단결정 다이아몬드공구를 사용한 Cu 도금된 몰드의 미세 구조체 가공특성
Machining Characteristics of Micro Structure using Single-Crystal Diamond Tool on Cu-plated Mold
Article information
Abstract
The optical film for light luminance improvement of back light unit that is used in light emitting diode/liquid crystal display and retro-reflective film is used as luminous sign consist of square and triangular pyramid structure pattern based on V-shape micro prism pattern. In this study, we analyzed machining characteristics of Cu-plated flat mold by shaping with diamond tool. First, cutting conditions were optimized as V-groove machining for the experiment of micro prism structure mold machining with prism pattern shape, cutting force and roughness. Second, the micro prism structure such as square and triangular pyramid pattern were machined by cross machining method with optimizing cutting conditions. Variation of Burr and chip shape were discussed by material properties and machining method.
1. 서 론
최근의 광학부품은 표면에 미세패턴을 부여하여 광확산, 광반사 및 광효율을 향상시키는 방향으로 발전하고 있다 [1]. 특히 최근에 많이 사용되고 있는 LCD (Liquid Crystal Display) 및 LED (Light Emitting Diode) 장치의 BLU (Back Light Unit) 필름 및 야광 재귀반사용 필름 등은 미 세 V형 프리즘 구조체를 기반으로 하여 제조되며, 이들 구조체 어레이의 정밀도에 따라 그 광학적 성능이 좌우되 고 있다. 이에 따라 이러한 미세 구조체 패턴을 효율적이고 정밀하게 가공하기 위해 MEMS (Micro Electro Mechanical System) 공정, 레이저 패터닝 및 기계적 가공 등 여러 가지 방법들이 시도되고 있다[2-3].
프리즘기반 미세 구조체 어레이 패턴 필름은 선삭에 의 한 롤 가공법과 셰이핑 또는 플레이닝에 의한 평판가공법 으로 마스터 금형을 만들고 이를 필름으로 직접 성형하거 나 마스터 금형에서 복제 금형을 만든 후에 성형하는 방 법으로 만들어 진다[4]. 대면적 제품의 경우에는 이것을 전주공정으로 복제하여 여러 매를 접합한 금형을 만들어 필름을 성형하는 방법이 적용되고 있다[5-6]. 이와 같은 금형 가공에 있어서 평판 가공법은 선삭의 롤 가공법보다 교차가공에 특화되어 사각 피라미드 및 삼각피라미드 패 턴과 같은 입방체 형상의 금형 가공에 적합하다[7-8]. 이 에 따라 평판 금형의 표면에 미세 프리즘 기반의 구조체 어레이 패턴을 가공하는 것은 광학필름의 성능을 좌우하 는 가장 중요한 핵심기술 중의 하나가 되고 있다[9].
광학 부품용 금형은 중심선 표면거칠기(Ra) 15 nm 이하 의 정밀한 가공면이 필요하게 되므로, 우수한 가공성과 칩 배출 능력을 가지는 단결정 다이아몬드(SCD, Single Crystal Daimond) 공구를 주로 사용하고 있다. SCD공구의 형상에 따라 경면, 사각 체널 및 필러 형상과 같은 초정밀 미세 패턴 금형에 다양하게 사용되고 있다[10].
평판 광학 부품 금형소재로, Cu 도금 소재는 스템퍼 복 제 공정이 용이하고 경제적인 이점으로 많이 사용되고 있 다. 그러나 낮은 경도로 미세한 구조체 가공에서 버 및 형 상 오류가 쉽게 발생할 수 있으며, 실제로 프리즘 패턴의 교차가공 (Cross Machining) 을 1회 (1차 그루브가공으로 프리즘형상, 2차 그루브가공으로 사각피라미드 형상 형성) 수행하는 시뮬레이션에서 1 μm이하의 버가 쉽게 발생한 다는 연구결과가 보고되고 있다[11].
따라서 본 연구에서는 V형 SCD공구를 사용하여 Cu 도 금된 소재에 대해서 미세 패턴의 평삭가공실험을 수행하 며 버 및 표면 결함이 최소로 되는 가공조건을 확립하고, 피치 50 μm, 높이 25 μm 수준의 미세프리즘 패턴 및 이 를 기반으로 한 사각 및 삼각 피라미드 구조체의 금형가 공에 적용하고자 하였다. 이에 따라 프리즘 패턴을 절삭깊 이와 절삭속도별로 가공하였고 가공 표면의 상태 및 절삭 력을 분석하였다. 이를 바탕으로 1회 및 2회 교차가공법 을 통하여 실제로 사각 및 삼각 피라미드 구조체 패턴을 가공하였다. 가공 표면상태 및 미세 버의 발생 상태분석 및 패턴 형상에 따른 가공 현상과 그에 따른 생성 칩의 변 화 등에 대한 가공특성을 조사하였다.
