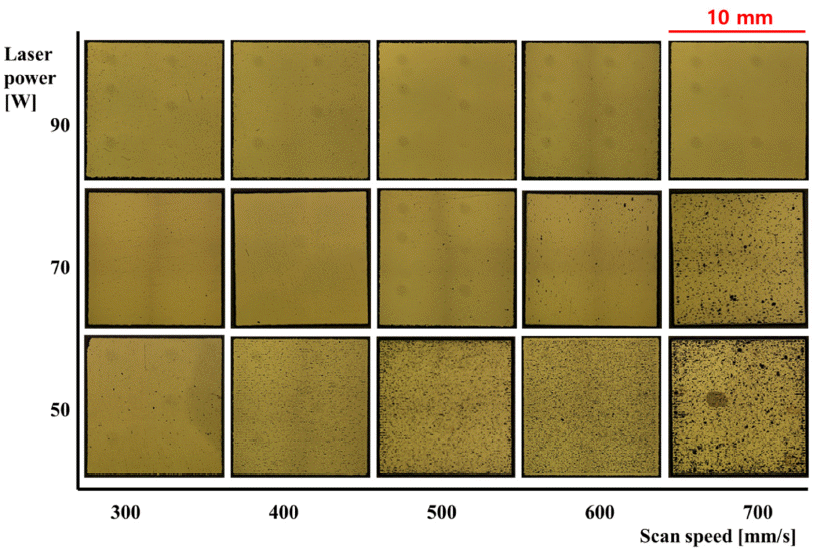
Optical microscope images of samples by additive manufacturing process parameters; Laser power (50, 70, 90W), Scan speed (300, 400, 500, 600, 700 mm/s).
수집한 3차원 이미지를 정량화하여 평가하기 위해서 슬 라이스된 이미지를 기반으로 정보 처리를 수행하였다. 본 연구에서는 1장의 3차원 이미지는 1000장의 단층 이미지 로 구성되어 있으며, 각 이미지의 픽셀 사이즈는 256×256 으로 되어 있다. 해당 이미지로부터 제품 샘플이 포함된 부분을 Crop하여 Artifact가 없는 내부 이미지를 추출하였 고, 조형체의 끝부분에서 생기는 회절 패턴 등으로 분석에 용이하지 않은 부분은 제거하여 700장의 조형체 단층 이 미지를 수집하였다. 해당 이미지는 Random Crop, Contrast/ Brightness 조절 등을 통한 이미지 증강 기법으로 10,000 장의 기계 학습용 이미지화 되었으며, 해당 이미지의 초기 5,000장을 기계학습 모델을 위해서, 2,000장을 학습 정도 를 평가하는 용도(Validation)로, 나머지를 3,000장을 모델 성능 평가에 활용하였다. 이러한 기계 학습을 위해서 NVIDIA사의 GeForce 2080 Ti를 장착한 GPU 연산을 수 행하였고, 기계학습용으로 공개되어 있는 PyTorch라이브 러리를 활용하여 평가하였다. 이미지는 3차원 기공의 형 태와 상관관계가 큰 에너지 밀도를 중심으로 “unmelt”, “proper”, “over-melt” 분류하여 평가하였다.
3. 결과 및 고찰
3.1. 공정 변수와 조형체 밀도, 기공의 형상과의 상관관계
적층 제조 공정에서 기계적 특성에 크게 영향을 주는 주 요 공정 변수는 레이저 출력과 레이저 조사 속도이며, 레 이저 출력이 높고 조사 속도가 느릴수록 에너지 밀도가 높으며, 충분한 에너지 밀도가 있어서 금속 분말의 용융이 이루어져서 고밀도의 조형이 가능함을 확인할 수 있다.
