펄스전류활성소결법을 이용한 스퍼터링 타겟용 Cu-Mn 소결체 제조 및 특성평가
Fabrication and Property Evaluation of Cu-Mn Compacts for Sputtering Target Application by a Pulsed Current Activated Sintering Method
Article information
Abstract
Cu-Mn compacts are fabricated by the pulsed current activated sintering method (PCAS) for sputtering target application. For fabricating the compacts, optimized sintering conditions such as the temperature, pulse ratio, pressure, and heating rate are controlled during the sintering process. The final sintering temperature and heating rate required to fabricate the target materials having high density are 700°C and 80°C/min, respectively. The heating directly progresses up to 700°C with a 3 min holding time. The sputtering target materials having high relative density of 100% are fabricated by employing a uniaxial pressure of 60 MPa and a sintering temperature of 700°C without any significant change in the grain size. Also, the shrinkage displacement of the Cu-Mn target materials considerably increases with an increase in the pressure at sintering temperatures up to 700°C.
1. 서 론
스퍼터 타겟은 스퍼터링 공정을 통해 박막화 시킨 후 식 각을 통해 배선을 형성시킨다. 이러한 금속 배선은 극미세 패턴으로 형성된 소자내부에서 전기적 신호를 전달하는 통로로써 디바이스의 수율 및 신뢰성을 좌우하는 핵심 소 재이다. 이와 같은 배선용 스퍼터 타겟의 소재로는 Al, Cu, Al 합금 및 Cu 합금 소재가 있다. 범용 디바이스에서 주로 Al 타겟 및 Al 합금타겟이 사용되어 왔으나, 최근 디 바이스의 고집적화가 진행됨에 따라 Al 소재보다 낮은 비 저항을 가지는 Cu 및 Cu계 스퍼터 타겟의 수요가 증가하 고 있는 추세이다.
최근 타겟 소재의 고기능화를 위한 연구개발이 진행되 어지고 있다. 금속타겟의 제조기술은 제조방법에 따라 크 게 용해/주조법과 분말야금법으로 구분이 가능하다. 그 중 용해/주조법은 금속타겟을 제조하기 위한 가장 일반적인 방법으로써 대량 생산이 용이하여 제조단가를 낮출 수 있 는 장점을 가지고 있다. 하지만 주조결함, 결정립 제어, 고 밀도, 미세조직 제어 및 균일물성의 한계가 있어 압연 및 열처리 공정 등의 후처리 다단계 공정이 요구되어 지고 있다. 반면, 분말야금 기술의 경우 균질한 상 분포와 미세 한 결정립 제어, 고순도화 및 고융점 소재 제조가 용이하 다. 조성 및 성분비의 설계 자유도 범위가 커서 고성능, 고 기능성 타겟을 제조할 수 있는 장점이 있어 최근 용해/주 조법의 대체 공정으로 활발히 적용되고 있다[1].
종래의 분말야금법 중 스퍼터 타겟제조 방법으로 널리 사용되고 있는 방법으로는 온도와 압력을 동시에 가하여 비교적 고밀도 소결체를 얻을 수 있는 열간등압소결(Hot Isostatic Pressing)과 열간가압소결(Hot Pressing)방법이 주 로 사용되어 왔다. 두 소결공정 모두 장시간 성형공정으로 인한 결정립제어의 한계, 외부 간접가열방식에 의한 소결 체 내·외부 물성편차, 값비싼 공정 단가 등의 이유와 IT 산업의 급격한 발전에 따른 고성능 고효율의 스퍼터 타겟 소재가 요구되고 있어 새로운 공정기술 개발이 요구되고 있다.
최근 단일공정으로 단시간에 치밀화를 할 수 있는 펄스 전류활성 소결법은 기존의 연소법과 열간 가압기술(Hotpress, HIP)을 결합한 방식이다. 펄스 직류전류를 이용하여 소결하고자 하는 분말에 직접 직류전류를 인가하여 분말 주위에 발생하는 줄열을 이용한 가압 소결법으로 짧은 시 간에 치밀한 생성물을 얻을 수 있는 방법이다[2-4].
