건축 스케일 적층제조 기술동향
Technology Trend of Construction Additive Manufacturing
Article information
Abstract
The transition from “More-of-Less” markets (economies of scale) to “Less-of-More” markets (economies of scope) is supported by advances of disruptive manufacturing and reconfigurable-supply-chain management technologies. With the prevalence of cyber-physical manufacturing systems, additive manufacturing technology is of great impact on industry, the economy, and society. Traditionally, backbone structures are built via bottom-up manufacturing with either pre-fabricated building blocks such as bricks or with layer-by-layer concrete casting such as climbing form-work casting. In both cases, the design selection is limited by form-work design and cost. Accordingly, the tool-less building of architecture with high design freedom is attractive. In the present study, we review the technological trends of additive manufacturing for construction-scale additive manufacturing in particular. The rapid tooling of patterns or molds and rapid manufacturing of construction parts or whole structures is extensively explored through uncertainties from technology. The future regulation still has drawbacks in the adoption of additive manufacturing in construction industries.
1. 서 론
주거와 관련된 건축 산업분야는 협의의 개념에서 건축 물을 시공하는 분야이나 광의의 개념에서는 주거와 관련 하여 소요되는 제품의 최종수요 산업이다. 건축 산업분야 는 제조 산업의 패러다임 전환에 따른 기술/산업적 변화에 영향을 받으며, 실제로 건축 산업의 생산성 혁신은 제조 산업 혁신기술의 도입을 통해서 향상되는 특징을 가진 다[1]. 최근 건축 산업의 혁신은 기술전주기 영역에서 디 지털화, 자동화시공기술의 확산, risk management tool 의 보편화, 공정관리/물류관리와 같은 요소기술이 개별적 혹 은 통합적으로 관리되는 체계(BIM, building information management)를 갖추면서 비약적인 생산성 개선이 이루어 지고 있다. 더 적극적인 형태의 혁신은 건축과 제조 산업 이 결합된 공업주택(pre-fabricated house) 유형을 통해서 확인할 수 있다. 건축제품의 규모측면에서, 현재 자동화 건축기술의 개발방향은 크게 초대형 건축물 제조기술과 소형건축물의 비정형 구현기술의 두 축으로 전개되고 있 다. 국가와 지역 및 시대에 따라서 수요건축의 주류 유형 이 달라질 수 있으나 향후 분산발전 ICT(Information & Communication Technology) connected 주택[2] 무인배송 인프라[3] 지능화된 도로와 자율운전기술[4] 등의 발전은 소형 단독주택의 수요를 높일 것으로 예상된다. 3D 프린 팅 기술로 잘 알려진 적층제조 기술[5] (AM, additive manufacturing)은 최종제품보다 작은 크기의 원료를 반복 적인 적층의 과정을 통해서 제조하는 접근방법(bottom-up manufacturing)을 이용하고 제품설계에서 제품제작 전 주 기에서 컴퓨터를 이용하는 제조기술(CAM, computeraided manufacturing)이다. 이러한 접근방식은 원소재의 제 품화 과정에 소요되는 소재의 낭비를 줄이는 효과(lean manufacturing)와 복잡한 형상의 제품을 제조할 수 있어 고효율 기능중심의 제품개발(function basis design)을 가능 하게 한다. 제품공급 측면에서는 기존의 중앙집중식 생산 (centralized manufacturing)을 대체하는 분산생산(distributed manufacturing)을 통해서 소비가 발생하는 장소와 시간에 적기에 공급이 가능하기 때문에(on-demand manufacturing) 제품판매를 위한 과잉생산과 예비부품의 인벤토리 관리를 절감하는 효과를 구현할 수 있다. 또한, 자동화된 생산과 적층제조 기술개념에 의해서 생산 공정, 생산 인력 및 공 급채널을 줄일 수 있어(eliminated manufacturing) 제조경 쟁력을 높일 수 있다. 적층제조기술의 이러한 기술구성 개 개 념은 실물제품 생산과 관련한 혁신적인 생산기술을 제공 하며, ICT 기반 network 융합을 통해서 대량 맞춤형 시장 에 대응 가능한 협업제조시스템(reconfigurable manufacturing system)을 제공하게 된다. 이러한 적층제조기술의 근원적 기술개념과 효과는 건축 산업이 추구하는 발전방향과 동 일하고 개인 맞춤형 제품의 적기 공급으로 요약할 수 있 는 시장가치 창출의 목표 측면에서 일치성이 높다. 이러한 맥락에서, 건축 산업 자체가 적층제조기술의 원형을 표현 하고 있다고 볼 수 있다. 다만, 현재 건축물 시공 과정에 서 사람 중심으로 체화된 기술적 노하우와 반자동 장비를 향후 코드화된 DATA와 자동화된 장비로 대체하고 궁극 적으로, 자율운영이 가능한 시공 장비와 학습이 가능한 인 공지능 기술로 대체되는 사이버-물리 시공 시스템(CPS, Cyber Physical System)[6]으로 변화할 것으로 예상된다. 본고에서는 적층제조기술과 건축 산업에서의 적층제조기 술의 도입현황을 소개하고 향후 적층제조기술이 건축 산 업, 특히 소형 건축물 시공을 어떤 모습으로 변화시킬 것 인가를 추론해 보고자 한다.
