선택적 레이저 용융 공정을 이용한 316L 스테인리스 강의 제조 시 공정 중단 및 재 시작이 미세조직과 국부 물성에 미치는 영향
Effect of Process Stopping and Restarting on the Microstructure and Local Property of 316L Stainless Steel Manufactured by Selective Laser Melting Process
Article information
Abstract
This study investigates the effect of process stopping and restarting on the microstructure and local nanoindentation properties of 316L stainless steel manufactured via selective laser melting (SLM). We find that stopping the SLM process midway, exposing the substrate to air having an oxygen concentration of 22% or more for 12 h, and subsequently restarting the process, makes little difference to the density of the restarted area (~ 99.8%) as compared to the previously melted area of the substrate below. While the microstructure and pore distribution near the stop/restart area changes, this modified process does not induce the development of unusual features, such as an inhomogeneous microstructure or irregular pore distribution in the substrate. An analysis of the stiffness and hardness values of the nano-indented steel also reveals very little change at the joint of the stop/restart area. Further, we discuss the possible and effective follow-up actions of stopping and subsequently restarting the SLM process.
1. 서 론
선택적 레이저 용융(Selective Laser Melting) 공정으로 제작되는 부품의 경우 다른 금속 3D 프린팅 공정들(Direct energy deposition, Wire Arc Additive Manufacturing, Binder jetting, Fused deposition modeling 등)로 제작한 부품들에 비해 정밀도나 물성이 우수하기 때문에 별도의 후가공처 리 없이 사용될 수 있다[1, 2].
일반적으로 선택적 레이저 용융 공정을 이용한 부품의 제작은 적층 공정시작부터 공정이 다 끝날 때까지 쉬지 않고 한번에 이루어진다. 그러나 실제 산업 현장에서는 분 말 금속이 부족하여 재충전하거나 장비 오류로 인하여 중 간에 공정이 멈춘 경우가 발생할 수 있으며, 이 때 문제 조치 후 다시 장비를 가동하여 이어서 공정을 진행하는 경우가 생길 수 있다. 이와 관련하여 문제 조치 후 공정을 이어 진행할지 처음부터 공정을 모두 다시 시작할지 결정 하는 것은 산업적으로 중요한 이슈가 된다[3]. 적층 공정 을 멈추었다가 다시 시작하는데 문제가 없다면 제한적인 분말 금속 공급으로 인한 제품의 크기와 그에 따른 장비 의 한계성을 극복할 수 있으며 선택적 레이저 용융 공정 을 이용한 다양한 하이브리드 공정의 개발에 도움이 될 것으로 보이며 이에 대한 연구들이 진행되고 있다[4].
M. S. Hossain 등은 전기 센서의 하우징을 선택적 레이 서 용융 공정을 이용하여 제작을 하다가 중간에 중단 후 센서를 삽입하고 그 위에 공정을 다시 진행하여 하우징의 일체화를 시도한 바 있다[4, 5]. 공정이 중간에 중단되었다 가 재 시작하여 제작된 부품의 경우 처음부터 끝까지 한 번에 이루어진 부품에 비해서 상대적으로 구조적 물성에 차이를 보일 것으로 예상이 되었으며, 이와 관련하여 공정 의 신뢰성을 확보하는 것이 중요하다. P. Stoll 등은 스테 인리스 강 316L를 이용하여 공정 중단 후 재 시작을 한 다음 인장 시편을 준비하고 물성 평가를 통해 약 15%정 도 인장 강도가 낮아진다는 결과를 제시하였다[6]. 또한 V. Hammond 등은 AlSi10Mg 합금을 이용하고 AM 공정 중단 후 재 시작하여 제조한 소재에서 경도와 인장 강도 가 약 10% 저하됨을 확인하였다[7]. I. D. Jung 등의 연구 에서는 레이저 용융 공정을 진행하여 센서의 홈을 만들고 공정을 중단한 다음, 홈 내부의 분말을 비운 후 센서를 넣 고 일정 두께의 판으로 덮어 그 위에 다시 공정을 진행하 여 제작품의 물성을 변화하지 않고 센서가 정상 작동할 수 있는 점을 보여주었다[8]. 그러나 현재까지 선택적 용융 공정의 중간 및 재시작한 소재의 부위별 미세조직 분석 및 국부적 물성의 차이에 대한 연구는 부족한 실정이다.
