3차원으로 정렬된 h-BN을 이용한 향상된 기계적 특성을 가지는 배터리 하우징용 고분자 복합소재 제작
Fabrication of 3D Aligned h-BN based Polymer Composites with Enhanced Mechanical Properties for Battery Housing
Article information
Trans Abstract
As the demand for electric vehicles increases, the stability of batteries has become one of the most significant issues. The battery housing, which protects the battery from external stimuli such as vibration, shock, and heat, is the crucial element in resolving safety problems. Conventional metal battery housings are being converted into polymer composites due to their lightweight and improved corrosion resistance to moisture. The transition to polymer composites requires high mechanical strength, electrical insulation, and thermal stability. In this paper, we proposes a high-strength nanocomposite made by infiltrating epoxy into a 3D aligned h-BN structure. The developed 3D aligned h-BN/epoxy composite not only exhibits a high compressive strength (108 MPa) but also demonstrates excellent electrical insulation and thermal stability, with a stable electrical resistivity at 200 °C and a low thermal expansion coefficient (11.46ⅹppm/℃), respectively.
1. Introduction
최근 탄소 배출량 저감 등 국제 환경 규제가 엄격해짐에 따라 이산화탄소가 배출되지 않는 전기차의 수요가 급격히 증가하고 있는 추세이다[1]. 하지만 전기차 내부 고용량 배터리는 열폭주로 인한 발화 및 폭발 등의 안전성 문제를 발생시켜 중요한 사회적 문제로 인식되고 있다[2, 3]. 진동, 충격, 열 등을 포함한 외부 자극으로부터 배터리를 보호하는 배터리 하우징(battery housing)은 전기차의 안전성 문제를 해소하기 위한 가장 중요한 요소이다. 기존 배터리 하우징은 우수한 기계적 특성, 방열 특성 때문에 Al계 금속 재료들(6061 합금, 7075 합금, 등) [4]이 많이 사용되고 있지만, 최근 전기차의 경량화를 통한 연비 향상 시도가 계속되며 금속을 대체할 소재로 고분자 복합소재가 활발하게 연구되고 있다[5, 6]. 고분자 복합소재를 배터리 하우징으로의 적용을 위해서는 경량화뿐 아니라 우수한 기계적 강도, 열적 안정성 및 전기 절연성 등 다양한 물성이 함께 확보되어야 외부 충격으로부터 배터리를 보호하고 누설 전류 및 열적 변형으로 인한 파손 또한 방지함으로써 고성능, 고연비 전기차의 안전성을 보장할 수 있다[7].
기계적 강도, 열적 안정성 및 절연성이 향상된 복합소재를 제작하기 위해 기능성 세라믹 필러를 고분자 소재에 첨가하는 연구가 활발히 진행되고 있다[8]. 첨가되는 세라믹 필러는 크게 산화물 소재, 탄화물 소재, 질화물 소재가 있다. 산화물 소재(Al2O3, MgO, SiO2) [9-11]의 원료 단가는 저렴하지만 상대적으로 낮은 기계적 물성을 나타내고, 탄화물 소재(SiC, WC) [12-15]는 열적 안정성이 우수하지만 상대적으로 높은 전기전도도의 단점이 있다. 이에 반해 질화물 소재는 우수한 기계적 강도, 전기 절연성을 나타내며, 특히 hexagonal Boron Nitride (h-BN)는 높은 절연성 (6 eV), 우수한 기계적 강도 (< 100 GPa)와 열적 안정성 (~ 3000 ℃)을 가지고 있고 다른 질화물 대비 가격이 상대적으로 저렴한 장점이 있다[16]. 다만 현재까지 연구된 h-BN 기반 복합소재는 고함량으로 첨가 시 응집에 의한 분산성 저하 문제로 오히려 기계적 강도가 감소하는 경향이 많이 보고되고 있다[17-19]. 이는 세라믹 필러 소재를 고분자 기지상에 단순 혼합을 통해 분산시키는 전통적인 복합소재 제작 방법의 한계에 의해 발생하는 현상이다. 이를 해결하기 위해 최근 적은 필러 함량으로 복합소재의 기계적 강도를 극대화 시키고 응집 문제를 해소하기 위해 3차원 정렬된 필러 구조체 제작 후 고분자 기지상을 충진시키는 새로운 접근 방식이 제시되기도 했다[20, 21]. Direct laser writing (DLW) [22], Proximity-field nanopatterning (PnP) [23], Additive manufacturing (AM) [24] 등 3차원 정렬 구조체를 제작하는 다양한 기술들이 개발되었지만 제작 공정이 복잡하고 비싸며 제작 가능한 크기 제한으로 배터리 하우징에 접목이 어렵다는 한계를 나타낸다.
