MoS2 첨가에 따른 Fe-Cr-Mn-C-V계 소결합금의 기계적 특성 평가
The Effects of MoS2 Addition on the Mechanical Properties of Fe-Cr-Mn-C-V P/M Alloy
Article information
Abstract
The connecting rod is one of the most important parts in automotive engines, transforming the reciprocal motion of a piston generated by internal combustion into the rotational motion of a crankshaft. Recent advances in high performance automobile engines demand corresponding technological breakthroughs in the materials for engine parts. In the present research, the powder metallurgy (P/M) process was used to replace conventional quenching and/or tempering processes for mass production and ultimately for more cost-efficient manufacturing of high strength connecting rods. The development of P/M alloy powder was undertaken not only to achieve the improvement in mechanical properties, but also to enhance the machinability of the P/M processed connecting rods. Specifically MoS2 powders were added as lubricants to non-normalizing Fe-Cr-Mn-V-C alloy powder to improve the post-sintering machinability. The effects of MoS2 addition on the microstructure, mechanical properties, and machining characteristics were investigated.
1. 서 론
최근 자동차산업의 발달과 함께 고출력 엔진개발의 수 요가 증가함에 따라 고성능, 고정밀도를 요구하는 부품의 개발이 지속적으로 요구되고 있다. 특히, 자동차 엔진의 핵심부품인 커넥팅로드(Connecting rod)는 연료의 폭발로 인한 피스톤의 직선운동을 크랭크축의 회전운동으로 전환 시키는 동력 전달 부품으로 높은 강도 및 인성, 피로 강도 와 같은 우수한 기계적 특성이 요구되며, 이에 따른 커넥 팅로드 대한 합금설계, 제조공정, 열처리 기술 등의 다양 한 연구가 진행되고 있다.
일반적으로 커넥팅로드의 기본재료는 기계적 특성, 경 제성 등을 고려하여 철강 재료가 주로 사용되고 있으며, 기계적 특성을 향상시키기 위해 다양한 원소들을 첨가시 켜 합금설계를 수행하고 있다. 자동차업계에서는 제조공 정의 단축, 생산성의 향상, 제조공정 원가를 절감하고 성 능을 개선하고자 소입, 소려(Quenching & Tempering) 과 정을 거치지 않는 치환형 합금원소(Mn, Si)첨가에 의한 고 용강화와 미량의 탄질화 화합물 형성 원소 (V, Nb, Ti)에 의한 결정립 미세화 효과, 석출강화를 이용하여 강도를 향 상시키는 비조질강(Non-normalizing alloy) 개발에 관심이 모아지고 있다[1].
최근에는 고용강화 및 석출물에 의한 결정립 미세화와 석출 강화를 목적으로 Fe-Cr-Mn-V-C 조성의 합금계가 주 목 받고 있다. Fe-Cr-Mn-V-C 조성의 합금계에서 Cr, Mn 은 확산 거동을 통하여 고용강화 효과를 얻을 수 있으며, V는 소결 후 VC 탄화물을 생성하여 소결 중 오스테나이 트 입계의 성장을 방해하여 결정립 미세화 및 석출강화 효과로 인하여 기계적 특성을 향상시키기는 장점을 가지 고 있다. 그러나 상기 조성으로 설계된 합금은 경도 및 강 도가 높아 가공특성이 좋지 않은 단점을 가지고 있기 때 문에 절삭성을 향상시키기 위한 연구가 요구되고 있는 실 정이다[2]. 본 연구에서는 상대적으로 낮은 에너지로 원재 료 소모가 없고 제품의 최종 형상과 가깝게 제조할 수 있 는 분말야금공정(powder metallurgy process)을 이용하여 시편을 제조하였으며, 절삭성 향상을 위해 합금 첨가원소 를 첨가하여 기계적 강도 및 절삭가공성의 두 가지 관점 에서 특성평가를 진행하고자 하였다. 하지만 기존의 분말 야금공정은 공정 중 분말 입자의 유동성 및 반발력 등으 로 인해 성형체 내부에 기공이 발생하여 강도 및 밀도가 저하되는 문제점을 가지고 있어[3-6] 이를 해결하기 위해 분말야금공정 중에 동적 성형 공정인 자기펄스압축성형 (Magnetic Pulsed Compaction)공정을 이용하여 Fe-Cr-Mn-V-C 조성의 고밀도 성형체를 제조하였고, 가공성 및 기계 적 특성 향상을 위해 MoS2의 첨가에 따른 미세조직 변화, 기계적 특성 및 절삭가공성 평가를 수행하였다.
