TiH2를 이용한 nano Mo-ODS 합금의 Y2Ti2O7 미세화 연구
The Use of TiH2 to Refine Y2Ti2O7 in a Nano Mo-ODS Alloy
Article information
Trans Abstract
Mo-ODS alloys have excellent mechanical properties, including an improved recrystallization temperature, greater strength due to dispersed oxides, and the ability to suppress grain growth at high temperatures. In ODS alloys, the dispersed Y2O3 and added Ti form Y-Ti-O complex oxides, producing finer particles than those in the initial Y2O3. The complex oxides increase high-temperature stability and improve the mechanical properties of the alloy. In particular, the use of TiH2 powder, which is more brittle than conventional Ti, can enable the distribution of finer oxides than is possible with conventional Ti powder during milling. Moreover, dehydrogenation leads to a more refined powder size in the reduction process. This study investigated the refinement of Y2Ti2O7 in a nano Mo-ODS alloy using TiH2. The alloy compositions were determined to be Mo-0.5Ti-0.5Y2O3 and Mo-1.0Ti-0.5Y2O3. The nano Mo-ODS alloys were fabricated using Ti and TiH2 to explore the effects of adding different forms of Ti. The sintered specimens were analyzed through X-ray diffraction for phase analysis, and the microstructure of the alloys was analyzed using scanning electron microscopy and transmission electron microscopy. Vickers hardness tests were conducted to determine the effect of the form of Ti added on the mechanical properties, and it was found that using TiH2 effectively improved the mechanical properties.
1. Introduction
몰리브데넘(Mo)은 refractory metal의 한 종류로서 높은 융점(2620°C), 우수한 크리프 저항성 및 내식성, 낮은 열팽창 계수, 우수한 열 전도성을 가지며 비중이 낮아 다양한 산업 분야에 적용하기 위한 연구가 다양하게 진행되고 있다[1, 2]. 특히, Mo는 기존의 니켈 및 코발트 합금보다 뛰어난 고온 저항성을 보여 터빈 및 로켓 엔진 등 고온환경에서 적용할 수 있는 차세대 합금으로 주목받고 있다[3]. 그러나, 순수 몰리브데넘은 낮은 강도, 상온에서의 부족한 연성, 낮은 재결정 온도, 높은 취성-연성 전이 온도 등의 단점을 지니고 있으며, 이러한 문제점을 극복하고자 지난 수십 년간 몰리브데넘의 상온 및 고온 특성을 개선하기 위한 다양한 연구가 진행되어 왔다. 특히 몰리브데넘을 나노 사이즈로 제조하는 방법은 Mo의 특성을 개선하는 효과적인 접근법 중 하나로, 소결 시 구동력이 높은 나노 사이즈의 Mo로 인해 소결 온도를 낮추고 밀도를 향상시키며, 결정립의 미세화를 촉진하는 등의 효과를 얻을 수 있다[4-6]. 또한 Mo 기지내에 다양한 희토류계 산화물(Y2O3, La2O3, ZrO2 등)을 분산시켜 기계적 특성을 향상시키는 Mo-산화물 분산 강화(ODS)합금에 대한 연구도 활발히 진행되고 있다[7, 8]. ODS 합금에서 가장 중요한 요소는 산화물의 크기와 분산도로, 산화물이 미세하고 고르게 분포할수록 합금의 성능이 향상되며, 밀링과 같은 초기 공정 단계에서 산화물의 크기를 조절하는 것이 최종 산화물의 크기 및 분포에도 영향을 끼칠 수 있다는 사실 또한 많은 연구들을 통해 확인되었다[9, 10]. 이러한 다양한 첨가 산화물 중에서도 뛰어난 고온 안정성으로 인하여 초기 성장이 느리게 일어나 미세하고 고른 산화물을 형성하는 Y2O3를 Mo에 적용하기 위한 연구가 다양하게 진행되고 있다. 또한, Y2O3가 분산된 ODS 합금에 다양한 원소들(Ti, Zr, Hf)을 첨가하면 기존 Y2O3보다 미세한 Y2Ti2O7 산화물 입자를 형성하고, 이러한 Y2Ti2O7 상은 고온에서의 높은 활성화 에너지로 인하여 성장이 느리게 일어나 고온 안정성을 크게 향상시킨다[11-13]. 특히 Mo-Y2O3 ODS 합금에 Ti원소 첨가 시 소결중 Y-Ti-O 다원계 산화물이 생성되어 나노스케일의 산화물 분포를 향상시켜 재결정화 온도를 상승시키고, 결정립 성장을 억제하여 고온에서의 기계적 특성을 크게 향상시킬 뿐만 아니라 Ti가 Mo 기지에 고용되어 합금의 고용강화 효과도 볼 수 있다[14].