본 연구에서 freeze-casting 공정을 이용하여 제작된 3차원으로 정렬된 h-BN구조체 기반 고성능 에폭시 복합소재 제작 방법을 제시한다. Freeze-casting 공정은 손쉽고 빠르게 균일한 3차원 세라믹 필러 구조체를 제작할 수 있으며, 제작 가능한 재료가 다양하고 복합소재 내 응집 문제를 효과적으로 줄일 수 있어 다양한 응용 분야에 적용 가능성이 높다. h-BN/에폭시 복합소재는 freeze-casting 공정으로 균일한 3차원 구조의 h-BN 를 형성 후, h-BN 구조체에 에폭시를 침투시켜 제작한다. 제작된 3차원 h-BN/에폭시 복합소재는 1.74 vol% 필러 함량을 첨가했을 때 가장 높은 압축강도 (108.9 MPa)를 나타냈다. 또한 200 ℃ 까지 안정적인 전기 절연성 및 열팽창률을 나타내었다. 이러한 복합소재는 배터리 하우징 소재로 적용시 높은 기계적 강도와 절연성으로 외부적인 요인으로 부터 배터리를 효과적으로 보호할 수 있으며, 경량화를 통해 주행 가능 거리 향상의 효과를 나타낼 수 있을 것으로 예상된다.
2. Experimental Procedure
2.1 h-BN 3차원 구조체 제작
h-BN (Hexagonal Boron Nitride, Sigma-Aldrich, Co., USA) (0.5g, 1 g, 1.5 g, 2 g) (그림 S 1)와 바인더 (30 wt%) (Polyvinyl Ahlconl, Sigma-Aldrich, Co., USA), 분산제 (1 wt%) (DisperBYK-104, BYK, Co., Germany)를 각각 함량별로 증류수와 섞은 후 상온에서 교반기로 24시간 동안 혼합하여 슬러리를 제작했다. 이 슬러리는 액체질소를 이용해 -80 ℃로 동결된 구리 막대 위에서 freeze-casting했다. 슬러리를 완전히 동결시킨 후 freeze-dryer (ilShin Biobase, South Korea)를 이용해 24시간 동안 건조시켜 h-BN 구조체를 제작했다.
2.2 h-BN/에폭시 복합소재 제작
에폭시 수지 (AC-526N-CL, Hightemp-korea, Co., Korea)와 경화제의 중량비를 1:1로 혼합한 후 h-BN 구조체를 진공 데시게이터에 위치시킨 후 1시간 동안 구조체 내의 공기를 제거하며 에폭시를 침투시켰다. 이 후 오븐에 넣어 150 ℃에서 1 시간동안 경화시켜 복합소재를 제작했다.
2.3 h-BN 구조체 및 복합소재 물성 분석
제작한 3차원으로 정렬된 h-BN 구조체와 복합소재는 전계 방출 투과 전자 현미경(JSM 7610F, JEOL, Japan)을 이용해 측정했다. 기계적 강도 측정을 위해 구조체 배열 방향은 응력이 가해지는 수평 방향으로 복합소재를 제작했으며, bar 형태(6ⅹ6ⅹ12 mm3)의 시편으로 5개씩 함량별로 가공하여 만능시험기 (UNITECH-T, R&B, Korea)를 이용해 500 N으로 압축강도를 측정했다. 복합소재의 체적 저항은 가열 가능한 패러데이 케이지 내부에 샘플을 위치 시킨 후 고저항 전류 계측기(2985B, Keysight, USA)를 이용해 500 V/mm로 측정했으며, 열팽창률 측정장비(DIL 402, NETZSCH, Germany)를 이용해 열팽창률을 측정했다.