2. 실험방법
본 연구에서 원재료는 HOGANAS사에서 제조한 Fe-1Cr-0.1Mn-0.2V 조성의 합금분말을 사용하였으며, 재료의 기계적 특성 및 절삭성 향상을 위해 탄소(C)와 MoS2 분말 을 첨가하여 3차원 혼합기(Tubular Mixer)로 혼합분말을 제조하였다. 그림 1은 실험에 사용된 분말의 형상 및 크기 를 나타내는 미세조직 사진이며, 분말의 입도분석 결과 Fe-1Cr-0.1Mn-0.2V 조성의 합금분말의 평균 입도는 110.46 μm, 첨가원소로 사용된 MoS2 분말의 평균입도는 13.08 μm로 분석되었다. MoS2 첨가에 따른 재료의 미세 구조 및 기계적 특성을 관찰하기 위하여 첨가량을 0~1 wt%까지 변화시켰으며, 이렇게 제조된 분말의 화학조성 을 표 1에 나타내었다.
제조된 혼합분말은 자기펄스압축성형장치로 1.5 GPa의 압 력으로 성형한 후, 잔류오스테나이트 생성 억제를 위해 그리 고 온도에 따른 소결 밀도를 고려하여 가장 낮은 온도인 1,120°C에서 소결을 실시하였다. 질소 분위기에서 1,120°C의 온도로 3시간 동안 소결하여 그림 2와 같은 시편을 제조하 였고, 제조된 시편의 기계적 특성 평가를 위해 인장시험기 (Instron)를 이용하여 ASTM E 8M-08 규격으로 인장시험을 수행하였고, 로크웰 (케이디정밀)과 비커스 경도기를 이용하 여 경도를 측정하였다. 또한, 절삭가공성은 소결 시편의 드 릴링 실시하여 토크(torque) 및 추력(thrust force) 값을 측정하 였다. 광학현미경(Nikon, ECLIPSE MA 100)과 주사전자현미 경(FEI company, NOVA NANO 200)을 이용하여 미세조직을 관찰하였으며, MoS2 첨가에 따른 화학적 조성 변화를 관찰 하기 위해 에너지 분산 분광기(Energy Dispersive Spectroscopy, EDS)를 이용하여 분석을 실시 하였다.
3. 결과 및 고찰
3.1. MoS2 첨가에 따른 미세조직 분석
그림 2는 자기펄스압축성형장치로 제조된 시편이며, 소 결하기 전 성형체 및 소결체의 평균밀도를 아르키메데스 방법을 이용하여 측정한 결과, 성형체는 7.14 g/cm3였으며, 소결체는 7.28 g/cm3로 소결 전, 후 밀도차이가 약 2% 정 도 차이를 보였고 MoS2의 첨가량에 따른 소결 전, 후 시 편의 밀도 변화는 거의 없었다. 소결 후 상대 밀도는 약 93%로 측정되었다.
