Kinetic spray 공정을 이용한 Cu repair 코팅 소재 제조 및 열처리에 따른 미세조직과 물성 변화
Manufacturing of Cu Repair Coating Material Using the Kinetic Spray Process and Changes in the Microstructures and Properties by Heat Treatment
Article information
Abstract
This study is a basic research for repair material production which manufactured a Cu repair coating layer on the base material of a Cu plate using kinetic spray process. Furthermore, the manufactured material underwent an annealing heat treatment, and the changes of microstructure and macroscopic properties in the Cu repair coating layer and base material were examined. The powder feedstocks were sphere-shaped pure Cu powders with an average size of 27.7 μm. The produced repair coating material featured 600 μm thickness and 0.8% porosity, and it had an identical α-Cu single phase as the early powder. The produced Cu repair coating material and base material displayed extremely high adhesion characteristics that produced a boundary difficult to identify. Composition analysis confirmed that the impurities in the base material and repair coating material had no significant differences. Microstructure observation after a 500°C/1hr. heat treatment (vacuum condition) identified recovery, recrystallization and grain growth in the repair coating material and featured a more homogeneous microstructure. The hardness difference (ΔHv) between the repair coating material and base material significantly reduced from 87 to 34 after undergoing heat treatment.
1. 서 론
스퍼터링 타겟 소재는 스퍼터링 공정의 원료 물질로서 일반적으로 주조, 압연 공정을 이용한 제조법 및 분말을 기본으로 하여 성형체 제조, 소결(sintering), HIP(hot isostatic pressing) 등을 이용한 제조법 등으로 생산되고 있 다[1-3]. 이러한 스퍼터링 타겟 소재는 스퍼터링 공정을 통하여 최소 30~40%, 최대 70%까지 사용된 후 폐 타겟재 로 처리된다[4, 5]. 이에 고가의 스퍼터링 타겟 소재에 대 하여 폐 타겟재를 다시 재활용할 수 있는 기술에 대하여 관심이 증가하고 있다.
최근 Yoon 등[6]은 순수 Ru 폐타겟재를 사용하고 플라 즈마 공정을 이용하여 고순도 Ru 분말을 제조하고 이를 다시 Ru 스퍼터링 타겟 소재로 제조하는 폐타겟 재활용 및 타겟 제조 기술을 개발한 바 있다. 그러나 이 경우 폐타 겟 세척, backing plate와 분리, 폐타겟 재용융, 분말 제조, 소 결, 성형, backing plate에 재접합, 특성 제어를 위한 후가공 등 수많은 단계의 공정이 필요하며 높은 재생산 비용의 문 제점이 있다. 따라서 보다 단순한 공정으로 제조될 수 있는 경제성 있는 폐타겟 재활용 기술이 요구되고 있다.
Kinetic spray 공정은 보통 1~50 μm의 입도를 가지는 금 속이나 복합 재료 분말을 고압의 N2, He, air 혹은 혼합 가 스등을 이용하여 초음속(500~1200 m/s)으로 가속화시켜 치밀한 코팅층을 형성하는 기술이다[3]. 이 공정은 고온의 열원을 사용하지 않고 운동 에너지에 의한 소성 변형을 통해 모재 표면에 입자를 적층시킬 수 있기 때문에, 타 열 원을 사용한 일반 용사 코팅 공정인 arc, flame, 플라즈마, HVOF(high velocity oxy-fuel) 등과는 다르게 산화물 생성 이나, 상변화가 거의 일어나지 않는 장점을 가지고 있다. 저자들은 상기 kinetic spray 공정을 이용하여 열적으로 민 감한 소재인 Cu계, Ti, Ta 코팅 소재 등을 제조하고, 후 가 공처리를 통해 물성을 제어하여 고밀도, 고순도 스퍼터링 타겟 소재 제조의 기초 연구를 수행한 바 있다[7-9].
