Manufacturing and Macroscopic Properties of Kinetic Spray Ni-Cr-Al-Y Coating Layer
Article information
Abstract
This study attempts to manufacture a Ni-Cr-Al-Y coating layer using a kinetic spray process and investigates the microstructure and physical properties of the manufactured layer. The Ni-22Cr-10Al-1Y (wt.%) composition powder is used, and it has a spherical shape with an average diameter of 23.7 μm. Cu plate is used as the substrate. Optical microscope, X-ray diffraction, scanning electron microscope and Vickers hardness test are carried out to characterize the macroscopic properties of the coating layer. Furthermore, the coating layer underwent vacuum heat treatment at temperatures of 400°C and 600°C for 1 hour to check the effect of heat treatment temperature on the properties. The manufactured coating layer is 1.5 mm thick, and featured identical phases to those found in the powder. The porosity of the coating layer is measured at 2.99%, and the hardness is obtained at 490.57 Hv. The layer shows reduced porosity as heat treatment temperature increased, and hardness is reduced at 400°C but shows a slight increase at 600°C. Based on the findings described above, this study also discusses possible manufacturing methods for a Ni-Cr-Al-Y coating layer using the kinetic spray process.
1. Introduction
The Ni-Cr-Al-Y-based alloy features excellent corrosion resistance and high-temperature oxidation resistance. Due to these characteristics, the alloy is used as a surface treatment material for products exposed to hightemperature corrosive environments. Ni-Cr-Al-Y coatings can be used to protect metal components in high temperature applications such as aircrafts, power generation, and diesel engines.
The commonly employed coating method of Ni-Cr-Al- Y is plasma spray coating [1]. The plasma spray coating process has advantages of low cost, higher coating capability on various high-functional materials such as metal and ceramics, and fast coating speed [2]. However, plasma spray coating also has a disadvantage of requiring a heat source with extremely high temperatures, which leads to oxidation of the coating layer.
The kinetic spray (in other words, cold spray) process is a coating method which forms dense layers by spraying metal particles or composite powder with a particle size of 1-50 μm at supersonic speed (500-1200 m/s) using high pressure compressed gas (He, N2, or mixture) [3]. Rather than utilizing high temperature heat sources, the kinetic spray process fixates particles on a base material through plastic deformation caused by kinetic energy at a low temperature. Therefore, unlike other spray coating methods, it can be used for materials with high oxidation affinity such as copper, titanium, amorphous materials and nanocrystalline materials, and it is also known to be a coating method capable of producing a coating layer with high density.
Many studies are currently underway to manufacture coating layers with excellent properties utilizing the advantages of the kinetic spray process. McCune et al. [4] have reported the differences in microstructure and physical properties of kinetic spray coating layers after heat treatment. However, there have been few studies reporting the property change of Ni-Cr-Al-Y coating layers manufactured using the kinetic spray process [5] and heat treatment.
In accordance with that, this study attempted to manufacture a high density Ni-Cr-Al-Y coating layer using the kinetic spray process as a new manufacturing process for this material. This study also investigated the changes in microstructure and physical properties of the manufactured Ni-Cr-Al-Y coating layer depending on a heat treatment temperature.
2. Experimental
The powder used in this study consisted of Ni-22Cr- 10Al-1Y (wt.%) composition. SEM (Tescan, VEGA II RLMU) was used for the observation of powders used in this study. Fig. 1 showed (a) the powder particle shape, (b) cross-sectional microstructure and (c) particle size distribution. The initial powder particle shape was mostly spherical. During the observation of the cross-sectional microstructure of the powder after etching, as shown in Fig. 1(b), uneven shapes and sizes of inner grains were confirmed. Furthermore, the powder particle size distribution ranged from 14.2 μm to 39.1 μm, and the average particle size was measured at 23.7 μm.