본 연구에서는 치밀한 Cu-Mn 스퍼터 타겟재료를 직류 전류와 높은 소결압력을 인가 할 수 있는 펄스전류활성 소결장치로 12분 이내의 짧은 시간에 제조하였다. 제조된 소결체의 수축변위, 밀도, 순도, 상분석 및 미세조직등을 분석하였다. 또한 제조된 스퍼터 타겟 및 상용타겟을 인라 인 스퍼터 장비에 장착하여 실제 Cu-Mn 박막을 제조하였 으며, 제조된 두 가지 박막에 대한 물성을 비교하였다.
2. 실험 방법
본 실험에 사용된 원료 분말은 가스아토마이저 공정으 로 Cu-Mn 합금분말을 제조하였다. 원료 잉곳은 Cu(RND Korea co., 순도 99.999%) 및 Mn(RND Korea co., 순도 99.999%)으로 비율은 99:1 중량비로 하였다. 가스아토마 이저 공정은 직경 4 mmØ 크기의 오리피스를 이용하여 분말을 제조하였다. 공정조건은 용융온도 1200°C, 용융 유 지시간 30분, 진공도 8 × 10−3 torr 및 12 bar의 가스 압력 으로 Ar 가스를 분사하며, Cu-Mn 합금분말을 제조하였다.
그림 1은 가스아토마이저 공정으로 제조된 Cu-Mn 합금 분말의 미세조직 분석 결과이다. 미세조직 분석결과 그림 1(a)와 같이 구형의 형상을 주로 띄었으나, 부분적으 로 구형이 아닌 불규칙한 형상 및 원통형 분말도 관찰되 었다. EDAX 성분 분석결과 초기 조성비와 유사한 조성 (Cu:Mn = 98.93:1.17 wt.%)으로 분석되었다. 그림 2(b)는 제조된 Cu-Mn 합금분말을 투과전자현미경(Trasnmission electron microscope, TEM)으로 미세조직 분석결과이다. 분석결과 분말의 내부보다는 외각 부분에 최대 6배 이상 높은 함량으로 산소가 존재하는 것으로 분석되었다. 이는 제조된 원료분말의 산화에 의한 표면 우선산화로 판단된 다. Cu와 Mn은 그림 1(c)의 TEM-Mapping 결과와 같이 하나의 분말 안에 고르게 분포되어 있는 것으로 분석되 었다.
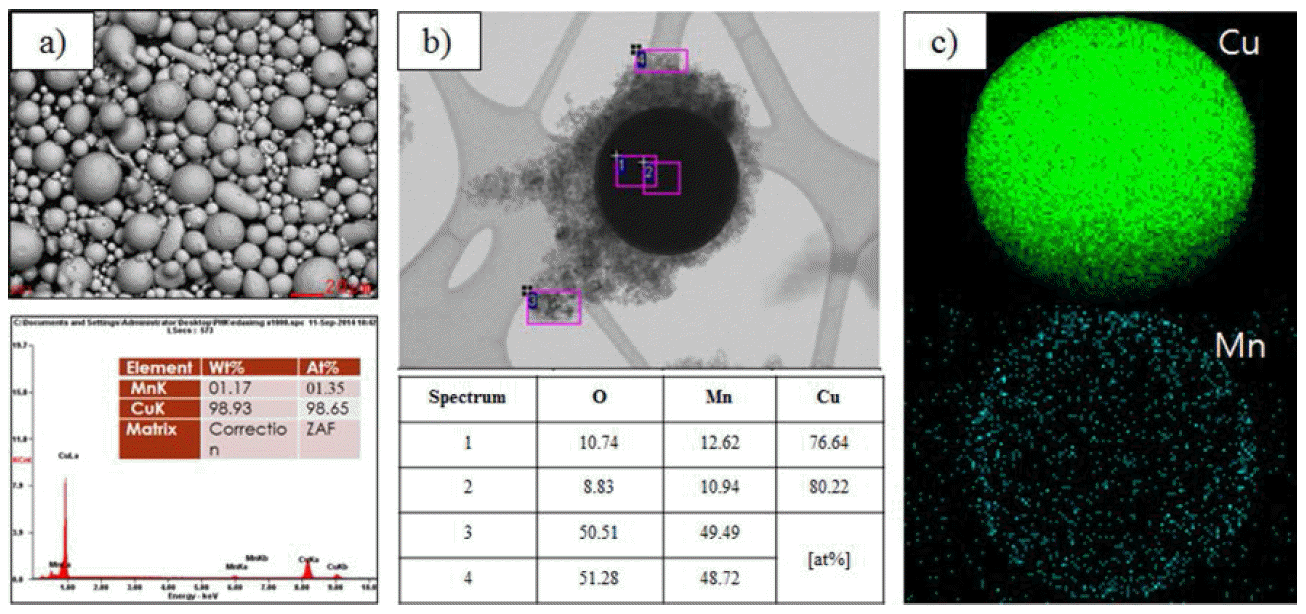
Analysis results of Cu-Mn alloy powder: (a) Microstructure, (b) EDAX, (c) TEM image, and (d) EDS mapping.