그림 3은 MoS2의 첨가량에 따른 소결 시편의 에칭 전 광학사진을 관찰한 것으로, 사진의 검은 점들은 기공과 게 재물들인 것으로 확인되었다. 각 시편 별로 기공율의 차이 는 거의 없었으나 MoS2를 첨가한 소결 시편(그림 3(b): 0.35 wt%, (c): 0.7 wt%, (d): 1 wt%))에서는 비교적 크기 가 작은 기공들이 많이 관찰되었다. 그림 4는 MoS2의 첨 가량에 따른 소결 시편의 미세조직 변화를 나타내는 주사 전자현미경 사진이다. MoS2가 첨가되지 않은 시편의 미세 조직은 그림 4(a)과 같이 대부분 미세한 펄라이트(pearlite) 조직이 형성되었고, 일부 페라이트(ferrite) 조직이 형성되 었다. 또한, MoS2가 0.35 wt% 첨가된 시편(그림 4(b))의 경우 대부분 펄라이트 조직을 형성되었고 부분적으로 페 라이트 조직과 페라이트 기지에 석출된 2상(secondary phase) 조직이 일부 관찰되었다. MoS2가 0.7 wt% 첨가된 그림 4(c) 시편의 미세조직에서는 펄라이트 조직과 페라이 트 조직 사이에 형성된 2상 석출조직 영역이 더욱 확대되 었다. MoS2가 1 wt% 첨가된 시편(그림 4(d))에서는 2상 석출 조직 영역이 조대하게 분포함에 따라 상대적으로 펄라 이트와 페라이트 조직이 크게 감소한 것으로 관찰되었다. MoS2는 1,185°C의 온도에서 분해가 일어나는데 