3. Results and Discussion
그림 1 (a)는 freeze-casting을 통한 3차원 연결성 구조 기반 복합소재 제작의 전체적인 개략도를 보여준다. h-BN와 PVA, 분산제를 혼합한 슬러리를 제작 후 freeze-casting을 통해 수용액 내의 물이 얼면서 얼음 경로에 따라 필러들이 정렬되며, freeze-drying 공정을 통해 얼음 영역을 선택적으로 승화시켜 3차원으로 정렬된 h-BN 구조체를 형성하게 된다. PVA 바인더는 물에 녹는 플라스틱 수지로서 접착 성능이 우수한 특징으로 슬러리 내의 분산제에 의해 분산된 h-BN 필러를 물리적으로 접착시켜주는 역할을 하게 된다. 3차원으로 정렬된 h-BN구조체에 에폭시를 조밀하게 침투시켜 복합소재를 제작했다. 그림 1 (b)에서 볼수 있듯이 정렬된 3차원 h-BN 구조체의 단면 구조 배열 이미지를 통해 h-BN구조체가 큰 구조적 결함 없이 효과적으로 분산된 연결성 필러 구조를 확인할 수 있다. 또한 제작된 3차원 구조체는 h-BN 필러들간 상호 접합은 유지하면서97 % 이상 공기로 채워진 경량 다공성 구조체이다. 하지만 PVA 및 분산제의 상호 작용으로 인한 h-BN 필러간 계면에서 물리적인 결합이 향상되었으며, 1 g의 구조체 위에 100 g의 무게추를 올려 놓아도 구조의 변형이 발생하지 않는 고강도의 우수한 복합소재 물성을 확보할 수 있다(그림 1 c). h-BN 구조체 내부로 고강도 에폭시를 균일하게 충진시켜 최종적인 3차원 정렬 h-BN 기반 에폭시 복합소재를 제작한다(그림 1d). 제작된 3차원 h-BN/에폭시 복합소재의 단면 EDS mapping 이미지를 통해 h-BN 필러와 에폭시 수지의 규칙적, 반복적 배열된 구조를 확인할 수 있으며, 이는 복합소재 내 필러의 높은 균일성 및 연결성 확보가 가능한 효율적인 접근 방식이라는 것을 의미한다(그림 1 e).
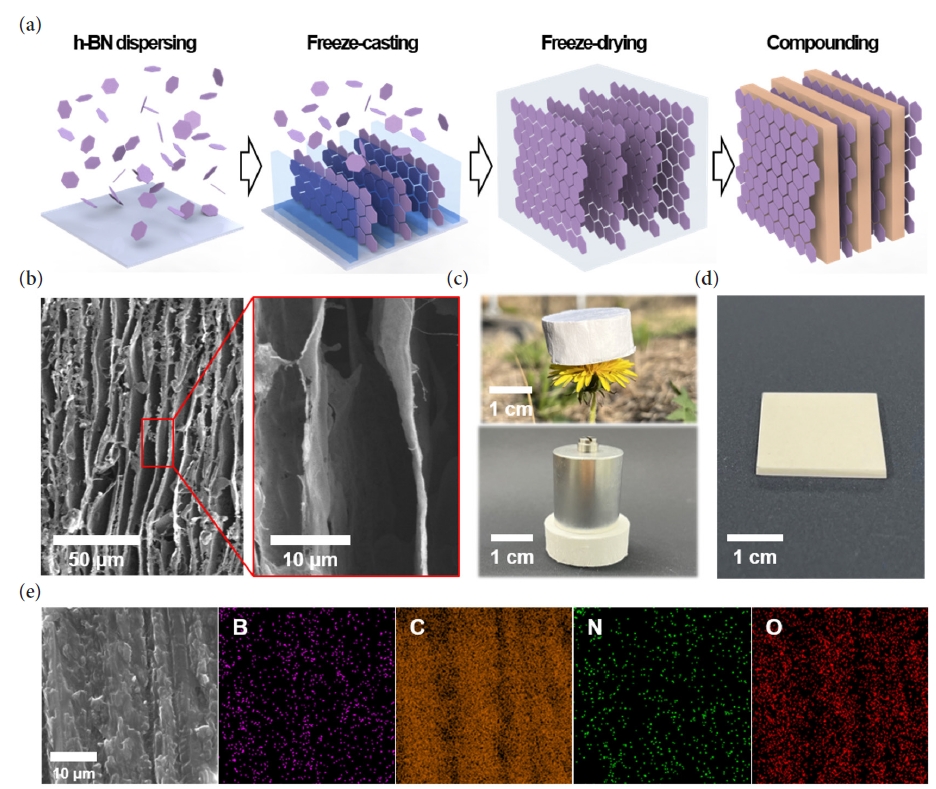
(a) Schematic illustration of the formation mechanism of aligned h-BN structure based epoxy composite. (b) SEM images of the aligned h-BN structures. (c) Optical images of the aligned h-BN structures above the flower and below weight. (d) Optical images of the aligned h-BN composite (e) EDS mapping images of the aligned h-BN/Epoxy composite.