2. 미세 프리즘 구조체의 가공 장치 및 방법
2.1. 미세 프리즘 기반 구조체의 형상
그림 1은 V형상의 프리즘 패턴 가공과 이를 기반으로 한 사각 및 삼각 피라미드 구조체의 응용 가공 개념도를 나타낸 것이다. 그림 1(a)와 같이 1차 그루브 가공으로 형 성되는 프리즘 패턴은 90°형상에 피치 50 μm, 높이 25 μm 이다. 2차 그루브 가공은 90° 회전 후 1차그루브 가공으로 생성된 프리즘 패턴과 교차가공으로 밑변 50 μm, 높이 25 μm의 사각 피라미드 패턴을 그림 1(b)와 같이 형성하 게 된다. 3차 그루브 가공은 소재의 45° 회전 후 사각 피 라미드를 양분하며, 단변 50 μm, 장변 70.71 μm, 높이 약 14.84 μm의 삼각 피라미드 패턴을 그림 1(c)와 같이 형성 하게 된다. 1차 그루브 가공은 연속적인 가공으로 하나의 입구 및 출구를 가지며, 2차 그루브 가공 및 3차 그루브 가공은 패턴의 수에 따라 입구 및 출구가 반복되는 단속 적인 가공으로 구성된다.
2.2. 가공장치
실험에 사용된 실험장치는 그림 2(a)와 같이 X, Y, Z, C, A축 등의 5축으로 구성되어 CNC 제어로 정밀 구동 되는 자유형상 미세 복합 가공기 (UVM-450C, Toshiba) 가 사용되었다. 리니어모터로 구동되는 X, Y, Z의 직선 축은 각각 450 × 450 × 250 mm의 이송거리와 0.01 μm 의 분해능을 가지고 있다. 회전축은 공작물을 회전시키 는 C축과 공구를 회전시키는 A축으로 구성되며, 각각의 회전 각도는 1/10000°로 제어 가능하다. 주 절삭 이송은 X축, 패턴의 피치는 Y축, 절삭깊이는 Z축으로 제어된다. C 축은 X-Y면 상에 설치되어 360°로 회전하며, 그 위에 진공 척을 설치하여 공작물을 고정하고 가공 위치를 조 절할 수 있다.
A축은 그림 2(b)와 같이 Z-Y면에 설치되고 가공 공구 및 공구동력계 (Type 9256C2, Kistler) 가 부착된다. 가공 된 미세 구조체 금형의 가공형상과 표면의 평가를 위해 광학현미경 (OM:Optical Microscope, BX51M, Olympus and KH-8700, Hirox) 을 사용하여 가공된 구조체의 치수 확인 및 표면거칠기를 측정하였다. 또한 주사전자현미경 (SEM: Scnning Electron Microscope, CX-200 Coxem) 으 로 패턴의 가공 상태와 발생 칩의 형상을 관측하였다.
2.3. 가공방법
가공실험에 사용된 소재는 그림 3과 같이 50 × 50 × 30 μm 크기의 고경도의 금형강 (Stavax, HRC 56) 소재의 표면 상에 200 μm 두께로 Cu를 전주 도금한 것이다. 패턴가공 을 위해 Cu 도금면에 반경 10 mm의 SCD공구를 사용하 여 절삭깊이 5 μm, 가로 이송량 30 μm의 가공조건으로 중심선 표면거칠기 (Ra) 12 nm 수준의 경면가공을 수행 하였다. 가공된 동도금 표면의 비커스경도는 약 219 Hv 정도이다.
그림 4는 본 실험에 사용된 단결정 다이아몬드공구의 모습으로서, 그림 4(a)와 같이 가공 대상 프리즘 패턴의 형 상에 따라 형상각 90°와 공구와 공작물간의 가공 간섭을 고려하여 전면 여유각 6°로 설계되었다[12]. 그림 4(b)는 제작된 공구이며, 형상각은 Fig, 4(c)와 같이 90.15°, 여유 각은 그림 4(d)와 같이 6.01° 정도였다.