하지만 Mo의 소결은 일반적으로 1400°C 이상의 고온에서 이루어진다. 이 과정에서 Ti가 산화되어 100nm 이상의 조대한 산화물이 생성될 수 있으며, 이는 전위 집중을 유발하여 크랙을 초래하고, 합금의 특성을 저하시킬 수 있다[15]. 또한 미세 Ti 분말의 경우 제조공정이 어렵기 때문에 단가가 높고 금속 형태의 Ti의 경우 세라믹 상인 산화물 분말보다 밀링 중 미세화가 어렵다는 단점이 있다. 이에 대한 해결책으로, 수소 취성으로 미세화가 용이한 TiH2를 적용할 경우 밀링과정에서 미세화가 빠르게 일어날 뿐만 아니라 열처리를 통한 탈수소화 과정이 추가적인 미세화를 가능하게 한다. 또한 소결 중 탈 수소화가 진행되어 생성된 수소 가스가 시편 내 잔존 산소를 포집하여 합금의 밀도를 높이고 치밀화를 촉진한다. 이 과정에서 생성된 미세 Ti는 낮은 온도에서 핵 생성이 가능하여, 미세하고 균일한 산화물의 형성이 가능해진다[16]. 따라서 TiH2를 이용한 Y2Ti2O7 상이 형성된 ODS 합금 제작 시 우수하고 균일한 미세구조를 형성한 합금 제작이 가능할 것으로 판단하였다.
본 연구에서는 나노 사이즈의 Mo와 Y2O3, Ti, TiH2를 이용하여 Y2Ti2O7 상이 분포된 Mo-ODS 합금을 제작하였으며, TiH2를 통해 nano Mo-ODS 합금의 Y2Ti2O7 상의 미세화에 대한 연구를 진행하였다. 이를 위해 분말 및 소결 시편의 상 분석 및 미세구조 분석을 진행하였으며, 기계적 특성 분석을 통해 Ti첨가 형태에 따른 산화물의 크기 및 균일성이 합금의 기계적 특성에 미치는 영향을 분석하였다.
2. Experimental methods
본 연구에서는 MoO3(99.9%, 45μm, EML), Y2O3(99.9%, 35nm, RND Korea), Ti(99.9%, 45um, Kojundo Chemical), 및 TiH2(99.9%, 10μm, RND Korea) 분말을 원재료로 사용하여 Y2Ti2O7산화물이 분포한 Mo-ODS 합금을 제조하였다. Y2O3의 첨가량은 기존의 연구결과에서 최적의 특성을 나타내는 함량인 0.5Wt.%로 설정하였다. 과도한 산화물의 첨가는 연성 및 인성 저하를 초래하고 고온에서 산화물의 급격한 성장이 일어나기 때문에 적절한 첨가량이 중요하다[17]. 순수 Ti 분말이 첨가된 조성은 ODS-Ti로, TiH2 분말을 첨가된 조성은 ODS-TiH2로 명명하였으며, 자세한 조성은 Table 1과 같다. 이때의 Mo의 분율은 환원된 나노 Mo의 분율을 기준으로 계산되었다. 해당 분말은 Planetary mill(PM400, Retsch)을 통해 볼(Sus 304 ball, 5mm)과 분말을 10:1의 비율로 장입하여 200 rpm의 회전 속도로 밀링을 진행하였다. 