1.1 Additive manufacturing (3D printing)
적층제조기술은 표준용어 규정[5]에 따르면 CNC공정과 같이 원료소재에서 불필요한 부분을 제거하면서 제품화하 는 가공기반 기술(subtractive manufacturing)이나 사출성 형, 다이캐스팅, 소성가공과 같이 원료소재에 유동성을 부 여한 후 툴을 이용하여 원하는 형상의 제품으로 만들어가 는 기술(formative manufacturing)과 다르게 3D 모델 정보 를 이용하여 층별로 소재를 접합하여 물건을 만드는 과정 이다. 상세한 제품화 과정(그림 1)은 Pre-AM 단계에서 제 품사양과 기능을 기반으로 3D modelling을 시행하고, CAE실행 및 CAD수정과정을 반복적으로 수행하여 최종 적인 3D model을 완성한 후, 출력이 가능한(printable 3D model) 파일 포맷 형태로 변환 하고, 공정이나 목적에 따 라서 원본 모델 이외의 부가적인 형상을 형성하여 빌드 플랫폼에 변환 모델을 배치한다. 최종적으로, 3D model을 슬라이싱(slicing)과정을 통해서 2차원 패턴과 각 패턴을 생성하는 툴 패스(G-code)를 획득한다. AM 단계는 획득 한 툴 패스를 기반으로 적층제조 장비를 운전하여 층층이 제품화 하고, Post-AM 단계는 적층 제조된 파트를 빌드 플랫폼으로부터 분리하는 과정과 적층제조 공정에 따라서 요구되는 후처리(heat-treatment, densification, curing, support removal)공정 및 가공을 선택적으로 수행하는 단계, 그리 고 Qualification 단계는 제조된 파트의 특성을 평가하는 단계로 비파괴 검사를 통한 결함검사, CAD-to-Part 형상 일치성 검토, 그리고, 필요에 따라서 동일한 적층과정으로 제조된 표준화된 witness sample을 이용한 파괴분석 과정 을 통해 전주기를 표현할 수 있다. 적층제조기술은 많은 상용기술이 존재하며 다양한 기준에 따라서 기술 분류가 가능하다. 적층제조기술의 표준화된 기술 분류는 공정기 구와 적층기구를 기준으로 표 1에 요약한 바와 같이 7대 기술 군으로 구분한다. 그러나 최근에는 기존의 기술 분류 체계상의 기술이 가지는 제약성을 극복하기 위해서 2가지 이상의 기술개념이 결합된 하이브리드 형의 기술[8]이 상 용화되고 있다. 하이브리드화의 대표적인 유형은 적층제 조기술과 절삭가공기술이 결합되는 방식으로 분말금속을 이용한 3차원 프린팅기술과 결합된 PBF+CNC, DED+ CNC 유형이 존재하며, 폴리머 압출식 적층제조 장비와 CNC 장비를 동일한 빌드 플랫폼에 장착하여 대형 폴리머 파트를 제작하는 기술(Thermwood LSAM)등이 존재한다. 적층제조기술은 다양한 산업에 적용되고 있다[8]. 산업분 야와 관계없이 제품개발 주기 상 적층제조기술의 활용 유 형은 상품 디자인 단계에서의 기능성 RP제작(Rapid prototyping), 제품화 과정에서 툴 제조(Rapid tooling), 그 리고, 직접 제품제조(Rapid manufacturing)의 방식이 있다. 이러한 활용유형은 제품화 전주기 적층제조기술의 적용 유형의 모식도(그림 2)로 전주기를 도식적으로 확인 할 수 있다. AM for RP는 제품설계 과정에서 제품의 디자인 적 합성(design review)을 실물제조를 통해서 검토하고, AM for RT에서는 AM기술을 제품 제조에 소요되는 몰드 혹은 패턴을 제조하는 과정에 국한하여 적용하고 후처리 또는 제품화 과정에서는 기존의 제조기술을 적용하는 유형이다. AM for RM은 제조하고자 하는 제품을 AM을 이용하여 제조하는 기술이며 AM 결과물이 제품이 되는 Direct RM 기술과 AM을 통해서 중간재를 생성하는 Indirect RM 기 술이 있다. Indirect RM 기술은 최종 형성된 제품의 강도 부족 등의 이유로 기존의 제조기술을 이용하여 내부 구조 를 재구성하는 과정 등이 필요하다.
