동결건조 공정에서 Tert-butyl alcohol 기공형성제가 텅스텐 다공체의 기공구조에 미치는 영향
Effect of Tert-Butyl Alcohol Template on the Pore Structure of Porous Tungsten in Freeze Drying Process
Article information
Abstract
The effect of tert-butyl alcohol (TBA) as a freezing solvent on the pore structure of a porous tungsten body prepared by freeze-drying is analyzed. TBA slurries with a WO3 content of 10 vol% are prepared by mixing with a small amount of dispersant and binder at 30°C. The slurries are frozen at -25°C, and pores are formed in the frozen specimens by the sublimation of TBA during drying in air. After hydrogen reduction at 800°C and sintering at 1000°C, the green body of WO3 is completely converted to porous W with various pore structures. Directional pores from the center of the specimen to the outside are observed in the sintered bodies because of the columnar growth of TBA. A decrease in pore directionality and porosity is observed in the specimens prepared by long-duration drying and sintering. The change in pore structure is explained by the growth of the freezing solvent and densification.
1. 서 론
동결건조 공정은 재료 내부의 기공 양, 기공 크기 및 방 향 등을 용이하게 제어할 수 있는 장점이 있어 연료전지 및 인체 내 임플란트 지지체 등의 다공체 제조에 응용되 고 있다[1-3]. 동결건조에서 기공은 고체 분말이 첨가된 액체 동결용매를 응고시킨 후 고상화된 동결용매를 승화 시켜 제거된 자리에서 주로 형성되기 때문에 동결용매의 응고조직이 곧 기공구조를 결정하게 된다. 또한 냉각속도 및 온도 등 응고조건은 동결용매의 결정성장과 최종 미세 조직에 영향을 미치기 때문에 기공구조를 결정하는 요인 이다[4, 5].
기공구조에 중요한 영향을 미치는 동결용매는 일반적으 로 물(H2O) 또는 camphene(C10H16)이 사용되고 있다[1, 6]. 그러나 물의 경우 낮은 증기압(0.1 kPa, -20°C)과 응고 시 커다란 부피변화(11%)로 승화공정과 시편의 형상 유지에 어려움이 있다. Camphene은 상대적으로 높은 융점(47°C), 작은 부피변화(-3.1%)와 높은 증기압(0.4 kPa, 25°C)의 장 점이 있으나 다양한 기공구조의 제어에는 한계가 있다. 따 라서 기공구조 즉 응고조직 제어의 관점에서 2성분 계 동 결용매를 이용한 다공체 제조가 보고되었다. 대표적으로 camphor-naphthalene(C10H16O-C10H8) 계는 nonfaceted-faceted 상이 형성되기 때문에 아공정, 공정, 과공정 조성에서 각 각 수지상, rod상, 판상의 형태로 응고조직이 발달하여 다 양한 기공구조를 갖는 다공체로의 제조가 가능하다[7].
한편, 상온에서의 높은 증기압(6.1 kPa, 25°C)때문에 승 화가 용이한 tert-butyl alcohol(TBA)을 동결용매로 사용하 는 연구도 보고된 바 있다[8]. TBA를 이용한 동결건조로 기공의 형상과 방향성이 제어된 다공성 Al2O3의 제조가 가능함을 보여주었다[8-10]. 그러나 기존의 공정은 세라믹 다공체 제조에 한정되어 있으며, 이는 금속 계의 경우 우 수한 분산안정성을 가지는 슬러리의 제조에 어려움이 있 기 때문이다. 따라서 금속분말 대신 금속산화물 분말을 원 료로 사용하여 시편을 제조하고 수소분위기에서 환원하는 공정 등을 통하여 금속 다공체로 제조하는 연구가 일부 보고되고 있으나[11, 12], TBA를 동결용매로 사용하는 연 구는 거의 이루어지지 않고 있다.
본 연구에서는 TBA 동결용매를 이용한 동결건조 공정 으로 금속 계 다공체 제조의 가능성을 확인하고자 하였다. WO3 원료분말을 동결용매와 혼합하여 슬러리로 제조한 후 동결건조와 수소분위기에서의 열처리를 통해 W 다공 체를 제조하였다. 공정변수에 따라 다공체의 기공구조와 미세조직에 미치는 영향을 해석하여 요구되는 기공특성을 만족하는 W 계 다공체를 제조하기 위한 최적의 공정조건 을 제시하고자 하였다.