한편 폐타겟에 대하여 간단한 표면 세척 처리 후 kinetic spray 공정을 이용하여 분말을 폐타겟에 적층시켜 타겟으 로 다시 제조할 경우 적층된 소재에서 산화물 등 불순물 을 억제할 수 있고 제조되는 타겟재의 형상 제어가 가능 하며 밀도도 높은 repair 소재를 제조할 수 있을 것으로 예 상된다. 즉 kinetic spray 공정이 폐타겟 direct-repair 기술 로서 적용 가능성이 높을 것으로 판단된다.
한편 기존의 용사 코팅 공정 및 kinetic spray 공정을 이 용하여 구조용 부품의 파손 부위를 repair 시도한 연구들 이 보고되어 왔다. Sahraoui 등[10]은 HVOF 공정을 이용 하여 Cr, Cr3C2-25%NiCr, WC-12%Co 등의 소재를 gas turbine shaft의 repair에 사용하고 마모 특성을 조사하였다 . Champagne 등[11]은 kinetic spray 공정을 사용하여 마그네 슘 rotorcraft components 를 제조, 시도한 바 있다. 그러나 현 재까지 kinetic spray 공정을 이용하여 스퍼터링 타겟용 소재 의 direct-repair 를 시도한 연구는 보고된 바 없다.
본 연구에서는 kinetic spray 공정을 이용한 폐타겟의 direct-repair의 기초 연구로서, Cu 판재(모재)에 kinetic spray 공정을 이용하여 Cu 분말을 적층시켜 repair 코팅 소 재를 제조하고 그 미세조직과 물성을 조사하였다. 이와 함 께 repair 코팅 소재의 미세조직 및 물성에 미치는 열처리 영향에 대해서도 함께 조사해 보았다.
2. 실험방법
본 연구에 사용된 분말은 atomization 법으로 제조된 순 수 Cu 분말이었다. 그림 1은 SEM(scanning electron microscope)을 이용하여 관찰한 feedstock Cu 분말의 형상 (a), 분말의 내부 조직(b) 및 분말 입자의 크기 분포(c)를 제시한 것이다. 사용된 분말은 모두 구형의 형상을 가지고 있었으며 18~38 μm의 분말 입자 크기 분포를 가지고 평 균 입자 크기는 27.7 μm로 측정되었다.
3. 결과 및 고찰
Kinetic spray 공정을 이용하여 제조된 Cu repair 코팅층 의 광학 현미경 관찰 사진(에칭하지 않은 사진(a), 에칭한 미세조직 사진(b))을 그림 2에 나타내었다. 그림에서 알 수 있듯이 모재와 동일한 소재(Cu) 분말을 사용하여 코팅 층을 제조한 결과 에칭하지 않은 경우(a)에는 모재와 코팅 층 사이의 계면이 거의 구분되지 않았다. 에칭한 시편의 경우 미세조직의 차이를 통해 코팅층과 모재의 계면을 확 인 할 수 있었다. 단면 관찰 결과 코팅층은 600 μm 수준 의 두께를 가지며 모재와 박리 없이 잘 결합되어 적층되 어 있었다. 제조된 Cu repair 코팅층은 기공도 0.8%를 나 타내는 높은 밀도의 소재임을 확인할 수 있었다.
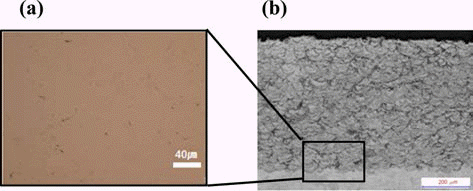
Optical microscopies of kinetic sprayed Cu repair coating material: (a) unetched and (b) etched conditions.
상기 분말을 이용하여 선행 시험을 수행하였으며, 그 결 과를 토대로 얻어진 표 1의 kinetic spray 공정 조건으로 Cu repair 코팅층을 제조하였다. 모재는 순수 Cu의 평판을 사용하였으며, 송급 가스는 He(helium) 가스를, 분말 예열 온도는 300°C로, 노즐 압력은 26 bar, 용사 거리는 30 mm, 노즐은 de laval 타입을 사용하여 제조하였다.