입도분석장치(Malvern, mastersizer 2000E)를 이용하여 소결에 사용될 Cu-Mn 합금분말의 입도 분석결과 평균 20.56 μm(D 0.1:11.25 μm, D 0.5:20.56 μm, D 0.9:33.96 μm) 크기로 분포되어 있는 것으로 분석되었다. 또한 ICP (Induction couple plasma) 순도 분석결과 초기 99.999%의 잉곳에서 99.992%의 순도를 가지는 원료분말로 분석되었 다. 이는 가스아토마이저 공정 중 불순물 혼입에 의해 순 도가 낮아진 것으로 판단된다.
그림 2는 원료분말의 X선 회절분석을 이용한 상분석 결 과이다. 상분석 결과 Cu 단일상만 분석되었다. 순수 Cu 피크와 비교시 격자상수의 증가(3.616Å에서 3.622Å)된 결 과를 보였으며, 이는 고용한도 이내로 첨가된 Mn으로 인 해 전율고용체 형태로 존재하기 때문에 Cu 피크만 분석된 것으로 사료된다.
제조된 Cu-Mn 합금분말의 소결을 위해 그라파이트 몰 드에 합금분말을 충진 후 상하부를 그라파이트 펀치로 막 아주었으며, 밀봉된 그라파이트 몰드 셋트를 펄스전류활 성 소결장치에 장착 시켰다. 그림 3에 펄스전류활성 소결 장치의 개략도를 나타내었다. 참고로 펄스전류활성 소결 장치는 최대 30,000 A의 직류 전류를 사용할 수 있으며 (puls 12 ms on time and 2 ms off time), 최대 300 ton의 압력을 인가할 수 있다. 실험 순서로는 1단계에서 챔버 내 에 제조된 Cu-Mn 합금분말이 충진된 그라파이트 몰드 셋 트를 장입한 후 6 × 10−3 Pa의 진공상태로 챔버 내부를 형 성하였다. 초기 원할한 가스 배출을 위해 최소 소결압력인 10 MPa만 인가하였으며, 2단계로는 그라파이트 펀치에 직류 전류를 흘려주어 소결을 진행하였다. 이때 수축길이 의 변화를 관찰하며, 실험을 종료하였다. 온도의 변화를 확인하기 위하여 K 타입의 열전대를 하부 펀치 중앙 및 외각(시편의 5 mm 부근)에 삽입하여 시편의 내외부 온도 를 측정하였다. 이때 승온속도 80°C/min으로 약 9분간 가 열하였으며, 목적온도인 700°C에 도달 시 3분간 등온 유 지 후 장비의 전원을 off 시킨 다음 챔버 내에서 냉각 시 키는 것으로 소결 진행을 마무리 하였다. 그림 4에 소결이 진행되는 4단계를 나타내었다.
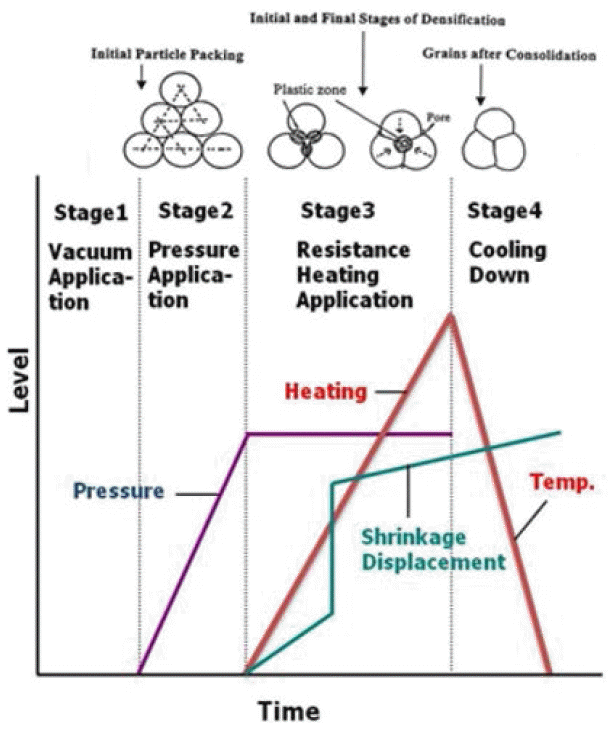
Schematic representation of the temperature, pressure and shrinkage displacement SPS of Cu sintered-body for different sintering pressure.