2. 건축 적층제조기술
분류의 정량적 기준은 없으나 제품의 크기에 따라서 마 이크로 적층제조기술, 적층제조기술, 그리고 건축 스케일 적층제조기술로 분류할 수 있다. 건축 스케일 적층제조기 술은 대형의 파트를 제조하는 데 적용되는 적층제조기술 을 상징적으로 표현하는 용어이다. 적층제조기술을 통해 서 생산되는 제품에 따라서 최종적으로 수요 되는 건축 상품을 직접적으로 제조(RM)하는 기술과 건축 상품제조 에 소요되는 각종 툴을 제조하는 과정(RT) 에 적용되는 기술로 구분 가능하다. 이와 별도로, 제품화 과정이 일체 화된 제품을 생산하는 기술과 최종 제품을 분할한 파트를 제조하고 조립하는 방식이 있다. 건축시공의 특성상 전자 는 시공현장에서 직접 전개되는 반면 후자는 공장 환경에 서 생산되고 현장에서 조립되는 과정으로 진행된다.
2.1 건축파트 직접 제조 적층제조기술(RM)
건축파트 직접 제조 적층제조기술은 원료소재와 3D 모 델을 투입하여 적층제조 공정을 통해서 건축파트를 생산 하는 경로기술이다. 바인더 젯팅 적층제조기술(binder jetting AM), 직접 에너지 적층제조기술(directed energy deposition AM) 및 압출식 적층제조기술(material extrusion AM)이 대표적인 적층제조기술이다. 그림 3에는 바인더 젯팅 기술의 기본적 공정도와 건축 상품 응용사례를 나타 냈다. 바인더 젯팅 기술을 통한 3D 실물제조는 공통적으 로 슬라이싱 과정을 거치고, 슬라이싱된 2차원 패턴을 생 성하기 위해서 일정한 두께의 분말 층을 소위 리코터 (recoater)로 알려진 장치를 이용하여 형성하는 과정(a-1)과 다수의 노즐을 포함하는 프린팅 헤드를 이송하면서 선택 된 영역에 바인더를 토출(a-2)하는 방식으로 2차원 패턴을 형성한다. 이 과정을 반복적으로 적용하여 3차원 제품을 제조하며, 필요에 따라서 2차원 패턴 형성 후 IR 히터를 이용하여 바인더를 경화하는 과정을 적용하기도 한다. 일 정한 용기 내에서 작업이 이루어지므로 분말 용기 자체가 내부에 제조되는 파트를 지지하는 서포트 기능을 수행하 나 적층제조 후 분말베드로부터 파트를 꺼내는 작업 (depowdering) 과정이 필요하다. 일반적으로, 사용되는 바 인더는 열경화성 수지를 이용하므로 분말-바인더 강도를 높이기 위해서 후열처리를 통해 바인더를 경화하는 과정 이 depowdering 공정 전에 적용되기도 한다. 건축 파트를 바인더 젯팅 적층제조하는 기술은 크게 분할파트 제조-조 립 경로와 일체형 상품 적층제조로 구분된다. 두 가지 상 품제조 경로의 선택은 근원적으로 장비가 허용하는 적층 제조 공간크기와 상품크기에 의존하며 부가적으로 건축 상품의 강도를 높이기 위한 후속 치밀화 공정과도 관계된 다. 실제로, 그림 3의 (b)의 사례는 최종 건축 상품을 결합 을 고려한 파트로 분할하고 각 파트를 바인더 젯팅 공정 을 통해서 적층제조한 후 소결의 과정을 통해서 강도를 높인 건축 상품화 경로기술의 사례인 반면 그림 3 (c)는 일체화된 건축 상품을 대형의 바인더 젯팅 장비를 통해서 제조한 사례를 나타낸다. 이러한 기술은 일체화된 파트의 적층제조는 별도의 서포트 없이 제품 디자인의 자유도를 높일 수 있는 장점이 있고, 대형화된 장비를 통해서 시공 현장에서 적층 제조하는 방향으로 기술이 전개되고 있다. 