SnO2-CoO/carbon-coated CoO core/shell 나노선 복합체의 합성 및 구조분석
Synthesis and Characterization of SnO2-CoO/carbon-coated CoO Core/shell Nanowire Composites
Article information
Abstract
SnO2-CoO/carbon-coated CoO core/shell nanowire composites were synthesized by using electrospinning and hydrothermal methods. In order to obtain SnO2-CoO/carbon-coated CoO core/shell nanowire composites, SnO2-Co3O4 nanowire composites and SnO2-Co3O4/polygonal Co3O4 core/shell nanowire composites are also synthesized. To demonstrate their structural, chemical bonding, and morphological properties, field-emission scanning electron microscopy, transmission electron microscopy, X-ray diffraction, and X-ray photoelectron spectroscopy were carried out. These results indicated that the morphologies and structures of the samples were changed from SnO2-Co3O4 nanowires having cylindrical structures to SnO2-Co3O4/Co3O4 core/shell nanowires having polygonal structures after a hydrothermal process. At last, SnO2-CoO/carbon-coated CoO core/shell nanowire composites having irregular and high surface area are formed after carbon coating using a polypyrrole (PPy). Also, there occur phases transformation of cobalt phases from Co3O4 to CoO during carbon coating using a PPy under a argon atmosphere.
1. 서 론
최근 핸드폰, 노트북, PC 등과 같은 전자 기기 분야의 발달로 경박단소화, 휴대화 및 고출력화가 필수적으로 요 구됨에 따라 고성능 및 고효율의 에너지 저장장치에 대한 관심이 높아지고 있다. 다양한 에너지 저장장치 중에서 리 튬이온 전지는 다른 에너지 저장장치에 비해 높은 에너지 밀도(>150 Wh/kg), 높은 용량, 낮은 자가 방전율 및 넓은 작동전압 범위(~4 V) 등의 장점을 가지고 있기 때문에 차 세대 에너지 저장 소자로써 각광받고 있다[1, 2]. 리튬이온 전지는 크게 음극(anode)과 양극(cathode), 전해질(electrolyte) 및 분리막(separator)으로 구성되며 이온화 경향 차이가 큰 두 전극 사이에서 전해질을 통해 리튬 이온이 이동하면서 발생하는 전기화학반응으로 충전 및 방전이 이루어진다[3]. 따라서 리튬이온 전지의 성능향상을 위해서는 우수한 충 전 및 방전 특성과 가역 특성을 지닌 전극재료의 개발이 반드시 필요하다. 