밀링 시간은 20분 밀링, 10분 휴식의 사이클로 순수 휴식시간을 제외하고 총 20시간 동안 밀링을 진행하였으며, 공정 중 분말의 산화를 방지하기 위하여 Ar 가스를 주입하였다. 또한 밀링과정에서 분말의 응집을 방지하기 위하여 매 사이클 마다 회전방향을 반대로 진행하였다. 제조된 밀링 분말은 주사 전자 현미경(SEM, JSM-6360, JEOL)을 이용하여 Ti 첨가형태에 따른 밀링 분말의 크기 및 미세구조를 확인하였다. 이렇게 제조된 밀링분말은 튜브로를 이용하여 수소 분위기에서 600°C까지 10°C/min의 속도로 승온을 한 후 해당온도에서 3시간 동안 환원을 진행하여 nano-Mo ODS 분말을 제조하였다. 제조된 나노 Mo-ODS 분말은 X선 회절기(XRD, Miniflex 600, Rigaku)를 이용하여 스캔 속도를 10°/min로 상 분석을 실시하였다. 이후 일축 성형기를 이용하여 300 MPa에서 성형 시편을 제조한 후, 튜브 로를 이용하여 수소 분위기에서 1400°C까지 10°C/min의 속도로 승온을 진행한 후 해당 온도에서 5시간 동안 소결을 진행하였다. 제조된 소결 시편은 XRD를 이용한 상 분석 및 아르키메데스법을 이용한 밀도 분석을 실시하였으며, 투과 전자 현미경(TEM, JEM2100F, JEOL)을 이용하여 결정립 미세화, 산화물 분산도 및 크기를 분석하였다. 또한 비커스 경도 측정을 실시하여 기계적 특성을 평가하였다.
3. Results and Discussion
Fig. 1. (a), (b)는 Ti 첨가 형태를 달리 한 ODS 합금의 밀링 분말의 SEM 분석 결과이다. 분석결과, ODS-0.5TiH2 밀링 분말이 ODS-0.5Ti 분말보다 미세하고 균일하게 밀링이 진행된 것을 확인하였다. 이는 TiH2의 초기 분말이 10μm 이내로 Ti 분말보다 미세하고 수소 취성으로 인해 밀링 중 미세화가 더욱 빠르게 진행되었기 때문으로 판단하였다. 이후 밀링분말의 환원을 진행하였으며, 환원분말의 SEM 분석결과는 Fig. 1. (c), (d)와 같다. Fig. 1. (c) 에서 확인되는 Ti 가 첨가된 환원 분말에서는 환원 과정을 통해 나노 사이즈의 Mo가 확인되며, 완전히 미세화가 진행되지 않은 5μm 이하의 Ti로 예상되는 입자들이 확인되었다. Fig. 1. (d)에서 확인되는 TiH2가 첨가된 환원분말의 SEM 분석 결과, 고에너지 밀링을 통해 미세화가 진행된 TiH2가 환원 중 탈 수소화 과정으로 인하여 분말의 미세화가 한 번 더 진행되었기 때문에 ODS-Ti 환원 분말보다 더욱 균일하고, 미세한 형태를 나타내는 것으로 확인되었다.