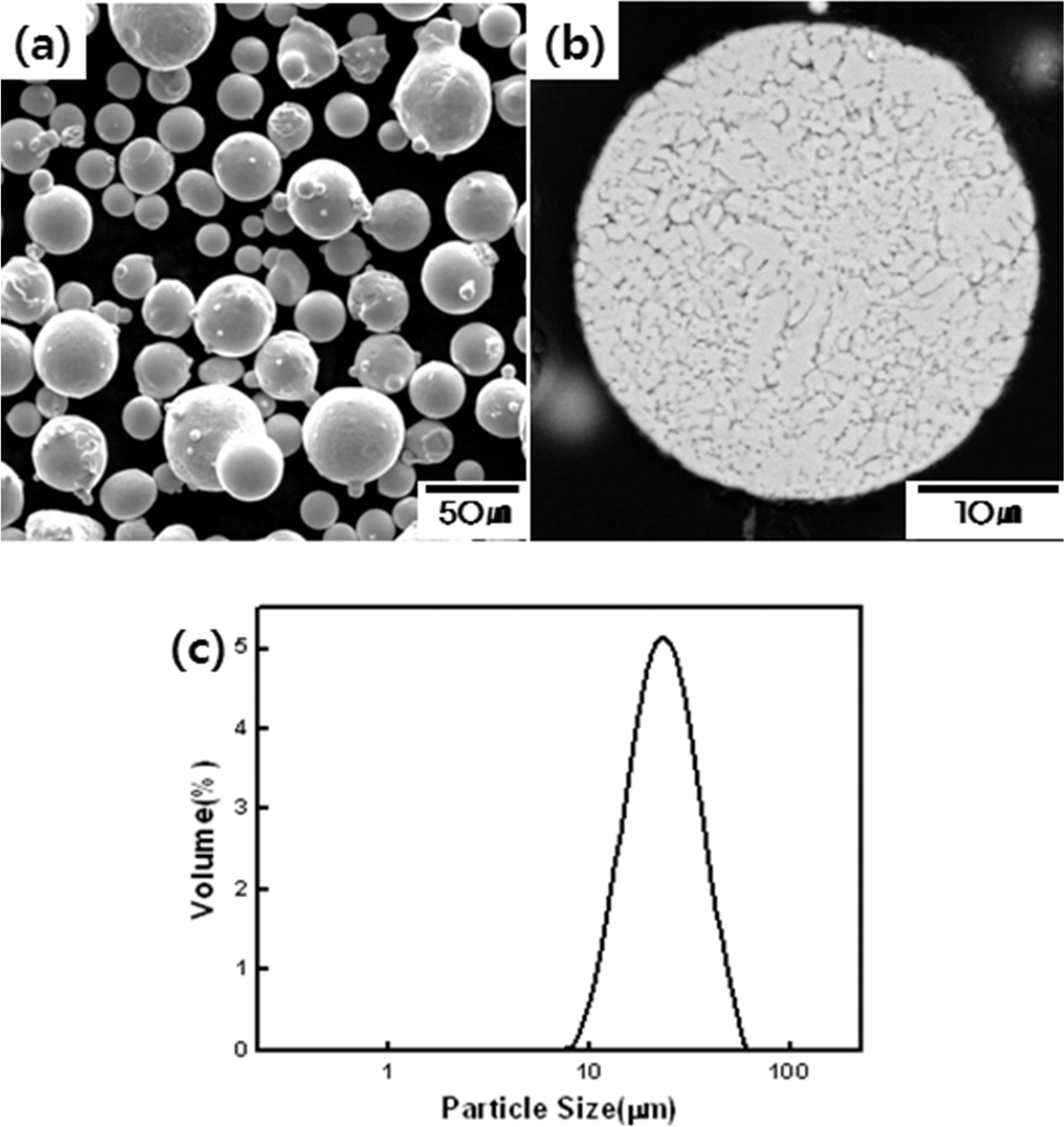
Characteristics of powders used in this study: (a) the shape of Ni-Cr-Al-Y powders, (b) cross-sectional SEM observation result of Ni-Cr-Al-Y powder and (c) the size distribution of powders of Ni-Cr-Al-Y powder.
As shown in Table 1, the optimal process conditions for the coating layers in this study were decided from the various preliminary experimental tests. Based on the information provided in the table, the coating layer was manufactured using the kinetic spray coating process. For the carrier gas, 800°C N2 was used, and pure Cu was used as the substrate material. In addition, the substrate material underwent blasting treatment and the powder was preheated up to 900°C to improve deposition efficiency.

