폐초경 스크랩 코발트 침출용액으로부터 옥살산 및 수산화물 침전에 의한 코발트 분말 회수
Cobalt Recovery by Oxalic Acid and Hydroxide Precipitation from Waste Cemented Carbide Scrap Cobalt Leaching Solution
Article information
Abstract
Cobalt (Co) is mainly used to prepare cathode materials for lithium-ion batteries (LIBs) and binder metals for WC-Co hard metals. Developing an effective method for recovering Co from WC-Co waste sludge is of immense significance. In this study, Co is extracted from waste cemented carbide soft scrap via mechanochemical milling. The leaching ratio of Co reaches approximately 93%, and the leached solution, from which impurities except nickel are removed by pH titration, exhibits a purity of approximately 97%. The titrated aqueous Co salts are precipitated using oxalic acid and hydroxide precipitation, and the effects of the precipitating agent (oxalic acid and hydroxide) on the cobalt microstructure are investigated. It is confirmed that the type of Co compound and the crystal growth direction change according to the precipitation method, both of which affect the microstructure of the cobalt powders. This novel mechanochemical process is of significant importance for the recovery of Co from waste WC-Co hard metal. The recycled Co can be applied as a cemented carbide binder or a cathode material for lithium secondary batteries.
1. 서 론
코발트는 강자성을 띠는 은회색 금속으로 주로 자석, 염 료, 이차전지 및 공구용 초경합금, 고성능 합금원소 등에 사용된다. 최근 친환경 에너지에 대한 관심이 높아지고 산 업이 발달함에 따라 인공지능, 전기차 및 우주항공산업 분 야에서 이차전지, 첨단 공구소재의 수요가 늘어나고 그에 따라 코발트의 수요가 크게 증가하고 있다. 하지만 코발트 는 지구의 지각에 약 0.0025%만 존재하고 매장량의 대부 분이 특정 국가에 편중되어 있다[1]. 이와 같은 코발트의 공급 부족 문제를 해결하기 위해 이차전지 분야에서는 하 이-니켈(High-Ni), NMC(lithium nickel manganese cobalt oxide), LFP(lithium iron phosphate carbon) 등 코발트 저 감형 양극재의 재료를 개발하고 있으며, 초경 합금의 경우 코발트 대신 니켈이나 철 또는 금속간 화합물 FeAl을 코 발트 대체용 바인더 소재로 하여 다방면의 연구가 진행되 고 있지만 코발트의 성능을 대체하기엔 한계가 있다[2]. 따라서 제한된 유한한 자원을 효율적으로 사용하기 위해 폐리튬이온전지 및 폐초경합금 등 폐기된 소재 및 부품에 서 코발트를 회수하려는 다양한 연구가 진행중에 있다. 그 중 폐초경합금 재활용 공정의 경우 아연 공정(zinc process), 고온 산화공정(High-temperature oxidation process), 전기 용해 공정(electro-dissolution process) 등이 상용화 또는 연구개발 중에 있다. 아연 공정이란 폐초경합금을 아 연용탕에 넣어 코발트와 탄화 텅스텐으로 분리하는 공정 이다. 하지만 코발트는 고온 열처리 과정에서 휘발되어 회 수율 낮고 입도 제어가 어렵고 불순물 함량이 높아 재사 용하기에 부적합하다. 고온 산화 공정은 폐 초경 분말을 고온의 열을 가해 탄화 텅스텐과 코발트를 산화시킨 후 볼밀링과 침출 공정을 통해 텅스텐과 코발트를 회수한다. 하지만 산화 공정시 많은 시간과 에너지가 발생하고 환원 공정 및 탄화 공정 등 추가적인 공정이 필수적이다[3-5]. 전기 용해 공정은 폐 초경 분말 내 코발트를 직접 회수하 여 초경 합금 재활용 공정 중 대표적으로 사용하는 공정 이지만 공정 시간이 길고 환경 부담이 크다[6, 7]. 이처럼 현재 다양한 방법으로 폐초경 합금을 재활용하는 공정이 개발되어 왔으나, 가공공정에서 발생하는 폐초경 슬러지 의 경우 유의미한 재활용 공정이 개발되어 있지 않아 전 량 폐기되고 있는 실정이다.