제조된 코팅층 및 모재의 미세조직과 상분석을 위하여 단면으로 절단 후 마운팅(mounting)하고 SiC paper #2000 까지 연마한 뒤 diamond paste 1 μm 수준까지 미세 연마 하였다. 연마된 시편에 대해서 광학 현미경을 이용하여 repair 코팅층의 두께와 적정 형성 유무를 확인하였다. 기 공도는 시편을 200 배율로 조직을 관찰한 후 이미지 분석 (image analyzer) 프로그램을 이용하여 측정하였다. 기공도 측정의 신뢰성을 높이고자 시편의 모든 영역에서 20장의 조직 사진(배율 200)을 찍고 분석에 사용하였다. 한편 미 세조직은 연마된 시편에 대하여 질산:증류수=6:4 비율로 에칭한 후 관찰하였다. 제조된 코팅층과 초기 분말의 경도 측정을 위하여 micro Vickers hardness 장비를 사용하였다. 코팅층의 경우 부위별 경도값이 다를 것을 예상하여 하중 50 g, 10초 부여 조건으로 부위별로 12회씩 경도 측정한 후 최대, 최소값을 제외한 평균값을 사용하였다. SEM/ EDS(scanning electron microscopy/energy dispersive X-ray spectrometer)를 사용하여 초기 분말과 제조된 코팅층의 조성 및 내부 미세조직을 조사하였다. 이와 함께 XRD(Xray diffraction, Ultima VI)를 이용하여 초기 분말, 제조된 코팅층을 분석하여 코팅 공정 전, 후 산화물 생성이나, 상 변화 유무를 확인하였다. 제조된 코팅층과 모재의 미세조 직 및 특성의 차이를 줄이기 위하여 튜브 로에서 어닐링 열 처리를 수행하였다. 열처리 조건은 진공 분위기(2×10−2 torr. 이하)에서 목표 온도까지 5°C/min. 속도로 승온하고, 목표 온도(500°C)에서 한 시간 유지한 뒤 노냉(furnace cooling) 하였다. 열처리된 시편은 as-sprayed 시편과 마찬가지로 기공도와 경도를 측정하였고 XRD 및 EDS line scan 분석 을 통하여 열처리 전 후 시편을 비교, 분석하였다.
제조된 Cu repair 소재의 XRD 분석 결과를 그림 3(a)에 나타내었다. 초기 분말 및 repair 소재가 모두 동일한 α- Cu 단상만을 보였으며, XRD 결과에서 산화물은 검출되지 않았다. 그림 3(b)는 EDS line scan분석을 이용하여 모재 와 제조된 repair 코팅 소재의 Cu 및 O원소의 함량을 측 정, 비교한 결과이다. 제조된 repair 코팅층에서 모재와 유 사한 함량과 분포의 Cu 및 O 원소가 검출되었다. 즉 코팅 소재나 모재와의 경계면에서 특별하게 높은 수준의 O 불 순물이 나타나지 않았다. 이상의 결과들을 통해 상변화나 산화물의 생성을 억제할 수 있는 kinetic spray 공정의 장 점을 활용하여 Cu repair 소재 제조가 가능함을 확인할 수 있었다.
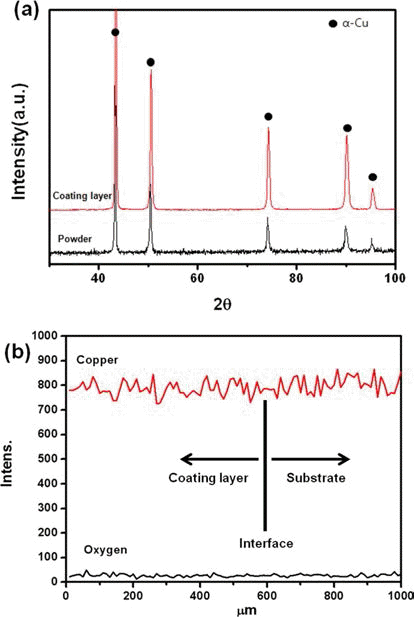
Result of (a) XRD analysis of initial powder and kinetic sprayed Cu repair coating material and (b) EDS line scan analysis of Cu repair coating and base materials.