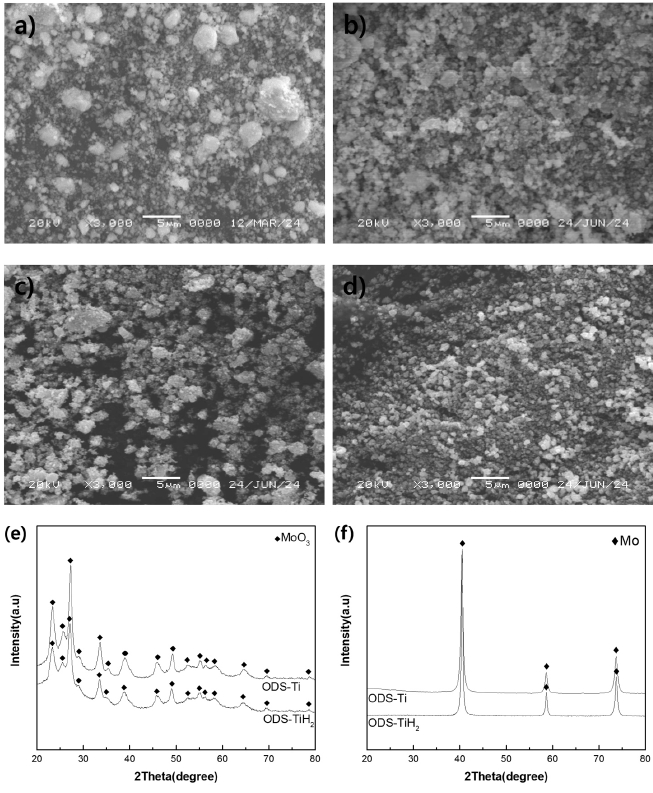
Scanning electron microscopy images of planetary ball-milled nano Mo-ODS powder, (a) ODS-0.5Ti, (b) ODS-0.5TiH2 and X-ray diffraction patterns of Mo-0.5Y2O3-0.5Ti powder, (c) ball-milled powder, (d) hydrogen reduced powder
XRD을 통해 관찰한 Ti 첨가형태에 따른 밀링 분말 및 환원 분말의 상분석 결과는 Fig. 1. (e), Fig. 1. (f)와 같다. Fig. 1. (e)에서 확인되는 밀링 분말 분석 결과 밀링과정에서 분말의 미세화 및 비정질화로 인하여 피크의 확장이 발생하였기 때문에 MoO3(JCPDS NO: 65-2421) 이외의 다른 상은 관찰되지 않았다. 또한 산화물의 경우 미세화로 인해 피크가 확인되지 않으며, 그 외 불순물 및 다른 산화물 상은 확인되지 않았다. Fig. 1. (f)에서 확인되는 환원분말의 XRD 분석 결과 Y2O3 및 Ti는 결정화 온도 이하이기 때문에 관찰되지 않았으며, MoO3의 환원이 완전히 진행되어 Mo 피크만이 확인되었다.
Fig. 2는 XRD를 통한 ODS-Ti 및 ODS-TiH2 소결 시편의 XRD 분석 결과이다. Fig. 2. (a)의 ODS-0.5Ti 시편에서는 Mo와 Y2Ti2O7 다원계 산화물 상이 안정적으로 형성된 것을 확인하였다. Fig. 2. (b) 의 ODS-0.5TiH2 시편에서도 Y2Ti2O7 상이 확인되었으며 이외에 다른 상은 확인되지 않기 때문에 시편 내의 TiH2가 환원 및 소결 중 완전히 탈 수소화가 진행된 것으로 판단되었다. ODS-1.0Ti 및 ODS-1.0TiH2 시편의 경우, Y2Ti2O7 다원계 산화물 상이 확인되었다. 그 이외에도 TiO2 상이 확인되었으며, 이를 통해 Mo와 Ti는 전율고용체 관계에 있지만, 첨가된 Ti는 고용체를 형성하지 않고 소결 중 미세 산소와 반응하여 Ti계 산화물을 우선적으로 형성하는 것을 확인할 수 있다.
이후 성형 시편 및 소결 시편의 밀도를 측정하였으며, 그 결과는 Table 2 와 같다. 성형 밀도 분석 결과, ODS-0.5Ti, ODS-0.5TiH2 시편은 각각 38.33%, 38.12%, ODS-1.0Ti 및 ODS-1.0TiH2 시편은 37.62%, 37.41%로 ODS-Ti 성형시편이 ODS-TiH2 성형시편보다 성형밀도가 미세하게 높은 값을 나타내는 것을 확인하였다. 또한 소결 시편 밀도 측정결과, ODS-0.5Ti 시편은 98.8%, ODS-0.5TiH2 시편은 99.1%, ODS-1.0Ti 시편은 98.1%, ODS-1.0TiH2 시편은 98.3%로 ODS-Ti 및 ODS-TiH2 시편 모두에서 Ti 함량이 0.5 wt.% 첨가된 시편에서 더 높은 밀도값을 나타내었다. 이는 초기 성형 밀도에 의한 결과로 성형성이 좋은 Mo 분률이 높은 ODS-0.5Ti 및 ODS-0.5TiH2 시편에서 더 우수한 밀도값을 보이는 것으로 판단된다. Ti 첨가 형태에 의한 밀도차이는 성형 시편의 경향성과 반대되는 결과를 나타내며, 모든 TiH2를 이용한 소결 시편에서 밀도가 상승하는 것을 확인하였다. 이는 소결 과정에서 분말의 미세화로 인해 소결 구동력이 상승하여 치밀화가 촉진되었으며, 탈수소화 과정에서 시편 내 잔존 산소가 포집됨에 따라 합금의 기공이 감소하고, 그 결과 밀도가 증가한 것으로 판단된다.
