레이저 파우더 베드 퓨전 3차원 적층된 Cu-10Sn 합금의 미세조직 및 기계적 특성
Microstructure and Mechanical Properties of Laser Powder Bed Fusion 3D-Printed Cu-10Sn Alloy
Article information
Trans Abstract
This study investigated the optimal process conditions and mechanical properties of Cu-10Sn alloys produced by the powder bed fusion (PBF) method. The optimal PBF conditions were explored by producing samples with various laser scanning speeds and laser power. It was found that under optimized conditions, samples with a density close to the theoretical density could be fabricated using PBF without any serious defects. The microstructure and mechanical properties of samples produced under optimized conditions were investigated and compared with a commercial alloy produced by the conventional method. The hardness, maximum tensile strength, and elongation of the samples were significantly higher than those of the commercially available cast alloy with the same chemical composition. Based on these results, it is expected to be possible to use the PBF technique to manufacture Cu-10Sn products with complex 3D shapes that could not be made using the conventional manufacturing method.
1. Introduction
일반적으로 3D프린팅으로 알려진 적층 제조(Additive Manufacturing, AM) 기술은 물체를 층별로 한 층씩 적층하여 생산하는 제조 공정이다[1]. AM의 단계는 다음과 같다: (1) CAD(Computer-Aided Design)를 이용하여 설계 모델을 생성하고 이 모델에서 STL(Standard Triangle Language)파일을 추출한 뒤, (2) STL파일에 프린팅 조건을 적용하여 모델 인쇄를 위해 3D 프린팅 장비에 업로드 되는 빌드 파일을 얻어 (3) 최종적으로 적층 제조를 하게 된다. 일반적으로 AM 적층 조형체는 바로 사용할 수 있으며 조립을 위해 최소한의 후가공이 필요할 때도 있다. 폴리머 및 세라믹 등 다른 종류의 재료와 비교할 때 금속 재료의 3D 프린팅은 항공우주, 자동차 및 방위 관련 응용 분야의 성장에 매우 중요한 부분으로 자리잡고 있다[2].
Powder Bed Fusion (PBF) 방식은 고출력의 밀도 레이저를 통해 금속 분말 미분(분말 직경 약 15 - 45㎛)을 용융하고 빠르게 냉각하여 각 층을 쌓아 정밀한 3차원의 부품을 제조하기 위해 개발된 적층 기법이다. PBF 공정에서 적층물의 각 층은 금속 미분이 매우 얇게 미리 깔려 있는 빌드 플랫폼에서 시작된다. 레이저를 고속으로 스캔하여 각 층의 단면을 원하는 형태로 녹여, 금속 분말이 완전히 용융되고 빠르게 냉각된 뒤 빌드 플랫폼이 설계된 한 층의 높이만큼 낮아지고 새로운 분말 층이 롤러 혹은 리코터에 의해 쌓인 후 다음 층이 용융되는 형태로, 이와 같은 과정이 반복하여 3차원의 정밀한 부품이 성형되게 된다. 분말 입자는 CAD설계에 따라 분말 베드에서 선택적으로 용융되어 3D 물체의 형상을 형성하게 된다[3].
한편, 구리-주석(Cu-Sn) 합금 또는 청동 합금은 우수한 내마모성, 내식성, 열전도성 및 전기전도성 때문에 베어링, 슬리브, 부시, 전기 커넥터 등의 형태로 다양한 산업 분야에서 사용되고 있다[4-7]. 염수에서의 우수한 부식 저항력으로 인해 Cu-Sn 합금은 해양 산업에서 다량 사용되고 있다[8]. Cu-Sn 합금은 Sn 함량이 증가함에 따라 기계적 특성과 화학적 내성이 향상되기 때문에 고Sn 함량 Cu-Sn 합금의 응용 범위를 확장하려는 시도가 이루어지고 있다[9-11]. 기존의 공정에서 단조, 압연, 인발 또는 절곡과 같은 소성 가공 공정은 합금을 필요한 모양으로 제조하고 정밀하고 복잡한 기계 부품을 생산하는 데 널리 사용되어 왔다. 그러나 Cu-Sn 합금에서 Sn의 분율이 높을 경우 취성이 상대적으로 강한 금속간화합물 상이 쉽게 생기기 때문에 가공성이 낮아 소성가공에 적합하지 않다[12, 13]. 이와 같은 이유로 Sn 이 10 wt.% 정도 함유된 Cu-Sn 합금은 주로 주조법으로 제조되고 있다[14-16].