CP-Ti 조형 샘플의 레이저 출력과 조사 속도에 따른 아 르키메데스 원리로 측정한 밀도(g/cm3)와 상대 밀도(%)를 Table 2에 나타냈다. 레이저 출력 50W에서는 300 mm/s 에서 4.439 g/cm3으로 가장 높은 밀도를 가졌고, 반대로 700 mm/s에서 3.886 g/cm3로 가장 낮은 밀도를 가지므로, 조사 속도가 높아질수록 충분한 용융이 이루어지지 않아 밀도가 낮아짐을 알 수 있었다. 70 W에서는 500 mm/s에 서 4.479 g/cm3 밀도가 높게 나타났으며, 300 mm/s와 700 mm/s에서는 각각 그보다 낮은 4.446 g/cm3, 4.293 g/cm3 값 을 가졌다. 90W에서는 550 mm/s에서 4.485 g/cm3로 가장 높은 밀도를 보였으며, 300~650 mm/s 속도 전체적으로 50 W, 70W 레이저 출력에서의 시편 밀도 보다 높은 밀도 값을 가짐을 알 수 있었다. 이는 이미 알려진 바와 같이 적층 제조 공정을 위한 processing window가 존재하며 이 를 정량적으로 예측하기 위한 연구가 소재 별로 이루어지 고 있다.
적층 제조 공정 최적화 과정에서 공정 변수 설계 및 제 어는 레이저 에너지 밀도를 기준으로 정한다. 레이저 에너 지 밀도는 다음과 같은 공식으로 나타낸다.
레이저 에너지 밀도(Laser energy density)는 레이저 출 력(laser power)에 비례하는 관계에 있으며, 레이저 조사 속도(Scan speed), 해칭 거리(Hatch spacing), 레이어 두께 (Laser thickness)와는 반비례 관계에 있다. 조형체의 밀도 와 레이저 에너지 밀도와의 관계는 Fig. 3(a)에서와 같이 나타낼 수 있다. 해칭 거리와 레이어 두께는 동일한 값을 적용했기 때문에 레이저 출력을 스캔 속도를 나눈 값을 X 축으로, 조형체의 밀도를 Y축으로 그래프를 작성하였다. 50 W에서는 에너지 밀도가 증가함에 따라 조형체의 밀도 가 증가했다. 70 W에서는 전체적으로 50W 조형체의 밀 도보다 높은 수치를 보였고, 500 mm/s에서는 가장 높은 밀도를 나타냈다. 90 W에서 레이저 에너지 밀도 증가에 따른 조형체의 밀도는 매우 비슷한 수치의 높은 밀도를 가지나, 높은 레이저 출력으로 과 용융 되었을 가능성이 있으므로 예상된다. 그러므로 X-ray tomography을 통해 3 차원 이미지 분석으로 기공의 형태를 파악하는 것과 에너 지 밀도의 관점에서 기공을 특성화 하는 것은 중요하다.
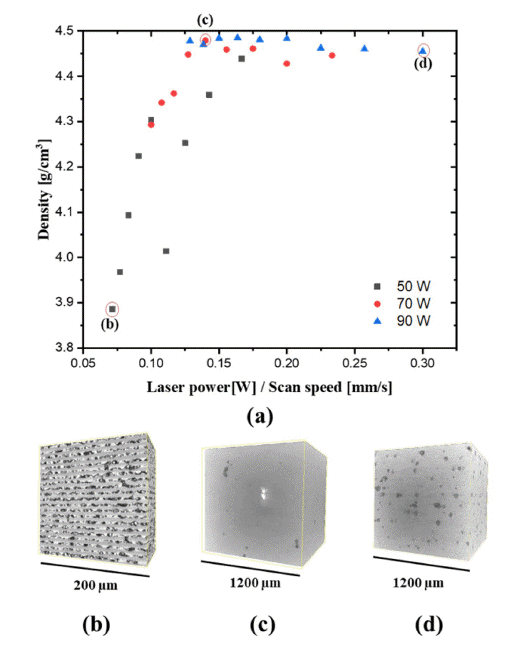
Relationship between energy density and density of 3D printing samples and X-ray tomography 3D images; (a) Energy density - Density of samples graph (b) 50W 700 mm/s (c) 70 W 500 mm/s (d) 90 W 300 mm/s samples.