다음은 Ti 첨가형태에 따른 Y2Ti2O7 상의 형성 거동을 관찰하기 위해 소결 시편의 TEM 분석을 진행하였으며, Fig. 3는 ODS-Ti 및 ODS-TiH2 소결 시편의 TEM 분석 결과이다. 산화물의 크기 및 분포도 측정을 위해 시편 당 400개 이상의 산화물의 크기 및 분포를 측정하였으며 그 결과는 Fig. 4 와 같다. 측정 결과, ODS-0.5Ti 및 ODS-1.0 Ti 시편의 산화물의 평균 크기는 17.43nm, 19.85nm, ODS-0.5TiH2, ODS-1.0TiH2. 시편의 평균 산화물 크기는 14.27nm, 18.07nm로 측정되었다. 이를 통해 ODS-TiH2 시편에서 평균 산화물의 크기가 ODS-Ti 합금의 산화물 평균 크기보다 미세하게 형성된 것을 확인할 수 있다. 표준편차 또한 모든 ODS-TiH2의 시편에서 동일 조성의 ODS-Ti 시편보다 낮은 것으로 확인되며 ODS-TiH2 시편에서 더욱 미세하고 고른 분포의 산화물이 형성됨을 확인하였다.
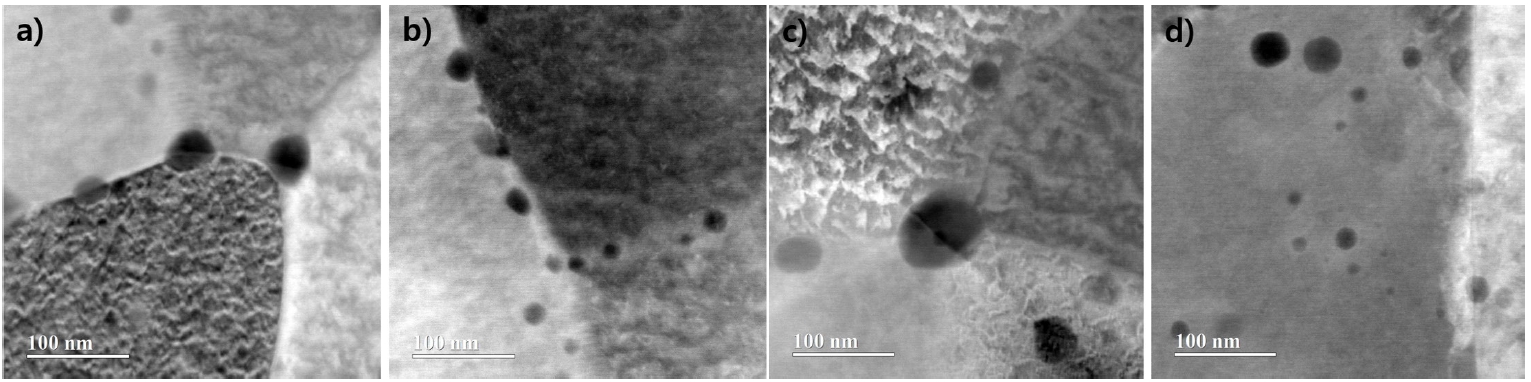
Transmission electron microscopy images of (a) ODS-0.5Ti, (b) ODS-0.5TiH2, (c) ODS-1.0Ti, and (d) ODS-1.0TiH2 alloys.