지금까지는 흑연(graphite)이 가장 대표 적인 리튬이온 전지의 음극 물질로 알려져 있으며 이러한 흑연은 안정한 층상구조의 특성을 갖고 있어 우수한 충전 및 방전 성능을 제공하는 반면에 이론용량이(~372 mAh/ g) 낮다는 한계로 고용량을 요구하는 전자기기에 실질적 인 적용이 제한되고 있다[4, 5]. 따라서 음극 재료인 흑연 을 대체하기 위한 새로운 물질로써 고용량 특성을 갖는 산화물 기반 물질들(SnO2, SiO2, CoO, Fe2O3 등)에 대한 연구가 많이 이루어지고 있다[6]. 하지만, 산화물 기반의 물질은 일반적으로 충전 및 방전 과정에서 발생하는 리튬 이온의 삽입/탈리에 의해 전극에 큰 부피 변화를 유발하게 된다. 이러한 전극 재료의 부피 변화는 리튬이온 전지의 수명 특성에 악영향을 미치기 때문에 산화물 기반 물질을 전극으로 사용하기 위해서는 반드시 위와 같은 문제점을 해결해야 한다. 지금까지 전극 물질의 부피 변화를 최소화 하기 위해서 (1) 일차원 나노선과 같은 geometry 제어하는 방법, (2) 복합체 형성하는 방법 및 (3) 전극 코팅하는 방 법 등의 전략들이 연구되어 왔다. 일차원 나노 구조는 다 른 차원의 구조에 비해 리튬 거동에 의한 부피 변화가 작 을 뿐만 아니라 넓은 부피 대비 표면적(surface area to volume ratio)과 전자 이동에 용이한 통로 역할을 하기 때 문에 우수한 전기화학적 특성을 제공할 수 있다[7]. 예를 들면, An 등은 순수한 TiO2 나노선을 전기 방사법으로 합 성한 후 TiO2 나노 입자와 함께 전기화학적 특성을 비교 평가하였으며 결과적으로 나노선 전극이 나노 입자보다 우수한 초기용량 및 가역용량을 나타내는 것을 확인하였 다[7]. 복합체 형성의 경우, 전극 내 존재하는 물질들이 활 성화되는 전위의 차이를 이용하여 전극 내 반응을 제어함 으로써 충전 및 방전 시 발생하는 부피 변화를 최소화할 수 있다[8]. 예를 들면, Nithya 등은 볼밀을 이용하여 SnxSbyCuz를 합성하였으며 물질을 이루는 각 원소의 비율 조절을 통해 Sn90Sb8Cu2에서 가장 우수한 초기 용량(~780 mAh/g)과 50 cycles 후 89.1%에 해당하는 용량 유지률 특 성을 보고하였다[9]. 특히, 전극 코팅하는 방법 중에 탄소 물질을 전극 표면에 코팅하는 연구는 탄소가 가지는 높은 기계적 강도, 높은 전기 전도도, 및 전기화학적 안정성에 의해 산화물 기반 전극 물질의 부피 팽창을 방지할 수 있 는 가장 확실한 방법이다. 예를 들면, Yoshio 등은 열기상 분해법을 통해 탄소가 코팅된 Si 입자를 제조하였고, 탄소 물질을 코팅한 것이 ~800 mAh/g의 우수한 용량과 콜롱 효율 및 우수한 수명특성을 제공한다는 것을 보고하였다 [10]. 이와 같이 전극 물질의 부피 변화를 최소화하기 위 한 각각의 방법들이 보고되고 있지만 아직까지 이 세가지 전략을 모두 사용하여 전극재료를 제조하는 연구는 미흡 한 실정이다.
따라서 본 연구에서는 충전 및 방전 과정에서 전극 재 료가 갖는 부피 변화의 문제를 최소화하고, 전기화학적 특 성을 향상 시키기 위하여 앞에서 언급한 세 가지 전략을 모두 사용하여 전극을 합성하였다. 이를 위해 리튬이온 전 지의 전극 물질 중에서도 높은 이론용량을 보이는 SnO2(~790 mAh/g)와 CoO(~715 mAh/g)를 선택하였으며 [11, 12], 전기방사법과 수열합성법을 이용하여 나노선 복 합체 제조 및 탄소 물질 코팅을 진행하였다. 따라서 우리 는 SnO2-CoO/carbon-coated CoO core/shell 나노선 복합체 를 성공적으로 제조하였으며 그들의 구조적 및 화학적 특 성을 규명하였다.