그러나 적층과정에서 분말베드를 일정하게 유지해야하는 점, 미 사용된 분말을 depowdering 하는 공정과 장치가 필 요하다는 점, 적층 제조된 파트의 강도의 한계와 이방성이 존재한다는 점 등에서 문제를 가지고 있다. 직접 에너지 적층제조기술(DED)는 주로 금속을 이용한 적층제조기술 에 적용된다. 고밀도 에너지원인 레이저, 전자빔 및 아크 를 이용하여 분말이나 선재의 금속을 용융-응고하는 방식 으로 파트를 적층 제조하는 기술이다. 대표적으로 그림 4 (a)에는 레이저를 이용한 DED공정기술을 나타냈다. 국부 적으로 조사된 레이저에 의해서 금속의 용융 풀이 형성되 고 분말을 레이저 축에 평행한 방향으로 공급하는 방식으 로 비드가 형성된다. 선재를 이용하는 경우에는 선재를 직 접 용융 풀에 주입하는 방식으로 비드를 형성한다. 대형의 구조물의 경우 건축과 항공분야에서 주로 격자 구조제품 의 형성에 활용된다. 그림 4 (b)는 다관절 로봇과 아크 용 접기술을 접목하여 격자구조의 금속 구조물을 형성하는 기술의 예시이다. 국부 영역에서 금속의 용융과 응고가 발 생하므로 적층제조물에 매우 높은 잔류응력이 형성되는 문제점과 높은 생산성을 높이는 경우 정밀도가 낮아지는 문제점이 있어 응력을 제어할 수 있는 공정기술, 후열처리 기술, 후 가공기술이 현장에서 이루어질 수 있는 연구개발 이 요구된다. 그림 4 (c)에는 일반적으로 DED를 이용한 적층제조의 예시를 보여준다. 적층제조를 최소화하기 위 해서 금속기판을 이용하고 최종적으로 제품의 일부가 되 도록 디자인하는 방식이다. 건축 구조물의 경우에도 적절 하게 디자인된 금속 기판을 성형하고 추가적인 파트를 DED를 이용하여 적층 제조하는 방식으로 접근하는 것이 생산성과 품질 측면에서 장점이 있을 것으로 판단된다. 압 출식 적층제조기술은 그림 5에 제시한 바와 같이 유동성 을 가지는 피드스탁을 가압하여 노즐을 통해서 선형의 적 층물을 생성하는 방식이다. 열가소성 수지를 핫 노즐을 통 해서 용융하고 압출하여 선형의 형성물을 원하는 위치에 쌓아가는 방식이 대표적인 기술이다. 최근에는, 열가소성 수지에 분말이나 선재형태의 폴리머, 금속, 세라믹 첨가물 을 혼합하여 기능을 강화한 압출식 적층제조물을 형성하 는 기술이 제시되고 있고 상온경화 세라믹을 압출 적층 제조하는 기술이 건축분야에서 활용되고 있다. 그림 5에 는 폴리머 및 폴리머 복합소재를 이용한 건축파트의 응용 사례를 나타냈으며, (a)는 압출식 적층제조 공정기구를 나 타내고 열가소성 폴리머를 이용한 압출은(a-1)과 같은 핫 노즐을 이용하고 상온경화 모르타르 피드스탁의 압출(a-2) 의 경우 가압형 압출기를 이용한다. (b)는 대형 건축물을 작은 크기의 파트로 분할하고 각 파트를 압출 적층제조 후 현장에서 조립하는 유형의 기술이며 (b-1)은 폴리머 압 출적층 사례(Oak-Ridge NRL) (b-2)는 모르타르 압출적층 사례를 나타낸다. (c)는 전체 구조물을 일체화된 방식으로 적층 제조한 유형, (c-1)은 폴리머 건축물을(c-2)는 모르타 르 건축물을 나타내며 건축과 관련된 상온 경화형 세라믹 소재를 이용한 건축파트 압출 적층제조 기술은 3장에 상 세히 소개한다.