소결된 시편의 밀도는 아르키메데스 방법으로 밀도를 측정하였으며, ICP 분석을 이용하여 순도 분석을 진행하 였다. 또한 각 온도 구간에서 제조된 소결체의 파단면을 주사 전자 현미경을 이용하여 파단면을 관찰하였으며, 소 결체의 미세조직 관찰을 위해 증류수와 Nitric acd용액을 50 대 50 비율로 하여 약 1분 동안 전해연마 하였다. 또한 소결 후의 상변화 관찰을 위하여 X선 회절 분석을 실시하 였다.
최적공정에 의해 제조된 소결체는 그라인딩 머신을 이 용한 표면 연마 후 인라인 스퍼터 장비를 이용하여 박막 증착을 하였다. 제조된 박막의 미세조직 및 4 point probe 를 이용한 비저항 측정을 실시하였다.
3. 결과 및 고찰
Cu-Mn 합금분말을 이용하여 펄스전류활성 소결시 소결 시간에 따른 소결온도 및 수축길이 변화그래프를 그림 5 에 나타내었다. 초기 가스 배출을 원활하게 하기 위하여 소결압력은 520°C까지 기본 압력(10 MPa)로 진행하였다. 520°C 이후 소결압력을 10 MPa에서 60 MPa로 증가하며, 목 적온도인 700°C까지 승온속도 80°C/min으로 승온 후 700°C에서 3분간 등온유지 하였다. 그림 5의 수축길이 변 화 그래프와 같이 520°C 이전에는 수축보다는 팽창 현상 만 발생하였으며, 소결압력 10 MPa를 제외한 20 MPa 부 터의 압력에서는 팽창보다는 수축현상만이 관찰되었다. 소결압력이 증가할수록 최대 약 1.4 mm까지 수축되는 현 상이 발생하였다. 등온유지 시간동안 수축은 지속적으로 발생하였으며, 최종 3분에서는 수축이 더 이상 발생하지 않았다.
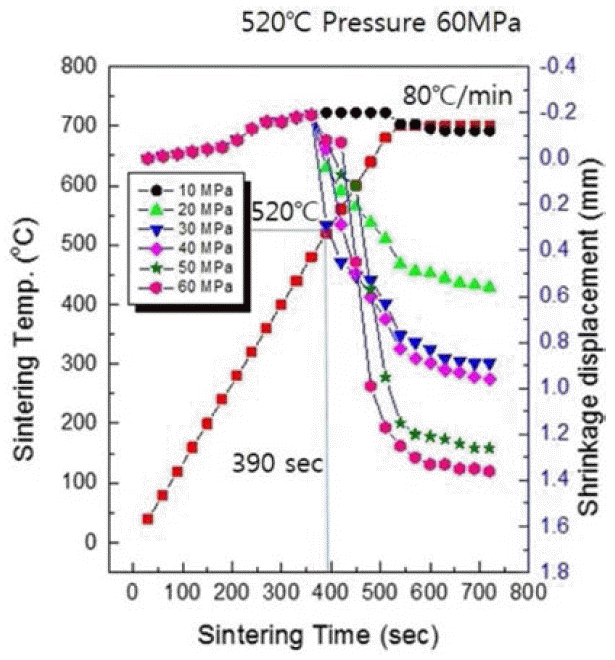
Variations of temperature and shrinkage displacement with sintering time during SPS of Cu-Mn sintered-body for different sintering pressure.