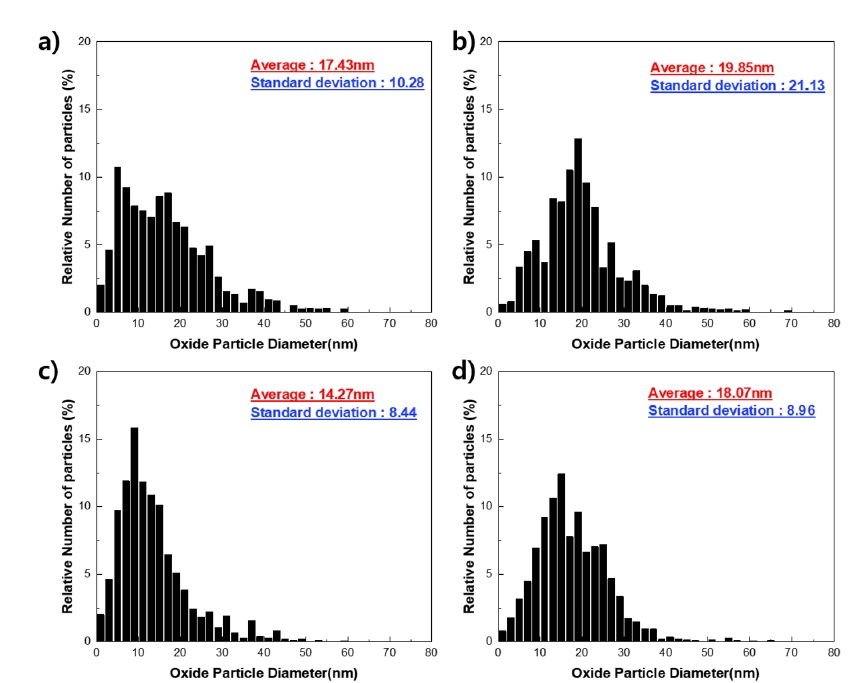
Size distribution of nanoparticles in Mo-ODS sintered specimens. (a) ODS-0.5Ti, (b) ODS-1.0 Ti, (c) ODS-0.5TiH2, and (d) ODS-1.0TiH2.
추가적으로, TEM 이미지를 통해 분석한 100여 개의 Grain size 분석 결과, ODS-0.5Ti, ODS-1.0Ti, ODS-0.5TiH2, ODS-1.0TiH2 시편에서 각각 284nm, 321nm, 212nm, 233nm로 모든 ODS-TiH2 시편에서 동일 조성의 ODS-Ti 보다 미세한 Grain size 형성이 확인되었다. 이는 첨가된 Ti 분말보다 TiH2 분말이 초기 밀링 및 열처리 과정에서 Ti 미세화에 유리하여, 소결 중 Y2Ti2O7 상 형성 시 미세하고 균일한 산화물이 형성되었으며, 이러한 산화물에 의한 결정립 성장 억제 효과로 Grain size또한 미세하게 형성된 것으로 판단된다. 이러한 결과를 통해 ODS-TiH2 합금에서 더욱 미세하고 균일한 산화물의 분포 및 미세한 Grain size를 나타내는 것으로 분석할 수 있다.
Fig. 5 은 ODS-Ti 와 ODS-TiH2의 Ti 함량에 따른 Vickers Hardness 측정 결과이다. ODS-0.5Ti, ODS-1.0Ti 및 ODS-0.5 TiH2, ODS-1.0TiH2시편의 경도 값은 각각 358.1 Hv, 304.5 Hv, 367.8 Hv, 355.0 Hv로 확인되었다. 이는 기존 Pure Mo 합금에 비해 27% 이상 향상된 수치이다[18]. 또한, 모든 ODS-Ti 및 ODS-TiH2 시편에서 Ti 첨가량이 0.5 wt.% 인 시편에서 더 높은 경도 값을 나타내었다. 이러한 결과는 Table 2 및 Fig. 3에서 확인할 수 있듯이 Mo의 높은 분율, Y2Ti2O7 상의 안정적인 형성 및 Ti계 조대산화물의 미형성으로 인하여 더 높은 밀도 값을 나타내었기 때문으로 판단된다. 또한 동일한 Ti 함량에서 Ti를 이용한 ODS 시편에 비해 TiH2를 이용한 ODS 시편에서 미세하고 균일한 산화물 형성이 더 유리하며, 이로 인해 결정립 성장 억제가 효과적으로 이루어졌으며, 그 결과 더 높은 경도값을 나타내는 것을 확인하였다.