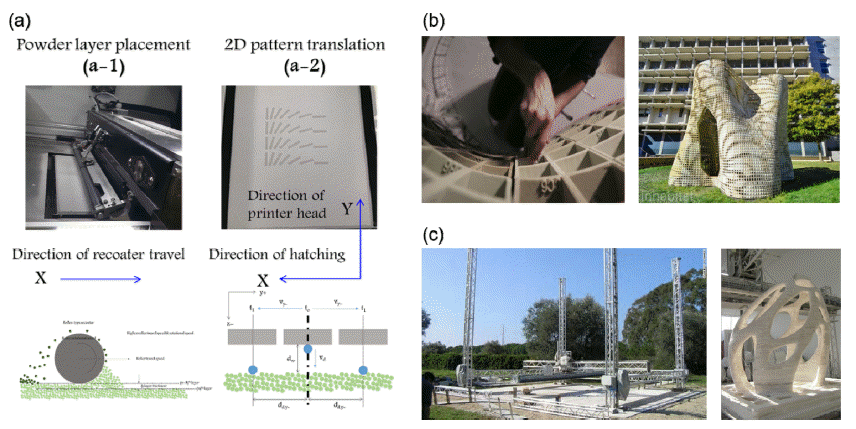
Binder jetting for construction scale AM : (a) KITECH, basic binder jetting process, powder placement and 2D pattern translation, (b) UC Berkeley, printed block assemble for complex shape construction via binder jetting, (c) D-shape, large scale binder jetting).
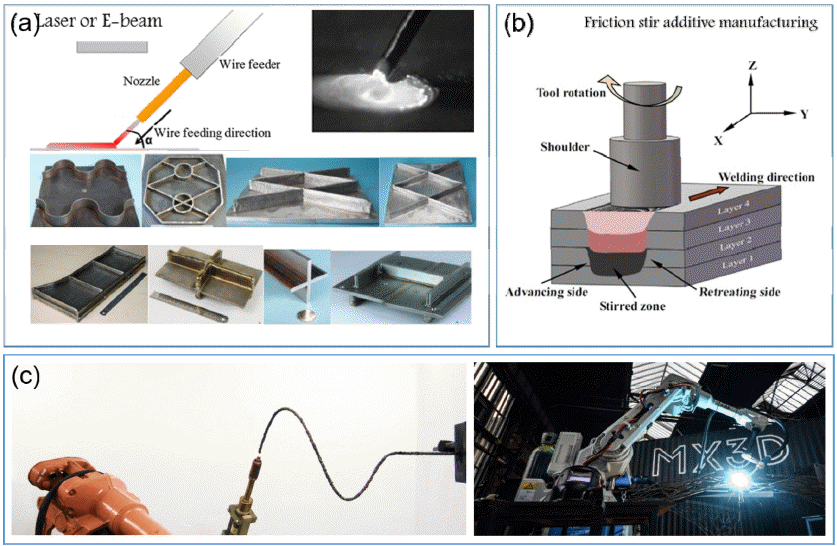
Direct Energy Deposition for structure manufacturing : (a) DED Process via linear of powder material, (b) friction welding DED process, (c) toolpath drawing process via robot arm, MX3D.