그림 6은 그림 5의 수축길이 변화 그래프의 데이터 값 과 초기분말의 압축된 두께 및 최종 소결체의 상대밀도를 이용하여 소결이 진행되는 동안 밀도 변화가 어떻게 진행 되는지를 유추하였으며, 다음과 같은 식을 이용하여 밀도 변화 값을 나타내었다.
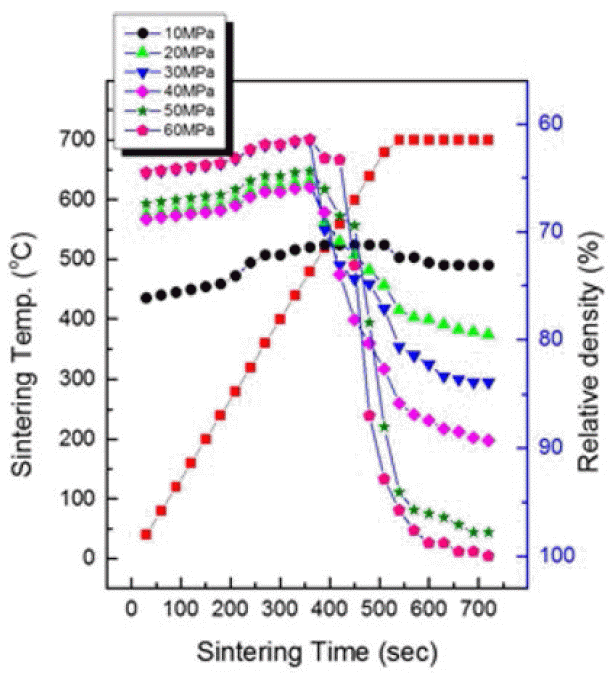
Variations of temperature and relative density with sintering time during SPS of Cu-Mn sintered-body for different sintering pressure.
여기서 DT는 초기 분말 충진상태의 상대밀도, Lf는 최종 소결체의 두께, LT는 초기 두께 및 Df는 최종 소결체의 상 대밀도이다[5]. 10 MPa에서 60 MPa의 압력 증가에 따라 제조된 소결체의 상대밀도는 각각 73.1, 79.5, 83.9, 89.3, 97.8 및 100%로 측정되었다. 소결압력이 증가할수록 치밀 화 속도 및 상대밀도는 증가하였다.
소결압력이 증가할수록 치밀화 속도가 빠른 이유는 다 음과 같이 생각된다. 첫 번째는 펄스전류에 의해 분말과 분말 접촉점에서 높은 줄(Joule) 열 발생으로 고온이 되므 로 원자의 확산이 빠르고, 분말과 분말 사이에 플라즈마 발생으로 분말표면이 이온화된 가스와 출돌로 분말 표면 정화가 일어나고, 또한 전기장 하에서 원자의 확산이 빠르 기 때문에 낮은 온도에서도 빠른 시간 내에 소결이 쉽게 이루어지기 때문으로 생각된다[6-9]. 두 번째는 소결 중 가한 압력은 소결에 대한 구동력을 증가시키며, 압력이나 충격에너지가 커짐에 따라 밀도가 증가한 후 일정한 포화 치에 도달된다. 물질의 소성변형은 항복응력 이상에서 발 생되므로 치밀한 생성물을 얻기 위해서는 일정 임계치 이 상의 압력을 인가해야 되며, 소결에 대한 전체 구동력 FD 는 다음과 같은 식으로 표현된다.
여기서 γ는 계면에너지, Pa는 인가압력, r은 입자의 반경이 다. 전북대학교 손인진 교수 연구팀은 안정화 지르코니아 를 고주파유도 가열 소결 중 상대 밀도에 미치는 압력 영 향을 조사 연구하였다[10]. 1000°C에서 소결하는 도중에 상대밀도는 60 MPa에서 100 MPa로 증가함에 따라 상대 밀도는 현저히 증가하였다.
그림 7은 소결온도 700°C에서 압력 변화에 따라 제조된 Cu-Mn 소결체의 X선 회절분석 결과이다. 압력변화에 따 라 제조된 소결체는 모두 Cu 단일상만 분석되었다. 초기 원료 분말의 X선 회절분석과 동일하게 Mn은 고용한도 이 내로 첨가되어 전율고용체로 존재하는 것으로 판단된다. 가스불순물의 혼입으로 인한 Cu2O 또는 MnO 같은 제 2 차상은 관찰되지 않았으며, 이는 고진공 하에서의 공정 및 단시간의 소결시간에 기인한 결과이다. X선 회절 분석 데 이터를 이용하여 소결체의 결정립 크기를 분석하였으며, 이때 다음과 같은 Suryanarayana and Grant Norton식을 이 용하여 구하였다[11].