적층 제조물의 기공은 기계적 물성에 큰 영향을 미친다. 특히, 바늘 형태의 기공은 크랙의 생성점으로 작용하여 피 로 성능이 크게 약화되는 등 기공의 형상을 정량적으로 살펴보는 것은 매우 중요하다. 3가지 조건의 조형체 X-ray 분석 결과를 기공의 크기 및 분포를 계산하여 Fig. 4에 표 시하였다. 에너지 밀도가 낮은 경우에는 분말이 제대로 녹 지 않고 부분적으로 용융된 형태로, 기체의 이동이 가능한 채널형 구조로 기공이 형성됨을 알 수 있었고, 정량화 하 였을 때도 적층 제조 양상에 따라 다양한 크기의 기공이 존재하는 것을 확인할 수 있다. 고밀도의 조형이 가능한 레이저 파워 70W, 스캔 속도 500mm/s에서는 15 μm 이 하의 기공으로 구성되어 있으며, 에너지 밀도가 높은 조건 (90 W, 300 mm/s)에서는 16~25 mm 크기의 기공이 형성되 었고, 70W에 비해 기공의 개수도 많음을 알 수 있다.
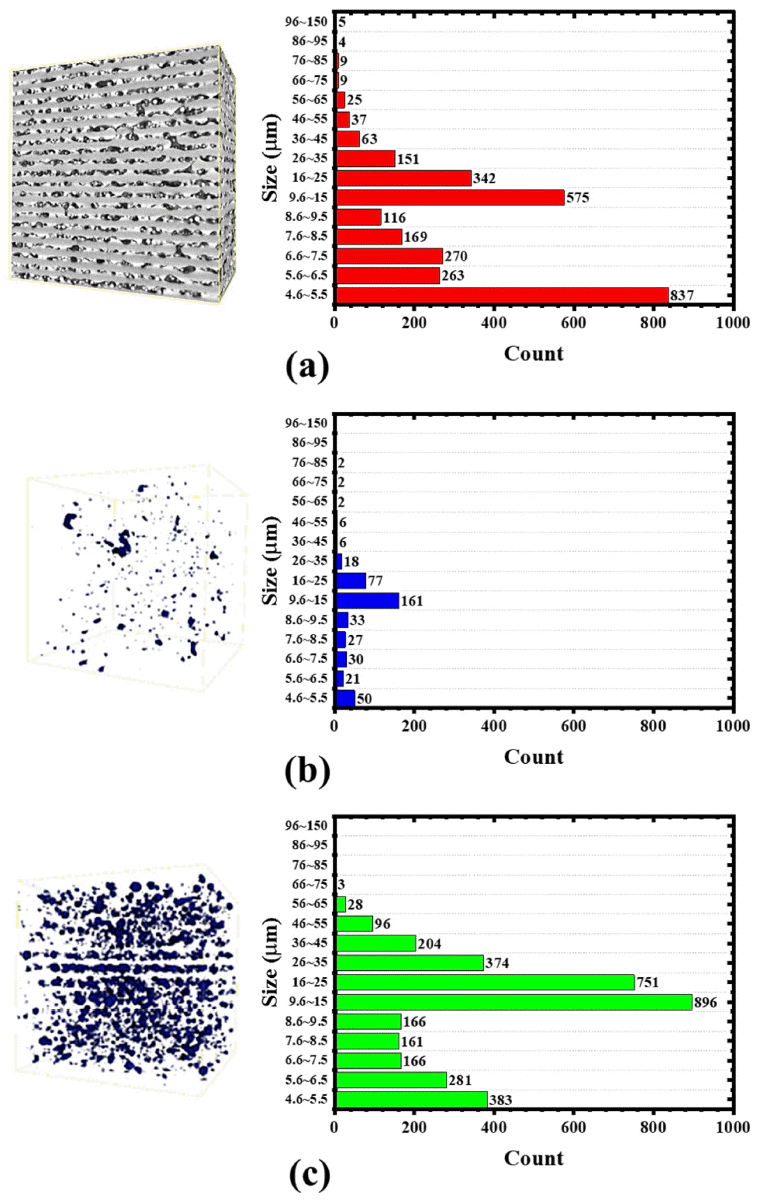
X-ray Tomography analysis data of 3d printing samples; (a) 50W 700 mm/s (b) 70W 500 mm/s (c) 90W 300 mm/s.