2.2 건축파트 제조용 툴 제조 적층제조기술(RT)
적층제조기술을 이용하여 몰드나 패턴을 제조하고 이를 기존의 콘크리트 캐스팅 공정을 연계하는 방식은 일종의 연속적 혁신의 유형이라 할 수 있다. 그림 6 (a)에는 우레 탄 폼 소재를 이용한 거푸집 제조, EPS(Expanded polystyrene) 를 이용한 거푸집 내부 구조물 제조, 그리고 폴리머 를 이용한 건축 상품 패턴의 제조 사례를 나타낸다. 우레 탄 폼 거푸집 제조의 경우 우레탄 폼을 압출식 적층제조 를 통해서 직접 거푸집을 제조하는 방식이다. EPS를 이용 한 기술은 비정형의 콘크리트 파트를 제조하기 위해서 기 존의 거푸집 내부에 EPS를 이용하여 라이너를 제조하는 기법이다. 기존의 CNC를 이용하여 가공을 통해 EPS 라이 너 파트를 제조하던 기술을 그림 6 (b)EPS sheet를 이용한 sheet lamination AM 기술로 대체한다. Sheet lamination 적층제조는 일정한 크기의 sheet 형 피드스탁을 공급하고 이를 이전 층과 접합(lamination)한 후 커터나 레이저 등을 이용하여 2차원 패턴을 외곽선 따기 형태로 전사하는 과 정을 반복적으로 수행한다. EPS sheet를 절단하는 전형적 인 방법은 열선이나 열 로드를 이용하는 방법이 있으나 고려대학교의 경우 레이저를 이용하는 기술을 제시하고 있다. 생산성 측면에서 sheet lamination 기법은 sheet의 두 께를 높이고자 하나 두께가 두꺼운 경우 계단 효과(staircase effect)에 의해서 품질이 저하되는 문제가 있다. 이러 한 문제를 해결하기 위해서 수직한 면의 절단방식이 아니 라 경사방식의 절단이 이루어지도록 하는 툴 운동 최적화 가 제시되고 있다. 이상의 툴 제조하는 기술은 콘크리트 캐스팅을 위한 몰드 제조에 초점을 맞춘 경우이다. 제조된 몰드나 몰드 툴이 반복 사용이 어려우므로 소량의 제품을 생산하는 경우에 적합성이 높다. 반면에 몰드를 이용하여 제조하기 어려운 복잡한 형상의 콘크리트 파트를 제조하 거나 동일한 형태의 파트 수가 많이 있는 경우, 그리고 지 속적으로 수요가 발생하는 경우에는 적층제조기술을 패턴 을 제조하는 과정에 적용하는 것을 검토할 필요가 있다. 패턴은 반복사용 가능성에 따라서 영구 패턴(permanent patterns)과 소실모형 패턴(consumable patterns)로 구분할 수 있다. 영구 패턴은 제품의 형상을 기반으로 설계된 3D 모델을 설계하고 이를 적층제조를 통해 패턴을 제조한 후 다시 패턴을 이용하여 몰드를 제조하는 과정을 거친다. 콘 크리트 캐스팅의 경우 경화에 소요되는 시간이 전체 파트 제조에서 율속이 되므로 몰드의 수가 생산성을 결정하게 된다. 따라서 몰드 제조비용이 싼 경우 하나의 패턴을 이 용하여 다수의 몰드를 제조할 수 있으므로 콘크리트 캐스 팅 연계 건축 파트 제조에서 생산성이 개선될 수 있다. 격 자구조를 가지는 일체화된 건축 파트를 제조하는 기술을 몰드를 이용하여 제조하는 경우 소모성 패턴을 이용하는 것이 가능하다. 대표적으로, 왁스와 같은 저융점 소재를 적층제조한 후 세라믹 슬러리를 통해 몰드화 하고 온도를 높여 저융점 소재를 녹여내 내부구조(cavity)를 형성한다 [8]. 내부구조에 다시 콘크리트를 캐스팅한 후 외부 몰드 를 파괴하면 복잡한 형상의 건축파트를 제조할 수 있다. 이상의 기술동향을 통해서 적층제조기술이 다양한 유형의 경로를 통해서 건축 상품 제조에 활용될 수 있다는 것을 알 수 있다. 그러나 적용기술과 제조경로에 따라서 건축 상품의 품질, 물성, 생산성 및 경제성이 달라지므로 시장 의 니즈에 부합하는 기술의 선택이 어려운 문제점을 가지 고 있다는 점을 지적한다.