2. 실험방법
SnO2-CoO/carbon-coated CoO core/shell 나노선 복합체 를 제조하기 위하여 우리는 전기방사법과 수열합성법을 이용하여 3단계 공정을 진행하였다. 먼저 전기방사법을 이용한 SnO2-Co3O4 나노선 복합체의 합성은 다음과 같다. 4 wt%에 해당하는 tin(II) chloride dehydrate(SnCl2 ∙ 2H2O, Aldrich)를 ethanol(CH3CH2OH, Aldrich)에 용해시키고, 동 시에 Sn 전구체와 1:1의 무게비를 갖는 cobalt(III) acetate tetrahydrate((CH3COO)2Co ∙ 2H2O, Aldrich)를 N,N-dimethylformamide( DMF, Aldrich)에 30분간 용해시켰다. 그런 다음 균일하게 용해 된 Sn과 Co 용액을 섞고 충분히 혼합 하고, 이 용액에 11 wt%의 polyvinylpyrrolidone(PVP, Mw = 1,300,000 g/mol, Aldrich)를 첨가하여 전기방사를 위한 용액을 합성하였다. 제조된 용액을 23 gauge needle이 장 착된 syringe로 옮기고, syringe needle의 끝과 Al foil 포집 판 사이에 DC power supply을 이용해 ~9.5 kV에 해당하 는 고전압을 인가하여 전기방사를 실시하였다. 전기방사 에 영향을 미치는 변수인 syringe needle 끝과 Al foil 포 집판 사이 수직 거리는 15 cm로, syringe pump의 유량은 0.02 ml/h, 온도 및 습도는 각각 ~25°C 및 ~35%로 유지하 였다. 이렇게 포집된 나노선은 승온 속도를 1°C/min으로 설정하고 500°C에서 5 시간 동안 열처리하여 SnO2-Co3O4 나노선 복합체를 제조하였다. 두 번째 공정은 다음과 같이 진행되었다. 앞에서 제조한 SnO2-Co3O4 나노선 복합체에 Co 전구체인 cobalt(II) nitrate hyxahydrate(Co(NO3)2 ∙ 6H2O, Aldrich), 그리고 계면활성제인 Hexadecyltrimethylammonium bromide(CH3(CH2)15N(Br)(CH3)3, CTAB, Aldrich) 을 DI water와 methanol이 혼합된 용매에 넣고 교반기를 이용하여 분산시켰다. 이 때 DI water와 methanol의 부피 비는 1:5로 고정하였다. 이것을 autoclave로 옮겨 180°C에 서 24 시간 동안 수열합성을 진행하였으며 반응이 완료된 물질을 DI water와 ethanol을 이용하여 3번 세척하고, 80°C에서 건조시킨 다음 400°C에서 5 시간 동안 열처리하 여 SnO2-Co3O4/ polygonal Co3O4 core/shell나노선 복합체 를 제조하였다. 마지막으로 SnO2-CoO/carbon-coated CoO core/shell 나노선 복합체 제조법은 다음과 같다. DI water 에 앞에서 제조된 SnO2-Co3O4/polygonal Co3O4 core/shell 나노선 복합체와 polypyrrole(PPy, Aldrich)을 넣고 교반기 를 이용하여 충분히 분산시킨 다음, ammonium persulfate ((NH4)2S2O8, Aldrich)를 첨가하여 120°C에서 8 시간 유지 하였다. 특히 PPy는 화학적 및 전기화학적 방법들을 통한 합성 및 형태 제어에 용이 하기 때문에 선택하였다. 위와 마찬가지로 세척한 후에 Ar 분위기에서 400°C로 2 시간 열처리 하였다. 따라서 3단계 공정을 통하여 제조된 SnO2-Co3O4 나노선 복합체, SnO2-Co3O4/polygonal Co3O4 core/shell 나노선 복합체 및 SnO2-CoO/carbon-coated CoO core/shell 나노선 복합체는 본 논문에서 각각 sample A, sample B 및 sample C로 언급될 것이다.
제조된 물질들의 형태 및 구조분석은 주사 전자 현미경 (field-emission scanning electron microscopy, FESEM, Hitachi S-4800)과 투과 전자 현미경(transmission electron microscopy, TEM, Tecnai G2)을 이용하였고, 결정구조 및 화학적 결합상태의 분석은 X-선 회절분석(X-ray diffraction, XRD, Rigaku Rint 2500)과 X-선 광전자 주사법(X-ray photoelectron spectroscopy, XPS, ESCALAB 250 equipped with an Al Kα X-ray source)을 통하여 수행하였다.