PBF 기술은 타이타늄, 크롬, 코발트, 알루미늄, 구리, 강철 및 초합금을 포함한 다양한 금속 분말에 광범위하게 사용되고 있다. PBF 기술의 발전과 함께 다양한 연구에서 부품의 밀도가 품질에 중요한 역할을 한다는 것을 입증하고 있으며, 부품의 밀도에 대한 영향에 학자들의 폭넓은 관심이 집중되고 있다[17-19]. 하지만 PBF 기술을 이용, 구리 및 구리 합금을 사용하여 결함 없는 부품을 제조하기 위해서는 구리의 낮은 레이저 에너지 흡수율과 높은 열전도성으로 인해 레이저 스캔으로 충분한 깊이의 용융풀을 형성하기 어려운 단점을 극복해야 하며, 이를 위해 높은 레이저 출력과 스캔 속도의 조합이 필요하다[20].
현재까지 다양한 소재에 대한 PBF 제작이 시도되었으나, Cu-10Sn (wt.%) 합금의 PBF는 앞서 언급한 레이저 흡수율에 의한 제약으로 논문에서 그 사례를 찾아보기 어렵다. 본 연구의 주요 목적은 PBF 제조방식에서 매우 높은 레이저 출력을 사용하여 Cu-10Sn 분말의 최적화된 공정 변수를 찾고, 이 때 얻어지는 미세 구조 및 기계적 물성을 알아보는 것이다. 이를 위해 분말 입도 및 조성 분석, 시편 적층, 공정조건 수립을 위한 다양한 레이저 조건에서의 밀도 및 공극률을 측정하였고, 이를 토대로 결함이 최소화된 공정조건으로 제작한 PBF 프린팅 된 Cu-10Sn 합금의 미세조직 및 기계적 특성을 분석하였다.
2. Experimental Procedure
2.1. PBF 공정에 사용된 분말 원소재
본 연구에서 사용된 분말은 Gas atomization을 이용하여 제조된 Cu-10Sn (wt.%) 분말을 사용하였다. 주사전자현미경(Scanning Electron Microscope, SEM, MIRA 3 LMH, TESCAN, Czech Republic)을 통해 분말의 형상을 관찰한 결과를 Fig. 1에 나타내었다. Gas atomization에 의해 대부분의 분말이 구형의 형태로 제작된 것을 확인할 수 있다. 분말의 크기 및 입도분포를 확인하기 위해 PSA(Particle Size Analysis, Mastersizer 3000, Malvern Panalytical, United Kingdom) 분석을 진행하였다. Fig. 2 는 PSA 결과를 나타낸다. PBF 공정에 사용된 분말의 입도는 19.6 - 55.9 ㎛의 크기를 가지고 있으며 약 34.9 ㎛의 평균 입자 크기를 갖는 것을 확인할 수 있었다. 분말의 조성을 확인하기 위해 EDS(Energy-Dispersive X-ray Spectroscopy, XFlash6, Bruker, U.S.) 분석을 진행하였다. EDS 분석 결과 실험에 사용된 구리 분말의 Sn 함량은 약 9.31 wt.%으로 확인되었다.
2.2. Powder Bed Fusion
본 연구에서는 Cu-10Sn 분말을 결함이 거의 없이 PBF 3차원 적층 할 수 있는 공정 조건을 탐색하기 위해 PBF 공정탐색실험을 먼저 수행하였다. 공정탐색실험은 3차원 정육면체(10 X 10 X 10 mm³)의 시편을 다양한 공정조건으로 제작하는 방법으로 수행하였다. PBF 공정에서 레이저에 의한 용융풀의 크기와 형태를 결정하는 주요 공정변수는 hatching distance (h), layer thickness (t), laser power (P) 및 scanning speed (v) 등이 있으며, 이와 같은 공정변수들은 적층 중 단위 체적의 소재를 적층 하는 동안 아래 수식으로 주어지는 단위 체적 당 열에너지를 소재에 부가한다.