본 연구에서 질화물 필러인 h-BN의 화학적 표면 손상처리 공정 없이 물에 분산시켜 균등하게 정렬된 3차원 구조체로 제작하기 위해 바인더를 이용한 분산 방법을 고안했다. 또한 슬러리 내의 PVA 함량 (10 wt%, 30 wt%) 및 필러의 함량 (2.5 wt%, 5 wt%, 7.5 wt%, 10 wt%)에 따라 3차원 구조체를 제작 후 단위 면적당 일정한 힘으로 눌렀을 때 변형 정도를 분석하여 3차원 구조체의 안정성을 비교했다. 그림 2 (a)는 freeze-casting으로 제작된 구조체를 90도 회전한 후, 면적 4 cm2 당 100 g (98 N)의 무게추를 올렸을 때 24.5 Pa 압력으로 가해지는 구조체의 변화를 확인했다. h-BN 필러 함량 대비 PVA 바인더를 10 wt% 함량으로 구조체를 제작했을 때 필러의 함량이 2.5 wt%, 5 wt%, 7.5 wt%, 10 wt%로 증가할수록 압축에 의한 구조 변형률은 다소 감소했지만 무게추가 한쪽으로 기우는 것을 확인할 수 있다 (그림 2 b). 이는 적은 바인더 함량으로 인해 필러간 계면에서의 결합 밀도가 감소하였으며, 동결 과정 중 필러의 응집 문제와 분산 저하로 균일도가 떨어져 구조체 전체의 강도가 약화된 것을 의미한다. 반면 필러 함량 대비 바인더 함량이 30 wt%일 때 필러의 함량이 증가할수록 PVA 함량 또한 함께 증가해 수용액에서 h-BN 필러간 계면에서의 결합 밀도가 향상되어 구조체의 강도가 향상된 것을 확인할 수 있다(그림 2 c). 그림 2 (d)는 필러의 함량이 증가할수록 h-BN 필러들 사이를 유기적으로 결합해 줄 수 있는 바인더의 함량이 증가하기 때문에 구조체의 안정성이 더 우수하다는 것을 보여준다. 구조체를 제작 후 윗부분부터 아랫부분까지 순서대로 top, middle, bottom으로 구역을 나누어 벽간 거리 분석을 진행했다. 바인더와 필러 함량에 따라 제작된 구조체의 top, middle, bottom 각각의 벽간 거리 비교를 통해 분산 정도를 정량적으로 확인할 수 있다(그림 2 e). 필러 함량이 적을수록 top, middle, bottom 구역의 벽간 거리는 균일하지 않으며 2.5 wt%와 5 wt% 일때 넓은 벽간 거리로 인해 구조가 불안정하여 쉽게 무너진 것을 나타낸다. 필러 함량 7.5 wt%에서 구역별 벽간 거리 차이는 1% 내로 가장 적어 균일하게 분산된 것을 확인할 수 있다. 하지만 10 wt%의 필러 함량에서 과포화 상태의 필러와 높은 점도로 인해 얼음이 생성되는 형상이 달라져 top, middle, bottom의 벽간 거리에서 차이가 나타나게 된다[25]. Turbiscan analysis를 통해 슬러리 분산 안정도를 측정해 보았을 때, PVA 30 wt%, h-BN 7.5 wt% 슬러리에서 ∆BS와 Turbiscan stability index (TSI)에서 가장 낮은 절댓값을 가지며, 분산 안정도가 가장 높은 것을 확인할 수 있다. 이는 슬러리 내 쌓이는 침전물이 가장 적은 것을 의미하며 분산성이 향상되었기 때문에 동결 건조 후 구조체에서 가장 균일한 벽간 거리를 나타내게 된다 (그림 S 2). 결과적으로 바인더의 함량에 따른 점도는 구조적 안정성에 더불어 필러의 분산에도 영향을 미친 것을 의미한다.