2. 실험방법
W 다공체 제조를 위한 원료로 순도 99.9%, 평균 입자 크기 1 μm의 WO3 분말(Kojundo Chemical Lab. Co.)을 사 용하였다. WO3 분말은 응집체 제거 및 미세화를 위해 직 경 5mm의 고순도 Z r O2 볼을 사용하여 에탄올 내에서 5 시간 동안 볼 밀링하였으며 볼과 분말의 무게 비는 15:1 로 하였다. 동결용매로는 Sigma-Aldrich 회사제품의 TBA (순도 99.5%)를 사용하였으며 슬러리의 분산성 향상을 위 해 0.5 wt%의 citric acid 분산제를 첨가하였다. 또한 동결 건조한 시편의 형상유지를 위해 1wt%의 polyvinyl-butyral 을 결합제로 첨가하였다.
동결건조를 위한 슬러리는 동결용매를 약 30°C로 가열 하여 액상으로 만든 후 밀링한 WO3 분말, 분산제 및 결 합제를 첨가하여 1시간 동안 혼합하여 제조하였다. 이때 WO3 분말의 첨가량은 10 vol%가 되도록 하였다. 슬러리 는 -25°C로 냉각된 에탄올에 위치한 하부의 Cu 판과 직경 10 mm의 Teflon 실린더로 구성된 금형에 부어 일방향으로 동결한 후 3시간 동안 유지하였다. 금형에서 분리한 동결 체는 -10°C 또는 -25°C에서 건조한 후, 승온 속도 3°C/min 으로 800°C까지 가열하여 1시간 동안 수소분위기에서 환 원하였고 계속해서 1000°C까지 가열하여 소결하였다.
원료 및 밀링한 분말의 입도는 레이저 입도분석기(LSI3 320, Beckman Counter, USA)를 이용하여 측정하였으며, 분산제 첨가에 따른 슬러리의 분산 안정성은 분산안정화 도 분석기(Turbiscan, France)를 이용하여 분말 및 다공체 의 상과 미세조직은 XRD(D/Max-IIIC, Rigaku Denki Co.) 와 SEM(JSM-6700F, JEOL Co.)을 이용하여 분석하였다.
3. 실험결과 및 고찰
원료분말을 5시간 동안 볼 밀링한 후 관찰한 미세조직 사진과 입도분석 결과를 그림 1에 나타내었다. 볼 밀링한 분말에서는 일부 응집체가 관찰되며, WO3 분말은 약 0.8 μm 크기의 미세분말과 약 1.5 μm의 응집분말이 혼합된 전형적인 bimodal 형태의 분포를 나타내었다. 볼 밀링한 원료분말은 TBA 동결용매와 혼합하여 슬러리로 제조되었 으며, 이때 분산 안정성을 향상시키기 위해 분산제를 첨가 하였다.
그림 2는 WO3 분말이 첨가된 TBA 슬러리의 분산안정 성의 변화를 측정한 결과이다. 그림에서 TSI(Turbiscan stability index) 값은 시간에 따른 분산안정성의 변화로 발 생하는 각각의 backscattering percent간의 면적을 적분하 여 누적시킨 것으로 동일한 시간에서 비교할 때 TSI 값이 클수록 분산안정성이 감소함을 의미한다[13]. 그림 2와 같 이 모든 슬러리는 초기에 급격한 TSI 값의 증가를 나타내 나, 유지시간이 경과함에 따라 분산제를 첨가한 경우 상대 적으로 낮은 값은 보여준다. 따라서 본 실험에서 사용한 citric acid 분산제는 TBA/WO3 슬러리의 분산안정성 향상 에 기여함을 확인할 수 있다.
그림 3은 하부 몰드가 -25°C로 냉각된 금형에서 슬러리 를 동결한 후 -10°C에서 48시간 동안 건조한 성형체를 나 타낸 사진으로 균열 발생 및 뒤틀림 현상 등이 없이 우수 한 형상 안정성을 보여주었다. TBA는 -10°C에서 약 0.08 kPa의 상대적으로 낮은 증기압과 첨가한 polyvinyl-butyral 의 결합제 역할 등이 시편의 형태 안정성에 기여한 것으 로 판단된다[10, 14].
수소분위기에서 환원 처리한 건조시편의 상 변화를 해 석하기 위해 XRD 분석을 실시하였다. 그림 4(a)와 (b)는 각각 환원처리 전후의 XRD 결과를 나타낸 것으로 환원 전에는 WO3 피크만 관찰되나 800°C에서 1시간 동안 환 원한 경우는 반응상의 형성 없이 순수한 W상에 해당하는 피크만 존재한다. 이러한 결과는 일반적인 WO3의 환원온 도가 약 700°C임을 고려할 때[15] 본 실험조건인 800°C의 수소분위기 열처리는 WO3의 완전한 환원이 가능함을 나 타낸다.