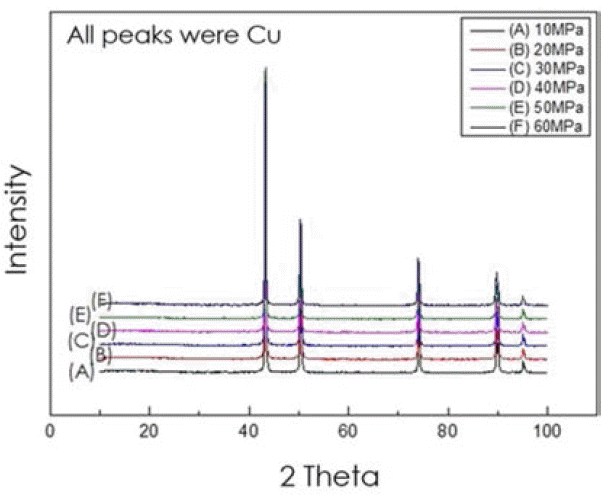
XRD patterns of Cu sintered-body for different sintering pressure: (a) 10 MPa, (b) 20 MPa, (c) 30 MPa, (d) 40 MPa, (e) 50 MPa, and (f) 60 MPa.
여기서 Bcrystalline는 미세화에 의한 반가폭증가, Bstrain은 변 형(strain)에 의한 반가폭 증가, λ는 파장, L은 결정립 크기, η는 변형(strain) 및 θ는 회절각도이다. Cu-Mn 소결체의 결정립 크기 측정결과 10 MPa에서 60 MPa로 압력이 증 가할수록 각각 31.4, 26.4, 23.5, 22.5, 22.2, 22.1 μm로써 소결압력에 비례하여 결정립 성장이 억제되는 것으로 분 석되었다.
일반적으로 분말에 인가된 소결압력 증가에 따라 소성 변형을 시킬 수 있는 구동력은 증가한다. 이로 인한 분말 내부의 기공 소멸에 큰 영향을 미치고 치밀화 속도는 빠 르게 진행되면서 원자 이동에 영향을 주지 않기 때문에 결정립 성장을 억제 시킨 것으로 생각된다.
그림 8은 수축변위가 발생하지 않은 400°C부터 최종목 적온도 700°C까지의 파단면 미세조직을 나타낸 것이다. 소결압력 60 MPa을 인가하지 않은 소결온도 그림 8(c) 600°C까지는 초기 원료분말과 동일한 형태의 구형의 형태 를 가지는 취성파괴의 파단면만 관찰되었다. 하지만 그림 8(d) 600°C에서 60 MPa의 압력을 인가하여 소결한 시편 의 파단면 경우 소결압력을 가하지 않은 600°C와 비교시 입자성장이 되는 미세조직을 관찰할 수 있었으며, 최종 소 결체인 그림 8(e) 700°C 소결체는 소성변형에 의한 치밀 화되어 딤플 파괴 및 입내 딤플파괴 현상을 관찰할 수 있 었다. 저온구간에서의 취성파괴는 저온에서 Cu-Mn 분말 의 치밀화가 진행되지 않으면서 분말의 결합력이 불안정 하여 소성변형을 동반하지 않은 취성파괴가 발생된다. 고 온구간에서의 딤플파괴는 소결체의 치밀화에 따른 분말과 분말 입자간 결합력이 증가하여 소성변형을 동반한 파괴 가 진행되어 딤플파괴가 발생하게 된다.