본 연구에서는 선택적 레이저 용융 공정을 중간에 중단 하고 베이스 플레이트를 완전히 꺼내지 않고 대기하였다 가 재 시작하여 시편들을 제작하고 중간 이음 부분에서의 미세조직 및 나노 인덴테이션을 이용한 국부적 기계적 특 성[9, 10]을 조사하였다. 이때 공정을 멈추는 동안에 산소 의 접촉을 최대한 줄인 아르곤 가스 상태로 유지한 시편 과 산소를 접촉시킨 시편을 각각 준비하고 제조 환경의 영향에 대해서도 조사, 비교하였다.
2. 실험 방법
선택적 레이저 용융 공정을 중간에 중단한 후 재 수행 하였을 때 제조된 소재의 이음 부분을 관찰하기 위해 시 편을 제작하였다. 적층 제조 시편들은 상용 스테인리스 스 틸 316L의 분말 금속을 이용하며 SLM Solution사의 SLM 125HL 장비를 이용하여 제조하였다. 시편 제작에 사용한 분말 feedstock은 스테인리스 강 316L 조성을 가지고 있었 다. 분말의 크기 분포는 베크먼-쿨터 사의 LS 13 320 레 이저 회절 입자 크기 분석기를 사용하였으며, Zeiss Ultra- 55장비를 통하여 주사 전자 현미경(Scanning Electron Microscopy)으로 분말 입자를 관찰하였다. 초기 분말들의 관찰 사진 및 분말 입자의 크기 분포 분석 결과를 그림 1 에 제시하였다. 분석 결과 분말 입자의 평균 직경은 36.13 μm로 얻어졌다.
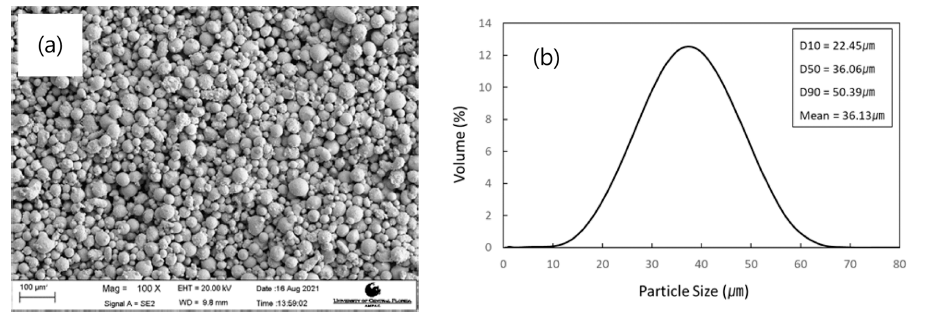
316L stainless steel powder characteristics; (a) scanning electron micrograph (SEM) observation image, and (b) particle size distribution of powders.
그림 2에 본 연구에서 사용한 시편들의 준비 방법 및 분 석 내용의 개념을 도시화하여 제시하였다. 제조된 시편들 의 크기는 10 mm× 10mm× 50 mm이었으며 바 형상으로 준비하였다. 먼저 바닥의 서포트로부터 정상적인 적층 공 정을 수행하였고, 시편의 중간 높이 25 mm에서 공정을 중 지하고 대기 시간을 가졌다. 그 후 최종 높이인 50mm까 지 공정을 다시 이어 진행하였다. 이 때 사용한 선택적 레 이저 용융의 공정 변수를 Table 1에 나타냈다. N. D Vallejo 등과 본 연구의 저자들은 기존 연구에서 스테인리 스 스틸 316L에 대한 최적 공정 조건을 연구하였으며[11], 이를 참고하여 본 연구에서는 SLM Solution 제조사에서 스 테인리스 스틸 316L에 대해 제시한 최적 값을 사용하였다.
시편 제조 중간에 공정을 중지하고 재 수행까지의 대기 시간은 12시간을 적용하였다. 또한 공정 중지 중 대기 시 간 동안 챔버의 산소 농도들을 두 가지 경우로 제어하여 시편들을 준비하였다. 첫 번째 경우는 그림 3 (a)와 같이 공정이 멈춘 동안 챔버의 산소의 농도가 0.3% 이하가 되 도록 챔버에 아르곤 가스를 주입하여 시편을 공기 중에 노출시키지 않고 유지하였다. 두 번째 경우는 그림 3 (b) 와 같이 공정이 멈춘 12시간 동안 챔버의 산소의 농도를 22% 이상으로 제어하여 시편을 공기 중에 노출하였다.