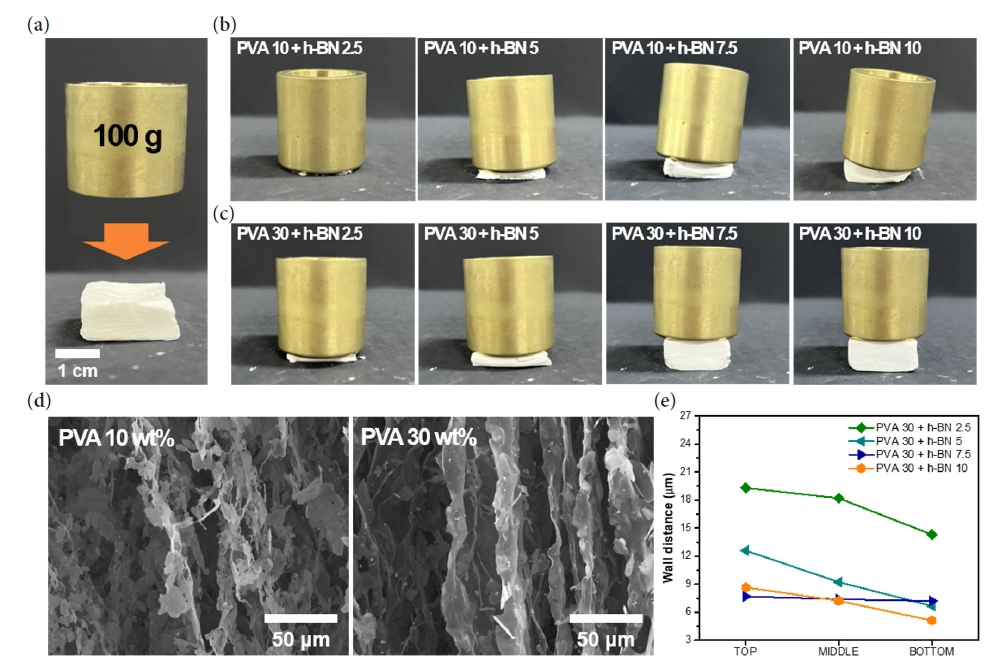
(a) Optical images of static load test of the aligned h-BN structure using a 100g weight. Optical images of 100g loaded 3D aligned h-BN at filler content of 2.5 wt%, 5 wt%, 7.5 wt%, and 10 wt% with (b) Polyvinyl Alcohol 10 wt% and (c) PVA 30wt%. (d) SEM images of 3D h-BN structures with PVA 10wt% and PVA 30 wt%. (e) Graphs of the wall distance of 3D h-BN structure according to filler content.
3차원으로 정렬된 h-BN 구조체로 제작된 복합소재의 기계적 강도는 배터리 하우징용 소재에 적합한 압축강도를 측정했다. 외부 압력으로부터 배터리 또는 전자 장치의 구성 요소가 손상될 수 있어 이를 방지하기 위해 배터리 하우징 소재의 압축강도는 안정성과 내구성을 보장하는데 필수적인 요소이다. 그림 3 (a)의 그래프는 필러 함량에 따른 3차원 h-BN/에폭시 복합소재의 압축 강도를 나타낸다. 필러 함량이 증가함에 따라 압축 강도가 증가하는 경향을 보였으며, 1.74 vol% 함량의 h-BN이 첨가되었을 때 108.9 MPa의 가장 우수한 압축 강도를 나타내었다. 하지만 2.32 vol%의 필러 함량일 때 강도가 다시 감소하는 경향을 보였다. h-BN 복합소재의 강도 증감 거동을 분석하기 위해 파단면을 FE-SEM으로 측정했다. 필러가 첨가되지 않은 순수한 에폭시는 한 방향으로 응력이 작용되어 92.8 MPa에서 쉽게 파단되었다(그림 3 b). 반면 필러 함량이 증가함에 따라 라멜라 구조로 3차원 h-BN 필러의 결합력이 증가하고, 에폭시를 침투한 복합소재에 가해지는 응력이 h-BN 구조체에 효율적으로 필러로 전달되어 균열이 억제되며 압축강도가 증가했다(그림 3 c, d). 