이러한 기공의 형상과 공정 변수의 상관관계는 이미 기 존 연구논문을 통해서도 공정 윈도우로 보고 되고 있는데, 에너지가 충분하지 않을 때는 금속 분말이 용해되지 않아 고밀도의 조형체를 형성할 수 없으며, 에너지가 과하게 주 입되었을 때는 미처 빠져나가지 못한 기체가 고립되는 형 태로 구형의 기공이 다수 형성된다고 알려져 있으며 본 연구에서도 유사한 결과를 확인할 수 있었다. 단, X-ray 분석으로 통해서 얻은 기공은 3차원 이미지의 명암을 통 해서 구분하게 되는데, 분석 중에 포함되는 저밀도 개재물 이나 이미지 분석 상의 임계값 설정에 따라서 달라지게 되며, 이로 인해서 조형체의 측정 밀도와 3차원 분석과의 유의미한 차이가 존재하였다. 특히, 과용융 상태에서는 측 정된 밀도가 98%였으나, 3차원 이미지 분석 시의 밀도는 95% 이하로 이미지 분석 방법 중에 적용되는 자동 임계 치 측정 등의 설정 등에 유의하여 추가 연구를 수행할 필 요가 있다. 본 연구에서는 3차원 GeoDict소프트웨어를 사 용하여 자동으로 제안해 주는 임계값을 기준으로 단순화 된 기계학습 모델을 이용하여 자동으로 분류할 수 있는지 를 살펴보고자 한다.
3.2. 기공 형상 분류를 위한 기계 학습 적용
적층 제조 중 발생하는 기공의 형상은 조형 조건에 따 라서 크게 3가지(“unmelt”, “proper”, “over-melt”)로 분류 할 수 있으며, 기공의 형상에 대해서는 적층 제조물의 위 치나 경계부위에서의 판단이 어려울 수 있어, 향후 대량생 산 체계에서 자동화를 고려한다면 인공지능에 의한 기계 학습 모델을 적용할 필요가 있다. 특히, 형상이 본 연구에 서 사용된 큐브 형태가 아닌 판상이나 침상의 제품인 경 우에는 동일한 공정 조건으로 조형 시에도 다른 형태의 거동을 보일 수 있으므로, 본 연구에서는 X-ray tomography로 수집된 이미지를 기반으로 기계 학습을 수행하 였다. X-ray Tomography를 통해서 시편당 600×600 픽셀 의 1000장의 projection 이미지를 도출할 수 있었으며, 이 를 기반으로 학습용 데이터 및 검증 데이터를 추출하여 기계 학습을 수행하였다. 본 기계 학습은 Deep learning 엔진인 PyTorch를 활용하여 NVIDIA GTX 1080Ti로 학습 을 진행하였으며, 기계학습 모델 중 비교적 간단한 구조인 CNN(Convolution Neural Network) 모델로 학습하였다 (Loss Fn: Cross entropy, Optimizer: Adam). X-ray tomography의 특성 상 표면 쪽의 이미지는 회절 패턴에 의한 artifact가 존재하므로 Fig. 5 (a)에서 첫번째, 다섯 번째 이 미지를 제외한 내부 이미지를 중심으로 기계 학습을 시켰 으며, 이미지의 contrast와 brightness가 다르더라도 기계학 습 시 분류가 가능하도록 Random image를 생성하여 학습 을 수행하였다. 테스트 단계에 대해서 정상적인 시편과 에 너지 부족, 에너지 과다에 관한 분류를 수행한 결과 이미 지는 조건당 1000장씩 수행한 결과 중, 아래 Fig. 5(b)에 일부 이미지 결과를 나타내었다. 또한, Table 3에서와 같 이 3000개의 데이터를 기준으로 수행하였을 때 2개의 이 미지에 대해서만 오류가 발생하였고, 이는 테스트 정확도 99.978% 값으로 자동화 분류가 가능함을 확인하였다. 개 발과 관련된 코드를GITHUB에 공개하여 다양하게 활용이 가능하다[12]. 레이저 파워와 스캔 속도에 크게 변화시켜 복잡한 시편을 만들었을 때 분류할 수 있는지 여부에 대 해서는 추가적으로 테스트가 필요할 것으로 생각된다.