Optimal coating manufacture process conditions of kinetic spraying selected from various preliminary experimental tests
The manufactured Ni-Cr-Al-Y coating layer using the above conditions then underwent post heat treatment. The heat treatment was performed in a vacuum environment, and the heat treatment temperatures were 400°C and 600°C. The temperature was controlled by 5°C/min up to the target temperature, and heat treatment was performed at target temperature for 1 hour. Finally, furnace cooling was implemented. To observe the microstructure of the manufactured coating layer, HNO3 80 ml + HF 3 ml solution was used for etching, then a SEM (Tescan, VEGA II RLMU) was used to observe the microstructure. XRD (Rigaku, D/MAX RAPID-S) was used to perform phase analysis of the manufactured coating layer. Also, the porosity and hardness of the coating layer and heat treated material were measured. Porosity analysis was performed 20 times using image analyzer software based on images of all areas on the coating layer after fine grinding obtained using an optical microscope at x200. In addition to the porosity analysis, the hardness was measured using a Vickers hardness tester. The weight used for this study was 100 g, and 15 measurements of hardness were repeatedly conducted. The average hardness value, excluding maximum and minimum values, was used.
3. Results & Discussions
Fig. 2(a) is a macro image of the Ni-Cr-Al-Y coating layer manufactured using the kinetic spray process. The manufactured coating layer is firmly adhered to the substrate material without any signs of delamination between the coating layer and the substrate material. The thickness of the manufactured coating layer is 1.5 mm. Fig. 2(b) is an image of the cross-sectional microstructure of the manufactured coating layer. The kinetic spray Ni-Cr- Al-Y coating layer in this study represented a relatively dense microstructure compared to the plasma spray Ni- Cr-Al-Y coating layer [1]. However, occasional pores were observed between particle interfaces. The measured porosity of the coating layer is 2.99%. The observation of the inner microstructure of the coating layer after etching (Fig. 2(c)) revealed particle elongation perpendicular to the deposition direction. This was caused by plastic deformation due to a ductile powder deposition formed during the high impact spray process [6].
Hardness measurement revealed that the initial powder featured hardness of 354.85 Hv and the manufactured coating layer as 490.51 Hv, which indicates that the manufactured coating layer achieved higher hardness than the initial powder. The cause of the increased hardness of the manufactured coating layer compared to the initial powder is known to be the peening effect during powder deposition [7].
Fig. 3 is the XRD analysis result of the initial powder and the manufactured coating layer. The initial powder featured γ-Ni, γ’-Ni3Al and β-NiAl phases, and the manufactured coating layer also featured identical phases without newly formed phases. And then, oxide phase is hardly detected. This is the result of an advantageous kinetic spray process which does not cause phase change after deposition as it does not utilize a high temperature heat source.
Fig. 4 is the XRD analysis result of the kinetic spray Ni-Cr-Al-Y coating layer after heat treatment at different temperatures. Even after heat treatment, there were no new phases regardless of the temperature and only three phases of γ-Ni, γ’-Ni3Al and β-NiAl were observed. There is almost no peak of oxide. In particular, after heat treatment at 600°C, the γ’-Ni3Al phase and β-NiAl phase were observed more clearly compared to as-sprayed and 400°C heat treated.
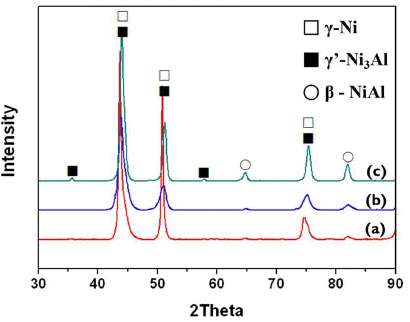
Results of the XRD analyses following the Ni-Cr-Al-Y coating layer’s heat treatment: (a) as-sprayed, (b) 400°C/1 hr heat-treated and (c) 600°C/1 hr heat-treated.