고온 소결 과정에서 Mo와 S로 분해되어 S는 반응성이 좋은 Cr과 반응 하여 CrXSX+Mo가 생성되고, Mo는 Fe와 결합하여 2상 석 출조직을 형성하는 것으로 보고 되고 있으며[7-8,14], 본 연 구의 고온 소결 과정에서 분해된 Mo는 Fe와 결합하여 각 소 결 시편에서 2상 석출조직을 형성하였으며 MoS2의 함량이 증가함에 따라 그 영역이 확대된 것으로 판단할 수 있다.
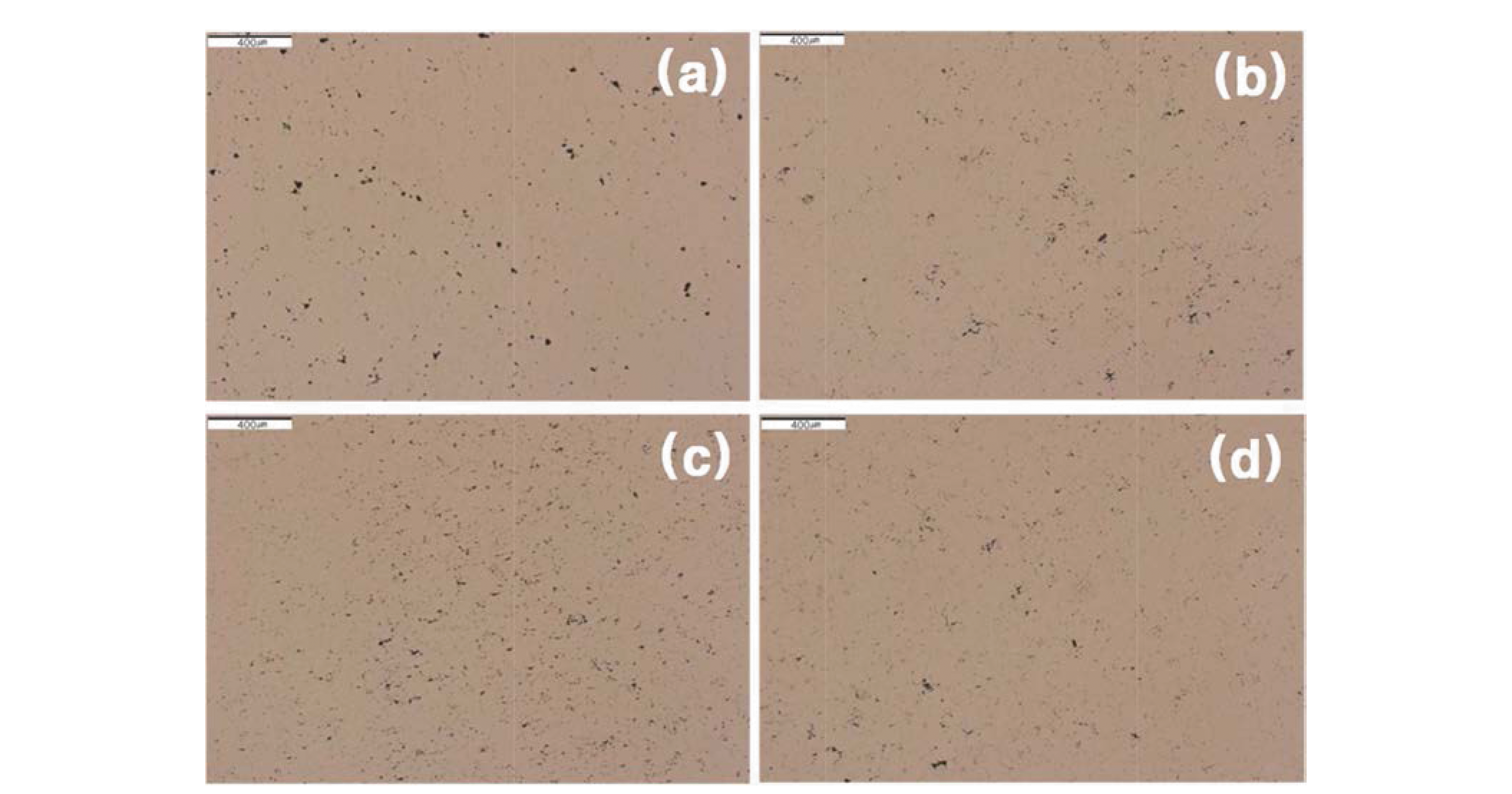
Optical images due to amount of MoS2 contents (a) 0 wt%, (b) 0.35 wt%, (c) 0.7 wt%, and (d) 1 wt% (Non-etching).
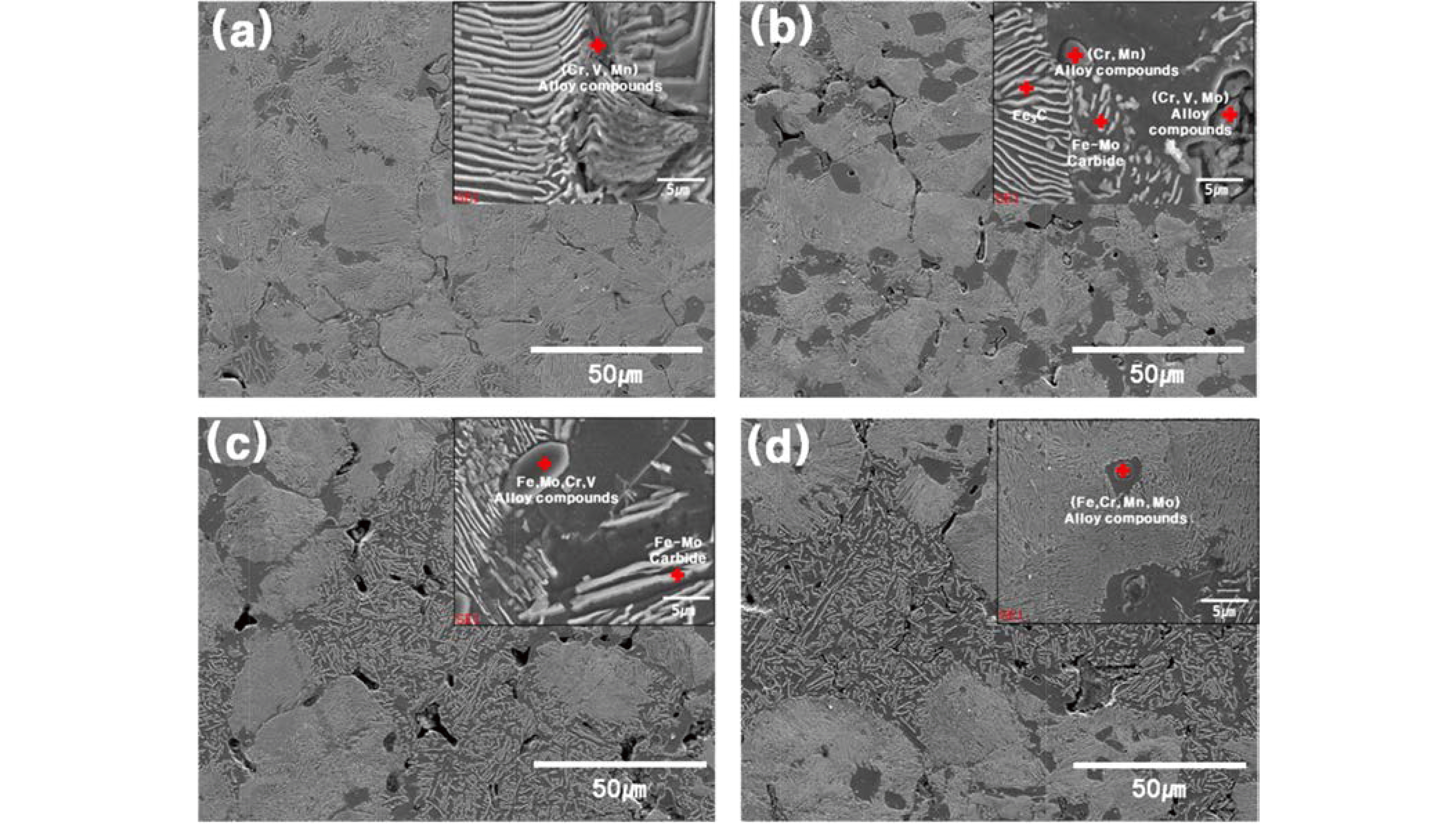
Microstructure and EDS analysis due to amount of MoS2 contents (a) 0 wt%, (b) 0.35 wt%, (c) 0.7 wt%, and (d) 1 wt%.
각 소결 시편의 미세조직을 EDS로 분석한 결과, MoS2 가 첨가되지 않은 시편은 펄라이트 조직과 페라이트 조직 그리고 복합(Cr, Mn, V) 화합물이, 0.35 wt%의 MoS2가 첨가된 경우 2상 석출상인 Fe-Mo 탄화물이 생성되었다. 