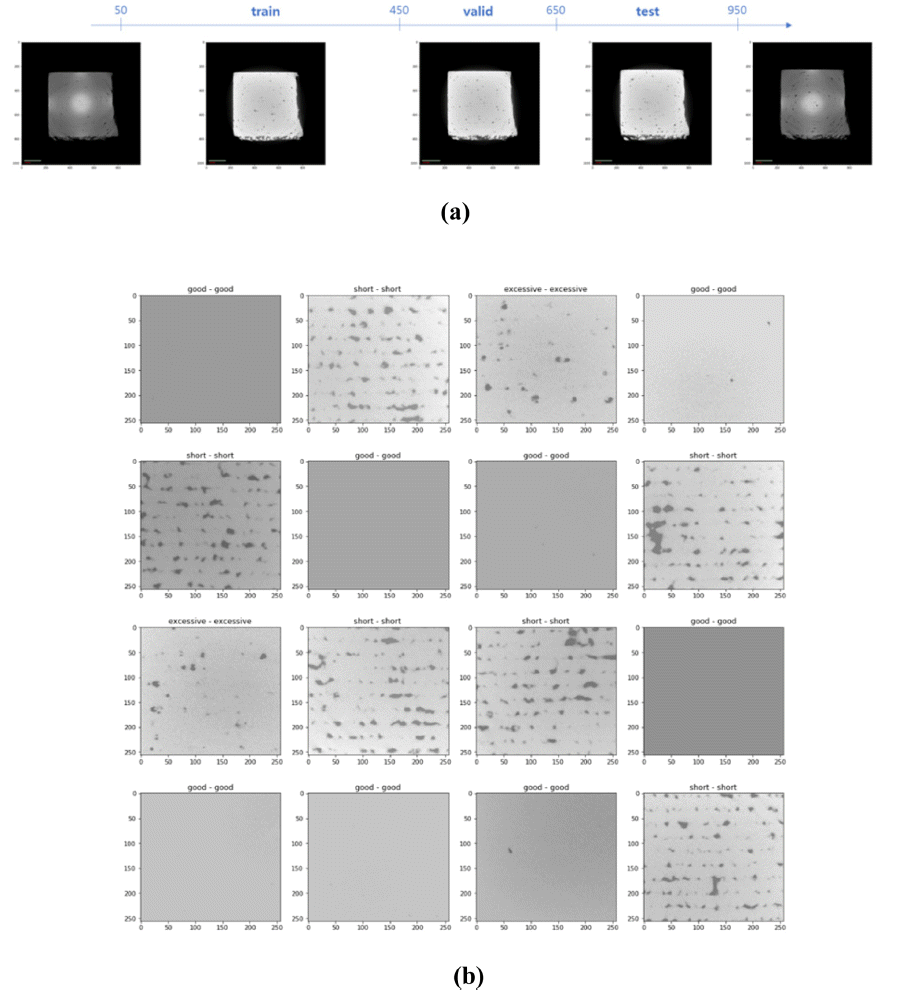
Machine learning results for classify the type of pores in the projected images from X-ray tomography analysis (a) Data classification (training/validation/test) (b) Result images.
4. 결 론
본 연구는 상용 티타늄 분말을 Powder Bed Fusion 방식 으로 레이저 출력 50 W, 70 W, 90W, 조사 속도 300~700 mm/s 조건에서 적층 제조를 실시하여, 공정 조건과 조형 체의 밀도, 기공의 형상에 대한 상관관계 연구를 수행하였 다. 기존에 잘 알려져 있듯이 용융 에너지가 부족할 경우 연결된 형태의 기공 구조를 가짐을 3D X-ray 분석을 통해 서 확인하였고, 에너지가 과도할 경우 구형의 기공이 생김 을 확인하였다. 본 연구를 통해서 X-ray 분석 방법이 조형 체 내의 결함을 정확하게 측정할 수 있음을 보였다. 단, 3 차원 분석에서의 기공 판단 임계치에 따라서 측정된 밀도 와 큰 차이가 날 수 있으므로 컴퓨터 비전 기반의 분석에 서는 유의할 필요가 있다.
공정 조건에 따라서 에너지부족, 적정 제조, 에너지과다 로 분류된 다수의 이미지를 기반으로 기계학습 기법을 적 용하여 높은 정확도를 가지고 공정 조건을 분류할 수 있 음을 확인하였다. 본 연구를 통해서 간단한 컴퓨터 비전과 적층 제조 기술이 상호 연계되어 자동화된 시스템 구축을 위해서 진행할 수 있음을 확인하였다.