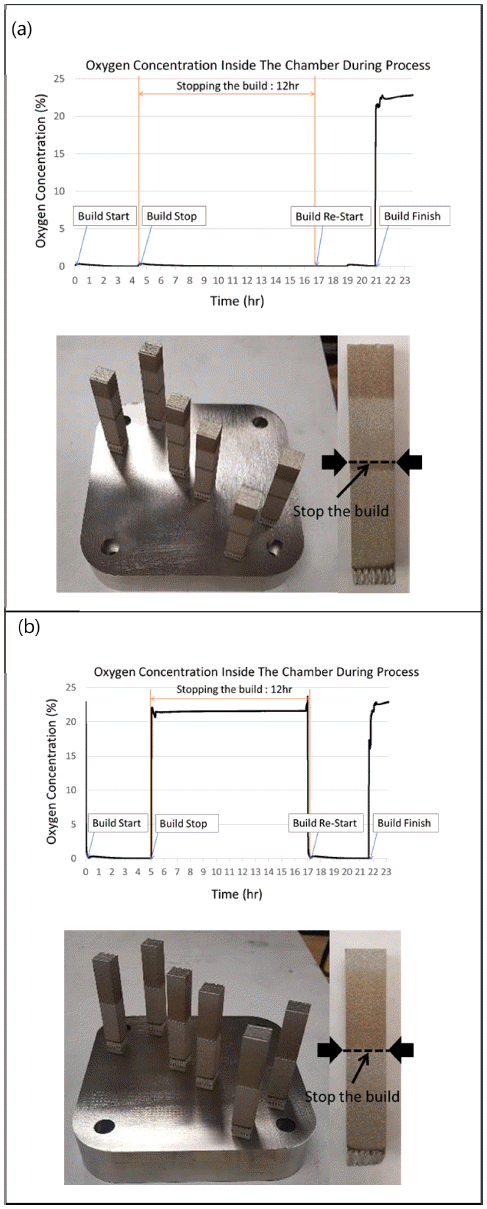
Oxygen concentration in the chamber and manufactured specimen; (a) less than 0.2% during stopping the build, and (b) above 22% during stopping the build.
제작된 시편의 공정 중단 면에 수직하게 절단하고 절단 면을 전처리 가공하여 이음 부분에서의 기공 분포와 용융 정도를 확인하였다[12, 13]. 이 때 이음 부분을 기준으로 양쪽 5mm씩, 높이 10mm의 육면체로 절단하고 이음 부 분에 수직하게 시편을 절단하였다. 준비된 시편에 대하여 에폭시로 마운팅 하고 시편을 고정하였다. 에폭시 레진과 경화제는 EpoxiCureTM 2를 사용하며 8시간 이상 경화시켰 다. 시편의 절단면을 연마하였으며, 이 때 시편 연마는 600 SiC, 800 SiC, 1200 SiC 패드 순으로 5분씩 수행하고 1 μm diamond paste, 1/4 μm diamond paste 패드로 10분씩 수행하였다. 시편 연마 후 시편의 기공 분포를 확인하였다. 또한 제조된 시편에 대하여 염산, 아세트산, 질산을 3:2:1 비율로 혼합한 산에 시편을 에칭하여 시편의 melt pool 조 직을 부위별로 조사하였다. 국부적 기계적 물성 확인을 위 하여 나노 인덴테이션을 이용한 물성 시험을 수행하였다. 그림 6 (a)와 볼 수 있듯이 시편의 아랫 부분부터 윗부분 까지 이음 부분에 걸쳐서 100개의 인덴테이션을 10 μm 간격으로 측정하였으며, 이를 5번 동일하게 반복 수행하 여 결과를 해석하였다. 그 결과를 통해 이음 부분에서의 강성과 경도를 측정하였다[14].