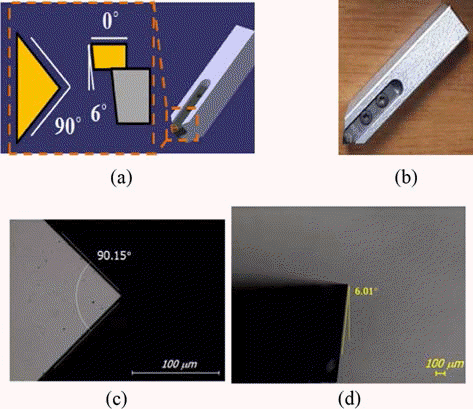
V-shape single crystal diamond tool. (a) fabricated tool, (b) measured shape angle and (c) measured clearance angle
Table 1은 프리즘 패턴 및 구조체의 가공조건을 선정하 기 위하여 우선적으로 설정한 예비실험의 가공조건이다. 예비 가공실험의 패턴의 피치는 10, 20, 30 μm로 설정하였 다. 이에 따른 절삭깊이는 5, 10, 15 μm으로 설정되어지며, 절삭속도는 실험에 사용된 가공기의 최대 속도 250 mm/ sec를 고려하여 100, 150, 200 mm/sec 등의 3단계로 나누 어 실험하였다.
3. 실험결과 및 고찰
3.1. 프리즘 패턴 가공 및 가공조건 선정
그림 5는 각 조건에 따라 프리즘 패턴을 가공한 결과이 다. 절삭깊이가 5 μm로 작고, 절삭속도는 200 mm/sec로 빠를수록 금형 패턴상부인 산 (peak) 의 가공형상이 양호 하게 나타나는 경향을 보였다. 절삭속도가 100, 150 mm/ sec에서는 산 부분에서 미세 버가 공통적으로 발생하였다 . 또한 절삭깊이가 적을수록 표면 상태는 좋아지는 것을 볼 수 있다. 이는 그림 6에서 보는 것과 같이 절삭되는 면 적이 작아지면 절삭저항이 작아지므로 이러한 효과로 인 하여 발생하는 버의 크기도 작아지고 표면의 가공 상태는 좋아지는 것으로 여겨진다[13]. 그림 6은 주 절삭력과 절 삭면적을 비교하여 나타낸 것이다. 절삭력은 절삭깊이가 작을수록 감소하는 경향을 보였다. 이는 절삭 면적이 줄어 들기 때문이다, 또한 절삭속도의 변화에는 절삭력은 그다 지 영향을 받지 않음을 알 수 있다. 이는 절삭면적이 거의 동일하기 때문이다[14].
그림 7에는 그림 5에 나타낸 가공표면의 조도를 측정하 여 비교하였다. 절삭깊이 5 μm, 절삭속도 200 mm의 조건 에서 Ra 약 14.8 nm로서 일반적인 광학 프리즘 부품의 요 구 표면거칠기 Ra 15.0 nm 정도에 근접하는 것을 볼 수 있다. 이상과 같은 예비실험결과 버의 발생이 적고 가공표 면의 상태가 가장 양호하게 나온 절삭조건인 절삭깊이 5 μm, 절삭속도 200 mm/sec를 본 실험의 적정 가공조건으 로 선정하고, 이후의 사각 및 삼각 피라미드 구조체의 가 공에 적용하였다.
3.2. 미세 프리즘 구조체 금형의 가공결과
적정 가공조건으로 미세 프리즘 구조체를 순차적으로 가공하여 그 결과 형상을 그림 8, 절삭면적 및 절삭력의 변화를 그림 9와 같이 나타내었다.
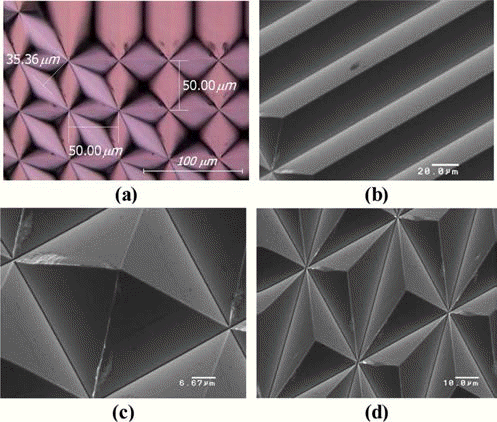
Machining results of (a) machined pattern size and pattern shapes, (b) prism, (c) square pyramid and (d) triangular pyramid pattern.
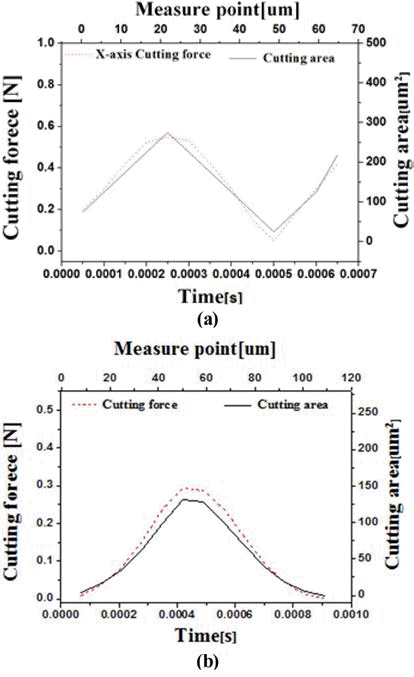
Comparison of cutting force and area with (a) square pyramid pattern and (b) triangular pyramid pattern machining.