3. 결과 및 고찰
그림 1은 SnO2-CoO/carbon-coated CoO core/shell 나노 선 복합체(sample C)의 제조를 위한 전기방사법의 모식도 및 실험과정을 간략하게 묘사하였다. 먼저 sample C의 core부분을 구성하고 있는 SnO2-Co3O4 나노선 복합체 (sample A) 제조를 위해 전기방사법을 이용하였다. 일반적 으로 전기방사법은 크게 용액 공급부(syringe, syringe pump, needle), 전압 인가부(power supply), 포집부(Al foil 포집판)로 구성되어 있으며 syringe needle 끝과 포집판 사 이에 인가되는 고전압이 needle 끝에서 일정하게 공급되 는 용액의 표면장력보다 높을 경우 방사가 발생하여 일차 원 형태의 나노선이 제조되는 원리를 갖는다. 더욱이 전기 방사법은 구동과 변수 제어가 용이하고, 대량생산이 가능 하여 일차원 나노선 제조를 위한 매력적인 합성법으로 알 려져 있다[13, 14]. 그런 다음, 미리 제조한 sample A 위에 polygonal Co3O4 성장 및 PPy를 이용한 carbon 코팅을 위 해서 수열합성법을 이용하였다. 수열합성법은 액상합성법 의 일종으로 물질이 고온 및 고압 하에서 용해도, 온도, 압 력 및 용매의 농도에 의존하는 특성을 이용해 재료를 합 성하거나 결정을 성장시키는 방법이다. 이 합성법은 공정 이 간단하고, 반응속도가 빠르며 형상과 크기 제어가 용이 한 장점이 있다[15]. 특히 본 연구에서는 수열합성법을 이 용하여 제조된 샘플들의 morphology 변화 및 상변화가 관 찰되었으며 이에 대한 자세한 내용은 뒷부분에서 자세히 다루도록 하겠다.

Schematic illustration of a synthetic process of SnO2- CoO/carbon-coated CoO core/shell nanowire composite using electrospinning and hydrothermal methods.
그림 2는 (a) sample A, (b) sample B, (c) sample C의 FESEM 이미지를 보여준다. 전기방사법을 이용하여 제조 된 sample A는 그림 2(a)에서 보여지듯이 매끈한 표면을 갖는 일차원 나노선의 형상을 하고 있으며 약 182-205 nm 직경을 갖는다. Sample B의 경우는 sample A의 표면을 따 라 약 100-128 nm의 크기의 polygonal 입자가 고르게 성 장하여 rough한 표면 형상을 보이며, sample B의 직경은 약 372~457 nm로 sample A 보다 다소 증가하였다. 이전 의 보고들에 의하면 Co3O4는 주로 (111) plane을 갖는 polygonal 형태로 성장한다[16, 17]. Sample B는 sample A 의 Co3O4가 결정 성장을 위한 seed 역할을 하여 수열합성 이 진행됨에 따라 polygonal 형상의 Co3O4 표면을 갖는 SnO2-Co3O4/polygonal Co3O4 core/shell 나노선 복합체가 형성되게 된다. 즉 다시 말하면 나노선 복합체 위에 polygonal Co3O4의 균일한 성장을 위해서 SnO2-Co3O4 nanowire composite를 도입하였으며 이러한 복합체 안의 Co3O4은 polygonal Co3O4결정 성장을 위한 seed 역할을 수행하게 된다. 이렇게 형성된 polygonal 나노선 복합체는 결국 나노선의 표면 roughness를 증가시키며 이러한 전극 의 표면적 향상은 리튬 이온 전지의 특성 향상에 기여할 것으로 사료된다. 따라서 FESEM 결과를 통하여 sample B의 표면에 성공적으로 polygonal Co3O4 층이 형성되었음 을 확인하였다. 이러한 전략은 일차원 나노선의 비표면적 향상을 위하여 도입 하였다. 더욱이 sample C는 제조된 sample B의 표면에 carbon 코팅을 실시한 것으로 직경은 약 566-663 nm의 범위 안에 놓여 있다. 즉, sample B보다 carbon 코팅 층만큼 그 직경이 증가한 것으로 판단되며 이 는 다시 말해 sample B의 표면 위로 carbon 코팅 층이 균 일하게 형성되었음을 의미한다. 이러한 carbon 코팅 층의 도입은 이차전지 전극의 부피팽창을 감소 시키기 위한 매 우 효율적인 전략에 해당된다. 이러한 core/shell 구조를 갖는 이중 코팅 층에 대해 더 자세히 분석하기 위하여 TEM 분석을 실시하였다.