Eq. 1에서 VED(volumetric energy density)는 단위 체적당 주어지는 에너지 밀도를 나타내며, 실제로 생성된 용융풀의 크기와는 독립적인, 공정변수에 의해 결정되는 겉보기 체적에 대한 투입 레이저 에너지 밀도를 나타낸다. 본 연구에서는 Table 1 과 같이 h 및 v를 고정변수로 하고, P 와 v를 독립 변수로 변경하면서 다양한 조건에서 정육면체 시편을 제작하여 시편의 밀도를 측정하여 기공 등의 결함의 밀도를 유추하였다. 공정 중 각 층은 지그재그 패턴으로 레이저 스캔하였다. 이 때, 재료의 이방성을 최소화 하기 위해 각 층의 레이저 스캔 경로의 층간 rotation은 67°로 설정하였으며, P 와 v는 각각 50 W, 100 mm/s 단위로 변경하면서 실험하였다. 여러 가지 레이저 출력과 스캔 속도로 샘플을 적층하였으므로, 시편들을 일정 간극을 두어 bed 내에 배치하여 한 bed 당 9개씩 배치하여 제작하였다.
2.3. 미세조직 및 기계적 특성 분석
제작된 시편들의 겉보기 밀도를 측정하기 위해 아르키메데스 방법으로 밀도측정기(Density Balance, Mettler Toledo, XS205 DualRange, Switzerland)를 사용하였으며, 밀도 측정에 앞서 표면의 이물질을 제거하기 위해 에탄올로 초음파 세척을 진행하였다. 이물질이 제거된 시편을 200°C의 히팅건으로 30초간 완전 건조 후, 밀도 측정기를 이용하여 시편의 밀도를 측정하였다. 밀도 측정은 정육면체 시편 전체를 한 번에 측정하였다. 측정된 밀도와 Energy density를 이용하여 겉보기 밀도 그래프를 나타내었다. 한편, 제작된 시편들의 레이저 조건에 따른 기공결함을 관찰하기 위해, 샘플을 커팅, 연마하여 광학현미경(Optical Microscope, GX41, OLYMPUS, Japan)을 사용, 단면을 관찰하였다 (Fig. 3). 이 때, 각 시편의 XY단면 5개, Z단면 5개의 광학이미지에서 평균 기공율을 측정하였으며, 기공율은 P = 350 W, v = 1,100 mm/s 조건에서 0.261 %로 가장 적은 기공율을 확인할 수 있었으며 이 조건에서 제작된 샘플의 미세조직을 주사전자현미경(Scanning Electron Microscope, MIRA 3 LMH, TESCAN, Czech) 및 X선 회절 분석(X-ray Diffractometer, Smartlab, Rigaku, Japan)을 통해 상세 분석하였다. 미세조직 관찰 시험편은 질산 30% 수용액으로 10초간 화학에칭하여 준비하였다. 동일 조건으로 제작된 샘플의 기계적 특성을 마이크로 비커스경도계(Micro Vickers hardness, HM-220B, Mitutoyo, Japan)를 활용하여 하중 0.3 Kgf, 유지시간은 5초로 설정하여 측정하였다. 인장시험은 만능인장시험기(Universal Testing Machine, Quasar50, GALDABINI, Italy)를 사용하였으며, 시험속도는 2 mm/min으로 수행하였다. 인장시험편은 ASTM E8/E8M 판상 규격 sub size 형태로 적층제조 하였으며, 적층 방향에 수직, 수평한 3 방향으로 각각 3개씩 출력하여 인장 강도와 연신율을 측정하였다.
3. Results and Discussion
3.1. 레이저 적층조건에 따른 미세조직의 변화
Fig. 4는 Table 1 의 공정변수들로 제작한 시편의 이미지이다. PBF 제작 공정중 크랙이나 분말 미용융에 의해 제작 중 파손된 시편은 없었으며, 육안 검사에서도 크랙 등의 결함은 관찰되지 않았다.