그림 4(a)는 제조된 Cu repair 코팅 소재를 SEM 으로 관 찰한 미세조직 결과이다. 초기 구형의 형상을 가지고 있던 Cu 분말들이 높은 속도의 입자 분사를 통해 최종적으로 길게 연신, 적층되어 있는 모습을 나타내고 있다. 일반적 으로 분말의 용융 없이 상기와 같이 길게 연신되어 적층 될 경우, 큰 소성 변형에 의한 가공 경화 효과를 보인다고 알려져 있다. 이와 함께 사진에서 형성된 repair 코팅 소재 가 매우 조밀한 구조를 가지고 있음을 다시 한번 확인할 수 있다. Cu repair 코팅 소재의 측정 위치(b)별 경도값(c) 측정 결과를 그림 4에 추가적으로 나타내었다. 코팅 소재 의 경도값은 137~159 Hv수준으로 측정되었으며 코팅 소 재 표면에서 모재와의 계면으로 가까워질수록 그 값이 상 승하는 경향을 보였다. 모재의 경우도 코팅 소재와의 경계 면에서 멀어질수록 경도값이 감소하고 있다. 이는 초기 분 말이 모재에 적층된 후 분말들이 연속적으로 추가 적층되 어 경계면(interface)에 가까운 입자들이 더 많은 변형을 받게 되어(peening 효과) 그 결과 경도값이 높아지는 것으 로 이해될 수 있다. 한편 저온 분사 전 모재의 경도는 평 균 65 Hv였으나 코팅 소재 적층 후 모재도 경계면 근처에 서 97까지 증가하는 결과를 통해, 적층되어 쌓이는 분말 입자들이 모재에도 소성 변형에 의한 가공 경화 효과를 가져오는 것으로 유추할 수 있다.
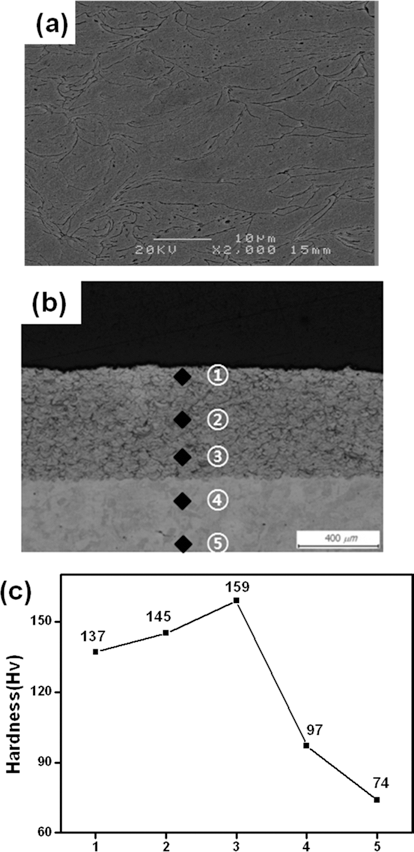
(a) SEM microscopy of etched Cu repair coating material, (b) hardness indentation positions and (c) results of Vickers hardness measurements (each number indicates the position in (b)).
그림 5는 500°C/1 hr. 어닐링 열처리 후 코팅 소재 중심 부(a)와 코팅 소재/모재의 경계면(b)을 SEM 으로 관찰한 사진들이다. 미세조직 관찰 결과(그림 5(a)), 열처리 전의 연신되고 불균일했던 조직(그림 4(a))에서, 전체적으로 회 복, 재결정 등의 조직 변화가 활발하게 일어났으며, 그 결 과 약 5 μm 크기의 미세한 결정립을 갖는 균질화된 조직 으로 변화하였다. 모재(b) 역시 열처리 이후 결정립 성장 이 일어나고 더욱 커진 결정립 조직이 관찰되었다. 즉, 초 기 저온 분사된 코팅 소재의 심한 소성 변형 조직과 모재의 조대한 결정립 조직이 열처리를 수행함에 따라서 회복, 재 결정, 결정립성장으로 인해 변화함을 확인 할 수 있었다. 한편 에칭하지 않고 측정되는 기공도 측정 결과 열처리 전 0.8% 였던 repair 코팅 소재의 기공도가 열처리 이후에 는 0.5% 수준으로 감소하였다. 이는 본 연구진에서 이전 보고한 바 있는 저온 분사 Cu 코팅층의 열처리 후 기공도 와 유사한 수준이다[12].