그림 3는 sample C의 TEM 이미지를 나타낸다. 그림 3(a)에서 보여지듯이 sample C의 core 영역에는 지지체 역 할을 하는 나노선이 나타나고 있으며, shell 영역은 지지체 표면 위로 어두운 영역과 밝은 영역으로 이루어진 이중층 이 관찰되고 있다. Shell 영역에서 상대적으로 어두운 영 역은 polygonal 형태의 Co phases에 해당한다. 그림 3(a)를 통하여 나노선 표면에 성장한 입자들이 FESEM 이미지 (그림 2(b))에서 관찰되는 polygonal 형태와 달리 불규칙한 형태로 구성되어 있음을 알 수 있다. 이러한 Co phases의 형태 변화는 carbon 코팅 과정의 상변화에 의한 것으로 판 단되며 이러한 상변화에 대한 내용은 그림 4에서 더 자세 히 논의될 것이다. 또한, shell 영역에서 상대적으로 밝은 영역은 carbon 코팅 층에 해당하며 약 85-102 nm의 두께 로 나노선 복합체의 표면에 균일하게 코팅되어 있다. Carbon 코팅 층은 구조적 안정성이 우수하므로 수명 특성 을 향상시키고, 여기에 더하여 conducting polymer인 PPy 를 통해 carbon 코팅 층이 형성되므로 전기 전도도를 증 가시켜 리튬이온 전지의 특성 향상에 긍정적인 영향을 끼 칠 것으로 사료된다[12, 18]. 따라서 FESEM과 TEM 결과 를 통하여 core-shell 구조를 갖는 SnO2-CoO/carbon-coated CoO 나노선 복합체가 성공적으로 제조되었음을 확인하였 다. 우리는 각 샘플의 결정 구조 및 화학적 결합 특성에 대해 좀 더 알아보기 위하여 XRD 및 XPS 분석을 실시하 였다.
그림 4는 제조된 sample A, sample B, sample C의 XRD 회절 패턴을 보여주고 있다. Sample A와 sample B에서는 SnO2와 Co3O4에 해당하는 회절 피크가 동시에 나타나고 있다. 26.6°, 33.9°, 37.9°, 51.8°, 54.8°, 64.7°, 66.0°에서 보 여지는 특정 회절 피크들은 tetragonal rutile 구조를 갖는 SnO2(space group P42/mnm [136])에 해당하며 이들은 각 각 (110), (101), (200), (211), (220), (112), (301) planes와 일치한다(JCPDS card No. 88-0287). 또한 19.0°, 31.2°, 36.8°, 38.5°, 44.8°, 55.6°, 59.4°, 65.2°에서 보여지는 특정 회절 피크들은 face-centered cubic구조를 갖는 Co3O4(space group Fd3m [227])에 해당하고, 각각의 회절 피크들은 (111), (220), (311), (222), (400), (422), (511), (440) planes 와 일치한다(JCPDS card No. 78-1970). 즉, XRD 분석 결 과를 통해 sample A와 sample B는 SnO2와 Co3O4가 동시 에 존재하고 있는 나노선 복합체임을 알 수 있다. 하지만 sample B의 경우는 SnO2에 해당하는 피크들의 강도가 감 소하였으며, 반대로 Co3O4에 해당하는 피크들의 강도는 크게 증가하였다. 