제작한 시편들의 밀도들 측정하기 위해, EDM(Electrical Discharged Machining) 장비로 절단 가공 후 밀도 측정을 진행하였고, 각 레이저 파라미터로 산출된 VED와 측정된 겉보기 밀도를 비교하여 Fig. 5에 나타내었다. 레이저 출력과 속도에 따라 동일 에너지밀도에서도 샘플의 밀도는 약간의 편차를 보이지만, 에너지 밀도가 높아지면 샘플의 밀도가 뚜렷하게 상승하며 에너지밀도 150 J/mm3 이상의 조건에서는 약 8.6 g/cm3 이상의 밀도로 수렴하는 것을 볼 수 있다. Cu-10Sn 합금의 이론밀도는 Sn이 완전히 고용화 되어 있다고 가정할 때 약 8.74 g/cm3 이므로, 8.6 g/cm3 이상의 샘플 밀도는 이론밀도 대비 98 % 이상이 매우 높은 밀도이며 이를 통해 에너지 밀도가 150 J/mm3 이상일 때에는 레이저에 의해 충분한 양의 Cu-10Sn 분말이 용융되어 이론밀도에 가까운 밀도로 적층재가 성형되며, 이로 인해 더 이상의 에너지밀도 증가에도 샘플의 밀도는 큰 상승이 없는 것으로 사료된다.
3.2. 최적 성형밀도로 적층제조된 Cu-10Sn 합금의 미세조직
Fig. 6 은 Fig. 2 와 Fig. 3의 결과에서 가장 높은 밀도를 보였던 P = 350 W, v = 1,100 mm/s 의 조건으로 적층제조된 Cu-10Sn 합금의 단면 미세조직을 광학현미경으로 관찰한 것으로, 레이저가 인가되며 분말이 녹아 용융풀이 형성되고, 레이저 스캔에 따라 용융풀들이 겹쳐져서 재료가 조형되는 공정의 특성상 용융풀들이 겹쳐진 특징적인 형태의 미세조직을 관찰할 수 있다. 화학에칭 후 관찰된 광학현미경 미세조직에서 용융풀 경계 영역이 뚜렷하게 관찰되는 것을 알 수 있는데, 이는 국부적인 급속 용융 과정에서 용융풀 경계부에 미세 원소가 편석될 수 있고, 이 부분이 용융풀이 응고 및 수축할 때 주변 영역간의 열변형 차이에 의해 상대적으로 높은전위밀도를 가지기 때문에 화학 에칭시 경계부가 두드러지게 나타나는 것으로 생각된다[21].
용융풀 경계부의 결정립 형태를 관찰해 보면 몇몇 Columnar grain은 용융풀 경계를 지나서 결정성장을 한 것을 알 수 있으며, 용융풀의 수평길이는 대략 500-700 µm 였다. 용융풀의 높이는 약 50 µm 정도로 관찰되었다.
Fig. 7 (a) 에 광학현미경으로 관찰된 합금의 전반적인 미세구조를 나타내었다. 넓은 영역에서 합금의 미세조직을 관찰해 보면 재료공정중 발생한 결함이 드물게 관찰되는데, 결함의 크기와 숫자는 크지 않았다. 미세조직에서 관찰되는 결함은 크게 2 가지의 결함으로 분류할 수 있었으며, Fig. 7 (b) 와 (c)에 대표적으로 관찰되는 2 가지의 결함을 전자주사현미경으로 관찰하여 나타내었다. Fig. 6 (b)에 나타난 것과 같은 구형기공은 공정중 유입되거나 분말상태에서 함유되어 있던 가스에 의한 gas pore 로 생각되며, 그 외 불규칙한 형태로 관찰되는, Fig. 7 (c)와 같은 결함은 레이저가 분말의 용융을 충분히 일으키지 못해서 용융풀 사이의 일부 영역이 미성형 상태로 남아 있는 lack of fusion 형태의 결함으로 생각된다. 이 중 gas pore의 경우 그 수와 크기가 작아 기계적 특성에 큰 영향을 미치지 않을 것으로 생각되지만 lack of fusion 결함의 경우 기계적 특성을 저하시킬 것으로 생각되며, 본 실험에서 높은 레이저출력(350 W)을 사용하였음에도 불구하고 구리의 높은 열전도도 및 낮은 레이저 흡수율로 인해 부분적으로 발생한 것으로 보인다. 추후 연구에서는 레이저 출력을 더욱 높이거나 hatch spacing을 줄이는 등의 노력으로 개선할 수 있을 것으로 기대된다.