4. Conclusion
본 연구에서는 Y2Ti2O7 상이 분포한 Mo-ODS 합금 소결시편을 제조하였으며, Ti 첨가 형태를 달리하여 미세구조 개선 및 기계적 특성의 향상을 확인하였다.
MoO3, Y2O3 분말과 Ti 및 TiH2 분말을 첨가하여 Mo-ODS 분말을 제조하였으며 20시간의 고에너지 밀링 결과 취성이 높은 ODS-TiH2 분말이 균일한 형태로 밀링이 진행되는 것을 SEM 분석을 통해 확인하였다. 이후 환원 공정을 통해 나노 크기의 Mo 분말을 제작하였고, 일축성형 및 1400°C 조건에서 열처리를 통해 소결 시편을 제작하였다. 상 분석 결과, Y2Ti2O7 다원계 산화물이 안정적으로 형성되었으며, 과량 첨가된 Ti 및 TiH2에 의해 Ti계 산화물의 형성 또한 확인하였다. 또한 아르키메데스를 통한 밀도분석 결과 ODS-TiH2 시편에서 더 높은 밀도를 나타내는 것을 확인하였으며, TEM 분석을 통해 미세구조 분석 결과 ODS-TiH2 시편에서 미세한 Grain size가 형성되었으며 미세하고 균일한 형태의 산화물의 형성을 확인하였다. 그 이유는 환원 및 소결 과정에서 TiH2의 탈 수소화가 진행되며 시편 내의 잔존 산소를 포집하여 기공을 감소시키고, 탈 수소화 이후 미세 Ti가 생성되어 Y2Ti2O7 상의 생성 및 성장이 느리게 일어나기 때문이며 이러한 미세 산화물이 소결 과정에서 결정립의 성장을 억제하였기 때문으로 판단하였다. 이로 인해 Vickers Hardness 측정결과, 모든 ODS-TiH2 시편에서 더욱 우수한 경도 특성을 확인하였다.
이러한 결과를 종합해 보았을 때 TiH2를 이용한 Y2Ti2O7 상이 분포한 ODS 합금의 제작은 Ti를 이용한 ODS 합금에 비해 고밀도, 균일한 미세구조 그리고 높은 경도 등 Y2Ti2O7 상이 분포한 ODS 합금 제작에 있어 우수한 특성을 나타내는 것으로 판단된다.
추후 연구에서는 상온 및 고온에서의 추가적인 기계적 특성 분석과 미세구조 분석을 통해 합금의 응용 가능성을 더욱 확장할 예정이다. 본 연구진은 현재 Mo-Si-B 합금 제작 시, Mo가 Intermetallic 상을 감싸고 있는 Mo-Si-B Core-shell 연구를 진행중이며, 본 연구를 통해 Y2Ti2O7 상이 분포한 Mo-ODS 합금을 이용하여 쉘의 특성을 향상시켜, 기존보다 우수한 Mo-Si-B 합금을 개발할 수 있을 것으로 기대된다. 나아가, 이러한 연구는 초고온 재료의 기초 연구와 원천기술 확장에 기여할 수 있을 것으로 판단된다.
Notes
Conflict of Interest
저자들은 이해상충관련 해당사항 없음을 선언합니다.
Author Information and Contribution
직위: 하윤철, 이원희: 학생, 변종민, 김영도: 교수, 박천웅: 연구원
Acknowledgement
본 연구는 2016년도 정부(교육부)의 재원으로 한국연구재단의 지원을 받아 수행된 기초연구사업임(2016R1A6A1A03013422), 본 연구는 2016년도 정부(교육부)의 재원으로 한국연구재단의 지원을 받아 수행된 기초연구사업임 (2022R1A2C10113).