이러한 현상의 원인은 수열합성 과정에 의해 나노선 복합체 표면(shell 영역)에 결정성이 매우 높 은 polygonal Co3O4가 성장하였기 때문이다. 뿐만 아니라 sample C에서는 sample A와 sample B와는 다른 피크들이 관찰되고 있다. 이는 CoO에 해당하는 피크들로 각각 36.5°, 42.4°, 61.5°, 73.7°, 77.6°에서 (111), (200), (220), (311), (222) planes에 대응하여 나타나고 있으며 이를 통 해 face-centered cubic구조(space group Fm3m [225])임을 확인하였다(JCPDS card No. 48-1719). 이러한 상변화는 carbon을 코팅하는 과정에서의 carbothermal 반응에 기인 한다. Carbothermal 반응은 금속산화물과 carbon의 엔트로 피 차이에 의해 발생하는데 carbon이 금속산화물 보다 산 화되는 반응 엔트로피가 더 높기 때문에 가해진 열에 의 해 carbon의 일부가 CO gas로 변하게 된다. 이와 동시에 금속산화물에서는 환원이 발생하게 되어 결과적으로 Co3O4에서 CoO로의 상변화가 발생하게 된다[12]. 반면, carbon은 비교적 낮은 온도(400°C)에서 탄화가 진행되기 때문에 코팅된 carbon층에서 결정화가 발생하지 않아 관 련 피크들이 XRD에서는 관찰되지 않고 있다.
그림 5는 모든 샘플들의 각 원소별 XPS스펙트럼을 보 여준다. 관찰된 모든 스펙트럼의 피크들은 C 1s line(284.5 eV)을 기준으로 보정하였다. Sample A와 sample B의 Sn 3d5/2 및 Sn 3d3/2 photoelectrons에 대한 XPS 피크들은 ~486.6 eV와 ~495.1 eV에서 관찰되고, 이는 Sn 원소가 Sn(IV) states, 즉, SnO2로 존재함을 의미한다[19]. 또한, Co 2p3/2과 Co 2p1/2 photoelectrons에 대한 XPS 피크들은 ~779.8 eV 및 ~795.0 eV와 ~781.8 eV 및 ~797.0 eV에서 나타나는데 이들은 각각 Co(III) states 와 Co(II) states임 을 의미한다. 따라서 Co 원소는 Co(II) states와 Co(III) states가 1:2의 비로 결합하여 형성된 Co3O4 (CoCo2O4)로 존재함을 알 수 있다[20]. 더하여 이 피크들보다 높은 결 합에너지인 ~788 eV 및 ~804 eV에서는 Co 원소의 statellite 피크들이 관찰되고 있다. 이러한 XPS 결과는 위 XRD결 과와도 잘 일치한다. 또한, sample C의 XPS 분석을 통해 서는 carbon 코팅 층의 표면 상태를 알 수가 있다. Carbon 코팅 층은 주로 C-C결합(~284.6 eV)을 하고 있고, C=O결 합(~288.1 eV)도 일부 존재하고 있다[17]. 여기서 특히 주 목할 것은 C-N 결합(~285.9 eV)이다[17]. Carbon의 전구 체인 PPy에는 N 원자가 많이 포함되어 있으므로 코팅과 정에서 carbon으로의 doping이 발생하여 XPS 분석에서 C-N결합이 관찰되고 있다. 하지만 sample C의 다른 원소 들의 결합상태는 carbon 코팅 층의 두께가 X-ray 의 침투 깊이보다 두껍기 때문에 XPS에서 잘 나타나지 않아 이를 이용한 XPS 분석에는 어려움이 있다.