Fig. 5 shows cross-sectional images of the kinetic spray Ni-Cr-Al-Y coating layer with different heat treatment temperatures. At 400°C (Fig. 5(a)), there were defects in some particle interfaces (circle), but at 600°C (Fig. 5(b)) the particle interfaces disappear and the defects are gradually reduced. As such, the microstructural evolution of the kinetic spray coating layer is reported to be formed through recovery, recrystallization and grain growth due to heat treatment.
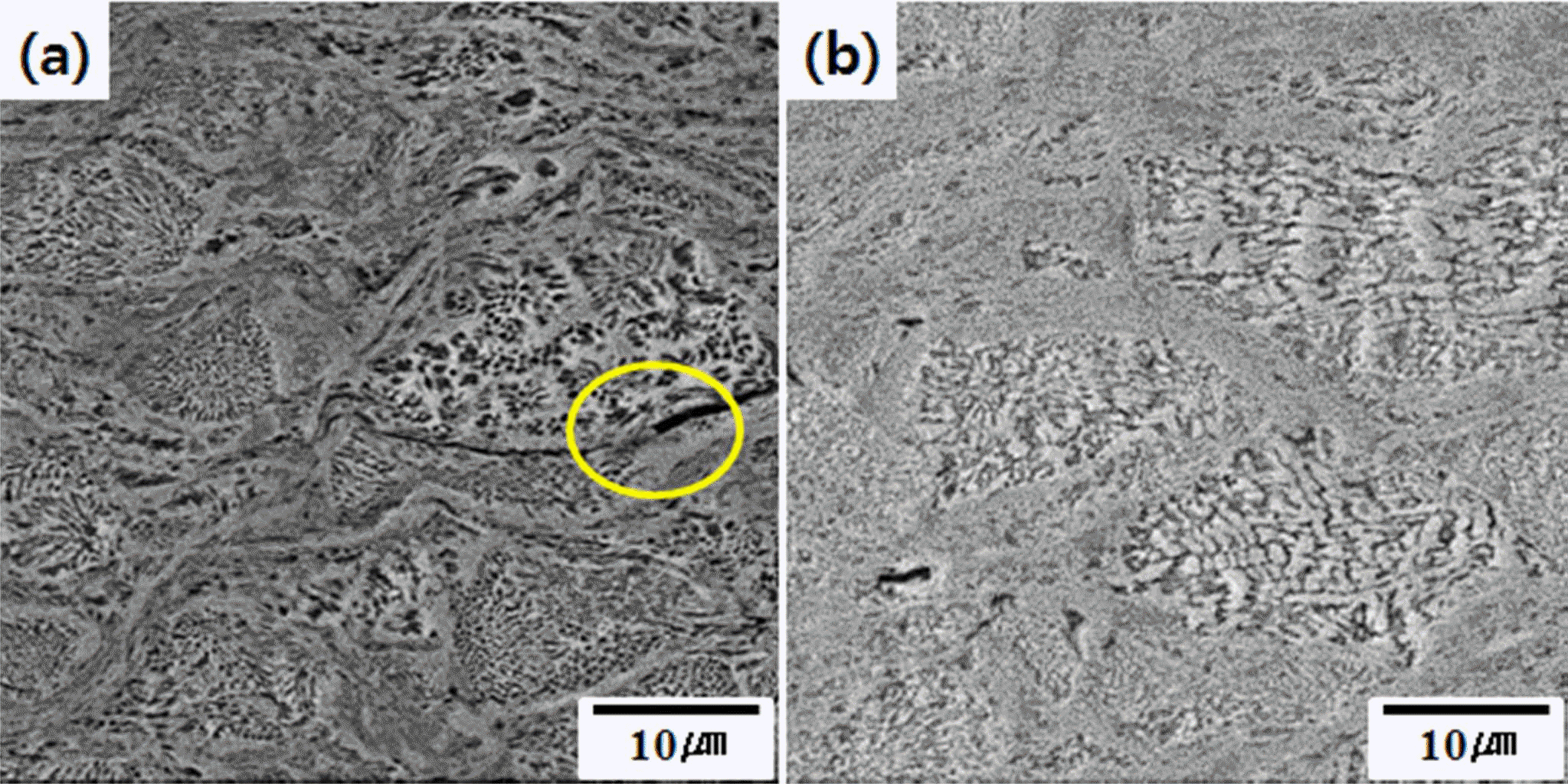
Microstructure after Ni-Cr-Al-Y coating layer’s heat treatment: (a) 400°C/1 hr, heat-treated and (b) 600°C/1 hr heattreated.