따라서 이번 연구에서는 폐초경합금 슬러지 분말을 기 계화학적 볼밀링을 통해 탄화 텅스텐 분말과 코발트 염으 로 분리한 후, 분리된 코발트 염을 pH 적정을 통해 분술 물을 제거하였다. 기존의 폐초경 슬러지 분리∙침출 공정은 대부분 고온의 산화배소 후 코발트 침출을 진행하기 때문 에 코발트가 산화되어 코발트의 산침출 효율이 낮아 이를 향상시키기 위해 추가적인 환원제 등을 사용하는 경우가 많으나, 본 공정에서는 탄화 텅스텐을 고상으로 분리하면 서 코발트를 금속상태에서 침출하기 때문에 침출방법이 간단하고 효율적인 장점이 있다. 이후 용해도가 낮은 침전 물 형성을 통해 선택적으로 금속 성분의 침전∙분리가 가능 하여 효과적인 회수가 가능한 옥살산 및 수산화물 침전 공정에 따른 코발트 화합물 및 금속 코발트 분말의 미세 조직 및 상변화를 비교 분석하였다.
2. 실험방법
본 연구에서는 초경합금 가공공정에서 발생하는 초경합 금 슬러지 분말(Wolfram Tech)을 원료 분말로 사용하였다. 초기 분말의 조성 및 함량은 Table 1에 나타냈다. 초경합 금 슬러지 분말은 절삭유 및 불순물을 제거하기 위해 증 류수로 세척 후, 0.5 M 황산(H2SO4, Junsei, 95%) 수용액 으로 습식 볼밀링하여 탄화 텅스텐(WC) 분말과 절삭과정 에서 생성된 금속 불순물이 포함된 황산 코발트 수용액으 로 분리하였다. 볼밀링은 유성형 볼밀(Pulverisette 5; Fritsch GmbH)을 사용하였고, 500 mL 용량의 초경 jar에 텅스텐 카바이드 볼(직경: 6 mm)과 슬러지 분말을 5:1 무 게비로 넣고 초경 jar 부피의 40%만큼 황산 수용액을 투 입하여 두 시간 동안 300 rpm으로 진행했다. 슬러지 분말 내 코발트를 포함한 잔류 금속 불순물을 최대한 침출하기 위해 위 과정을 세 번 반복하여 진행했다. 볼밀링 후 진공 여과를 통해 분말과 황산 코발트 수용액으로 분리하였다.
이후 pH 적정법을 통해 황산 코발트 내 금속 불순물을 제 거하였다. pH적정법은 포베 다이어그램(Pourbaix diagram) 을 기반으로 황산 코발트 수용액 내 텅스텐, 철 및 알루미 늄 등의 불순물들을 제거하기 위해 수산화나트륨(NaOH, 98.0%; Samchun Chemicals)을 사용하여 pH를 9까지 적정 후 진공 여과를 통해 침전물을 제거하였다. 불순물이 제거 된 황산 코발트 수용액은 두 가지 방법을 통해 코발트 금속 화를 진행하였다. 첫 번째 방법은 수산화나트륨 용액을 이 용해 pH를 11까지 적정한 후 한 시간 동안 격렬하게 교반 하여 수산화 코발트(Co(OH)2)를 침전시킨 후 진공여과 및 건조를 통해 Co(OH)2, 분말을 수득하였다. 두 번째 방법은 4M 옥살산(HO2CCO2H, ≥ 99.0%, Sigma-Aldrich)과 황산 코 발트 수용액을 30분 간 교반하여 황산 코발트(CoSO4)를 코 발트 옥살레이트(CoC2O4·H2O)로 반응시킨 후 진공여과 및 건조를 진행하였다. 이어서 코발트 옥살레이트를 대기분위 기에서 500°C로 두 시간동안 유지하여 산화 코발트(Co3O4) 로 제조하였다. 상기 두 가지 방법으로 제조된 수산화 코 발트와 산화 코발트 모두 수소분위기 하에서 800°C로 두 시간 동안 열처리하여 환원된 코발트 분말을 제조하였다.
pH 적정은 pH 미터기(FIVEeasy Plus; Mettler Toledo)를 이용해 진행하였다. 분말의 상분석은 X-선 회절분석기(Xray Diffractometer, X’pert PRO MRD, PANAlytical)을 이 용해 진행하였고, 접속이온빔장치(Focused Ion Beam, Crossbeam 540, Zeiss)를 이용하여 분말의 미세조직 및 입 도 크기를 분석하였다. 분말의 화학 조성은 유도결합 플라 즈마 분광광도계(ICP-OES; Optima 7300DV; LabX)를 이 용하여 분석하였다.