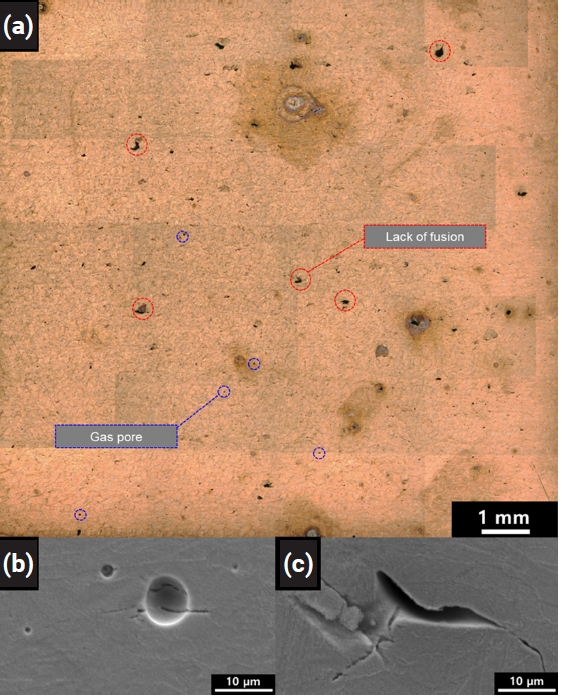
(a) Optical microscopy image of the macroscopic structure of the Cu–10Sn alloy and (b-c) scanning electron microscopy images of representative defects. (b) Gas pore and (c) lack of fusion.
전자주사현미경으로 합금의 미세조직을 더욱 자세히 관찰한 결과를 Fig. 8 에 나타내었으며, 급속응고에 의한 응고셀 구조가 확연히 관찰된다. 관찰된 응고셀의 크기는 대략 3 µm 였으며, 이와 같은 응고셀은 레이저에 의한 급속 용해 및 응고 과정에서 용질원자가 셀 벽으로 편석되며 일어난다고 알려져 있다[22]. Cu와 Sn의 합금으로 구성된 합금 조성을 고려할 때 응고중 최초 응고부인 응고셀 내부에는 Cu 분율이 상대적으로 높고, 셀 벽 부근에는 Sn 원자가 편석 되어 있을 것으로 생각된다. SEM으로 미세조직을 관찰하면서 에너지 분산 X선 분광법으로 셀 경계에 편석된 Sn을 정량 분석 시도하였으나, 본 연구에서 관찰되는 셀 벽의 두께가 매우 얇아 X선 분광법으로는 셀 벽과 응고셀 내부의 원소조성분포의 차이를 관찰할 수는 없었다.
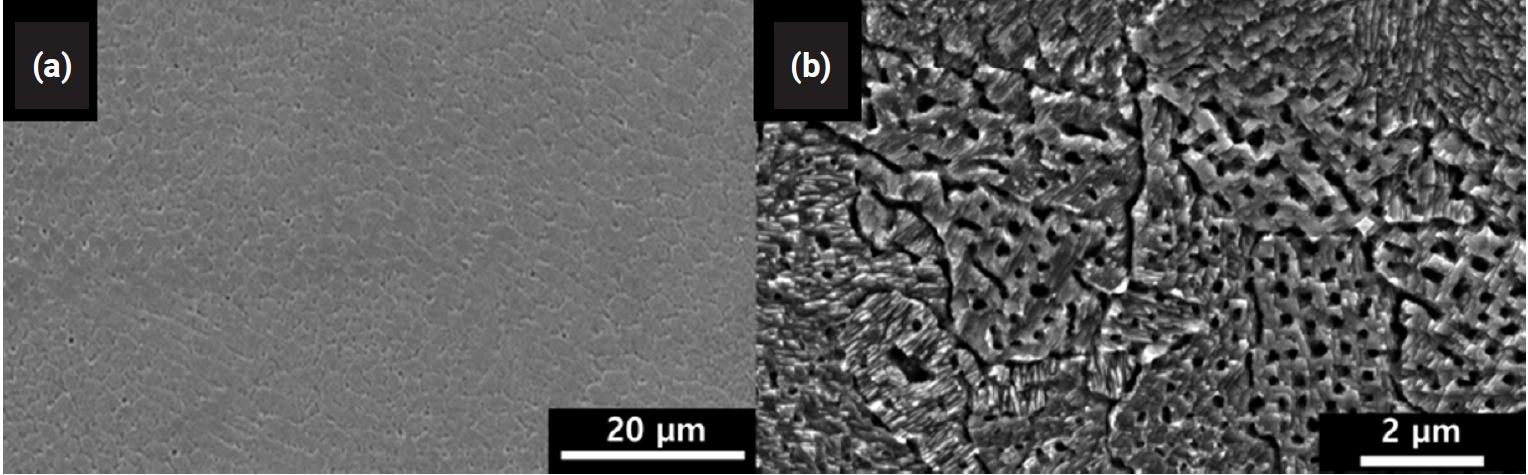
Scanning electron microscopy images of the solidification cell structure. (a) ×2,500, and (b) ×20,000.