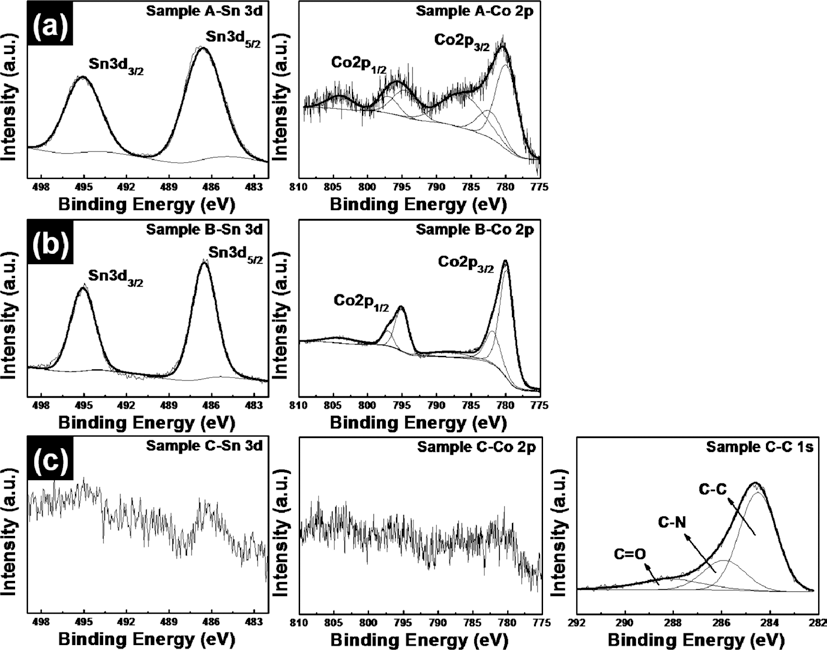
XPS spectra of the Sn 3d, Co 2p, and C 1s core levels for (a) sample A, (b) sample B, and (c) sample C.
따라서 지금까지의 FESEM, TEM, XRD 및 XPS 분석 을 모두 종합하였을 때 우리는 SnO2-CoO/carbon-coated CoO core/shell 나노선 복합체가 성공적을 제조되었음을 알 수 있었다. 이러한 나노선 복합체의 경우 리튬이온 전 지의 음극 전극으로 사용이 가능하며 전극 물질의 부피 변화를 최소화하여 전극 성능 향상에 크게 기여할 수 있 을 것으로 사료된다.
4. 결 론
본 연구에서는 전기방사법과 수열합성법을 이용하여 SnO2-CoO/carbon-coated CoO core/shell 나노선 복합체를 성공적으로 합성하였다. 이를 위해서 전기방사법을 이용 한 SnO2-Co3O4 나노선 복합체를 우선적으로 합성하였고 추가적으로 수열합성법 공정을 통해 복합체 표면에 Co 산 화물 입자를 성장시켰다. 그 결과 polygonal 형태의 Co3O4 가 표면을 따라 연속적으로 형성되었음을 확인할 수 있었 다. 일반적으로 이러한 산화물 기반 물질을 리튬이온 전지 의 전극으로 활용할 경우 리튬 이온의 거동에 의해 전극 구조의 부피 팽창이 발생하여 수명 등의 특성 저하가 발 생하게 된다. 이를 해결하기 위한 목적으로 제조된 나노선 복합체 표면에 PPy를 이용하여 carbon 코팅을 시도하였다. 그 결과 균일한 carbon 층이 우선적으로 코팅된 polygonal Co3O4 위에 적절히 형성되었음을 확인하였다. 하지만 carbon 코팅 과정에서 Co3O4에서 CoO로 변화함에 따라 polygonal 형태의 입자가 불규칙한 형태로 변화하였다. 이 러한 현상은 PPy를 이용한 carbon 코팅 시 carbothermal 반응으로 인하여 PPy가 환원반응의 반응기로 작용하는데 이는 Co3O4에서 CoO로의 상변화를 발생시키기 때문이다. 결과적으로 전극재료의 부피변화를 최소화하기 위해 사용 되는 (1) geometry 제어를 통한 일차원 나노선 제조, (2) 산화물 복합체 형성, (3) carbon 코팅 층 도입 전략을 모 두 고려하여 제조된 SnO2-CoO/carbon-coated CoO core/ shell 나노선 복합체는 고효율 리튬이온 전지를 위한 전극 재료로써 사용이 가능할 것이다.
감사의 글
This study was financially supported by the Research Program funded by the Seoul National University of Science and Technology.