또한, MoS2가 각각 0.7 wt%, 1 wt% 첨가된 경우 2상 석 출상인 Fe-Mo 탄화물 조직의 분포가 점차 확대되었으며, 소결 과정에서 분해되어 고용되지 못한 MoS2는 다른 합 금원소들과 복합화합물 형태로 결정립계를 따라 분포된 것이 관찰되었다. 이러한 복합화합물 형태의 게재물은 소 결 과정에서 고용되지 못하고 남아 결정립계에 편석 (segregation)이 되어 기공과 함께 잔존하고 있는 것으로 판단된다[12-13].
3.2. MoS2 첨가에 따른 기계적 특성 및 파단면 분석
MoS2의 첨가량에 따라 전체적인 경도 값 변화를 관찰하 기 위해 로크웰 경도(Rockwell hardness)를 측정하였다(하 중: 100 kgf, 볼 크기: 1/16”). 그림 5와 같이 MoS2의 첨가 량에 따른 소결 시편의 경도는 증가하는데 0.7 wt% 첨가 조건에서 최대 값(92 HRB)을 보였으며, 1 wt% 첨가 조건 에서는 경도가 미소하게 감소(89 HRB)하였다.
또한, 비커스 경도기로 소결 시편 내부에 형성된 각각의 미세조직에 대한 경도를 측정하였다. 그림 6은 MoS2가 1 wt% 첨가된 소결 시편에서 각각의 미세 조직(펄라이트, 페라이트, 2상 석출 조직)에 대한 비커스 경도 측정한 결 과를 보여준다. 측정 결과, 2상 석출 조직인 Fe-Mo 탄화 물의 경도 값이 가장 높았으며, 다음으로 펄라이트 조직 그리고 페라이트 조직 순으로 경도가 높게 측정되었다.