이는 필러 함량에 따라 h-BN 구조체의 벽간 거리와 관계 있으며, 벽간 거리가 작고 균일한 구조체 일수록 강도가 증가하는 것을 의미한다. 특히 벽간 거리가 가장 일정하고 균일한 구조체로 제작한 복합소재에서 가장 우수한 압축강도인 1.74 vol%를 나타냈다(그림 3 e). 하지만 그림 3 (f)의 2.32 vol% 복합소재에서 오히려 감소한 것을 확인할 수 있다. 이는 높은 점도로 인해 동결 중 얼음 결정 성장의 형태 변화로 구조체 내에서 구조적 결함이 발생했기 때문이며, 이로 인해 응력은 필러를 통해 분배되지 않아 불 균일하게 파단 난 것을 볼 수 있다. 따라서1.74 vol% 첨가한 복합소재 대비 기계적 강도가 감소했다. 바인더의 함량은 얼음의 성장 속도에 영향을 주게 되며, 점도가 높을 때 얼음은 천천히 얼어 이방성인 라멜라 (lamella) 구조가 아닌 등방성인 덴드라이트 (dendrite) 구조로 성장한다. 압축하기 전 복합소재의 단면을 통해 2.32 vol% 함량에서 덴드라이트 구조가 형성된 것을 확인할 수 있다 (그림 S 3). 이러한 무질서한 구조에서 면간 거리는 일정하지 않으며, 점도에 의해 얼음이 라멜라 구조의 수직 형태로도 생성되어 얼음이 빠져나간 자리는 구조체 내에서 기공으로 작용한다. 따라서 구조체 내의 기공으로 결합 밀도가 감소한 2.32 vol%의 복합소재에서 기계적 강도가 감소한 것으로 예측된다[26].
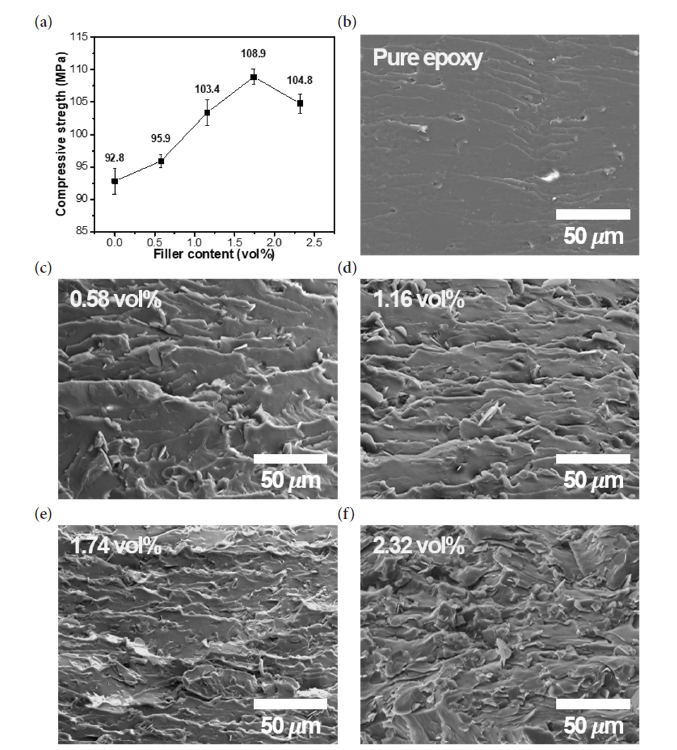
(a) Graphs of compressive strength of pure epoxy and h-BN/Epoxy composite with various filler contents. SEM images of the fracture surface of (b) pure epoxy, (c) h-BN 0.58 vol%, (d) h-BN 1.16 vol%, (e) h-BN 1.74 vol%, and (f) h-BN 2.32 vol% composite.