3. 실험 결과 및 고찰
광학 현미경을 이용하여 시편의 내부 미세조직을 관찰 하였으며 이음 부분과 내부에서의 기공 분포를 확인하였 고, 그 결과를 그림 4에 제시하였다. 내부 미세조직에서 공정을 중지 후 이어서 수행한 이음 부분이 내부와 뚜렷 이 구별되지 않았으며, 기공도 역시 이음 부분을 따라 일 정하게 배열되지 않는 특징을 보였다. 광학 현미경을 이용 해 얻어진 이미지들을 ImageJ 소프트웨어로 처리하여 총 면적에 대한 기공의 비율을 측정하고 상대 밀도를 계산하 였다. 얻어진 이음 부분에서의 상대 밀도는 99.9%였다. 시 편의 아랫 부분과 공정을 재 수행한 윗 부분을 비교해보 았을 때에도 역시 상대 밀도는 99.9%로 동일하였다. 선택 적 레이저 용융 공정에 따라 발생할 수 있는 기공들의 분 포가 공정을 중간에 중단 후 재 수행 시에 더 많이 분포 가 되거나 일정한 배열을 나타내는 등의 특이한 점은 찾 을 수 없었다. 또한 이러한 특징은 공정 중단 중 주변 분 위기(아르곤 및 산소)가 달라짐에도 불구하고 차이 없이 동일하게 확인되었다.
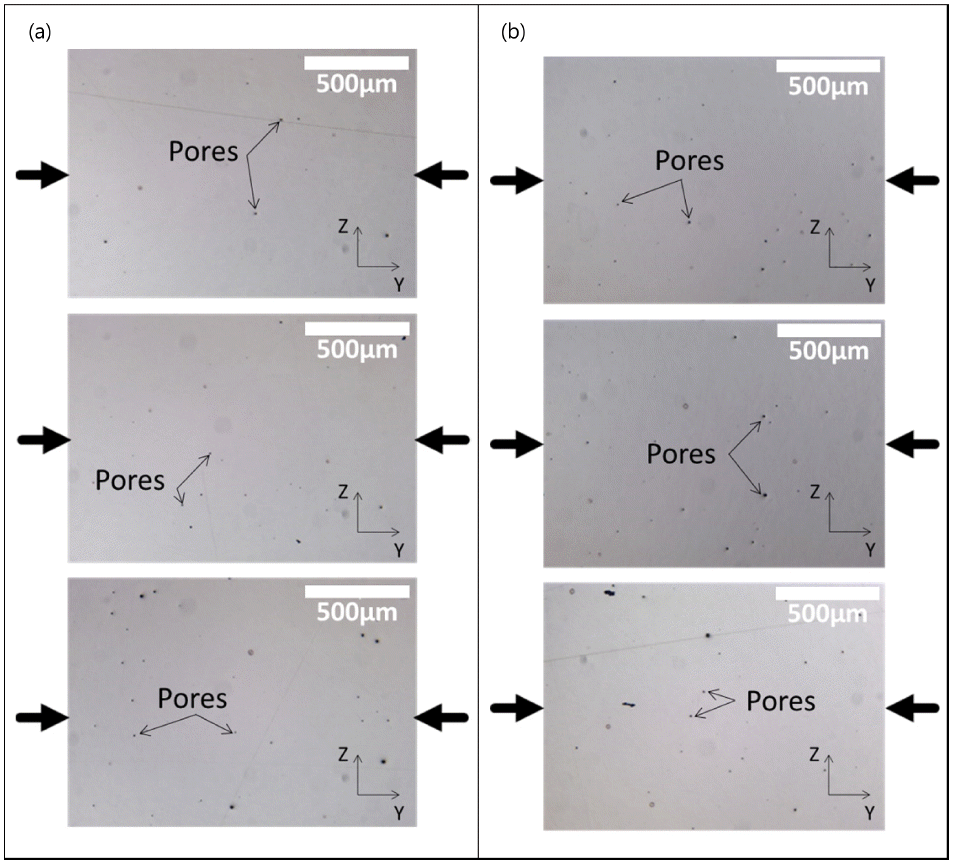
Pore distribution analysis results inside the specimens of (a) oxygen concentration of less than 0.2% during stopping the build, and (b) oxygen concentration of above 22% during stopping the build.
시편을 혼합산으로 에칭하여 선택적 레이저 용융 공정 에 따라 발생하는 금속 분말의 용융 정도를 관찰하였고, 그 결과를 그림 5에 나타냈다. 레이저 용융 및 응고에 따 라 형성된 melt pool이 형성되어 있었으며, 이와 함께 시 편 내부의 기공 및 산화물들이 관찰되었다. 그러나 그림 4 에서 나타난 결과와 유사하게 에칭 후 미세조직 관찰한 결과(그림 5)에서도 공정 중 중단 및 재 수행된 이음 부분 에서 기공이나 산화물이 더 많이 형성되거나 일정하게 배 열된 특징은 나타나지 않았다. 이러한 경향은 중단 중 주 변 분위기(아르곤 및 산소)에 무관하게 동일하게 나타났다. 상기 결과들을 통하여, 연구 수행 전 예상되었던 레이저 공정 중단에 따른 결함 분포의 차이와는 다르게, 공정을 중단하였다가 다시 재 시작하여도 국부적 결함이나 산화 물 분포 특성에는 차이가 없음을 알 수 있었다.