각각의 미세구조에 대한 경도측정 값을 고려할 때, 로크 웰 경도 변화에 영향을 미치는 인자는 Fe-Mo 탄화물과 결 정립계에 편석된 MoS2와 기공일 것이라 사료되며, 소결 과정에서 첨가원소의 Mo가 Fe에 고용되어 Fe-Mo 탄화물 을 형성하고 2상의 석출 조직의 영역이 증대되어 전체적 인 경도 값 상승을 가져왔고, 1 wt% 이상의 MoS2 첨가된 경우는 MoS2의 과다한 첨가로 인해 소결 과정에 분해되 지 않은 MoS2가 결정립계를 따라 내부에 편석이 되어 남 아 있었으며, 기공 또한 많이 형성되어 기계적 특성을 저 하 시키는 원인이 된 것으로 사료된다[8-11].
그림 7은 소결 시편의 MoS2 첨가량에 따른 인장강도 및 항복강도 변화를 나타내는 그래프이다. 시험결과 MoS2를 첨가하지 않은 시편이 가장 낮은 인장강도 및 항복강도 값을 나타내었고, MoS2의 첨가량이 증가함에 따라 시편의 인장강도 및 항복강도가 증가하여 0.7 wt%의 MoS2가 첨 가된 시편의 인장 및 항복강도는 각각 650 Mpa 및 597 MPa로 최대로 높게 측정되었다. 1 wt%의 MoS2가 첨가된 시편의 인장 및 항복강도는 0.7 wt%가 첨가된 시편보다 낮은 인장 및 항복강도를 나타내었으며, 이 결과는 경도 측정결과와 유사한 경향을 보였다. 1 wt%가 첨가된 시편 의 인장 및 항복강도가 감소한 원인을 분석하기 위해 각 각의 시편에 대하여 인장시험 후 파단면 분석을 실시하였 다. 주사전자현미경을 이용하여 파단면을 관찰한 결과, 취 성파면(Cleavage)와 연성파면(Dimple)이 복합적으로 관찰 되었다. 그리고 MoS2 첨가량이 증가할수록 딤플영역 및 딤플의 크기도 함께 증가했으며, 다량의 탄화물 및 개재물 이 관찰되었다. 이는 소결과정에서 첨가된 MoS2에서 분해 된 Mo가 Fe기지에 고용되거나 확산을 통해 입계 내부에 Fe-Mo탄화물을 형성하여 전위(dislocation)의 이동을 억제 하고, 탄화물 석출로 인하여 석출강화 효과를 기대할 수 있어 적절한 MoS2의 첨가는 인장 및 항복 강도를 향상시 키는 원인이 될 수 있다[14]. 하지만 과도한 MoS2가 첨가 되었을 경우(1 wt%이상), 인장 및 항복 강도가 감소하는 원인은 결정립계를 따라 분해되지 않고 잔존하는 MoS2와 기공, 그리고 경한 미세조직인 Fe, Cr, V 및 Mo 원소들의 복합탄화물 생성은 기계적 특성을 저하시키는 원인으로 사료된다. 그림 8(d)에서는 딤플 크기가 조대한 연성파면 이 관찰되었고[14-15], 그림 9에서 딤플 영역의 EDS분석 을 통하여 딤플 내부에 탄화물과 개재물이 형성된 것을 확인하였다.