각 가공 순서의 가공에서 그림 1의 모델링과 동일한 수 준의 가공형상을 그림 8(a)과 같이 확인하였다. 그러나 가 공표면 상태를 보면 모서리부분에서 버가 미세하게 발생 하는 현상을 관찰하였다. 구조체의 형상별 Cu 도금소재 가공특성 비교를 위해 그림 8(b)~8(d)와 같이 SEM으로 패 턴형상을 관측하였다. 프리즘 패턴의 표면 그림 8(b)에서 는 상면의 이상이 없었으나, 사각 피라미드 그림 8(c)에 서는 모서리에서 약 1 μm 크기의 버를 확인하였다. 또한, 그림 8(d)의 삼각 피라미드 패턴 모서리부에서는 0.5 μm 사이즈의 미세 버를 확인 할 수 있었다. 사각 피라미드 패턴가공은 그림 9(a), 삼각 피라미드 패턴가공은 그림 9(b)같이 절삭력과 절삭면적이 나타났다. 각 형상의 피치 간격만큼 일정한 절삭력과 절삭 면적이 반복되어 발생하 였다. 미세 버가 발생되는 부분은 대부분 절삭면적이 감 소하는 출구부분이며, 절삭면적에 비해 절삭력이 낮게 되 는 지점이 공통적으로 확인되었다. 이는 소재의 연성 특 성과 기계적 가공의 특성이 복합적으로 작용하여 생기는 현상이라 할 수 있다.
3.3. 가공 패턴에 따른 칩 형상 특성
프리즘 및 피라미드 구조체의 정삭가공에서 발생된 칩 의 형상을 그림 10과 같이 비교하였다. 대체적으로 가공 공구와 접촉한 부분은 깨끗한 표면으로 생성되었고, 이의 반대편은 제거된 소재가 소성변형을 일으켜 주름진 형상 의 유동형 칩 특성을 보였다. 또한, 출구부에서는 패턴 모 서리부에서 생성되는 버와 유사한 형상의 칩이 발생하는 것을 확인할 수 다. 그림 10(a)는 프리즘패턴 가공에서 발 생한 칩의 형상으로서 다이아몬드공구에 의한 연속가공의 특성으로 칩이 연속형으로 길고 매끄러운 형상이 얻어졌 다. 사각 및 삼각 피라미드 패턴 구조체 가공에서는 단속 가공의 특성상 짧게 절단된 칩이 생성되어야하지만, 사각 피라미드 패턴 구조체 가공에서는 그림 10(b)와 같이 미세 과절입 현상에 의한 연결된 칩이 발생하였다. 이는 실험과 정에서 미세 한 공구의 높이 편차가 발생한것이 주요한 원인이지만 Cu 와 같은 연질 재료의 특성에 기인한 것도 한 원인으로서 향후 이의 정밀화를 위한 대책이 필요함을 확인하였다. 절삭면적 및 다이아몬드공구 절인의 특성상 절삭력이 0으로 측정된 삼각 피라미드 패턴 구조체는 그림 10(c)와 같은 조각형태의 칩이 발생한 것을 확인할 수 있다. 이 형상의 칩 측면부에서는 Fig. 8(d)의 삼각 프 리즘패턴 교차가공에서 발생된 모서리 부의 버와 유사한 형태의 버가 발생하는 것을 확인 할 수 있으며, 이러한 버 의 형상을 통하여 Cu와 같은 연질금속의 미세 패턴 가공 상태를 예측하는 것이 가능함을 알 수 있게 하였다.
4. 결 론
본 연구에서는 V형 90°형상각의 SCD 공구로 Cu 도금 된 소재에 초정밀 평삭가공을 수행하여 미세 프리즘 패턴 을 기반으로 하는 미세 프리즘 구조체 패턴 금형을 가공 하여, 다음과 같은 결과를 얻었다.
SCD 공구를 이용한 Cu 도금 소재의 미세 프리즘 패턴 가공에서 절삭속도 200 mm/sec, 절삭깊이 5 μm로 가공시 미세 버 및 변형이 발생하지 않았고, 중심선평균 표면거칠 기가 14.8 nm로 광학부품으로서의 허용 거칠기를 만족하 는 가공조건을 확립히였다. 이를 바탕으로 피치 50 μm, 높이 25 μm의 사각 피라미드구조체와 이를 대각선방향으 로 이등분 가공하여 단변 50 μm, 장변 70.7 μm, 높이 14.8 μm의 삼각 피라미드 패턴 금형 가공에 적용하였다.
감사의 글
This work was supported by a 2-Year Research Grant of Pusan National University.