Fig. 9 에 XRD로 분석한 Cu-10Sn합금의 상분석 결과를 나타내었다. Cu-Sn 이원계상태도의 Cu-10Sn (wt.%) 조성을 보면, 평형상태에서 최초의 응고상은 α-Cu 고용체이며, 이후 포정반응으로 β 상이 석출된 후 δ 상이 β 로부터 분리된다[23]. XRD 결과에서도 동일한 상변화의 과정으로 형성된 α-Cu 상과 δ-Cu40.5Sn11 금속간화합물 상이 존재하는 것으로 나타나며, 응고중 Sn 용질원자가 응고셀 벽 부근으로 편석된다는 점을 고려할 때 δ상은 미세하게 α 내부에 혼재되어 응고셀 벽 부근에 석출되어 있을 것으로 짐작된다. 유사한 실험을 진행한 문헌[24]을 살펴보면 δ상은 수 nm 크기로 매우 미세하게 석출되어 있을 것으로 짐작된다. 응고셀 벽의 δ상 및 편석 거동은 추후 전자투과현미경을 활용하여 추가로 분석할 계획이다.
3.3. 기계적 특성
3.2 절에서 미세조직을 상세 관찰했던, P = 350 W, v = 1,100 mm/s 의 조건으로 적층제조된 Cu-10Sn 합금의 미소경도를 측정한 결과, 적층방향과 적층 수직방향으로 각각 측정한 결과에서 경도의 이방성은 관찰되지 않았다. 미소경도값은 최소 159.2 HV부터 최대 170.0 HV로 측정되었으며, 평균 경도는 164.4 HV로 측정되었다. 기존의 Cu-10Sn 상용 주조합금의 경도는 약 80 HV로 알려져 있으며, 이를 통해 PBF 적층제조된 Cu-10Sn 합금의 경도가 동일 조성 주조재에 비해 약 2배 정도로 높은 경도값을 가지는 것을 알 수 있다. 이는 급속응고에 의해 형성되는 미세한 결정립과 응고셀 구조에 의한 강화효과 때문으로 생각된다.
동일한 적층조건으로 인장 시험편을 적층방향에 수직, 수평으로 3 방향으로 적층제조 하였다 (x, y, z 방향, Fig. 10). 적층제조된 인장시험편의 그립부 두께와 폭, gauge length의 두께와 폭을 측정한 결과를 적층제조에 사용한 STL 파일의 치수와 비교해 보니 형상오차는 0.1 mm 이하로, 인장시험이 곧바로 가능한 수준의 형상정밀도로 적층제조가 가능함을 알 수 있었다. 각 방향별 3개의 인장시험편을 제작하여 x, y 및 z 방향으로 인장시험을 수행한 결과, x 와 y 방향의 인장거동에서는 전혀 차이를 보이지 않았으며 적층방향과 수직한 방향인 z 방향으로는 다른 방향보다 다소 낮은 강도와 연신율을 보이는 이방성을 보임을 확인하였다. 이와 같은 이방성은 PBF로 제작한 소재에서 일반적으로 관찰되는 현상으로, 용융풀 내부에 비해 다소 낮은 강도와 연신율을 보이는 용융풀 경계가 적층시 층간 계면에서 연속된 형태로 분포하기 때문으로 알려져 있다[25, 26]. PBF 3D 프린팅한 샘플의 x 방향과 z 방향의 대표적인 인장곡선을 Fig. 11에 나타냈으며, 관찰된 연신율과 항복강도, 인장강도를 Table 2에 나타내었다. 앞서 언급한 것 처럼 PBF 3D 프린팅으로 제조한 Cu-10Sn 합금의 강도와 연신율은 적층 수직방향(x, y 방향) 보다 적층방향(z 방향)으로 다소 낮은 결과를 보였으나, 동일한 조성의 상용 주조재의 인장강도와 연신율이 각각 약 280 MPa, 15 % 수준임을 고려할 때 주조재보다 훨씬 높은 기계적 특성을 보이는 것을 알 수 있었다. 이와 같은 높은 기계적 특성은 PBF 공정의 급속응고 과정에서 생기는 미세한 결정립과 응고셀 구조 때문으로 생각되며, 향후 PBF 공정으로 기존의 주조재를 대체하는 복잡한 형태의 Cu-10Sn 기계부품 및 구조를 제작 가능함을 보여준다.