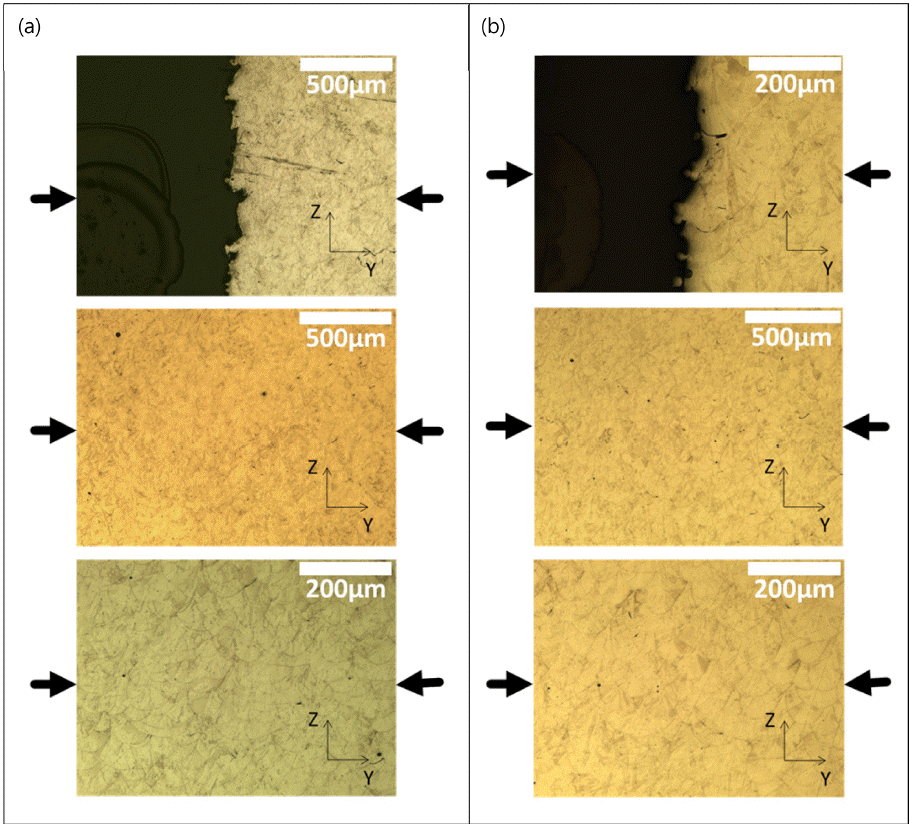
Melt-pool observation results inside the specimens of (a) oxygen concentration of less than 0.2% during stopping the build, and (b) oxygen concentration of above 22% during stopping the build.
나노 인덴테이션을 이용한 시편 이음 부분에서의 강성 과 경도 측정 결과를 그림 6에 제시하였다. 그림 6 (b)와 그림 6 (c)는 이음 부분에서의 강성과 경도의 값들을 각각 나타낸다. 여기에서 중간 이음 부분을 포함해 990 μm에 걸쳐 탐색을 하면서 강성과 경도가 크게 변화하는 위치를 찾아보고자 관련 실험을 수행하였다. 적층 가공한 시편의 한 층의 두께는 30 μm로 나노 인덴테이션을 실시한 전체 범위 990 μm에 비해 매우 좁은 영역이다. 나노 인덴테이 션을 실시한 100개 포인트 중 3%를 차지하는 최대 3개의 데이터가 시편 이음 부분을 대표하며, 그 외에 나머지 97%를 차지하는 97개의 데이터는 기존 적층 공정과 마찬 가지로 정상적으로 만들어졌다고 할 수 있다. 측정 결과 시편의 아랫 부분부터 윗 부분까지 이음 부분에 걸쳐 측 정 값들의 평균과 표준 편차에서 기공과 산화물이 형성되 거나 상변화에 따라 나타날 수 있는 뚜렷한 변화가 보이 지 않았다. 또한 거시적으로 일정한 값을 보이며 이음 부 분에 따른 특이한 차이를 나타내지 않았다.