3. 결과 및 고찰
Fig. 1(a)는 습식 볼밀링 전과 후 분말의 XRD 결과를 보 여주고 있다. 습식 볼밀링 전 슬러지 분말에서는 탄화 텅 스텐, 다이아몬드 및 코발트 상이 관찰되었으며, Table 1 의 ICP 결과와는 다르게 불순물 금속 피크가 검출되지 않 았는데, 이는 불순물 금속 원소들의 함량이 5% 이하로 매 우 미량이기 때문에 X-선 회절패턴에서 검출되지 않은 것 으로 보인다. 습식 볼밀링 후 X-선 회절패턴에서는 탄화 텅스텐 피크만 존재하는 것을 확인했으며, 이는 수 차례 볼밀링을 통해 슬러지 분말에 포함되어 있는 코발트와 잔 류 불순물들이 황산 수용액으로 침출되었기 때문이다. ICP 분석결과를 통해 탄화 텅스텐 나노분말의 순도는 98.4%로 나타났으며, 코발트 및 기타 금속 불순물들은 침 출용액에 존재하는 것을 확인할 수 있으며 Co의 침출효율 은 약 93%로 계산되었다(Table 2). 이때 코발트 염이 황산 과 반응하여 침출되는 반응은 다음과 같다.
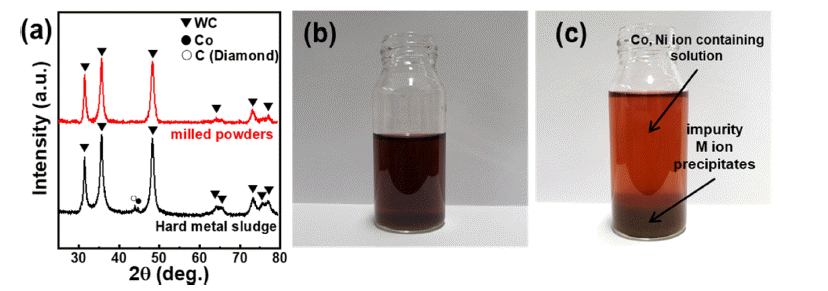
(a) XRD patterns of WC-Co hard metal sludge and mechanochemically milled powders. Digital images of (b) as-leached solution and (c) titrated solution to pH 9.
황산으로 습식 볼밀링 후 진공여과를 통해 분리된 황산 수용액은 코발트 이온이 주로 침출되어 있어, Fig. 1(b)에 서 보이듯이 보라색을 띄고 있는 것을 확인할 수 있다. 습 식 볼밀링 공정을 통해 침출된 침출용액은 주로 코발트 이온을 함유하고 있으나, 이외에도 텅스텐, 철, 알루미늄, 니켈 등 절삭공정에서 포함되는 불순물 금속을 포함하고 있다. 포베 다이어그램에 따르면, 텅스텐, 철, 알루미늄과 같은 불순물은 pH 9이내에서 수산화물 상태로 침전되므 로(Fig. 1(c)), pH 9까지 1차 적정 후 진공여과를 하여 불 순물을 제거하였다. 적정 후 황산 수용액에서 니켈의 함량 이 2.94%로 불순물 중 제일 높게 나타났는데(Table 2), 이 는 코발트와 니켈은 물리적, 화학적 성질이 비슷하고, 포 베 다이어그램에서 수산화 화합물로 상변화되는 영역이 겹치기 때문이다[8, 9]. 추가적으로 Cyanex 272와 같은 추 출용제를 사용한 용매추출법을 통해 Co와 Ni을 분리하여 Co의 순도를 향상시킬 수 있다.
1차 적정 후 진공여과를 하여 침전물을 제거한 코발트 함유 황산 수용액에서 수산화물 침전 및 옥살산에 의한 코발트 분말 회수를 진행하였다. 수산화물 침전은 용액을 pH 11까지 적정하여 황산 코발트를 수산화 코발트로 석출 시키는 것으로, 석출되는 반응은 다음과 같다.