4. Conclusion
본 연구에서는 PBF 3차원 적층 방식을 이용하여 고출력의 레이저로 난적층소재인 Cu-10Sn 합금을 적층제조하고, 미세조직 및 기계적 물성을 분석하였다. 레이저 출력과 스캔속도를 달리한 여러 공정 조건 중 공극률이 최소가 되는 조건을 선택할 수 있었으며, 이 조건을 바탕으로 시편을 제작하고 분석하여 다음과 같은 결론을 얻을 수 있었다.
1) PBF 방식으로 적층한 Cu-10Sn 합금은 레이저 출력 350 W, 스캔속도 1,100 mm/s 일 때 이론 밀도인 8.74 g/cm3에 근접하는 높은 밀도를 가지는 것을 확인하였으며, 본 공정조건에서 내부에 기공이 거의 없이 양호한 적층재를 얻을 수 있음을 알 수 있었다.
2) 적층제조된 Cu-10Sn 합금의 단면 미세조직을 광학현미경으로 관찰한 결과, PBF 공정의 특징인 용융풀들이 겹친 형태의 미세조직을 관찰할 수 있었으며 가스결함에 의한 구형 기공과 Lack of fusion에 의한 미성형된 공극결함이 관찰되었다. Gas pore의 경우 크기와 수가 작아 기계적 특성에는 큰 영향을 미치지 않을 것으로 예상되나, Lack of fusion 결함의 경우 구리의 높은 열전도도 및 낮은 레이저 흡수율로 인해 부분적으로 발생한 것으로 보이며, 다만 그 수는 많지 않았다. 이와 같은 Lack of fusion 결함은 향후 레이저 출력을 더욱 높이거나 hatch spacing을 줄이는 등의 노력으로 개선할 수 있을 것으로 기대된다.
3) 전자주사현미경 관찰 결과, 급속응고에 의한 응고셀 구조가 관찰되었으며 크기는 약 3 ㎛으로 관찰되었다. XRD 분석 결과 α-Cu 상과 δ-Cu40.5Sn11 금속간화합물 상이 존재함을 확인하였으며, PBF 적층 중의 급속응고 과정을 고려할 때, δ-Cu40.5Sn11 상은 Sn의 편석에 의해 응고셀 벽에 미세하게 분포하고 있을 것으로 예상된다.
4) PBF 적층제조된 Cu-10Sn 합금의 경도는 164.4 HV로, 기존 동일 조성 주조재와 비교하여 2배 이상 높음을 확인하였다. 인장항복강도와 연신율은 시험편의 방향에 따른 뚜렷한 이방성을 보였으며 적층방향으로의 강도와 연신율이 적층수직방향에 비해 다소 낮았다. 적층제조된 합금의 인장강도와 연신율은 방향에 따라 차이가 있으나 동일 조성 주조재에 비해 매우 높은 수준으로 측정되었으며, 이와 같은 높은 기계적 특성은 PBF 적층과정중의 급속응고에 의한 미세한 결정립의 형성 및 응고셀의 형성 때문으로 생각된다. 이와 같은 높은 기계적 물성을 고려할 때, 향후 기존 주조법을 대체하여 고출력 레이저를 응용한 PBF 공정을 고강도의 복잡한 형태의 Cu-10Sn 합금 기계부품 및 구조체를 제조하는 데 적용할 수 있을 것으로 기대된다.
Notes
Conflict of Interest
저자들은 이해상충관련 해당사항 없음을 선언합니다.
Author Information and Contribution
김종규: (주)대건테크 주임연구원/PBF 공정설계 및 샘플제작, 기계적 특성 분석 및 논문 초안 작성
원정훈: 석사과정 학생/미세조직 분석
이욱진: 조교수/실험디자인, 논문 퇴고
Acknowledgement
이 논문은 2022년도 정부(교육과학기술부)의 재원으로 한국연구재단의 지원을 받아 연구되었음(NRF-2022R1A2C1012478).