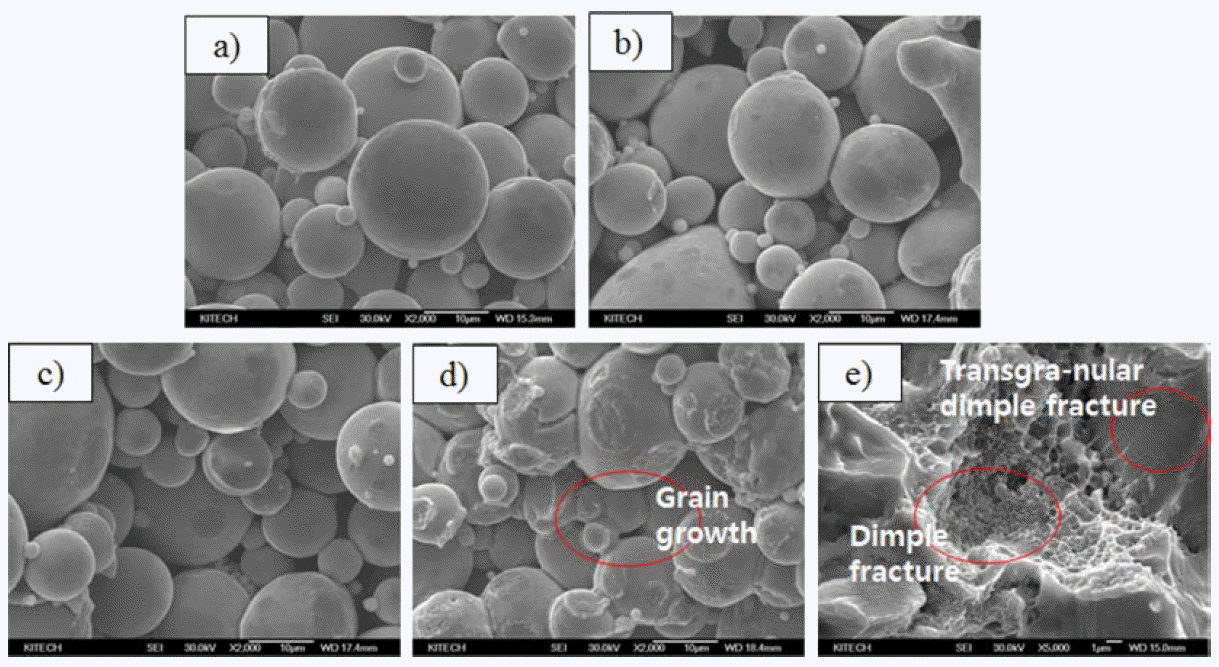
Microstructure of Cu-Mn sintered-body for differnet temperature under non pressure and 60 MPa: (a) non pressure 400°C, (b) non pressure 500°C, (c) non pressure 600°C, (d) 60 MPa, 600°C, and (e) 60 MPa, 700°C.
표 1에 최적 공정조건하에 제조된 직경 200 mmØ, 두께 6.35 mm의 Cu-Mn 소결체 및 주조법으로 제조되어 상용 되고 있는 Cu-Mn 스퍼터 타겟의 중앙 및 외각 부위의 시 편을 채취하여 밀도 및 결정립 크기를 측정하였다. 주조법 으로 제조된 상용타겟과 펄스전류활성 소결법에 의해 제 조된 타겟의 물성 비교시 상대밀도는 최대 약 2%정도 높 고, 결정립 크기는 최대 3배 이상 미세한 것으로 분석되었 다. 펄스전류활성 소결법으로 제조된 타겟이 더 우수한 물 성을 가지는 이유는 초기 원료분말부터 미세하고 저온 단 시간에 고압력 하에서 소결을 진행하여 입자 성장이 거의 일어나지 않아서라고 판단된다.
펄스전류활성 소결법으로 제조된 Cu-Mn 스퍼터 타겟의 ICP 순도 분석결과 초기 원료분말과 동일한 99.992%의 순도를 가지는 것으로 분석되었다. 초기 원료분말과 거의 동일한 순도 분석결과의 이유로는 저온 단시간에 고진공 분위기에서 소결이 진행되다보니 불순물 혼입을 방지할 수 있었으며, 또한 소결 중 발생하는 분말과 분말사이의 공극에서 스파크 현상에 따른 청정효과에 의한 결과라고 생각된다.