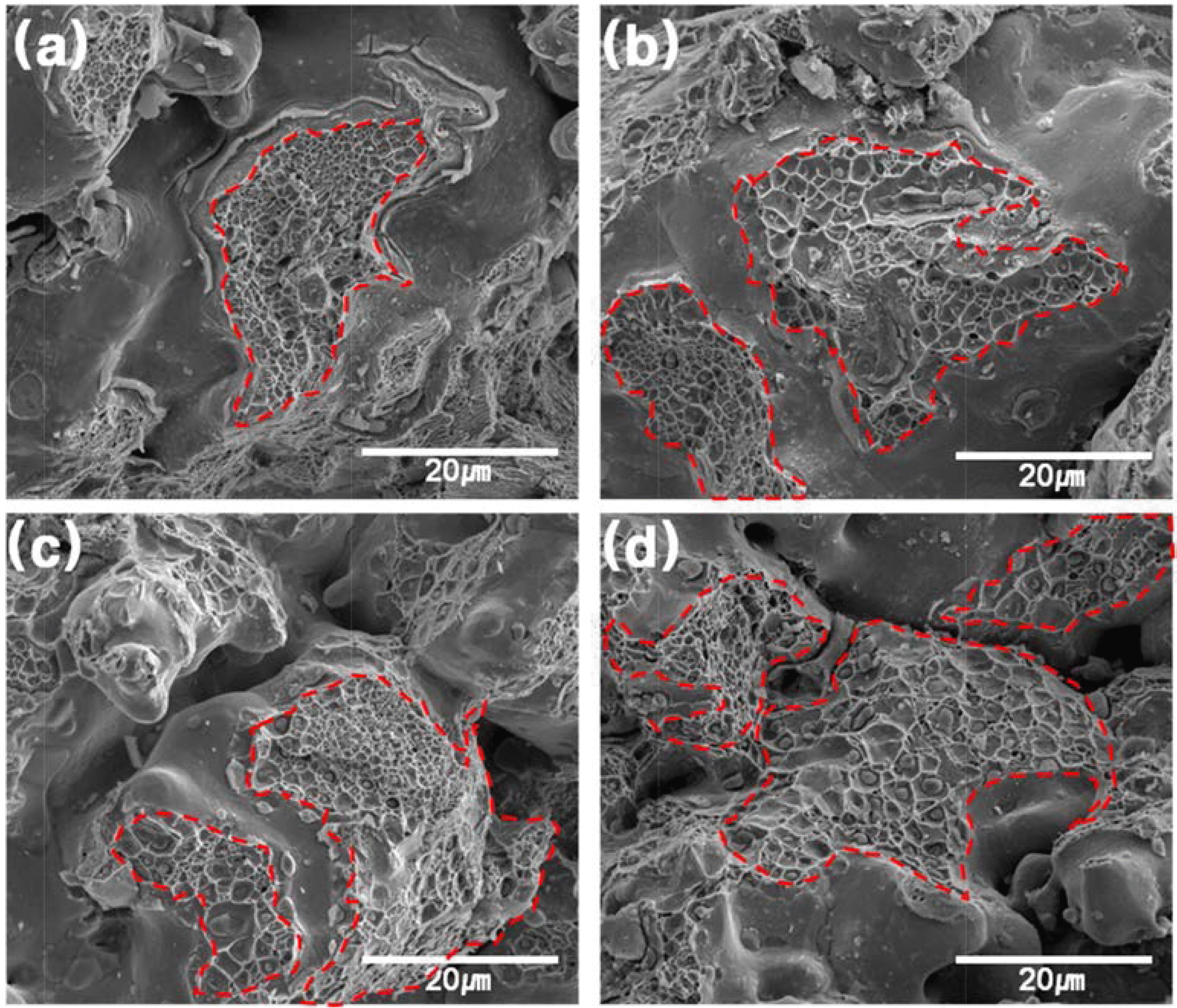
Microstructure of fracture surface due to amount of MoS2 contents (a) 0 wt%, (b) 0.35 wt%, (c) 0.7 wt%, and (d) 1 wt%.