3. 상온 경화형 건축소재 압출식 적층제조기술
건축 구조물은 상온에서 경화되는 기구를 가지는 세라 믹 소재를 이용한다. 수화반응(hydration)을 통해서 경화되 는 시멘트[12]가 대표적이다. 또 다른 경화기구로 탄산화 반응(carbonation)을 통해서 경화가 발생하는 석회석 기반 소재[14]가 있다. 현재 건축 파트를 제조하는 기술은 수화 반응을 기반으로 상온경화를 유발하는 피드스탁을 압출식 적층제조기술을 적용하여 제품화하는 기술이다. 수화반응 을 위한 활성 시멘트 크링커와 잔골재를 이용한 모르타르 가 대체적으로 기초가 되는 소재이며 강도 강화를 위한 선형 첨가물의 첨가[19], 굵은 골재를 첨가한 콘크리트가 적층제조에 된다. 궁극적으로 소재는 테라포밍(terraforming) 기술에서 요구되는 것과 같이 적층제조가 이루어지 는 환경에서 직접 구해지는 소재를 이용하는 방식[20]으 로 진화할 것으로 보인다. 모르타르를 이용한 압출식 적층 제조는 공장 환경에서 분할된 파트를 생산하고 현장 이송 하여 조립하는 기술이 주류기술이나, 서비스공급과 직관 적인 공정적용이 가능한 이점을 통해 자연환경이나 시공 환경에 따라, 건설 시공현장에 장비를 직접 이송하여 일체 화된 수직골조를 적층 제조하는 기술이 개발되고 있다. 이 러한 모르타르를 이용한 압출식 적층제조는 모르타르 소 재가 가지는 경화특성 및 유변학적 거동[24, 25]을 제어하 는 기술이다. 모르타르를 이용한 압출식 적층시공 과정의 주요 공정인자와 개요를 표 2에 요약했다.
압출식 적층제조 시스템 구성[23]은 크게 모르타르 유체 를 공급하는 물질이동 경로, 압출물을 일정한 툴 패스로 이송하는 운동계통, 물질 이송경로를 주기적으로 세척하 는 계통, 장비의 운전 건전성과 제조 파트의 형상 건전성 을 모니터링 하는 계통, 대형 파트 제조와 관련한 안전장 치, 그리고, 공정을 전주기적으로 관리하는 제어계통으로 구성된다. 이 중 핵심이 되는 물질이동 경로는 펌프를 통 한 압출공급 방식과 압출기를 통한 공급방식으로 구분된 다. 툴 패스를 구현하는 운동계통은 표 3에 요약한 바와 같이 다양한 좌표계를 이용하는 로봇 시스템이 적용된다. 일반적인 유형은 gantry 로봇, 타워 크레인 로봇, 델타로봇, 다관절 로봇[26]이 있고, 장비의 이동과 설치 편의성 및 작업공간의 제약성을 낮추기 위해서 이동식 차량에 장착 된 다관절 붐을 이용하는 방식과 소형 로봇이 직접 적층 제조되는 파트의 적층위치를 이동하는 방식이 연구되고 있다. 각각의 운동계와 로봇시스템은 장단점을 가지고 있 다. 그러나 향후 현장 적층제조기술이 다양한 소재와 다양 한 공정이 적용되어 건축 상품의 완성도를 높이는 방식으 로 진화한다는 측면에서 각각의 기술이 경쟁적인 방식보 다는 복합적으로 사용되는 방식으로 변화할 것으로 보인 다. 현장에서 건축파트를 직접적으로 적층 제조하는 경우 에는 요구되는 특성은 표 4에 요약하였다. RM의 구현을 위해 적층제조 장비가 이동-설치-해체 과정이 요구되므로 장비의 구조적 강건성, 설치/해체 편의성이 요구된다. 그 밖에도, 대형의 건축물을 제조하므로 수직골조 적층물의 제조 과정에서의 결함발생과 부적절한 시공이 발생하는 경우 제조된 파트의 철거와 재시공이 상당한 비용과 공기 의 연기를 유발한다. 따라서 시공 전 주기에서 장비의 건 전성, 공정의 건전성 및 제조되는 파트의 형상 건전성을 실시간 모니터링[27, 28]하고 이를 바탕으로 공정을 관리 [29]하는 기술이 요구된다. 또한, 수직골조의 구조적 안전 성과 건축 상품제조 완결성을 높이기 위해서는 다양한 소 재와 건축부재를 이용한 다양한 공정기술이 적층제조 장 비와 연계될 수 있는 기능 확장형 장비기술이 요구된다. 이에 다양한 공정을 수행하기 위해서는 고 하중 프레임에 기반한 협업형 제조 하드웨어와 다양한 기능을 설계, 수행, 통제할 수 있는 소프트웨어의 개발이 요구된다.