배터리 하우징용 고분자 복합소재의 추가적인 요구사항은 누설 전류 및 전기적 위험으로부터 배터리를 보호하는 전기 절연성과 열팽창으로 인한 파손을 방지하는 열적 안정성이다. 특히, 최근 배터리 열폭주 등의 이슈에 대해 대비하고자 제작한 3차원 복합소재의 비저항과 열팽창률에 대한 평가를 200 ℃까지 진행하였다. 복합소재에 대한 비저항은 DC 전류를 통해 측정되며 상온부터 200 ℃까지 측정해 보았을 때, 온도가 상승함에도 각 함량별 복합소재의 전기 저항은 안정적이고 일정하게 유지되며 온도에 따라 낮아지는 것을 확인할 수 있다. 이는 h-BN와 에폭시의 유사한 전기 저항 (1016 Ω∙cm)을 가지는 절연성 필러에 절연성 고분자를 침투시켰기 때문에 전기 저항의 차이가 발생하지 않은 것을 의미한다(그림 4 a). 또한 전기차의 배터리 하우징은 다양한 외부 환경에 따른 온도 차이 및 배터리 열에 의한 수축 팽창으로부터 안정성이 요구된다. 이로 인해 복합소재의 열팽창률을 측정해 보았을 때, 필러의 함량이 증가할수록 열팽창률이 낮아지는 것을 확인할 수 있다(그림 4 b). 이는 3차원으로 정렬된 필러로 응력이 분배되어 에폭시의 열팽창을 억제시켰으며 열 응력이 증가되었기 때문이다. 따라서 1.74 vol%의 복합소재에서 가장 낮은 열팽창률 (11.46ⅹppm/℃)을 나타냈으며, 이는 순수 에폭시 (18.36ⅹppm/℃) 대비 38 % 낮은 열팽창률을 가진다. 정렬된 라멜라 구조에 비해 무질서한 라멜라 구조에서 기공이 더 생기며 구조간 결합력이 약해진다. 또한 복합소재로 제작시 이러한 필러의 기공들은 기계적 강도를 감소시키는 동시에 열 응력도 감소시킨다[27]. 따라서 2.32 vol%의 복합소재의 구조체는 약해진 구조체의 기공으로 인해 열팽창률이 오히려 증가했다. 이렇게 개발한 3차원으로 정렬된 h-BN 가벼우며 절연 특성과 기계적 특성이 우수하여 배터리 및 배터리 하우징에 활용 가능할 것으로 기대된다.
4. Conclusion
본 연구에서 h-BN을 이용해 3차원으로 필러를 정렬하여 기계적, 전기적, 열적 특성이 우수한 배터리 하우징용 고분자 복합소재를 개발했다. 바인더 함량에 따른 향상된 분산 방법을 적용하여 균일하게 정렬된 3차원 h-BN 구조체를 제작방법을 제시했다. 이 3차원 h-BN 구조체를 이용한 우수한 특성을 가지는 h-BN/에폭시 복합소재를 구현했으며 필러 함량이 1.74 vol%일 때 108.9 MPa의 압축 강도를 나타냈으며, 이는 순수 에폭시 대비 17.3% 향상된 우수한 압축 강도를 나타냈다. 아주 적은양의 필러 함량으로 복합소재의 기계적 물성을 효율적으로 향상 시킬 수 있는 접근방법을 제시하고 증명했다는 점에서 중요한 의미가 있다. 또한 배터리를 보호하기 위해 배터리 하우징 소재에서 필수로 요구되는 전기 절연성과 열적 안정성에서 우수한 특성을 나타냈다. 이를 통해 온도차가 큰 다양한 기후에 따른 환경에도 사용 가능하며 친환경 자동차인 전기자동차를 넘어 우주선, 항공기, 등 배터리를 사용하는 다양한 운송 수단에도 활용될 것으로 기대한다.
Notes
Conflict of Interest Declaration
저자들은 이해상충관련 해당사항 없음을 선언합니다.
Author Information and Contribution
송기호: 위촉연구원/분말, 복합소재 제작, 분석 및 논문 초안 작성, 송현승: 석사과정 학생/분산 특성 분석, 이상인: 석사과정 학생/재료 미세구조 분석, 안창의: 선임연구원/연구디자인, 논문작성 및 연구책임자
Acknowledgements
이 성과는 정부(과학기술정보통신부)의 재원으로 한국연구재단의 지원 을 받아 수행된 연구입니다(NRF-2022R1F1A1069574).
Supplementary Materials
Supplementary data are available at https://doi.org/10.4150/jpm.2024.00220.
Electrocardiography. Atrial fibrillation with an absent P wave and a wide QRS complex interval (0.08 seconds).
(a) Turbiscan analysis of slurries according to h-BN filler content (holding time: 10 minutes) (b) Turbiscan stability index (TSI) profiles of h-BN slurries over time filler content.
SEM images of (a) 3D h-BN structures based on filler content, (b) h-BN/epoxy composite based on filler content before compressive strength.