선택적 레이저 용융 공정이 중지되었을 때 조치를 위해 장비의 문을 열면 제작품이 공기 중 산소에 노출될 수 있 다. 본 연구의 공기 중에 노출하여 대기한 시편과 아르곤 가스 중에 대기한 시편의 인덴테이션 강성 및 경도의 비 교 결과에서, 같은 시간 동안 산소에 노출이 되었다가 공 정이 다시 이어졌음에도 불구하고 아르곤 가스 중에서 대 기한 시편과 평균 물성의 관점에서 거의 차이를 보이지 않았다. 다만 유사한 평균 값을 보인다고 하더라도 산소에 중간 노출된 소재의 물성 변동폭이 아르곤에 노출된 소재 에 비하여 소폭 더 크게 나타났다. 이를 바탕으로 본 연구 에서 진행한 12시간의 공기 노출은 최종 제작품의 기본 기계적 물성에는 큰 영향을 미치지 않을 것으로 사료된다.
기존 연구에서는 공정이 중단되었을 때 베이스 플레이 트를 완전히 꺼냈다가 다시 금속 분말을 채워 리코터 정 렬을 하고 공정을 이어 다시 시편을 제작한 경우, 적층 두 께가 이전과 달라지고 그에 따른 물성 변화가 보고되었다 [6, 7]. 그러나 본 연구에서는 부품 제조 중간에 선택적 레 이저 용융 공정이 중단되었을 때, 베이스 플레이트를 완전 히 꺼내지 않고 분말 금속이나 아르곤 가스 등을 보충하 거나 장비의 오류를 조치한 후 공정을 이어서 한다면, 중 단 전, 후의 거시적 미세조직 및 물성에 변화가 없음을 제 시하였다. 또한 하우징 내부에 센서를 넣거나 중간에 조립 품을 생성하는 하이브리드 제조 공정에서 공정을 중단하 였을 때, 초기 리코터 정렬과 레이어 두께를 바꾸지 않은 상태에서 공정을 재 진행하면 제작품의 물성을 변화시키 지 않고 제작할 수 있을 것으로 예상된다.
산업체에서 선택적 레이저 용융 공정을 진행하는데 드 는 비용과 시간을 고려한다면 공정을 처음부터 다시 시작 하는데 많은 어려움이 따를 것이다[3]. 이에 공정이 중간 에 멈추어도 조치 후 공정을 이어 진행하는데 문제가 없 다면, 큰 경제적 이익이 있을 것으로 사료되며, 특히 압전 센서 등의 하우징을 일체형으로 제작하는 하이브리드 제 조 공정의 경우 그 이익이 더욱 클 것으로 기대된다.
4. 결 론
선택적 레이저 용융 공정을 중간에 멈추었다가 재 시작 을 하였을 때 중간 이음 부분에서의 미세 조직 및 나노 인 텐테이션을 통한 기계적 물성을 조사하였으며, 공정 중단 시 챔버 환경에 대한 영향을 검토하여 다음과 같은 결론 을 얻을 수 있었다.
1. 시편의 단면에서 이음 부분의 기공 분포를 관찰했을 때 이음 부분이라고 지정할 수 있는 기공이 크거나 일정 한 패턴으로 배열되거나 하는 특이한 사항은 나타나지 않 았다. 중간에 공정을 멈추어 공기(산소 농도 22%이상) 중 에 12시간 노출시키고 공정을 재 수행하였음에도 밀도는 99.8% 이상으로 이전 아랫 부분과 비교해 거의 차이가 없 었다.
2. 시편의 melt pool 조직을 관찰한 결과에서도 이음 부 분에서 용융 정도가 무너지거나 기공이 뚜렷하게 나타나 는 특이한 점은 없었고 용융 정도가 균일하게 잘 이루어 지는 것을 확인하였다.
3. 나노 인덴테이션을 통한 강성 및 경도 시험을 수행한 결과, 이음 부분에서 강성 및 경도 값이 달라지지 않았다. 선택적 레이저 용융 공정을 중지 후 재 수행한 시편의 이 음 부분에서 내부 조직을 관찰해보면 공정을 중간에 멈추 지 않고 일반적으로 수행하였을 때와 동일하게 나타났다.
감사의 글
본 연구는 산업통상자원부 및 한국산업기술진흥원의 글 로벌 인재 양성 사업(P0008750)의 지원으로 수행되었으며 이에 감사드립니다.