Fig. 2(a) XRD 결과에서 확인할 수 있듯이 pH 11까지 2 차 적정 후 수득한 분말은 Co (OH)2를 제외한 다른 피크는 나타나지 않았으며, 수소 열처리를 통해 환원한 분말의 경 우에도 코발트 피크만 존재하는 것을 확인할 수 있다. Fig. 2(b)는 C o (OH)2 나노분말의 사진 및 SEM 미세조직을 나 타낸 그림으로, Co(OH)2 나노분말은 갈색을 띄며 미세조 직 관찰결과 rhombohedral 구조를 가진 판상 형태가 응집 되어 꽃 형상(flower-like)을 보이는 것을 확인할 수 있다 [10]. Fig. 2(c)의 C o 분말 미세조직 분석을 통해, 판상 형 태가 응집된 Co (OH)2 나노분말이 환원되며 대략 200~400 nm의 입도를 가진 코발트 나노분말이 생성되었음을 확인 할 수 있다.
옥살산을 통한 코발트 분말 회수 방법은 용매 추출을 통 해 니켈을 제거한 황산 코발트 수용액을 옥살산과 반응시 켜 코발트 옥살레이트로 침전시켜 수득하였으며, 이때 황 산 코발트가 코발트 옥살레이트로 상변화되는 반응은 다 음과 같다.
코발트 옥살레이트는 300°C 이상에서 Co3O4로 상변화 가 일어나며, Fig. 3(a)의 XRD 결과를 통해 열처리 후 코 발트 옥살레이트가 Co3O4로 상변화 한 것을 확인하였다 [11]. 이후 Co3O4의 수소 열처리를 통해 환원된 분말의 XRD 측정 결과 코발트 피크 이외의 다른 피크는 나타나 지 않은 것을 확인할 수 있다. 코발트 옥살레이트의 미세 조직 관찰 결과 매끈한 표면과 침상형태를 띄고 있는 것 을 확인할 수 있다. 이는 코발트 옥살레이트는 인접 분자 내 수소 결합과 π-π 상호작용에 인해 평행 방향으로는 성 장이 지연되고, 면에 수직인 방향, 즉 (001) 방향으로 성장 하기 때문이다[12-14]. 또한 코발트 옥살레이트의 열처리 를 통해 제조된 Co3O4의 경우도 옥살레이트와 비슷하게 표면이 매우 거칠고 길이가 대략 4–10 μm 정도인 침상 모 양을 보이고 있다(Fig 3(c)). Co3O4에서 환원된 C o 분말의 미세조직의 경우 침상형태의 Co3O4가 환원되며 나뭇가지 모양의 미세조직을 보여, 수산화물 침전을 통해 제조된 Co 나노분말의 미세조직과 차이가 있는 것을 확인할 수 있다(Fig. 3(d)). 두 공정으로 제조된 코발트는 대략 90% 의 회수율을 보였다.
4. 결 론
본 연구에서는 기계화학적 볼밀링을 통해 폐초경 슬러 지 분말에서 코발트를 포함한 금속 이온을 침출한 후 pH 적정을 통한 금속 불순물을 제거 및 옥살산 및 수산화물 침전을 통해 코발트 금속 분말을 회수하고 제조방법에 따 른 미세조직 변화를 분석하였다. 수산화물 침전법으로 제 조된 Co(OH)2 나노분말은 rhombohedral 결정구조로 인해 판상형태가 응집된 꽃 형상(flower-like) 미세조직을 보였 고, 옥살산 침전을 통해 제조된 코발트 옥살레이트는 인접 분자 내 수소 결합과 π-π 상호작용에 (001) 방향으로 성장 하여 침상형태의 미세조직을 보이는 것을 확인하였다. 환 원된 코발트 분말의 미세조직은 환원 전 코발트 산화물의 형상에 크게 좌우되는 것을 확인하였다. 제조된 코발트 분 말은 니켈이 포함되어 있어 약 97%의 순도를 보이고 있 으나, 니켈 역시 초경합금에서 바인더 역할을 하기 때문에 초경합금을 제조하거나, high-Ni 이차전지 양극활물질 제 조를 위한 전구체로 활용이 가능할 것으로 기대된다. 또한 코발트 분말의 독특한 미세구조를 통해 촉매나 자성재료 로 응용이 가능할 것으로 기대된다.
감사의 글
이 논문은 2020년도 정부(산업통상자원부)의 재원으로 한국산업기술평가관리원의 지원(20011520, 스크랩을 활용 한 정밀가공용 100 nm급 텅스텐계 소재 및 공구제조기술 개발)과 2021년도 정부(산업통상자원부)의 재원으로 한국 에너지기술평가원의 지원을 받아 수행된 연구임(2021 7510100020, 저품위 공정 폐액으로부터 희소금속 회수 공 통 핵심(농축, 분리회수)공정 플랫폼 구축 및 소재화 기술 개발).