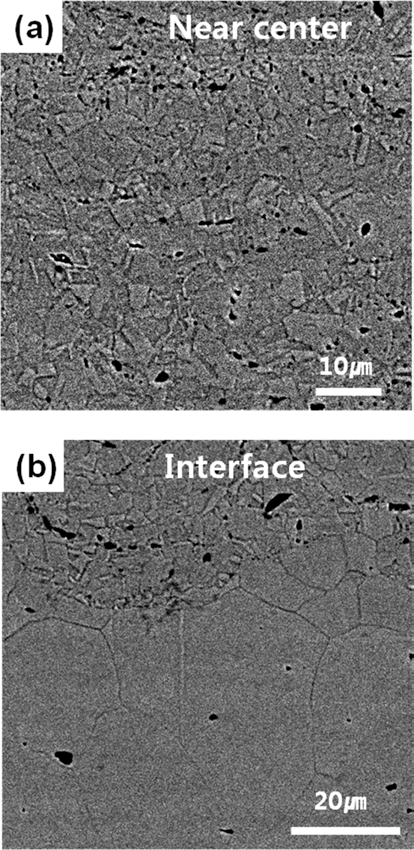
Microstructure observation results (a) inside Cu repair coating material and (b) near interface with substrate after annealing heat treatment (vacuum condition, 500°C/1hr.).
열처리 이후 XRD분석 결과(a) 및 EDS line scan 분석 결과(b)를 그림 6에 나타내었다. 그 결과(a) Cu repair 코 팅 소재와 모재는 열처리 이후에도 열처리 이전과 동일한 α-Cu 단상만을 가지고 있었다. 또한 XRD 결과에서 확연 한 다른 상 변화나 추가적인 산화물 생성은 나타나지 않 았다. 열처리한 시편의 EDS line scan 결과(b)에서도 코팅 층과 모재 모두에서 O원소 불순물의 함량 및 분포가 큰 차이 없이 유사하게 측정되었다. 또한 열처리 이후 부위별 Cu 원소 함량이 열처리 전 시편의 결과(그림 3(b))와 비교 하였을 때 더욱 균일하게 분포하고 있음을 알 수 있었다.
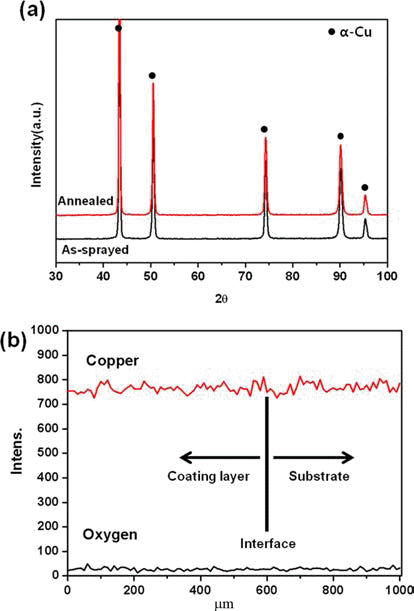
Result of (a) XRD analysis of kinetic sprayed and annealed Cu repair coatin materials, and (b) EDS line scan analysis of the material after annealing heat treatment (vacuum condition, 500°C/1 hr).