동결한 성형체를 -10°C에서 48시간 건조 후 1000°C에서 1 h 동안 소결한 경우와 -25°C에서 144시간 건조하고 1000°C에서 6시간 소결한 W 다공체의 미세구조를 각각 그림 5(a)와 (b)에 나타내었다. 그림과 같이 기공은 시편의 중심부에서 바깥쪽으로 방향성을 나타내며 형성되었고 이 는 주상(columnar) 형태로 성장한 TBA가 건조과정 중 승 화에 의해 제거되었기 때문이다[16]. 한편 그림 5(b)와 같 이 장시간의 건조 및 소결조건으로 제조한 시편에서 기공 의 방향성과 기공도가 감소함을 알 수 있다. 이는 건조과 정 중에 동결용매의 성장과 함께 장시간 소결에 따른 치 밀화에 기인한 것으로 해석된다.
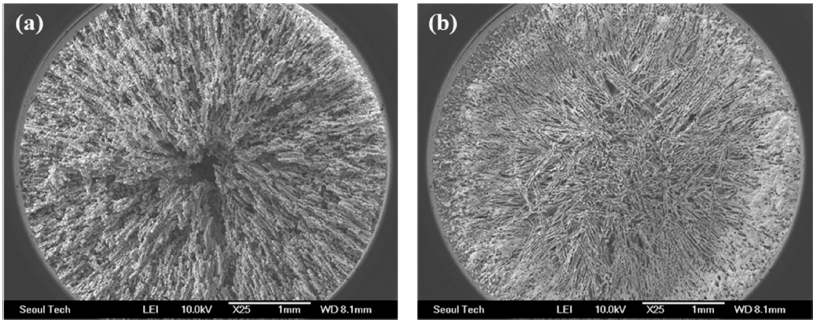
SEM micrographs of the porous W sample with different processing conditions: (a) dried at -10°C for 48 h and sintered at 1000°C for 1 h and (b) dried at -25°C for 144 h and sintered at 1000°C for 6 h.
그림 6은 소결한 다공체의 미세구조를 확대하여 관찰한 것으로, -10°C에서 48시간 건조한 시편의 경우 그림 6(a) 및 (b)와 같이 방향성 기공과 함께 조대한 구형 응집체가 결합된 미세조직을 보여준다. 이는 짧은 건조시간에 기인 하여 제거되지 않고 성형체 내에 잔존하고 있는 TBA가 소결과정 중 분말응집에 영향을 미쳤기때문으로 해석된다. 따라서 상대적으로 장시간 건조 및 소결한 시편의 경우는 그림 6(c) 및 (d)와 같이 지지체(stut)에서 응집분말은 관찰 되지 않고 치밀화된 미세조직을 나타낸다. 한편 기존의 연 구결과에 의하면[10, 17], TBA는 각 고리에 수소결합이 존재하는 육원자 고리의 결정구조를 나타내기 때문에 일 방향 응고 시 육각형의 응고결정이 형성되어 동결제 결정 이 제거된 자리에 형성되는 기공도 동일한 형상을 나타낸 다고 보고되었다. 그러나 본 연구에서는 육각형 기공 (hexagonal pore)이 관찰되지 않는 바 이는 슬러리의 일방 향 응고 등 동결조건이 상이했기 때문으로 해석된다.
4. 결 론
본 연구에서는 동결건조 공정으로 제조한 W 다공체의 기공구조에 미치는 TBA 동결용매의 영향을 분석하였다. WO3 분말이 혼합된 TBA 슬러리의 Turbiscan 분석을 통 해 citric acid 분산제가 첨가된 경우에서 우수한 분산안정 성을 나타냄을 확인하였다. TBA 슬러리는 하부가 -25°C 로 냉각된 금형에서 동결하였으며 공기 중에서 승화과정 으로 동결용매를 제거하여 형태 안정성을 갖는 성형체로 제조하였다. XRD 분석을 통하여 800°C, 수소분위기에서 환원한 동결건조 시편은 순수한 W 상으로만 존재함을 확 인하였다. 1000°C에서 소결한 다공체는 주상 형태로 성장 한 TBA때문에 시편의 중심부에서 바깥쪽으로 방향성을 갖는 기공이 관찰되었다. 장시간의 건조 및 소결조건으로 제조한 시편에서 기공의 방향성과 기공도의 감소가 관찰 되었으며 이는 건조과정 중에 동결용매의 성장과 함께 장 시간 소결에 따른 치밀화에 기인한 것으로 해석하였다. 따 라서 TBA 동결용매를 이용한 동결건조 공정조건의 제어 로 다양한 기공 특성을 갖는 W 다공체 제조가 가능함을 확인할 수 있었다.
감사의 글
이 논문은 2021년도 정부(과학기술정보통신부)의 재원 으로 한국연구재단의 지원을 받아 수행된 연구임(No. 2019R1A2B5B01070587).