펄스전류활성 소결법에 의해 제조된 타겟 및 주조법에 의해 제조된 타겟을 인라인 스퍼터 장비를 이용하여 Cu- Mn 박막을 제조하였다. 두 타겟 모두 박막 제조시 플라즈 마 발화를 위한 최초 발생되는 아크만이 측정되었으며, 공 정 중 아크 발생은 없었다. 이는 전반적으로 고밀도 특성 으로 인해 기공으로 인한 아크 발생은 없는 것으로 판단 된다. 제조된 박막의 미세조직 결과를 그림 9에 나타내었 다. 두 박막 모두 약 450 nm 정도로 Cu-Mn 박막이 형성 되었으며, 라멜라 구조로 형성되어 있는 것으로 분석되었 다. 4 point probe를 이용한 비저항 측정결과 상용 타겟으 로 제조된 박막의 경우 약 6.306 × 10−6 Ωcm, 펄스전류활 성 소결로 제조된 타겟으로 제조한 박막으로 경우 약 6.112 × 10−6 Ωcm로 측정되었다. 두 가지 타겟으로 제조된 박막 모두 유사한 비저항 값을 가졌지만 펄스전류활성 소 결법으로 제조된 타겟으로 제조한 박막이 좀 더 높은 비 저항 값을 가지는 이유는 타겟의 물성이 균일하면서도 미 세 결정립 특성 때문으로 판단된다.
4. 결 론
펄스전류활성 소결법을 이용하여 직류 펄스전류를 인가 하는 동시에 압력을 가하여 제조 된 Cu-Mn 소결체에 대 해 소결 압력변화에 따른 특성평가를 수행하여 다음과 같 은 결론을 얻을 수 있었다.
Cu-Mn 소결체는 520°C부터 급격하게 소결이 진행되 며, 700°C 온도에서 소결이 완료되는 것을 알 수 있었다. 소결압력이 증가할수록 입자간의 평균자유행로가 짧아져 소결이 빨리 진행되고 상대밀도 또한 증가하였다. 특히 700°C-60 MPa조건에서 소결된 소결체의 상대밀도는 이론 밀도에 가까운 100%의 고밀도를 얻을 수 있었다.
Cu-Mn 소결체의 X선 회절분석 결과, 모든 압력조건 에서 초기 원료분말과 동일한 Cu단일상만 분석되었다. 가 스 분술물의 혼입으로 인한 금속산화물과 같은 제 2차상 은 관찰되지 않았으며, 이는 고진공 하에서의 공정 및 단 시간의 소결에 의한 결과라고 생각된다. Mn의 미분석 이 유로는 고용한도 이내로 첨가되어 전율고용체로 존재하기 때문으로 판단된다.
소결압력 변화에 따라 제조된 소결체는 소결압력이 증가할수록 73.1%에서 최대 100%로 고밀도의 상대밀도 를 가지는 것으로 분석되었고, 마찬가지로 소결압력이 증 가할수록 31.4 μm에서 22.1 μm 크기의 미세결정립을 가 지는 것으로 분석되었다. 소결압력이 증가할수록 고밀도 및 미세결정립을 가지는 이유는 소결시 인가된 소결압력 은 소결에 대한 구동력을 증가시키기 때문으로 생각된다.
소결온도 700°C, 소결 압력 60 MPa로 제조된 소결체 의 순도 측정결과 초기 분말 99.992%와 동일한 99.992% 의 순도를 확인하였으며, 이는 펄스통전활성 소결공정 시 분말과 분말사이에 스파크 발생으로 인하여 소결체의 청 정효과를 통한 불순물의 혼입 억제가 가능한 것으로 판단 된다.
소결온도 변화에 따른 Cu-Mn 소결체의 파단면의 소 결거동을 관찰한 결과 소결온도 600°C에서 소결압력 유무 에 따라 취성파괴 및 딤플파괴가 발생하였다. 600°C 이후 의 소결온도에서는 취성파괴보다는 딤플파괴 현상만이 발 생하였다. 이는 분말과 분말의 결합력 상승에 따른 소성변 형에 의한 것으로 판단된다.
펄스통전활성 소결법 및 주조법으로 제조된 타겟을 이용하여 Cu-Mn 박막 제조시 플라즈마 발화를 위한 최초 아크 발생을 제외한 공정 중 아크 발생은 발생하지 않았 다. 두 박막 모두 약 450 nm 크기의 라멜라 구조를 가진 박막으로 제조되었으며, 4 point probe를 이용한 비저항 측정결과 펄스통전활성 소결법으로 제조된 박막이 6.112 × 10−6 Ωcm로 좀 더 높은 특성을 가지는 것으로 분석되 었다.