3.1 CPS AM
향후 건축 적층제조 시스템은 타 적층제조기술 분야에 서 이미 전개되고 있는 기술개발 방향인 디지털 기술과 물리파트 제조기술이 융합된 방식(cyber-physical system) 으로 발전해 나갈 것이다. 그림 8에는 AM 기반 CPS 시 스템과 플랫폼 수준의 AM 기반 CPS 시스템의 예상도를 나타냈다. 협의의 개념은 적층제조 장비 시스템으로 규정 할 수 있다. 적층제조와 관련한 물리 제조 시스템과 적층 과정에서의 건전성을 모니터링[29]하는 시스템 및 진단과 최적화된 적층변수를 생성하는 디지털 시스템이 실시간 연동되어 제어하는 구조가 (a)에서 제시된 유형으로 전개 될 수 있다. 반면에, 광의의 개념에서는 상품개발에서 상 품제조, 사용과정 및 폐기의 전주기 범위에서 플랫폼화된 운영체계에 의해서 관리되는 시스템, 건축의 경우 확장된 BIM(building information management)의 성격을 가지는 운영체계가 소위 디지털 트윈[7]을 통해서 물리적 제품 과 정과 사이버 가상 생산과정이 동기화된 체계라 할 수 있 다. 실제로, 건축 상품을 제작하는 공정에서 발견 가능한 문제는 그림 7과 같이 나타낼 수 있으며, 비드계면상의 결 합력 문제와 형상물의 탄성회복 및 좌굴 현상등의 원인으 로 발생한다. CPS는 이러한 문제점을 정량화하고 향후 DATA의 분석 등을 통해 자율운영이 가능한 기술을 통해 건축 상품의 품질, 물성, 생산성 및 경제성을 체계적으로 관리 가능할 것으로 보인다.
4. 결 론
건축 산업, 특히 소형 건축물 시장은 소량 다품종 제품 에 대한 수요가 높은 분야이며 디자인파트가 실물의 제품 으로 제작되는 측면에서 적층제조기술과 동질성이 높은 산업분야이다. 따라서 디자인의 자유도를 높이는 맞춤형 건축물 공급의 잠재성이 높은 적층제조기술이 소형 건축 물 시장에 새로운 혁신을 창출할 수 있을 것으로 기대한 다. 그러나 건축 산업분야는 항공/우주산업, 바이오디바 이스산업, 국방산업과 함께 높은 수준의 규제가 동반되는 산업적 특성을 가지고 있다. 이에, 적층제조기술의 건축 산업 도입을 위해서는 CPS 시스템 구 기술의 혁신성을 통 한 시장창출과 더불어 불확실한 미래 규제에 대한 대응기 술이 동반된 기술의 개발이 요구된다는 점을 마지막으로 언급하고자 한다. 미래 규제에 대한 선제적 대응측면에서 소재, 제품에 대한 표준화된 평가방법의 개발과 공정, 장 비, 프로그램 및 시공자에 대한 인증방안이 필요하다. 최 종 수요산업의 특징을 가지는 건축 산업에 수요 되는 적 층제조 제품은 타 산업과 수요가 중복되는 제품군과 건축 구조물과 같이 건축 산업에만 소요되는 제품군으로 구분 가능하다. 이러한 구분의 목적은 전자인 중복 수요 제품군 의 경우 타 산업분야와 공동의 품질평가 및 인증체계를 구축하는 접근방법을 선택할 수 있는 반면에 후자의 경우 건축 산업계가 독자적으로 적층제조기술과 관련한 전주기 평가/인증하는 체계를 구축하고 이를 규제화 하는 접근방 법이 필요하다. 기술의 개발초기에서부터 규제를 고려한 기술개발의 체계가 기술개발 투자의 불확실성을 낮추고 다양한 참여자의 시장진입을 촉진하는 바탕이 될 것이다.
Acknowledgement
본 리뷰논문은 도시건축사업 ‘소형 건축물 및 비정형 부 재 대상 3D 프린팅 설계, 재료 및 장비 개발 과제’ 국토 교통부/국토교통과학기술진흥원의 지원으로 수행되었음 (19AUDP-B121595-04).