3.3. MoS2 첨가에 따른 절삭 특성 평가
MoS2 첨가에 따른 절삭성 평가를 위해 드릴링 머신을 이용하여 토크 및 추력의 변화를 관찰하였다. 본 연구를 위해 절삭성 평가장치를 개발하였으며 드릴링 가공 시 회 전 모터에 걸리는 토크와 시편이 받는 힘(추력)을 로드셀 을 이용하여 측정하는 원리로 토크와 추력 변화에 따른 절삭/가공 특성을 간접적으로 평가하는 방법이다[16]. 그림 10은 MoS2의 첨가량에 따른 토크와 추력의 평균 값 을 비교한 그래프이며, MoS2 첨가에 따른 토크와 추력 값 이 감소하는 것을 확인하였다. MoS2 첨가량이 0.7 wt% 일 때 평균 토크와 추력 값이 가장 낮은 7.88 kgf와 0.23 Nm로 나타났으며, 1 wt% 첨가되었을 경우 추력 값이 8.99 kgf로 소폭 상승하였다. 이는 MoS2 첨가에 따른 2상 석출 영역의 확대와 연관되어 있으며, 0.7 wt%이상의 MoS2 첨 가 시에는 상대적으로 높은 경도를 갖는 2상 석출물 양의 증가로 인해 절삭성을 떨어뜨리는 것으로 판단되는데 이에 대한 추가적인 연구가 필요하다. 결론적으로 MoS2는 Fe-Cr-Mn-C-V계의 합금의 첨가되어 절삭성에 직접적인 영향을 미 치는 성분으로 본 연구에서는 MoS2를 0.7 wt% 첨가 시에 가공/절삭 특성이 가장 향상되었음을 확인하였다.
홀 가공에 있어서 생성되는 칩을 효율적으로 배출시키 는 것이 가공 측면에서는 중요하여 MoS2 첨가량에 따른 절삭 가공 후 칩 형상에 대한 관찰을 진행하였다. 그림 11 은 MoS2 첨가 여부에 따른 절삭 가공 후 배출된 칩의 SEM 이미지를 보여준다. 그림 11(a)와 같이 MoS2가 첨가 되지 않은 시편에서는 마찰 후 생성된 칩의 가장자리가 불연속적이며 마찰표면 또한 상대적으로 거친 형상을 나 타내고 있다. 그에 반해 MoS2가 첨가된 시편에서는 발생 된 칩이 끊기지 않고 연속적으로 흘러나가는 형태의 유동 형 칩이 배출되었으며(그림 11(b)), 이는 본 연구에서 MoS2는 드릴 가공 시 칩 처리성을 우수하게 하는 중요한 인자로 판단할 수 있다. 따라서 토크와 추력에 대한 결과 와 칩 형상을 종합적으로 고려하였을 때 MoS2의 첨가가 절삭성 향상에 효과가 있는 것으로 사료된다.
4. 결 과
본 연구에서는 Fe-Cr-Mn-V-C계 합금에 MoS2 첨가에 따 른 소결시편의 미세조직 및 기계적 특성변화를 분석하여 다음과 같은 연구결과를 얻었다.
MoS2 첨가에 따른 소결시편의 미세조직은 소결과정에 서 MoS2가 Mo와 S로 분해되어 Mo가 Fe와 결합하여 페 라이트 기지에 2상 석출 조직인 Fe-Mo탄화물을 형성하였 다. Fe-Mo 탄화물로 인해 기계적 특성이 향상되었으나, MoS2가 1 wt%이상이 첨가되면 소결과정에서 분해되지 않은 MoS2가 결정립계를 따라 기공과 함께 석출물 형태 로 잔존함으로써 기계적 특성이 오히려 저하 되는 것을 실험적으로 확인하였다.
드릴링을 통한 토크와 추력에 의해 제조된 시편의 절삭성 을 간접적으로 측정한 결과, MoS2의 첨가가 절삭특성을 향 상 시켰으며, 유동형 칩이 발생하는 것을 관찰하였다.
본 실험을 통하여 경도 및 인장 값과 절삭가공성을 고 려하였을 때, MoS2의 가장 적절한 첨가량은 0.7 wt%로 확 인되었으며, 추후 MoS2의 2상 석출조직이 절삭성에 미치 는 영향에 대한 연구 및 MnS와 같은 절삭성 향상 원소를 첨가하여 비교 분석 연구를 수행할 예정이다.
감사의 글
본 연구는 지식경제부 산업원천기술개발사업의 연구비 지원으로 수행 되었습니다(과제번호 : 10033672).