Fig. 6 is the porosity and hardness change of the kinetic spray coating layer at different temperatures. As depicted in Fig. 6(a), porosity showed a tendency of reduction as temperature increased. While there were no significant changes at 400°C, porosity at 600°C reduced significantly, by 1.85%. This is a result falling in line with Fig. 5 where the regional defects found on particle interfaces at 400°C significantly decrease at 600°C. Therefore, optimal heat treatment of a kinetic spray Ni-Cr-Al-Y coating layer allows a density improvement effect through porosity reduction. In the case of hardness (b), the hardness reduced at 400°C of heat treatment temperature. This is considered to be caused by the softening and recovering of the coating layer due to the annealing effect at 400°C heat treatment. On the other hand, the reduced hardness increased at 600°C heat treatment. Peng et al. [8] have reported that heat treatment applied to Ni-Cr-Al bulk alloy could cause the main reinforcement phase, γ’-Ni3Al phase, to reprecipitate and result in increased hardness. It is considered that heat treatment on the kinetic spray coating layer may produce a similar result, and this is confirmed by the main reinforcement phase, γ’-Ni3Al phase, being identified at 600°C heat treatment in the Fig. 4 XRD analysis result of the manufactured coating layer.
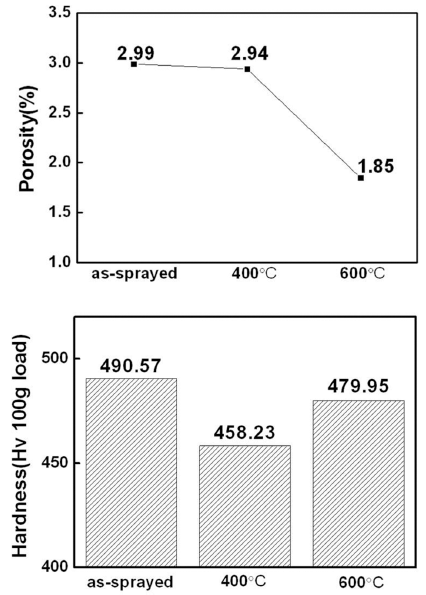
Changes in the porosity (a) and hardness (b) of the Ni-Cr-Al-Y coating layer following heat treatment.
Based on the findings above, this study was able to manufacture a high density Ni-Cr-Al-Y coating material with nearly no oxides using the kinetic spray process. In addition, post heat treatment on the manufactured layer enabled further improvement of density by reducing porosity and increasing the hardness of the manufactured coating layer. Thus, the kinetic spray Ni-Cr-Al-Y coating layer is expected to apply for the protection of metal components in anti-oxidation/anti-corrosion applications.
4. Conclusions
This study manufactured a Ni-Cr-Al-Y coating layer using a kinetic spray process and investigated the microstructure and properties after heat treatment to make the following conclusions:
A Ni-Cr-Al-Y coating layer with 1.5 mm thickness can be manufactured using the kinetic spray process. The porosity of the coating layer was measured at 2.99% and hardness measured at 490.57 Hv. XRD phase analysis identified γ-Ni, γ’-Ni3Al and β-NiAl phases in both the initial powder and coating layer.
After applying heat treatment to the Ni-Cr-Al-Y coating layer, porosity tended to decrease as heat treatment temperature increased. Porosity of 2.99% before heat treatment decreased to 1.85% after heat treatment at 600°C, making it possible to expect further density improvement. In the case of hardness, 400°C heat treatment decreased the hardness, but 600°C heat treatment produced a slight increase in hardness.
Acknowledgements
This research was supported by the Program for the Training of Graduate Students in Regional Innovation in Korea.