그림 7은 열처리 이후(annealed) 위치별로 코팅층과 모 재의 경도를 측정한 결과를 열처리 전(as-sprayed) 결과와 비교하여 나타낸 것이다. 최대 159 Hv 값을 나타내던 열 처리 전 Cu repair 코팅 소재의 경도값은 열처리 이후 최 대 63 Hv로 측정되었다. 열처리 이후 코팅 소재와 모재 모두에서 경도가 감소하는 경향을 보였다. 또한 열처리를 수행한 후 repair 코팅 소재 내부에서의 부위별 경도가 50~63의 분포로 나타났으며, 모재 내부에서의 경도는 40~44로 모두 감소함을 알 수 있다. 특히 열처리 이전에 모재와 코팅 소재의 경도 차이는 85 Hv가 났지만, 열처리 를 통하여 경도차이는 23 Hv로 확연히 줄어든 것에 주목 할 만하다. 즉 kinetic spray 공정으로 제조된 Cu repair 코 팅 소재/모재의 경우 열처리를 통하여 제조된 코팅층과 모 재의 특성 차이를 적게 조절할 수 있었다. 이는 그림 4(a) 와 그림 5에서 관찰된 미세조직 결과에서 알 수 있듯이 심 한 변형 조직으로 구성되어 있던 repair 코팅 소재의 미세 조직이 열처링 이후에도 여전히 모재와 차이는 존재하지 만 회복, 재결정, 결정립 성장 등의 과정을 통해 변화 (evolution)되고 그 미세조직학적 차이가 줄어들며 균일화 되는 데 기인하는 것으로 판단된다.
4. 결 론
본 연구에서는 Cu 모재 위에 kinetic spray 공정을 이용 하여 Cu repair 코팅 소재를 제조하였으며, 열처리에 따른 미세조직 및 특성 변화를 알아보고 다음과 같은 결론을 얻을 수 있었다.
Kinetic spray 공정으로 Cu 모재에 순수 Cu 분말을 이 용하여 repair 코팅 소재를 제조할 수 있었다. 제조된 코팅 소재의 두께는 600 μm 수준이었고, 0.8%의 기공도를 가 지는 고밀도 소재였다. 제조된 코팅 소재와/모재의 계면은 에칭을 하기 전에는 구분이 어려울 정도로 잘 결합되어 있었다.
저온 분사 공정으로 제조된 Cu repair 소재의 경우 초 기 사용한 분말과 동일한 α-Cu 상으로 구성되어 있었고 추가적인 상변화가 일어나지 않았으며 모재와 비슷한 수 준의 O 불순물 함량을 포함하고 있었다. Repair 코팅 소 재의 경도값은 부위별로 차이를 나타내었으며 모재와 인 접한 경계로 갈수록 경도가 증가함을 알 수 있었다. 모재 의 경우도 저온 분사 공정 이후 경도값이 증가하였으며 모재/코팅 소재와의 경계면으로 갈수록 경도값이 더 크게 나타났다. 한편 저온 분사 공정으로 repair 된 Cu 소재의 경우 길게 연신된 형태의 적층 모양을 보였으며 심한 변 형 조직을 나타내었다.
제조된 저온 분사 Cu repair/모재 소재에 대하여 500°C, 1시간, 진공 분위기 어닐링 열처리를 수행한 결과 기공도가 0.5% 수준으로 감소하였다. 열처리 이후에도 새 로운 상의 생성은 없었으며 repair 층의 Cu 성분은 더욱 균일하게 분포되었고O 불순물의 경우도 모재와 repair 소 재에서 유사한 수준으로 확인되었다. 이와 함께 열처리 전 심한 변형 조직이었던 repair 소재가 열처리를 통하여 회 복, 재결정, 결정립 성장 등이 일어나 상대적으로 균일한 미세조직을 나타내었다. 모재의 경우도 열처리에 따라 추가 적인 결정립 성장이 일어났다. 열처리 후 repair 소재와 모 재 모두에서 부위별 경도값의 차이가 각각 감소하였고 repair 소재와 모재의 경도값 차이도 현저하게 감소하여 열 처리를 통하여 특성이 더욱 균일해짐을 확인할 수 있었다.
감사의 글
본 연구는 산업 자원 통상부의 “산업 원천 기술 개발 사 업”과 미래 창조 과학부와 한국 연구 재단의 “지역 혁신 창의 인력 양성 사업”의 연구비 지원으로 수행되었으며 이에 감사드립니다.